Robot Locomotion
Gain essential insights into how Robot locomotion are shaping the future of robotics, complete with industry data and practical how-to guides.
Understanding the Role of Motion in Robotics
Robot locomotion is the driving force behind a robot's ability to move and perform tasks within its environment. This aspect of robotics is essential for enabling machines to carry out complex functions that require interaction with their surroundings. At its core, robot locomotion involves the mechanisms and technologies that allow robots to navigate spaces—whether it's the controlled environment of a factory floor or the unpredictable terrain of a disaster site. The relevance of locomotion in advancing technology cannot be overstated, as it directly impacts the efficiency and effectiveness of robotic systems. For instance, in logistics, robots equipped with advanced locomotion capabilities can autonomously navigate warehouses, improving the speed and accuracy of inventory management.
The implications of robot locomotion extend beyond current applications to future innovations. As robotics continues to evolve, the ability of robots to adapt to new environments and tasks will play a pivotal role in their development. Concepts like swarm robotics, where multiple robots work together seamlessly, rely heavily on advanced locomotion to ensure coordination and efficiency. Thus, understanding the dynamics of robotic movement is crucial for anyone involved in the design, implementation, or management of robotic systems.
Experience a New Level of Productivity in Meegle
Definition and relevance of robot locomotion
Elucidating the Core of Robotic Movement
Robot locomotion refers to the mechanisms by which robots achieve movement. This encompasses a range of technologies and designs aimed at facilitating the movement of a robot from one point to another, whether through walking, flying, swimming, or rolling. The definition of robot locomotion is broad, as it includes various forms of movement, each suited to different environments and tasks. For instance, wheeled locomotion is ideal for flat surfaces and is commonly used in industrial settings, while legged locomotion is better suited for uneven or complex terrains, such as those encountered in exploration or rescue missions.
The relevance of robot locomotion in robotics is significant, as it determines the practical applications and limitations of robotic systems. In the context of automation, locomotion is crucial for tasks that require navigation and precision. For example, in agriculture, robots equipped with sophisticated locomotion systems can traverse fields autonomously, performing tasks such as planting, monitoring, and harvesting crops with minimal human intervention. This capability not only increases productivity but also reduces the need for manual labor, addressing labor shortages and enhancing the overall efficiency of the agricultural sector.
Moreover, the importance of robot locomotion extends to research and development in robotics. Engineers and scientists continuously strive to improve locomotion technologies to create robots that are more adaptable and capable of performing a wider range of tasks. This ongoing research is critical for pushing the boundaries of what is possible in robotics, paving the way for future advancements that could redefine entire industries.
Click here to read our expertly curated top picks!
Importance of robot locomotion in modern technological advancements
The Driving Force Behind Innovation and Efficiency
The role of robot locomotion in modern technological advancements is both profound and far-reaching. As industries across the globe seek to enhance efficiency and innovation, robotic systems equipped with advanced locomotion capabilities are becoming indispensable. One of the primary impacts of robot locomotion is its ability to enable new capabilities that were previously unattainable. For instance, in the healthcare sector, robots with precise locomotion systems are being used for surgeries, delivering medications, and even providing companionship to patients, revolutionizing patient care and operational efficiency.
In the realm of manufacturing, robot locomotion is transforming production lines by allowing robots to move seamlessly between different tasks. This flexibility not only increases productivity but also reduces downtime and costs associated with reconfiguring production lines. According to a report by the International Federation of Robotics, the adoption of automation technologies, including advanced locomotion, could boost global manufacturing productivity by up to 30% by 2025. Such statistics underscore the critical role of locomotion in driving technological progress.
Furthermore, the integration of robot locomotion into existing technologies often leads to enhancements that improve overall system performance. For example, autonomous vehicles rely heavily on advanced locomotion systems to navigate complex environments safely and efficiently. These systems integrate sensors, machine learning algorithms, and real-time data processing to ensure accurate and reliable movement, significantly contributing to the development of self-driving technology.
In summary, the importance of robot locomotion in modern technological advancements cannot be overstated. Its impact on innovation and efficiency is evident across various sectors, driving new capabilities and enhancing existing technologies. As we continue to explore the potential of robotics, the advancement of locomotion systems will remain a key focus for researchers, engineers, and project managers alike.
Origins and evolution of robot locomotion
Tracing the Journey from Inception to Innovation
The evolution of robot locomotion is a fascinating journey marked by significant milestones and breakthroughs that have shaped the field. The origins of robot locomotion can be traced back to the early 20th century when the first rudimentary robots were developed. These early machines, often inspired by animal and human movement, laid the groundwork for future innovations in robotic mobility. One of the earliest examples of robotic locomotion was the "Elektro" robot, unveiled at the 1939 New York World's Fair, which could walk and perform simple tasks.
As technology advanced, so did the capabilities of robotic locomotion systems. The 1960s and 70s saw the development of more sophisticated robots, driven by the need for automation in manufacturing and other industries. During this period, significant progress was made in the design of wheeled robots, which became a staple in industrial automation due to their efficiency and ease of control. A notable example is the Stanford Cart, developed in the late 1960s, which was one of the first robots to demonstrate autonomous navigation.
The 1980s and 90s marked a pivotal era for robot locomotion, as researchers began to explore alternative forms of movement, such as legged locomotion and flying robots. This period saw the introduction of robots like the Honda ASIMO, a humanoid robot capable of walking and running, demonstrating the potential of advanced locomotion in robotics. The development of flying robots, or drones, also gained momentum during this time, opening new possibilities for applications in surveillance, agriculture, and beyond.
Today, the field of robot locomotion is characterized by rapid innovation and the integration of cutting-edge technologies. The advent of artificial intelligence and machine learning has revolutionized locomotion systems, enabling robots to learn from their environment and adapt their movement accordingly. Additionally, advances in materials science and engineering have led to the creation of lightweight and flexible robots, capable of traversing a wide range of terrains. As we look to the future, the evolution of robot locomotion promises to continue, driving new capabilities and expanding the horizons of what is possible in robotics.
Click here to read our expertly curated top picks!
How robot locomotion works
Unpacking the Mechanics of Robotic Mobility
The operation of robot locomotion is a complex process that involves a combination of mechanical, electronic, and software components working in harmony to achieve movement. At the heart of any locomotion system are the actuators, which are responsible for converting energy into motion. These can be electric motors, hydraulic systems, or pneumatic devices, each offering different advantages depending on the application. For instance, electric motors are commonly used in wheeled robots due to their efficiency and control, while hydraulic systems are favored in applications requiring high power and force, such as robotic arms.
The principles of movement in robot locomotion are governed by kinematics and dynamics, which dictate how a robot can move and interact with its environment. Kinematics focuses on the geometry of motion, determining the possible positions and orientations of a robot's limbs or wheels. Dynamics, on the other hand, considers the forces and torques required to achieve those movements. Understanding these principles is crucial for designing locomotion systems that are both efficient and effective.
Sensors play a critical role in robot locomotion, providing the data necessary for navigation and control. These can include cameras, LIDAR, accelerometers, and gyroscopes, which help the robot understand its surroundings and adjust its movement accordingly. For example, autonomous vehicles rely on a combination of sensors and GPS technology to navigate roads safely, while drones use onboard cameras and accelerometers to maintain stability during flight.
The integration of software and algorithms is another key component of robot locomotion. Control algorithms determine how a robot responds to sensor inputs and navigates its environment. Machine learning techniques are increasingly being used to enhance these algorithms, allowing robots to learn from their experiences and improve their performance over time. This capability is particularly important in applications where robots must adapt to dynamic and unpredictable environments, such as search and rescue missions.
In summary, the mechanics of robot locomotion involve a complex interplay of components and principles designed to achieve efficient and effective movement. By understanding these dynamics, engineers and project managers can design robust and adaptable robotic systems capable of meeting the demands of a wide range of applications.
Utilizing robot locomotion
Real-World Applications and Success Stories
The utilization of robot locomotion extends across a diverse array of industries, demonstrating its versatility and effectiveness in solving real-world problems. In healthcare, for instance, robots with advanced locomotion capabilities are revolutionizing patient care. Robotic surgical systems, such as the da Vinci Surgical System, use precise movement to perform minimally invasive procedures with high accuracy, reducing recovery times and improving patient outcomes.
In the logistics and warehousing sector, robot locomotion is streamlining operations by automating the movement of goods. Companies like Amazon and Walmart have integrated autonomous robots into their supply chains, with robots efficiently navigating warehouses to pick, pack, and transport items. This not only speeds up the process but also reduces labor costs and minimizes errors. A study by McKinsey & Company highlights that automation in logistics, fueled by advancements in locomotion, could lead to a 30% reduction in logistics costs by 2030.
Agriculture is another sector benefiting from the application of robot locomotion. Autonomous tractors and drones equipped with sophisticated locomotion systems are transforming farming practices by performing tasks such as planting, monitoring, and harvesting crops. These technologies enhance productivity and allow for precision agriculture, where farmers can optimize resource use and crop yields.
A notable case study is the use of robot locomotion in disaster response. During the Fukushima nuclear disaster, robots equipped with advanced locomotion systems were deployed to navigate hazardous environments and perform critical tasks, such as assessing damage and retrieving vital data. These robots were able to access areas that were too dangerous for humans, demonstrating the life-saving potential of robotic mobility.
In summary, the utilization of robot locomotion across various industries showcases its ability to enhance efficiency, accuracy, and safety. These real-world applications highlight the transformative impact of locomotion technologies and underscore the importance of continued innovation in this field.
Related:
Feature Management TemplateClick here to read our expertly curated top picks!
Advantages of implementing robot locomotion
Enhancements in Efficiency and Productivity
The implementation of robot locomotion in robotic systems offers numerous advantages that translate into tangible improvements in industrial and commercial applications. One of the primary benefits is the enhancement of efficiency and productivity. Robots equipped with advanced locomotion capabilities can perform tasks faster and more accurately than their human counterparts, reducing production times and minimizing errors. This is particularly evident in manufacturing environments, where robots with precise locomotion systems are used for tasks such as assembly, welding, and painting.
Another significant advantage of robot locomotion is its ability to operate in environments that are hazardous or inaccessible to humans. In industries such as mining, oil and gas, and construction, robots with locomotion systems can navigate dangerous terrains and perform tasks such as inspection and maintenance, improving safety and reducing the risk of accidents. According to a report by the International Robotics Federation, the adoption of robotics in hazardous environments can lead to a 25% reduction in workplace accidents.
The flexibility offered by robot locomotion is also a key advantage, allowing robots to adapt to changing tasks and environments. In logistics, for example, robots can be reprogrammed to handle different types of goods or navigate different warehouse layouts, providing agility and scalability. This flexibility is particularly valuable in industries where demand and production requirements fluctuate, enabling companies to respond quickly and efficiently.
In addition to these operational benefits, the implementation of robot locomotion can also lead to cost savings. By automating repetitive and labor-intensive tasks, companies can reduce labor costs and increase output, leading to higher profitability. A study by Deloitte highlights that companies implementing advanced robotics and automation technologies can achieve cost savings of up to 20% within the first year of adoption.
In conclusion, the advantages of implementing robot locomotion are manifold, driving improvements in efficiency, productivity, safety, and cost-effectiveness. As industries continue to embrace automation, the role of locomotion technologies will remain central to achieving these benefits and unlocking new opportunities for growth and innovation.
Click here to read our expertly curated top picks!
Challenges and solutions
Overcoming Obstacles in Robotic Mobility
The use of robot locomotion is not without its challenges. One common issue is the complexity of designing locomotion systems that can adapt to a wide range of environments. This requires a deep understanding of kinematics, dynamics, and control theory, as well as the ability to integrate multiple components seamlessly. To address this challenge, engineers often employ simulation tools and modeling software to test and refine designs before physical implementation.
Another challenge is ensuring reliability and robustness in locomotion systems, particularly in harsh or unpredictable environments. Factors such as terrain variability, weather conditions, and obstacles can significantly impact a robot's ability to move effectively. Solutions to these challenges include the use of robust sensors and feedback systems, as well as the development of adaptive control algorithms that allow robots to adjust their movement in real-time.
Power management is also a critical challenge in robot locomotion, especially for autonomous systems that require long operating times. Efficient energy use is essential to maximize battery life and ensure continuous operation. Engineers can address this by optimizing the design of locomotion systems for energy efficiency, as well as implementing power-saving strategies and advanced battery technologies.
Lastly, safety is a paramount concern in the deployment of robots with locomotion capabilities, particularly in environments where they interact with humans. Ensuring that robots can operate safely requires rigorous testing and the implementation of fail-safes and emergency protocols. This may involve the use of advanced sensors and machine learning techniques to detect and respond to potential hazards.
By identifying and addressing these challenges, engineers and project managers can enhance the reliability, efficiency, and safety of robot locomotion systems, ensuring their successful deployment and operation in a wide range of applications.
Future prospects of robot locomotion
Anticipating Innovations and Impact
The future of robot locomotion is poised for exciting innovations and developments that will further enhance the capabilities of robotic systems. As technology continues to evolve, several trends are anticipated to shape the future of locomotion in robotics.
One significant trend is the integration of artificial intelligence and machine learning into locomotion systems. These technologies have the potential to revolutionize robotic movement by enabling robots to learn from their environment and adapt their behavior accordingly. This could lead to the development of self-learning robots capable of performing complex tasks in dynamic and unpredictable environments, such as disaster response and exploration.
Advancements in materials science are also expected to play a crucial role in the future of robot locomotion. The development of lightweight, flexible, and durable materials will allow for the creation of robots that can move more efficiently and navigate a wider range of terrains. This could lead to innovations such as soft robotics, where robots mimic the flexibility and adaptability of biological organisms.
The continued miniaturization of components and the development of micro-robots are another area of focus. These tiny robots, equipped with advanced locomotion systems, could be used for applications such as medical diagnostics and environmental monitoring, where precision and agility are paramount.
Additionally, the rise of collaborative robots, or cobots, is expected to impact the future of locomotion. These robots are designed to work alongside humans, requiring advanced locomotion systems to ensure safe and efficient interaction. The development of cobots will likely drive further advancements in locomotion technologies, emphasizing adaptability, safety, and human-robot collaboration.
In conclusion, the future prospects of robot locomotion are promising, with innovations on the horizon that are set to redefine the capabilities of robotic systems. As these technologies continue to evolve, they will undoubtedly have a profound impact on the field of robotics, driving new opportunities for innovation and growth.
Click here to read our expertly curated top picks!
Summary and final thoughts
Recapping Key Insights and Encouragement
Throughout this comprehensive exploration of robot locomotion, we have delved into the principles, applications, and future potential of this critical aspect of robotics. We began by understanding the significance of locomotion in enabling robots to move and interact with their environment, highlighting its transformative impact across various industries.
The definition and relevance of robot locomotion were clarified, emphasizing its importance in achieving tasks that require movement and navigation. We explored its crucial role in modern technological advancements, driving innovation and efficiency across sectors such as healthcare, logistics, and agriculture.
The origins and evolution of robot locomotion were traced, showcasing key milestones and breakthroughs that have shaped the field. We unpacked the mechanics of robotic mobility, providing a technical exploration of how locomotion operates and the components involved.
Real-world applications and success stories demonstrated the versatility and effectiveness of robot locomotion in solving real-world problems, while the advantages of implementing locomotion systems highlighted tangible improvements in efficiency, productivity, and safety.
A step-by-step guide to integrating robot locomotion into robotic systems provided practical insights for successful implementation, while challenges and solutions offered strategies for overcoming common obstacles in robotic mobility.
Finally, we explored future prospects, anticipating innovations that will further enhance the capabilities of robotic systems and their impact on the field of robotics.
In closing, the exploration of robot locomotion underscores the importance of staying abreast of innovations in this field. As technology continues to evolve, understanding the dynamics of locomotion will be crucial for industry professionals looking to harness the full potential of robotics. By embracing these advancements, we can drive new opportunities for growth and innovation, shaping a future where robots play an integral role in our daily lives.
Click here to read our expertly curated top picks!
Examples of robot locomotion in action
Example: autonomous vehicles
Example: autonomous vehicles
Robot locomotion plays a pivotal role in enabling autonomous vehicles to navigate complex environments safely and efficiently. These vehicles rely on sophisticated locomotion systems that integrate sensors, cameras, and machine learning algorithms to understand and respond to their surroundings. For instance, Tesla's Autopilot system uses advanced locomotion technologies to manage tasks such as lane keeping, adaptive cruise control, and automatic parking. These capabilities allow autonomous vehicles to operate with minimal human intervention, paving the way for safer and more efficient transportation.
Example: humanoid robots
Example: humanoid robots
Humanoid robots utilize advanced locomotion techniques to mimic human movement, enhancing their usability in various applications. One of the most renowned examples is Boston Dynamics' Atlas, a bipedal robot capable of walking, running, and even performing backflips. The robot's locomotion system is designed to balance and adapt to different terrains, making it suitable for tasks that require human-like agility. This capability is particularly valuable in industries such as healthcare and customer service, where robots can assist with tasks traditionally performed by humans.
Example: industrial robots
Example: industrial robots
In manufacturing, robot locomotion is crucial for performing tasks that require precision and agility on production lines. Robots equipped with wheeled or tracked locomotion systems can move seamlessly between different stations, performing tasks such as assembly, welding, and painting. For example, Fanuc's robotic arms use advanced locomotion systems to achieve high precision and repeatability, ensuring consistent quality and efficiency in production processes. This application of robot locomotion enhances productivity and reduces operational costs, demonstrating its impact on industrial automation.
Experience a New Level of Productivity in Meegle
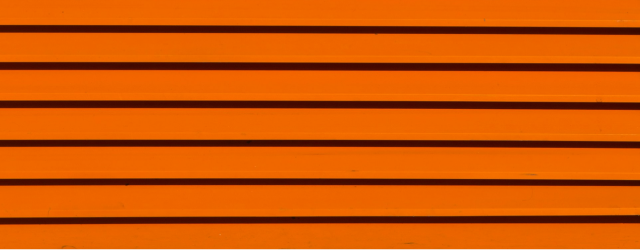
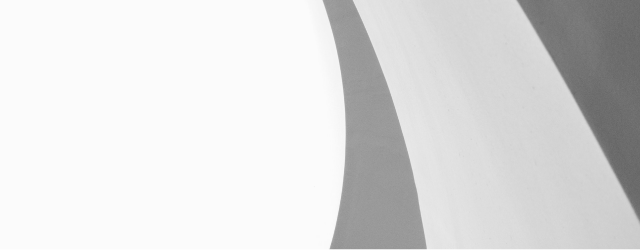
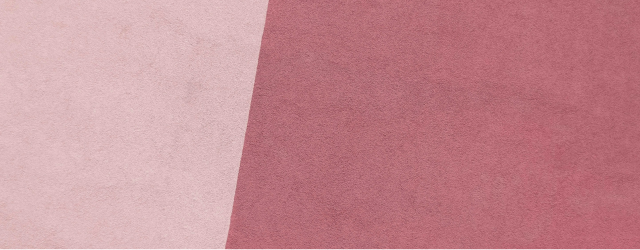
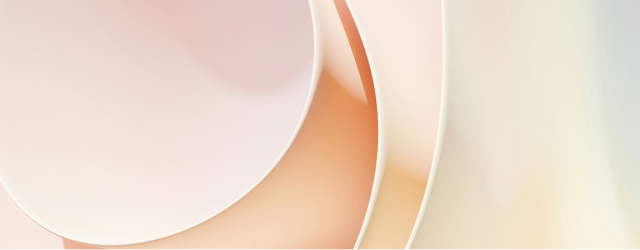
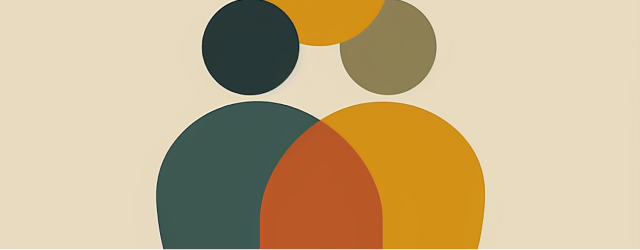
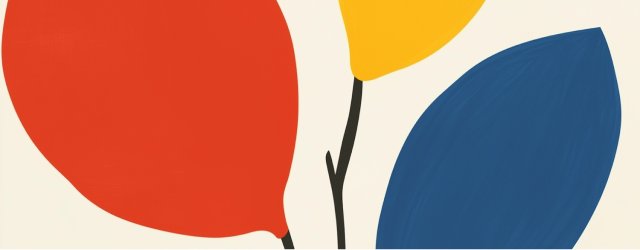
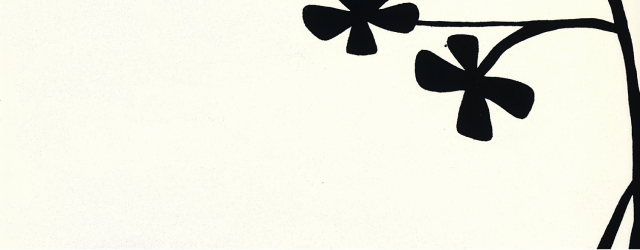