Automation In Food Safety
Uncover crucial insights into Automation in Food Safety, understanding their impact, challenges, and future trends in the dynamic landscape of the food industry.
Overview of Automation in Food Safety
Automation in food safety refers to the integration of advanced technologies like artificial intelligence (AI), the Internet of Things (IoT), and robotics into food safety protocols to enhance efficiency and reliability. In recent years, the food industry has witnessed a significant shift towards automated systems designed to streamline processes, reduce human error, and ensure compliance with stringent food safety standards. Automation is pivotal in modern food safety management, where it plays a crucial role in monitoring and controlling food production and distribution stages.
The integration of AI in food safety allows for predictive analytics, which can forecast potential risks before they become critical issues. IoT devices, such as smart sensors and connected systems, enable real-time monitoring of environmental conditions, ensuring optimal storage and transportation conditions. Robotics, on the other hand, facilitate automation in food processing and packaging, reducing human intervention and enhancing hygiene standards.
Current trends in automation within food safety practices include the widespread adoption of blockchain technology for traceability, the use of machine learning to improve quality control, and the implementation of autonomous systems for inspection and quality assurance. These technologies not only streamline operations but also provide a reliable framework for maintaining food safety standards in a globalized market.
Importance of Automation in Food Safety
Automation is critically important in ensuring efficient, accurate, and reliable food safety practices. The global food industry is characterized by its increasing complexity and scale, driven by consumer demand for diverse food products and international food trade. This complexity brings unique challenges in maintaining food safety, which automation effectively addresses.
With automated systems, food manufacturers can ensure compliance with global food safety regulations, such as the Food Safety Modernization Act (FSMA) in the United States and the European Union's General Food Law. Automation facilitates the traceability of food products, making it easier to identify and address contamination sources quickly. Additionally, the real-time data collection and analysis enabled by automation technologies allow for proactive decision-making, reducing the risk of foodborne illnesses.
Automation also plays a vital role in satisfying consumer expectations for safe and high-quality food products. As consumers become more informed and cautious about food safety, they demand transparency and accountability from food producers. Automated systems provide detailed insights into the food production process, enhancing consumer trust and confidence in food safety management.
All You Need for Project Management is Free in Meegle
Historical development of automation in food safety
Origins and Evolution
The origins of automation in food safety can be traced back to the industrial revolution when mechanization began to play a role in food production. However, the real evolution of food safety automation began in the late 20th century with the advent of computer technology and digital systems. During this period, the food industry started adopting computerized systems for quality control and monitoring, marking a significant shift from manual processes.
Key milestones in the evolution of food safety automation include the development of HACCP (Hazard Analysis Critical Control Point) systems, which introduced systematic preventive approaches to food safety. The introduction of AI and IoT in the early 21st century further revolutionized food safety practices, enabling real-time data collection and predictive analytics.
Cultural and economic factors have also driven the adoption of automation in food safety. Globalization has expanded food supply chains, increasing the need for efficient and standardized safety protocols. Additionally, economic pressures have pushed the food industry to seek cost-effective solutions, making automation an attractive option.
Impact on the Food Industry
Automation has transformed the food industry significantly in terms of efficiency, safety, and quality. By automating repetitive tasks, food manufacturers have achieved greater precision and consistency in food processing, reducing human error and contamination risks. Enhanced safety measures have not only improved product quality but also increased consumer trust.
Specific sectors within the food industry, such as dairy, meat processing, and beverages, have been notably impacted by automation. For example, the dairy industry uses automated pasteurization systems to ensure milk safety, while meat processors employ robotic systems for cutting and packaging, enhancing hygiene and reducing contamination.
The ripple effects of automation in food safety extend to global food supply chains and consumer expectations. With improved traceability and transparency, food producers can quickly respond to food safety incidents, minimizing disruptions in supply chains. Moreover, consumers benefit from safer food products and more information about their origins and handling processes, influencing purchasing decisions.
Technical aspects and implementation
Core Technologies
A range of cutting-edge technologies underpins food safety automation, including sensors, AI-powered systems, and robotics. Sensors are crucial in monitoring environmental conditions, such as temperature and humidity, to ensure optimal storage and transport. These devices provide real-time data, enabling quick adjustments to prevent spoilage and contamination.
AI-powered systems offer advanced capabilities in predictive analytics, allowing food producers to anticipate potential safety risks based on historical data and current conditions. Machine learning algorithms analyze complex datasets, identifying patterns and anomalies that could indicate contamination or quality issues. Robotics are also integral to food safety automation, performing tasks such as sorting, packaging, and inspection with precision and consistency.
Advancements in data analytics and predictive modeling further enhance food safety measures. By leveraging big data, food producers can gain insights into consumer behavior, production inefficiencies, and emerging risks, enabling proactive decision-making and continuous improvement.
Implementation in Food Processes
Implementing automation in food processes involves integrating advanced technologies into production, processing, and distribution stages. In food production, automated systems monitor raw material quality, optimizing recipes and formulations to ensure consistency. During processing, robotics and sensors maintain hygiene standards, reducing contamination risks.
One concrete example is the use of IoT devices in cold chain management. These devices track temperature and humidity levels during transportation, ensuring that perishable goods remain within safe ranges. If deviations occur, alerts are sent to operators for corrective actions, preventing spoilage.
Automation also integrates with existing systems and processes in the food industry, enhancing efficiency without disrupting operations. For instance, AI-powered software can overlay traditional quality control measures, providing deeper insights and reducing manual inspections.
Real-time monitoring and control of food safety variables are vital for maintaining consistent product quality. Automated systems enable continuous data collection and analysis, allowing for quick adjustments and immediate responses to emerging risks, ensuring that food products meet safety standards throughout their lifecycle.
Click here to utilize our free project management templates!
Benefits and challenges
Advantages of Utilizing Automation in Food Safety
The benefits of utilizing automation in food safety are manifold. Improved accuracy and consistency in food safety practices are among the most significant advantages. Automated systems minimize human error, ensuring precise execution of safety protocols and reducing contamination risks.
Efficiency is another key benefit, as automation streamlines operations and eliminates repetitive tasks. This efficiency translates into cost savings for food producers, who can allocate resources more effectively and reduce waste. Additionally, automation allows for scalability, enabling food manufacturers to expand operations without compromising safety standards.
Business operations benefit from automation through enhanced competitiveness. Companies that adopt automated systems can offer safer and higher-quality products, attracting consumers and gaining a competitive edge in the market. Moreover, automation facilitates compliance with regulations, reducing the risk of legal issues and ensuring adherence to food safety standards.
Challenges and Considerations
Despite its advantages, integrating automation technologies in food safety presents several challenges. Resistance to change is a common hurdle, as employees may be hesitant to adopt new technologies. To address this, companies must invest in training and stakeholder engagement to ensure a smooth transition.
High initial costs can also deter companies from implementing automation. While the long-term benefits outweigh these costs, initial investments in technology and infrastructure can be significant. Technical and operational hurdles, such as system integration and maintenance, require careful planning and execution.
Ethical and regulatory considerations must be addressed when implementing automation in food safety. Ensuring compliance with food safety standards and regulations is paramount, and automated systems must be designed to meet these requirements. Additionally, ethical concerns related to job displacement and privacy must be considered to ensure a balanced approach to automation.
Case studies and practical applications
Real-world examples
Real-world examples
Numerous real-world examples illustrate the successful implementation of automation in food safety. A major food manufacturer, for instance, has adopted robotics for quality control and inspection. These robots perform tasks such as sorting and packaging with precision, reducing human error and contamination risks. The result is improved product quality and safety, enhancing consumer trust and satisfaction.
In the distribution sector, a company uses IoT devices to track and ensure cold chain integrity. These devices monitor temperature and humidity during transportation, sending alerts if conditions deviate from safe ranges. This real-time monitoring ensures that perishable goods arrive at their destination in optimal condition, reducing spoilage and waste.
A food service provider has leveraged AI for predictive analytics to prevent foodborne illnesses. By analyzing data from various sources, including customer feedback and health reports, the AI system identifies potential risks and recommends preventive measures. This proactive approach has reduced the incidence of foodborne illnesses, safeguarding consumer health and enhancing the provider's reputation.
Lessons learned
Lessons learned
Successful case studies in food safety automation offer valuable lessons for future endeavors. Best practices include comprehensive stakeholder engagement, where employees and management collaborate to ensure smooth implementation and operation of automated systems. Continuous monitoring and evaluation of automation projects are essential for identifying areas of improvement and optimizing system performance.
These lessons emphasize the importance of adaptability and innovation in automation projects. By learning from successful implementations, companies can refine their approaches and explore new opportunities for automation in food safety. Collaboration and knowledge sharing among industry professionals can drive advancements and improve food safety standards across the board.
Click here to utilize our free project management templates!
Future trends and innovations
Emerging Trends
The future of food safety automation is poised for exciting developments, with several emerging trends set to transform the industry. One such trend is the increased integration of blockchain technology for traceability. Blockchain offers secure and transparent tracking of food products, enhancing accountability and trust in supply chains.
Machine learning is expected to play a growing role in predictive food safety management. By analyzing vast datasets, machine learning algorithms can identify patterns indicative of potential risks, enabling proactive interventions and reducing the incidence of foodborne illnesses.
As these trends unfold, their implications for the future of food safety automation are profound. Companies that embrace these technologies will gain a competitive edge, offering safer and higher-quality products while meeting evolving consumer demands for transparency and accountability.
Innovations on the Horizon
Innovations on the horizon promise to further enhance food safety practices. Autonomous systems for food inspection are being developed, offering the potential for more efficient and accurate assessments of food quality and safety. These systems can operate independently, providing continuous monitoring and reducing reliance on human inspectors.
Augmented reality is another promising technology, with applications in training and operational efficiency in food safety. AR can provide immersive training experiences for employees, enhancing their understanding of safety protocols and procedures. Additionally, AR can assist in real-time monitoring and decision-making, offering visual insights into food production processes.
These innovations could significantly enhance consumer trust in food safety practices, offering greater transparency and accountability. As companies adopt these technologies, they will be better equipped to meet the challenges of an increasingly complex and demanding food industry.
Click here to utilize our free project management templates!
Tips for automation in food safety integration
Do's | Don'ts |
---|---|
Conduct thorough research on available technologies | Rush into adopting automation without proper planning |
Engage stakeholders in the decision-making process | Ignore the importance of staff training and development |
Continuously monitor and evaluate the effectiveness of automation | Overlook compliance with regulatory standards |
Click here to utilize our free project management templates!
Conclusion
Summary of Key Insights
Automation technologies are revolutionizing food safety practices, offering enhanced efficiency, accuracy, and reliability. By integrating AI, IoT, and robotics, the food industry achieves consistent adherence to safety standards, reducing human error and contamination risks. Automation facilitates compliance with regulations, improves traceability, and boosts consumer trust, offering safer and higher-quality food products. Despite challenges such as resistance to change and high initial costs, the benefits of automation far outweigh these hurdles, providing valuable opportunities for innovation and growth in the food industry.
Encouraging Further Exploration
The transformative role of automation in food safety underscores the importance of ongoing innovation and adaptation. Industry professionals are encouraged to explore new opportunities for automation, leveraging emerging technologies to enhance food safety practices. Collaboration and knowledge sharing among stakeholders can drive advancements and improve safety standards across the board. By embracing automation, the food industry can meet evolving consumer demands and regulatory requirements, ensuring safe and high-quality food products for all.
All You Need for Project Management is Free in Meegle
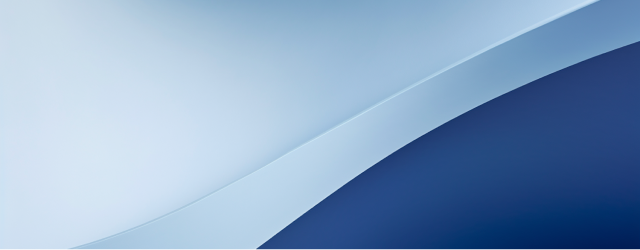
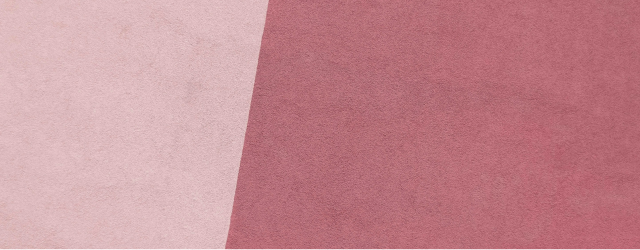
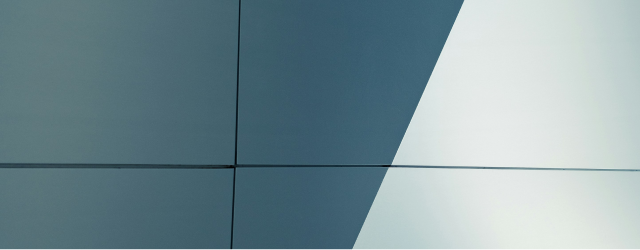
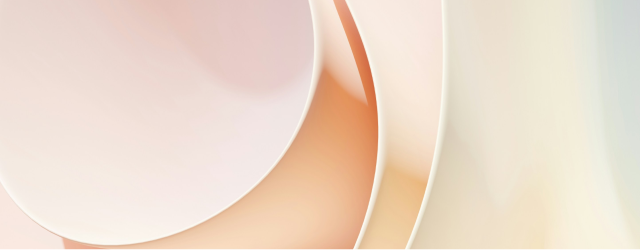
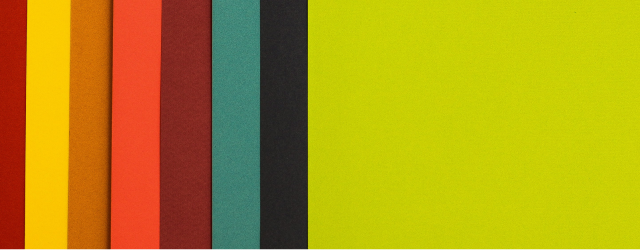
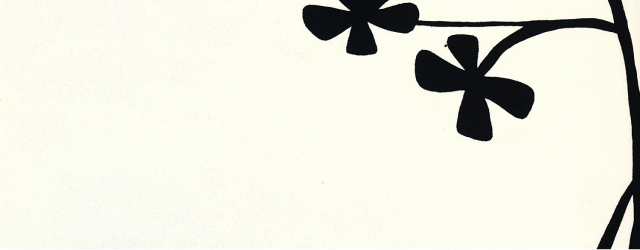
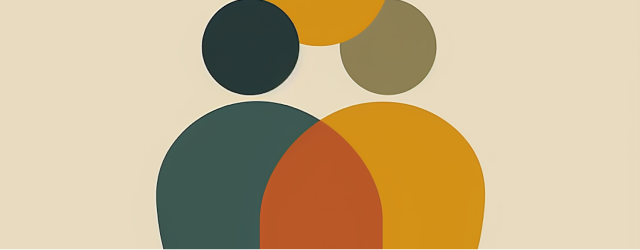
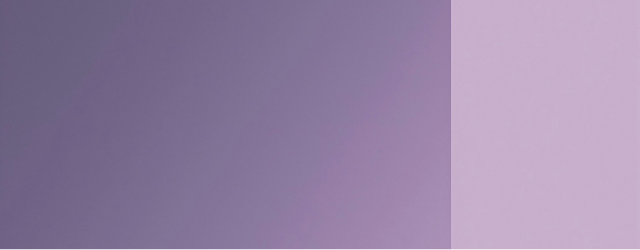