Quality Control In Construction
Unlock key insights and practical strategies on Quality Control in Construction to boost your construction project management efficiency and outcomes.
In the dynamic field of project management, Quality Control (QC) in construction stands as a pivotal element for ensuring project success. At its core, QC refers to the systematic process of checking and validating that the work being executed meets specified standards of quality. This encompasses a range of activities including inspections, testing, and the implementation of corrective measures. When executed effectively, these practices significantly enhance project outcomes by reducing risks, ensuring compliance with industry standards, and maintaining safety. The complexities of modern construction projects necessitate robust QC practices. With an increasing number of stakeholders, intricate designs, and a demand for sustainable practices, mastering QC becomes an essential skill for today's project managers. The integration of QC into project management not only helps in meeting client expectations but also plays a critical role in mitigating potential legal ramifications. By adhering to stringent QC protocols, construction projects are more likely to be completed on time, within budget, and to the highest quality standards. As the construction industry continues to evolve, so too does the importance of advanced QC strategies. By staying ahead of these trends, project managers can ensure not only the success of individual projects but also their continued competitive advantage in the marketplace.
This is your workflow, built your way.
Understanding quality control in construction
Quality Control (QC) in construction is a comprehensive discipline involving a variety of standards and practices designed to ensure that construction projects meet or exceed predetermined quality criteria. At its essence, QC is about ensuring that the final product aligns with the original design and specifications while adhering to safety and regulatory standards. Historically, QC in construction has evolved from basic oversight to a complex system of standards and procedures. Traditionally, QC might have involved simple inspections and checklists, but today it encompasses a wide range of activities including detailed testing, continuous monitoring, and the application of advanced technologies. Regulatory bodies and industry standards play a crucial role in shaping QC practices. Organizations such as the International Organization for Standardization (ISO) and local building authorities provide frameworks and guidelines that set the benchmarks for quality. For instance, ISO 9001 is a popular standard that outlines requirements for a quality management system, and is often adopted in construction projects to ensure consistency and quality. This evolution and standardization of QC practices have been driven by the need to manage increasingly complex projects, ensure safety, and meet the expectations of a more informed and demanding clientele. Today's QC practices are about more than just compliance; they are integral to risk management, cost control, and delivering value to stakeholders. As construction projects become more complex, the necessity for robust and effective QC procedures becomes increasingly apparent. By understanding and applying these principles, project managers can greatly enhance the quality and success of their construction projects.
Keep exploring: Discover more insights and tips in our recommended templates!
Key components of quality control in construction
Quality Control (QC) in construction is built on several key components, each playing a critical role in maintaining the standards of quality throughout the project lifecycle. One of the fundamental elements is inspection protocols, which involve systematic reviews and examinations of construction activities and outputs to ensure they meet predefined quality standards. These inspections are often scheduled at various stages of the project to catch and rectify any deviations early. Another vital component is testing procedures, which include a range of laboratory and field tests to verify the quality of materials and workmanship. For example, concrete strength tests, soil compaction tests, and weld inspections are common practices that provide quantifiable data on quality. Documentation is also a cornerstone of QC processes, as it records everything from plans and specifications to inspection results and corrective actions. This documentation is crucial not only for tracking the project's adherence to quality standards but also for future reference and accountability. Corrective actions are implemented when deviations from the quality standards are detected, ensuring that any issues are addressed and resolved promptly. Setting benchmarks and quality metrics is essential for evaluating project performance. These metrics help in comparing actual outcomes with the desired quality levels and are instrumental in continuous improvement processes. By establishing clear benchmarks, project managers can identify trends, make informed decisions, and implement strategies that enhance quality. These components work in unison to create a comprehensive QC framework that ensures construction projects are executed to the highest standards. Understanding how each element functions within a project is crucial for maintaining quality and achieving project success.
Benefits of implementing quality control in construction
Incorporating effective Quality Control (QC) measures in construction projects yields numerous benefits that extend beyond mere compliance with standards. One of the primary advantages is improved safety. By rigorously enforcing QC protocols, potential hazards and defects can be identified and mitigated early, significantly reducing the risk of accidents and ensuring a safer work environment for all involved. Another key benefit is the reduction of rework, which is often a costly endeavor in construction projects. By identifying and addressing quality issues early, QC helps in minimizing the need for corrections and adjustments, leading to significant cost savings and improved project timelines. Enhanced client satisfaction is another critical advantage. When projects are delivered on time, within budget, and to the promised quality standards, client trust and satisfaction are naturally bolstered. This can lead to repeat business and positive referrals, which are invaluable in a competitive industry. In the short term, effective QC measures can result in cost savings and efficient resource utilization. In the long term, these measures contribute to reputation building and sustainability. Companies known for their quality commitment are more likely to secure future projects and maintain a competitive edge. Moreover, QC plays an essential role in meeting legal and contractual obligations, avoiding potential litigation and penalties. In today's construction landscape, where projects are becoming increasingly complex and client expectations are higher than ever, the importance of robust QC measures cannot be overstated. By prioritizing and implementing strong QC practices, construction companies can achieve better project outcomes, foster client relationships, and enhance their industry standing.
Keep exploring: Discover more insights and tips in our recommended templates!
Challenges in quality control and solutions
The implementation of Quality Control (QC) in construction comes with its own set of challenges, which can hinder the efficacy of QC processes if not managed properly. One common challenge is resistance to change. Often, team members accustomed to traditional practices may be reluctant to adopt new QC protocols or technologies. This resistance can be mitigated through comprehensive training programs that emphasize the benefits and necessity of QC, as well as by fostering an environment that encourages open communication and collaboration. A lack of adequate training is another significant challenge. Without proper training, staff may not fully understand the QC processes or the importance of their roles in ensuring quality. Investing in continuous training and development programs can equip team members with the necessary skills and knowledge to perform QC tasks effectively. Resource constraints, including limited budget and manpower, can also pose significant hurdles. To navigate these challenges, project managers can prioritize QC activities and allocate resources strategically, focusing on high-impact areas. Engaging stakeholders is crucial in overcoming these challenges. By involving them in the QC planning and implementation phases, project managers can ensure alignment and buy-in from all parties involved. Technological and logistical barriers can also affect QC processes. However, these can be addressed by adopting innovative solutions such as digital tools and software that streamline QC activities, making them more efficient and effective. By understanding and addressing these challenges proactively, construction companies can ensure the successful implementation of QC measures that lead to improved project outcomes and client satisfaction.
Case studies of quality control in construction
Example 1: Large-Scale Infrastructure Project
In a large-scale infrastructure project, such as the construction of a major highway, QC strategies were meticulously planned and executed. The project's success was largely attributed to its comprehensive QC framework, which included regular inspections, material testing, and real-time reporting. Advanced technologies like drones and sensors were employed to monitor construction progress and detect potential issues early. The use of Building Information Modeling (BIM) provided a digital representation of the project, allowing for detailed planning and coordination among various stakeholders. As a result, the project was completed ahead of schedule and under budget, with minimal defects and high client satisfaction.
Example 2: Residential Development
In a residential development project, the QC team faced several challenges, including resistance from subcontractors to adhere to new QC protocols and a lack of initial training for workers. To overcome these obstacles, the project manager implemented a series of workshops and training sessions to educate the team on the importance of QC and how to effectively execute QC measures. By fostering a culture of quality and open communication, the team was able to address issues collaboratively. The project successfully achieved its quality benchmarks, resulting in high client satisfaction and positive feedback from homeowners.
Example 3: Commercial High-Rise Building
A commercial high-rise building project demonstrated the impact of a robust QC plan. The project utilized advanced QC practices, such as rigorous material testing and frequent inspections, to ensure compliance with stringent quality standards. The implementation of automated QC tools facilitated real-time data collection and analysis, enabling the team to make informed decisions quickly. This proactive approach to QC resulted in a high-quality build, minimal rework, and a reputation for delivering excellence. The project's success highlighted the importance of integrating QC into every phase of the construction process, from design to completion.
Keep exploring: Discover more insights and tips in our recommended templates!
Best practices and strategies for quality control
Implementing best practices in Quality Control (QC) can significantly enhance the effectiveness and efficiency of construction projects. One of the most critical best practices is promoting a culture of continuous improvement. This involves regularly reviewing QC processes and outcomes to identify areas for enhancement and implementing necessary adjustments. By fostering an environment where quality is prioritized, project teams can consistently deliver superior results. Stakeholder communication is another essential strategy. Keeping all stakeholders informed and engaged throughout the project lifecycle ensures alignment and builds trust. Regular updates and feedback sessions can help in addressing concerns and making timely adjustments to the QC plan. Integrating QC into existing project management frameworks, such as Lean or Agile methodologies, can also improve project outcomes. These approaches emphasize efficiency and adaptability, aligning well with the goals of QC. Training and developing a skilled QC team is vital for successful implementation. Investing in continuous learning opportunities and certifications for QC personnel ensures they are equipped with the latest knowledge and skills to execute QC tasks effectively. By adopting these best practices and strategies, construction companies can enhance their QC processes, leading to improved project outcomes, cost savings, and increased client satisfaction. These practices not only ensure compliance with quality standards but also contribute to the overall success and reputation of the organization.
Advanced tools and technologies supporting quality control
The advent of advanced tools and technologies has revolutionized Quality Control (QC) in construction, making it more efficient and effective. One of the most significant technologies is Building Information Modeling (BIM), which provides a digital representation of the physical and functional characteristics of a project. BIM facilitates precise planning, coordination, and execution, significantly reducing errors and rework. Drones are another innovative tool that has become increasingly popular in QC. They provide aerial views of construction sites, allowing for comprehensive inspections and progress monitoring. Drones can quickly identify potential issues such as structural defects or safety hazards, enabling timely corrective actions. Software solutions also play a crucial role in supporting QC processes. Various applications offer functionalities for tracking inspections, managing documentation, and analyzing data. These tools streamline QC activities, making them more manageable and transparent. Data analytics is another powerful tool that can be leveraged in QC. By analyzing large volumes of data from various sources, project managers can gain insights into trends and patterns, helping them make informed decisions. When selecting the right tools, it's essential to consider the specific needs and scale of the project. By integrating digital technologies and data analytics into QC processes, construction companies can enhance their quality management practices, leading to improved project outcomes and client satisfaction.
Keep exploring: Discover more insights and tips in our recommended templates!
Dos and don'ts of quality control in construction
Dos | Don'ts |
---|---|
Ensure thorough training for all project personnel | Do not overlook minor defects or issues |
Regularly update and review QC procedures | Avoid cutting costs at the expense of quality |
Foster a culture of open communication regarding quality | Do not ignore feedback from stakeholders |
Implement technology to enhance QC processes | Avoid relying solely on manual processes |
Encourage continuous improvement and adaptation | Do not resist necessary changes to QC practices |
Keep exploring: Discover more insights and tips in our recommended templates!
This is your workflow, built your way.
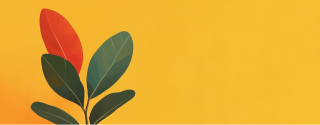
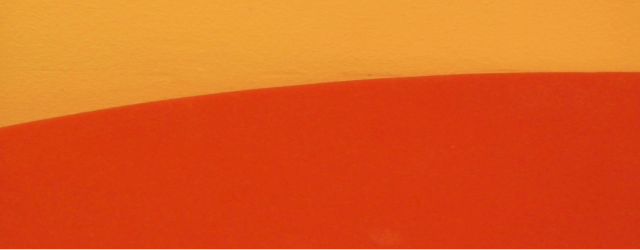
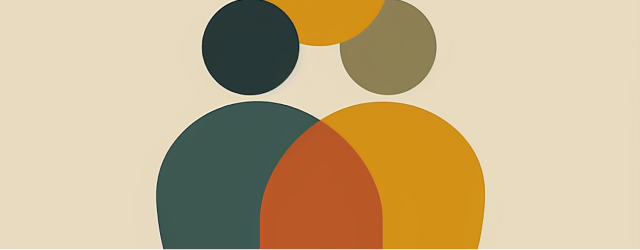
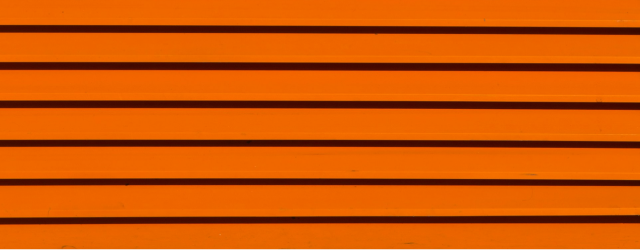
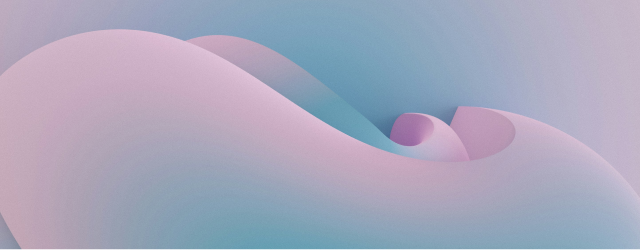
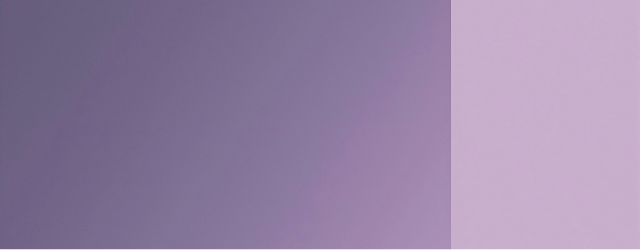
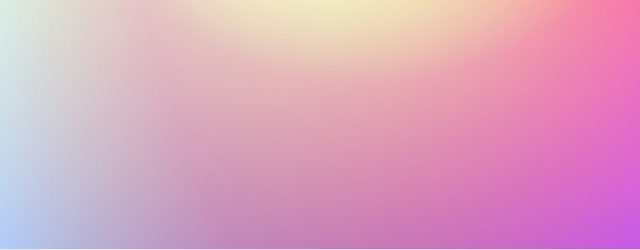
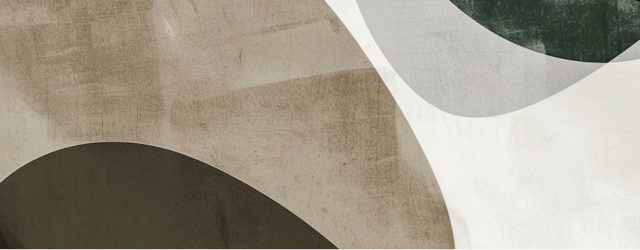