Wireless Network Solutions For EVs
Explore the critical role of Wireless Network Solutions for EVs in electric vehicle manufacturing, offering insights into technological impacts, industry challenges, and future trends.
Understanding Wireless Network Solutions for EVs
Wireless network solutions encompass a range of technologies that facilitate communication without physical connectivity. In the context of EV manufacturing, these solutions primarily include IoT, 5G, and other advanced wireless technologies that enable seamless connectivity and automation. The significance of these technologies is evident in their ability to enhance connectivity and facilitate real-time data exchange throughout the production process. By integrating wireless networks, manufacturers can automate processes, leading to increased efficiency and reduced human error. The ability to monitor and control production lines remotely, achieve predictive maintenance, and ensure quality control through real-time analytics are just a few of the transformative benefits. For example, IoT devices can monitor machinery health, predicting failures before they occur and minimizing downtime. Such advancements significantly reduce production costs and speed up the time-to-market for new EV models.
For project managers and professionals in the EV manufacturing sector, focusing on the incorporation of wireless technologies is becoming increasingly crucial. Not only do these technologies offer operational efficiencies, but they also provide a platform for innovation in vehicle design and functionality. Wireless networks support the production of smarter, more connected vehicles, aligning with consumer demands for advanced tech features in their cars. Current statistics highlight that the global IoT in the automotive market is expected to grow from $15.87 billion in 2021 to $82.79 billion by 2026, underscoring the expanding role of these technologies in the industry. Thus, incorporating wireless solutions is not just a strategic advantage but a necessity for those aiming to lead the market in the competitive world of EV manufacturing.
All You Need for Project Management is in Meegle!
Historical development
Evolution of Wireless Network Solutions for EVs in EV Production
Tracing the origins of wireless network solutions within the automotive industry reveals a journey marked by innovation and adaptation. The integration of wireless technologies in EV manufacturing has evolved significantly, beginning with early attempts at basic remote controls and telemetry systems. Over the years, advancements in technology have progressively introduced more sophisticated solutions, paving the way for modern applications that are now integral to EV production.
One of the earliest milestones in this evolution was the adoption of Bluetooth technology, which facilitated short-range communication between devices. This basic form of wireless networking laid the groundwork for more complex integrations. As technology advanced, so did the demand for more robust wireless solutions. The introduction of Wi-Fi allowed for greater data transmission capabilities, enabling wireless communication on a larger scale within manufacturing plants. These developments set the stage for the inclusion of IoT, a technology that would revolutionize connectivity in manufacturing environments by enabling devices to communicate and share data seamlessly.
The emergence of 5G technology represents the latest significant breakthrough, offering unprecedented speed and low latency. This advancement enables real-time data processing and enhances the capabilities of automated systems, making it possible for manufacturers to implement smart factories fully. However, the journey hasn't been without its challenges. Initial implementations faced issues such as limited bandwidth, security concerns, and interoperability problems. Nonetheless, these challenges have driven innovation, resulting in more secure and efficient wireless solutions.
Today, the landscape of EV production is shaped by these technological advancements, creating opportunities for further innovation and efficiency. The evolution of wireless network solutions continues to be a dynamic process, constantly adapting to new technological possibilities and market demands. This historical perspective highlights the importance of staying informed about technological trends and preparing for future advancements in wireless solutions.
Click here to read our expertly curated top picks!
Key technologies
Technological Backbone of Wireless Network Solutions for EVs
The technological backbone of wireless network solutions in EV production is composed of a synergy of advanced technologies, including IoT, 5G, and edge computing. Each of these plays a pivotal role in creating a seamless and efficient manufacturing environment, enabling manufacturers to optimize operations and enhance vehicle features.
IoT devices are fundamental in connecting various components within the manufacturing process. These devices collect vast amounts of data from different stages of production, from raw material handling to final assembly. The data collected is then transmitted to cloud-based platforms where it is analyzed in real-time to provide insights into production efficiency, machine health, and quality control. This level of automation and real-time monitoring helps to identify bottlenecks and improve overall production efficiency.
5G technology takes the capabilities of wireless networks to new heights with its high-speed data transmission and low latency. In EV manufacturing, 5G enables the real-time processing of data, which is critical for applications such as automated guided vehicles (AGVs) and robotic arms used in assembly lines. These applications require quick and reliable communication to function correctly and efficiently, ensuring that production workflows are not disrupted.
Edge computing complements these technologies by processing data closer to the source, reducing the need for data to travel back and forth to centralized data centers. This technology enhances the speed and efficiency of data processing, allowing manufacturers to make quick decisions based on real-time insights. For instance, an edge computing system can process data from IoT sensors on the production line to immediately alert operators to any anomalies that might require intervention.
Cloud computing and data analytics further support these technologies by offering platforms for data storage, processing, and analysis. They enable manufacturers to harness big data for predictive analytics, improving decision-making and operational efficiency. Looking ahead, future technological developments such as artificial intelligence (AI) and machine learning will likely further enhance these wireless solutions, driving innovation in EV manufacturing and beyond.
Market dynamics
The Role of Wireless Network Solutions for EVs in Shaping the EV Market
Wireless network solutions are playing a transformative role in shaping the dynamics of the EV market. As consumer preferences shift towards smart and connected vehicles, manufacturers are increasingly relying on wireless technologies to meet these demands and stay competitive. The influence of these solutions extends across various aspects of the market, from production efficiencies to consumer experiences.
One of the primary ways wireless network solutions are impacting the market is through their ability to drive innovation in vehicle features. Consumers today expect their vehicles to be more than just modes of transportation; they seek integrated technology that offers convenience, safety, and enhanced driving experiences. Wireless technologies enable features such as over-the-air updates, advanced driver-assistance systems (ADAS), and infotainment systems, which are becoming standard in modern EVs. These features not only meet consumer expectations but also provide manufacturers with a competitive advantage by differentiating their products in a crowded market.
Additionally, wireless network solutions contribute to reducing production costs and time-to-market, which are critical factors in the competitive automotive industry. By enabling real-time data exchange and automation, manufacturers can streamline production processes and make informed decisions that enhance efficiency and reduce waste. This operational efficiency translates to cost savings that can be passed on to consumers, making EVs more accessible and attractive.
The impact of global market shifts and regulatory pressures also influences the adoption of wireless solutions. Governments worldwide are implementing stricter emissions regulations and offering incentives for EV adoption, driving the demand for more efficient and sustainable production methods. Wireless technologies align with these goals by supporting smart manufacturing practices that minimize environmental impact and enhance energy efficiency.
In summary, wireless network solutions are not just tools for enhancing production processes; they are shaping the very nature of the EV market. By driving innovation, reducing costs, and aligning with regulatory demands, these technologies are enabling manufacturers to meet evolving consumer expectations and secure a competitive position in the market.
Click here to read our expertly curated top picks!
Case studies
Successful Applications of Wireless Network Solutions for EVs
Example 1: Tesla's Integration of Advanced Wireless Systems
Tesla has long been a pioneer in the EV industry, and its use of advanced wireless systems is a testament to its innovative approach. The company leverages IoT and 5G technologies to enhance its manufacturing processes and vehicle capabilities. In its Fremont factory, Tesla uses an extensive network of IoT sensors to monitor production lines in real-time, ensuring optimal efficiency and quality control. This integration allows Tesla to quickly identify and rectify any issues that arise, minimizing downtime and enhancing overall productivity. Furthermore, Tesla's vehicles are equipped with wireless connectivity that enables over-the-air updates, allowing the company to provide continual improvements to vehicle software without requiring physical intervention.
Example 2: BMW’s Use of IoT in EV Production
BMW has embraced IoT technology to revolutionize its EV production processes. By implementing smart factories equipped with IoT devices, BMW has achieved significant improvements in quality control and operational efficiency. IoT sensors are strategically placed throughout the production line to collect data on various parameters, such as temperature, pressure, and machine performance. This data is then analyzed in real-time to identify potential defects or inefficiencies, allowing BMW to take proactive measures to address them. The result is a streamlined production process that delivers high-quality vehicles with reduced waste and improved sustainability.
Example 3: Nissan’s Deployment of 5G Networks in Manufacturing
Nissan has taken a bold step in its EV manufacturing by deploying 5G networks to enhance connectivity and automation in its plants. The implementation of 5G technology allows Nissan to achieve real-time monitoring and control of its production processes, enabling greater flexibility and responsiveness. For instance, the use of 5G-powered robotic arms and AGVs has revolutionized Nissan's assembly lines, allowing for precise and efficient operations. This deployment not only improves production efficiency but also positions Nissan as a leader in adopting cutting-edge technologies in the automotive industry.
These case studies illustrate the tangible benefits and transformative impact of wireless network solutions in EV manufacturing. By integrating these technologies, companies like Tesla, BMW, and Nissan are setting new standards for efficiency, quality, and innovation in the automotive sector.
Challenges and solutions
Overcoming Obstacles with Wireless Network Solutions for EVs
Despite the numerous advantages of wireless network solutions in EV manufacturing, there are several challenges that manufacturers must address to fully realize their potential. Security concerns, interoperability issues, and infrastructure costs are among the primary obstacles that can hinder the successful implementation of these technologies.
Security is a significant concern in wireless networks, as the increased connectivity opens up potential vulnerabilities to cyberattacks. To mitigate these risks, manufacturers must prioritize cybersecurity measures, such as implementing robust encryption protocols and continuous network monitoring. Collaborating with cybersecurity experts and investing in advanced security solutions can help safeguard sensitive data and maintain the integrity of manufacturing operations.
Interoperability is another challenge, as the integration of diverse wireless technologies often involves equipment and systems from multiple vendors. This can lead to compatibility issues that disrupt production processes. Standardization efforts, such as developing industry-wide protocols and frameworks, are essential to ensure seamless interoperability among different devices and platforms. Manufacturers can also collaborate with technology partners to develop customized solutions that address specific interoperability challenges.
Infrastructure costs can be a barrier, especially for small and medium-sized manufacturers with limited budgets. The initial investment in wireless technologies, including hardware, software, and network infrastructure, can be substantial. However, manufacturers can explore cost-effective strategies, such as phased implementation and leveraging cloud-based solutions, to minimize upfront costs. Additionally, government incentives and subsidies for adopting smart manufacturing technologies can further alleviate financial constraints.
Project managers play a critical role in navigating these challenges and ensuring the successful integration of wireless network solutions. By understanding the unique needs of their operations and collaborating with technology partners, project managers can develop comprehensive implementation plans that address potential obstacles. Staying informed about industry trends and best practices will also equip project managers with the knowledge needed to overcome challenges and drive innovation in EV manufacturing.
Click here to read our expertly curated top picks!
Regulatory and ethical considerations
Compliance and Ethical Practices
The deployment of wireless network solutions in EV manufacturing is subject to various regulatory and ethical considerations that manufacturers must navigate to ensure compliance and ethical practices. Regulatory requirements often involve standards for data security, privacy, and environmental impact, all of which have implications for the strategic planning and decision-making processes in EV production projects.
Data privacy is a critical concern, as wireless networks collect and transmit vast amounts of data, some of which may be sensitive in nature. Manufacturers must adhere to data protection regulations, such as the General Data Protection Regulation (GDPR) in Europe, to safeguard personal data and ensure the privacy of individuals. Implementing data encryption, access controls, and anonymization techniques can help manufacturers comply with these regulations and protect sensitive information.
Environmental impact is another area of concern, as the increased use of wireless technologies can contribute to energy consumption and electronic waste. Manufacturers should consider the environmental implications of their technology choices and implement sustainable practices to minimize their carbon footprint. This may involve optimizing energy efficiency, recycling electronic waste, and using eco-friendly materials in the production process.
Ethical considerations also extend to the social impact of wireless technologies, such as the potential displacement of workers due to increased automation. Manufacturers should consider the broader social implications of their technology investments and develop strategies to support workforce development and retraining. Engaging in transparent communication with stakeholders and fostering a culture of ethical responsibility can help manufacturers navigate these complex issues.
To maintain compliance and ensure ethical practices, manufacturers should stay informed about relevant regulations and industry standards. Collaborating with regulatory bodies and industry associations can provide valuable guidance and support in navigating the complex regulatory landscape. By prioritizing compliance and ethical considerations, manufacturers can build trust with stakeholders and contribute to the responsible and sustainable advancement of the EV industry.
Click here to read our expertly curated top picks!
Tips for project managers: do’s and don’ts
Do's | Don'ts |
---|---|
Embrace innovation and stay updated with technological trends. | Avoid neglecting the importance of cybersecurity. |
Collaborate closely with technology experts and stakeholders. | Don't rush the implementation process without proper testing. |
Prioritize data privacy and ethical considerations. | Don’t overlook the need for continuous personnel training. |
Set clear objectives and monitor progress regularly. | Avoid ignoring the regulatory compliance requirements. |
Invest in scalable and flexible solutions for future growth. | Don’t underestimate the importance of infrastructure assessment. |
Click here to read our expertly curated top picks!
Conclusion
Key Takeaways
The integration of wireless network solutions in EV manufacturing is transforming the industry, offering significant benefits in terms of efficiency, innovation, and sustainability. By leveraging technologies like IoT, 5G, and edge computing, manufacturers can enhance connectivity, automate processes, and meet evolving consumer demands for smart and connected vehicles. The journey toward fully realizing the potential of these technologies involves navigating challenges related to security, interoperability, and infrastructure costs. However, with strategic planning, collaboration, and a focus on compliance and ethical practices, manufacturers can overcome these obstacles and position themselves for future success.
For professionals and aspiring project managers in the EV sector, staying adaptive and proactive in adopting wireless solutions is crucial. By embracing innovation and investing in cutting-edge technologies, they can drive operational excellence and secure a competitive advantage in the market. The future of EV manufacturing lies in the continued advancement and integration of wireless network solutions, making it imperative for industry leaders to remain committed to innovation and continuous improvement.
All You Need for Project Management is in Meegle!
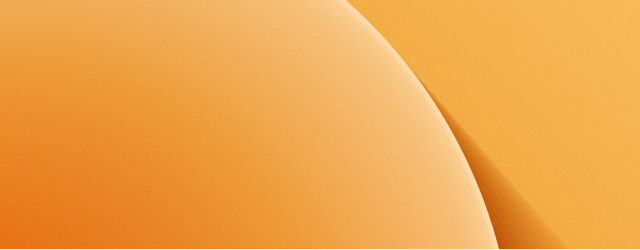
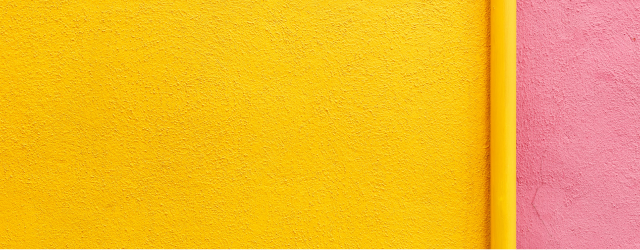
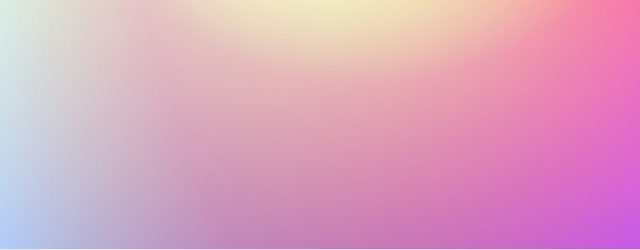
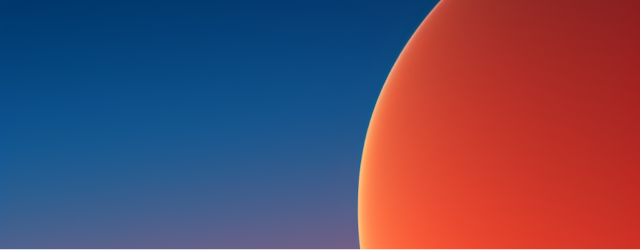
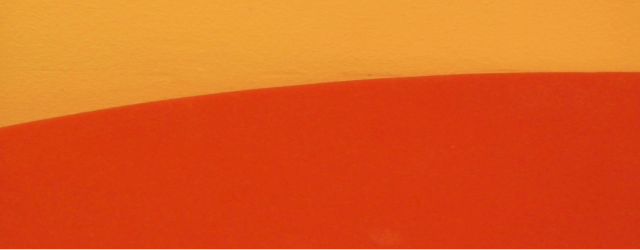
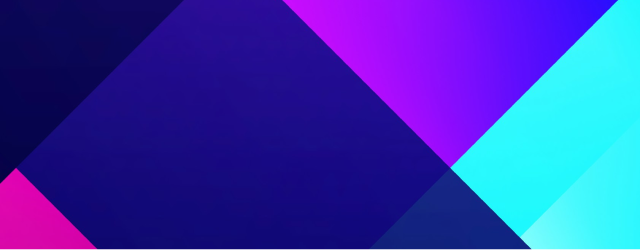
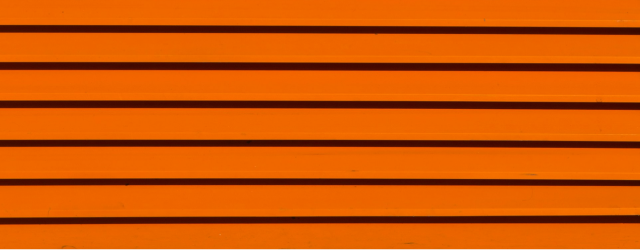
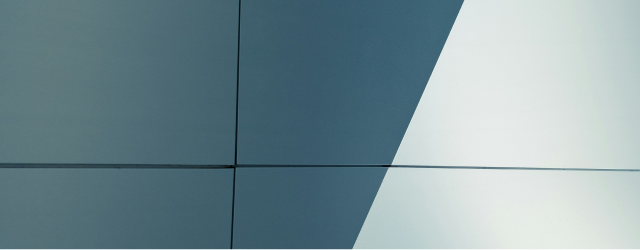