Battery Management Systems
Explore the critical role of Battery Management Systems in electric vehicle manufacturing, offering insights into technological impacts, industry challenges, and future trends.
The electric vehicle (EV) market is experiencing an unprecedented surge, driven by a global shift towards sustainable energy solutions and reducing carbon footprints. As the industry expands, a critical component has emerged at the heart of EV innovation—the Battery Management System (BMS). This technology is becoming indispensable in the EV manufacturing sector, as it holds the key to optimizing battery performance, ensuring safety, and enhancing vehicle efficiency. The interest among professionals to understand BMS is growing exponentially, not just because of its potential to revolutionize EV manufacturing but also due to its role in addressing the pressing challenges of battery longevity and reliability. BMS technology is not just a technical component; it's a strategic tool that paves the way for sustainable transportation solutions. This article dives deep into the world of BMS, offering insights for project managers and professionals who aspire to leverage this technology to its fullest potential. Through a comprehensive exploration, we'll uncover how BMS is shaping the future of electric mobility, setting the stage for a cleaner, more efficient transportation ecosystem.
All You Need for Project Management is in Meegle!
Understanding battery management systems
Defining Battery Management Systems and Their Core Components
A Battery Management System (BMS) is a critical technology in electric vehicles, responsible for managing the performance and health of the vehicle's battery pack. The core components of a BMS include cell monitoring, battery protection, and charge control, each playing a vital role in ensuring the efficient operation of the battery. Cell monitoring involves continuously assessing the voltage, current, and temperature of each battery cell to ensure they operate within safe parameters. Battery protection is crucial for preventing overcharging, over-discharging, and thermal runaway, which can compromise battery health and safety. Charge control, on the other hand, manages the charging process to optimize battery life and efficiency.
In the EV sector, the significance of a BMS cannot be overstated. As the primary guardian of the battery pack, the BMS contributes significantly to the safety, longevity, and performance of electric vehicles. Without a robust BMS, the risks of battery failures and safety hazards would increase exponentially, potentially leading to catastrophic outcomes. Furthermore, a well-designed BMS enhances the overall efficiency of an EV by ensuring optimal energy management, thereby extending the vehicle's range and performance.
Beyond its fundamental functions, a BMS plays a pivotal role in fostering innovation within the EV industry. By providing accurate data and insights into battery behavior, a BMS enables manufacturers to fine-tune battery designs and develop more sophisticated energy management strategies. This capability is crucial for overcoming some of the industry's biggest challenges, such as increasing energy density, improving charging rates, and ensuring thermal stability. As the EV market continues to grow, the role of BMS technology is only set to expand, making it a cornerstone of future advancements in electric mobility.
Historical development
Evolution of Battery Management Systems in EV Production
The evolution of Battery Management Systems in electric vehicle production is a fascinating journey that reflects the rapid technological advancements in the automotive industry. Initially, battery management involved basic monitoring systems used in hybrid vehicles, primarily focusing on fundamental aspects like voltage regulation and overcharge protection. These early systems were rudimentary and offered limited functionalities, but they laid the groundwork for more sophisticated solutions.
A significant milestone in the development of BMS technology came with the advent of fully electric vehicles. As the demand for higher energy efficiency and safety increased, the need for more advanced BMS solutions became apparent. This led to the integration of more comprehensive functionalities, such as state-of-charge (SOC) estimation and state-of-health (SOH) monitoring, which are critical for assessing battery performance and lifespan.
The transition from basic battery monitoring systems to sophisticated integrated BMS solutions marked a turning point in EV production. With the incorporation of real-time data analytics and advanced algorithms, modern BMS can provide precise insights into battery conditions, enabling predictive maintenance and performance optimization. This evolution was further driven by the convergence of various technologies, including Internet of Things (IoT), artificial intelligence (AI), and machine learning, which have significantly enhanced BMS capabilities.
Key technological advancements, such as the development of lithium-ion (Li-ion) batteries, also played a crucial role in shaping BMS design and function. As Li-ion batteries became the standard for EVs due to their superior energy density and performance, the complexity of managing these batteries increased. This complexity necessitated the development of more sophisticated BMS architectures capable of addressing challenges like thermal management and cell balancing.
In recent years, the focus has shifted towards developing BMS solutions that support fast charging and extend battery life, addressing some of the most pressing demands of the modern EV market. The evolution of BMS technology continues to be a dynamic field, with ongoing research and development aimed at pushing the boundaries of battery performance and safety in electric vehicles.
Click here to read our expertly curated top picks!
Key technologies
Technological Backbone of Battery Management Systems
The technological backbone of Battery Management Systems is built upon a combination of advanced software algorithms, robust hardware components, and efficient communication protocols. These elements work together to ensure the optimal performance and safety of electric vehicle batteries. At the core of a BMS are software algorithms that manage battery operations, such as state-of-charge (SOC) and state-of-health (SOH) estimations. These algorithms utilize complex mathematical models to predict battery behavior and make real-time adjustments to maximize efficiency and lifespan.
Hardware components of a BMS include sensors, controllers, and microprocessors, each playing a crucial role in data acquisition and processing. Sensors are responsible for monitoring parameters like voltage, current, and temperature across individual cells, providing the necessary data for the system to make informed decisions. Controllers and microprocessors process this data, executing the software algorithms to ensure the battery operates within safe and efficient limits.
Communication protocols are vital for seamless data exchange between the BMS and other vehicle systems. Protocols such as CAN (Controller Area Network) and LIN (Local Interconnect Network) enable reliable communication, allowing the BMS to interact with the vehicle's control systems and external devices like chargers. This connectivity is essential for coordinating battery operations and ensuring the vehicle's overall performance.
The integration of IoT, AI, and machine learning further enhances BMS functionalities, providing capabilities like predictive analytics and adaptive control. IoT connectivity allows for remote monitoring and management of battery systems, enabling real-time diagnostics and performance optimization. AI and machine learning algorithms analyze historical and real-time data to predict potential issues and optimize battery usage patterns, contributing to increased efficiency and reduced maintenance costs.
Real-time data analytics and cloud connectivity are increasingly important in modern BMS applications, offering a platform for continuous improvement and innovation. By leveraging cloud-based data storage and processing, manufacturers can gather insights from vast datasets, driving advancements in battery technology and management strategies. This capability is crucial for developing next-generation BMS solutions that address the evolving demands of the electric vehicle market.
The technological backbone of BMS is a dynamic and evolving landscape, with ongoing research and development focused on enhancing performance, safety, and efficiency. As the EV industry continues to grow, the role of these technologies in shaping the future of electric mobility will only become more significant.
Market dynamics
The Role of Battery Management Systems in Shaping the EV Market
Battery Management Systems play a pivotal role in shaping the dynamics of the global electric vehicle market. As the EV industry continues to expand, driven by increasing consumer demand for sustainable transportation solutions, BMS technology is at the forefront of innovation. The impact of BMS on market trends, consumer preferences, and competitive dynamics is profound, influencing various aspects of EV design and production.
One of the primary ways BMS technology drives innovation is through its influence on battery design and manufacturing processes. By providing precise insights into battery performance and health, BMS allows manufacturers to optimize battery chemistries and configurations, enhancing energy density and efficiency. This optimization is crucial for meeting consumer expectations for longer vehicle ranges and shorter charging times, key factors influencing EV adoption rates.
BMS technology also plays a significant role in enhancing vehicle performance and safety, two critical factors in consumer decision-making. By ensuring the battery operates within safe parameters and optimizing energy management, BMS contributes to improved vehicle reliability and efficiency. This capability is essential for building consumer trust and confidence in electric vehicles, driving market penetration and adoption.
Moreover, BMS influences competitive dynamics within the EV market by enabling manufacturers to differentiate their products through advanced battery management solutions. As the market becomes increasingly competitive, the ability to offer superior battery performance and longevity becomes a key differentiator. This differentiation, driven by BMS technology, allows manufacturers to capture a larger market share and establish a competitive edge.
The impact of BMS on market dynamics is further amplified by its role in addressing regulatory requirements and standards. As governments worldwide implement stringent regulations to promote EV adoption and reduce emissions, BMS technology is essential for ensuring compliance with safety and environmental standards. This compliance is critical for manufacturers to access global markets and compete effectively.
In summary, Battery Management Systems are integral to shaping the EV market, driving innovation and influencing consumer preferences and competitive dynamics. As the industry continues to evolve, the role of BMS technology in advancing electric mobility and sustainability will remain at the forefront, contributing to a cleaner and more efficient transportation ecosystem.
Click here to read our expertly curated top picks!
Case studies
Successful Applications of Battery Management Systems
Example: Tesla's BMS Strategy
Tesla is renowned for its innovative approach to electric vehicle manufacturing, and its Battery Management System strategy is no exception. The company's BMS technology is a key component of its success, contributing to the longevity and performance of its vehicles. Tesla's BMS is designed to optimize battery usage and extend life by implementing advanced algorithms for cell balancing and thermal management. This approach not only enhances vehicle performance but also ensures safety and reliability, critical factors in Tesla's market leadership. The company's commitment to continuous improvement and innovation in BMS technology is evident in its ability to offer industry-leading range and efficiency, setting a benchmark for competitors.
Example: Nissan's Leaf EV
Nissan's Leaf EV is another example of successful BMS implementation, focusing on optimizing energy management and safety. The Leaf's BMS is engineered to provide accurate state-of-charge (SOC) and state-of-health (SOH) estimations, enabling precise energy management and prolonging battery lifespan. Safety is a top priority, with the BMS incorporating features like overcharge protection and thermal management to prevent potential hazards. Nissan's approach to BMS has been instrumental in the success of the Leaf, making it one of the best-selling electric vehicles globally. By prioritizing safety and efficiency, Nissan has established the Leaf as a reliable and eco-friendly transportation option.
Example: BYD's BMS Innovations
BYD, a leading manufacturer of hybrid and electric buses, has pioneered innovative BMS solutions for efficient energy utilization. The company's BMS technology is designed to optimize battery performance in demanding operational environments, ensuring reliability and efficiency. BYD's BMS incorporates advanced features like real-time data analytics and cloud connectivity, enabling remote monitoring and management of battery systems. This capability is crucial for fleet operators, allowing for predictive maintenance and performance optimization. BYD's focus on BMS innovation has allowed it to capture a significant share of the global electric bus market, delivering reliable and sustainable transportation solutions.
These case studies highlight the diverse applications of BMS technology in the EV industry, showcasing the potential for innovation and success. By leveraging advanced BMS solutions, companies like Tesla, Nissan, and BYD continue to lead the way in electric mobility, setting new standards for performance, safety, and sustainability.
Challenges and solutions
Overcoming Obstacles with Battery Management Systems
Implementing Battery Management Systems in electric vehicles presents several challenges, but with the right strategies and solutions, these obstacles can be effectively addressed. One of the major challenges is thermal management, which is crucial for ensuring battery safety and longevity. Without proper thermal regulation, batteries are at risk of overheating, leading to potential safety hazards and reduced performance. To overcome this challenge, manufacturers can incorporate advanced cooling technologies and thermal management algorithms within the BMS. These solutions enable precise temperature control, enhancing safety and extending battery life.
Cost constraints pose another significant challenge in BMS implementation. Developing and integrating a sophisticated BMS can be expensive, impacting the overall cost of EV production. However, by leveraging economies of scale and adopting modular BMS architectures, manufacturers can reduce costs while maintaining functionality. Collaborating with suppliers and investing in research and development can also lead to cost-effective BMS solutions that do not compromise on quality or performance.
Integration complexity is a further challenge, particularly when it comes to seamlessly incorporating BMS into existing vehicle architectures. To address this, manufacturers should adopt standardized communication protocols and interfaces, allowing for easier integration with vehicle control systems. Comprehensive testing and validation processes are essential to ensure compatibility and performance, minimizing integration-related issues.
Continuous research and development play a vital role in overcoming these challenges, driving innovation and advancing BMS technology. By staying abreast of the latest advancements and trends, manufacturers can develop cutting-edge BMS solutions that address the evolving demands of the EV market. Industry insights and expert recommendations provide valuable guidance in navigating these challenges, ensuring successful BMS implementation.
In summary, while implementing Battery Management Systems presents several challenges, these obstacles can be effectively addressed with the right strategies and solutions. By prioritizing thermal management, cost efficiency, and seamless integration, manufacturers can leverage BMS technology to enhance safety, performance, and sustainability in electric vehicles.
Click here to read our expertly curated top picks!
Regulatory and ethical considerations
Compliance and Ethical Practices
The regulatory landscape surrounding Battery Management Systems is complex, with various safety standards, environmental regulations, and international compliance requirements to consider. Ensuring compliance with these regulations is critical for manufacturers to access global markets and avoid legal repercussions. Key regulatory standards, such as those set by the International Electrotechnical Commission (IEC) and the Society of Automotive Engineers (SAE), provide guidelines for battery safety and performance, influencing BMS design and implementation.
Meeting these regulatory standards requires a comprehensive understanding of the requirements and a commitment to ongoing compliance. Manufacturers must invest in rigorous testing and validation processes to ensure their BMS solutions meet safety and performance benchmarks. Collaboration with regulatory bodies and industry organizations can provide valuable insights and support, facilitating compliance and reducing the risk of non-compliance.
In addition to regulatory considerations, ethical practices are essential in BMS design and deployment. Sustainable practices, such as minimizing environmental impact and promoting recyclability, should be prioritized in BMS development. This commitment to sustainability is not only an ethical imperative but also a strategic advantage, aligning with consumer expectations and enhancing brand reputation.
Consumer safety is another critical ethical consideration, with manufacturers responsible for ensuring their BMS solutions protect users from potential hazards. Transparent communication and education about BMS functionality and safety features can build consumer trust and confidence, supporting market adoption and growth.
In conclusion, compliance and ethical practices are integral to successful BMS implementation, ensuring safety, sustainability, and market access. By prioritizing these considerations, manufacturers can develop BMS solutions that align with regulatory requirements and ethical standards, contributing to the advancement of sustainable and responsible electric mobility.
Click here to read our expertly curated top picks!
Do's and dont's of bms implementation
Do's | Dont's |
---|---|
Conduct thorough market research | Ignore regulatory compliance |
Prioritize safety and reliability | Overlook integration testing |
Engage with experienced suppliers | Compromise on component quality |
Invest in training and development | Neglect ongoing maintenance |
Click here to read our expertly curated top picks!
Conclusion
Key Takeaways
Battery Management Systems are a cornerstone of the electric vehicle industry, playing a critical role in advancing EV manufacturing, enhancing vehicle safety, and driving innovation. Through this exploration, we've highlighted the importance of BMS technology in optimizing battery performance, ensuring safety, and contributing to sustainability. As the EV market continues to evolve, professionals and aspiring project managers must stay informed about the latest advancements and trends in BMS technology to remain competitive. By understanding the challenges and opportunities presented by BMS, industry players can develop strategies that leverage this technology to its fullest potential, paving the way for a cleaner and more efficient transportation ecosystem. BMS will undoubtedly continue to be a driving force in the sustainable future of transportation, offering exciting possibilities for innovation and growth.
All You Need for Project Management is in Meegle!
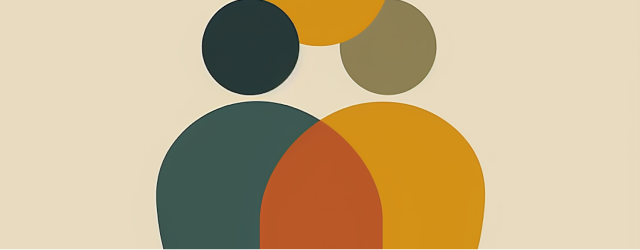
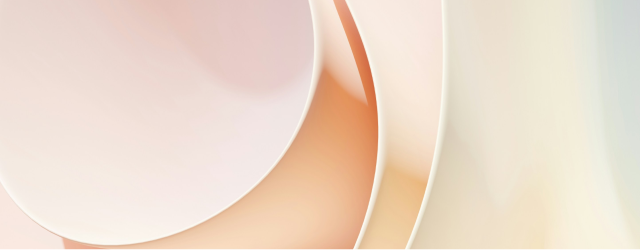
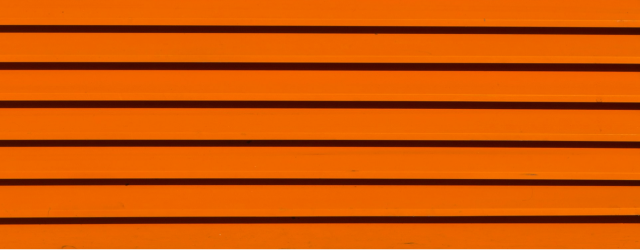
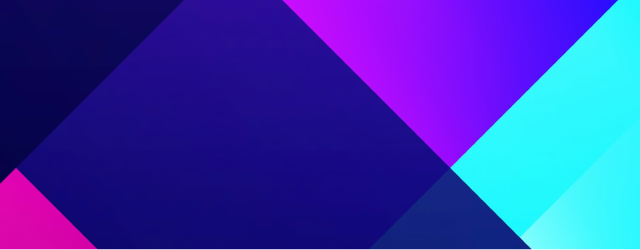
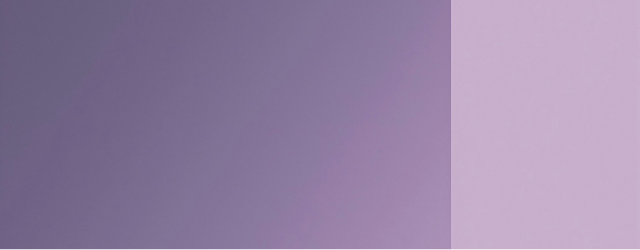
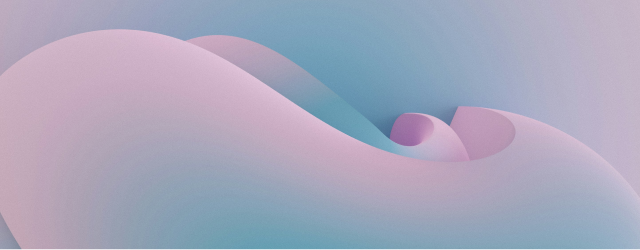
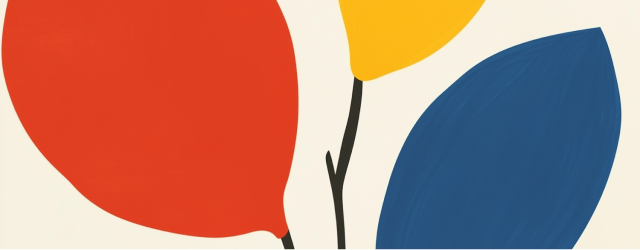
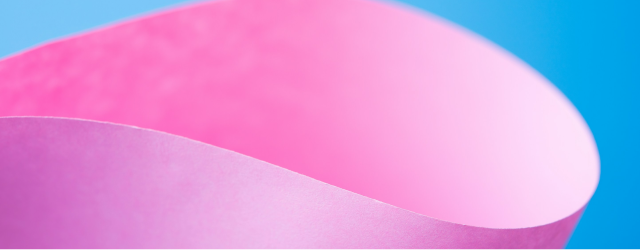