Robot Sensors
Gain essential insights into how Robot sensors are shaping the future of robotics, complete with industry data and practical how-to guides.
Understanding the Backbone of Robotics
In the realm of robotics, sensors are the critical enablers that provide robots with the ability to perceive and interpret their surroundings. These sensors collect crucial data and transmit it to the robot's control systems, allowing for intelligent decision-making and autonomous task execution. The relevance of robot sensors transcends industries, finding utility in manufacturing, healthcare, logistics, and even autonomous vehicles. For instance, in manufacturing, sensors are used to detect defects and ensure quality control. In healthcare, they enable precision in surgical robots. Understanding the intricate roles and capabilities of these sensors is imperative for harnessing the full potential of robotics in any professional field.
The application of robot sensors in autonomous vehicles exemplifies their importance. Here, sensors like LIDAR, cameras, and radar are used to perceive the environment, detect obstacles, and make real-time decisions for navigation. This sophisticated level of interaction with the environment is made possible through an array of sensors working in unison, showcasing the importance of robot sensors in modern technological ecosystems.
Moreover, the healthcare industry has seen significant advancements with the integration of sensors into robotic systems. Sensors in surgical robots allow these machines to perform complex surgeries with high precision, reducing the risks associated with human error. This integration demonstrates how robot sensors are not just ancillary components but are central to the functioning and efficiency of robotic systems, driving innovations that make processes safer, faster, and more reliable.
The significance of robot sensors is further highlighted in logistics and warehousing. Here, robots equipped with sensors efficiently manage inventory, track goods, and streamline operations by collecting and analyzing environmental data. The sensors enable robots to identify and pick items accurately, ensuring the supply chain's efficiency and reliability. These examples underscore the importance of understanding robot sensors for anyone looking to leverage robotics in their professional pursuits.
Experience a New Level of Productivity in Meegle
Definition and relevance of robot sensors
Core Components of Intelligent Robotics
Robot sensors are devices integrated into robotic systems to detect changes in the environment and physical conditions. These sensors translate physical quantities such as temperature, pressure, or motion into digital signals that robotic control systems can interpret and act upon. The ability to convert real-world phenomena into actionable data is what makes robot sensors indispensable in the modern technological landscape.
The relevance of robot sensors is underscored by their broad application across multiple domains. In manufacturing, sensors facilitate automation by allowing robots to perceive their environment, adapt to changes, and execute tasks with precision. For example, proximity sensors help in detecting the presence of objects, ensuring that robots can avoid collisions.
In the context of artificial intelligence (AI) and machine learning, sensors play a crucial role in data collection, which is essential for training algorithms. For instance, vision sensors gather visual data that AI systems use to recognize patterns and make predictions. This seamless integration of sensors and AI allows for the development of intelligent systems capable of performing complex tasks autonomously.
Moreover, the rise of the Internet of Things (IoT) has further amplified the relevance of robot sensors. In smart homes, for example, sensors detect temperature, humidity, and occupancy to optimize energy usage and improve comfort. This connectivity and data flow enable real-time monitoring and control, enhancing the efficiency and responsiveness of systems.
The relevance of robot sensors is not limited to operational efficiency; it extends to safety and reliability. In hazardous environments, sensors allow robots to perform tasks without putting human lives at risk. For instance, in nuclear facilities, robots equipped with radiation sensors can safely navigate and execute maintenance tasks. This application of sensors underscores their role in enhancing safety and reliability across various sectors.
Click here to read our expertly curated top picks!
Importance of robot sensors in modern technological advancements
Bridging the Gap Between Digital and Physical Worlds
In contemporary technology, robot sensors are pivotal in bridging the gap between the digital and physical worlds. They enable robots to perform complex tasks with minimal human intervention, offering improvements in safety, precision, and efficiency across various sectors. The importance of robot sensors is clearly illustrated in industries such as manufacturing, healthcare, and transportation.
In the manufacturing sector, robot sensors contribute to automation and quality control. Sensors like vision systems and tactile sensors allow robots to assess product quality, detect defects, and ensure adherence to specifications. This capability not only enhances the efficiency of production lines but also reduces waste and increases profitability. For example, a robotic arm equipped with force sensors can adjust its grip based on the object's weight and fragility, ensuring safe handling of delicate items.
In healthcare, sensors are instrumental in advancing robotic surgery and patient care. Surgical robots equipped with pressure and motion sensors enable surgeons to perform precise and minimally invasive procedures. These sensors provide feedback on the pressure applied, ensuring delicate tissues are not damaged and improving patient outcomes. Moreover, sensors used in patient monitoring devices continuously track vital signs, alerting healthcare professionals to any anomalies.
The transportation industry also benefits significantly from robot sensors, particularly in the development of autonomous vehicles. Sensors such as LIDAR, cameras, and radar systems allow vehicles to perceive their environment, recognize traffic signals, and navigate safely. These sensors collect and process vast amounts of data in real-time, enabling autonomous vehicles to make informed decisions on the road, thereby enhancing safety and efficiency.
As technology advances, the integration of sophisticated sensors is expected to further enhance the capabilities of robotic systems, making them indispensable tools in various industries. The development of more advanced sensors, capable of higher precision and reliability, will continue to drive innovation and efficiency across the board. This underscores the importance of robot sensors in modern technological advancements, highlighting their role in shaping the future of robotics and automation.
Origins and evolution of robot sensors
Tracing the Journey from Rudimentary to Advanced Systems
The evolution of robot sensors is a fascinating journey that highlights the progress from rudimentary systems to sophisticated, multi-functional devices. Initially developed for basic task execution, robot sensors have undergone significant advancements over the decades, bringing robots closer to human-like perception and interaction.
The journey of robot sensors began with the development of simple tactile sensors. These sensors were designed to detect physical contact and were primarily used in manufacturing for assembly line tasks. Over time, advancements in sensor technology led to the development of more complex systems, such as vision sensors capable of capturing and processing visual information.
A critical breakthrough in the evolution of robot sensors was the development of LIDAR technology. Initially used in military applications, LIDAR has found widespread use in autonomous vehicles, where it provides real-time 3D mapping of the environment. This advancement has been instrumental in enabling autonomous navigation and decision-making, marking a significant milestone in the evolution of robot sensors.
The integration of auditory sensors has also marked a significant advancement, enabling robots to perceive and process sound. This capability is particularly beneficial in applications such as voice-activated assistants and security systems, where sound perception is crucial. The development of auditory sensors highlights the progress made in creating robots that can interact with their environment in more human-like ways.
The evolution of robot sensors continues with the incorporation of AI and machine learning algorithms. These technologies enhance the ability of sensors to recognize patterns, predict outcomes, and adapt to changes in real-time. For instance, AI-driven sensors in autonomous drones can adjust their flight paths based on environmental changes, demonstrating the integration of advanced technologies in modern sensor systems.
This evolution of robot sensors reflects the continuous drive for innovation and improvement, bringing robots closer to human-like capabilities. Each milestone in the development of robot sensors has contributed to the creation of more advanced and capable robotic systems, setting the stage for future innovations and applications.
Click here to read our expertly curated top picks!
How robot sensors work
Delving into the Technical Aspects of Sensor Functionality
Robot sensors function by detecting changes in the environment and converting these changes into signals that the robot’s control system can process. This process involves several technical aspects, including the core components of the sensors, their functional principles, and the types of data they handle. Understanding these details is essential for successfully integrating sensors into robotic systems.
At the core of every robot sensor is a transducer, a device that converts physical quantities into measurable signals. For instance, a temperature sensor uses a thermocouple to convert thermal energy into an electrical signal, which the robot’s control system can interpret. This conversion process is crucial for enabling robots to understand and respond to their environment.
The functional principles of robot sensors vary depending on the type of sensor and the data it is designed to collect. For example, vision sensors use cameras and image processing algorithms to capture and analyze visual data. These sensors are equipped with lenses, image sensors, and processing units that work together to detect and interpret visual information. This capability is vital in applications such as object recognition and navigation.
In contrast, tactile sensors detect physical contact and pressure changes. These sensors use piezoelectric materials that generate an electrical charge in response to mechanical stress. This charge is then converted into a signal that the robot’s control system can use to determine the force applied and make necessary adjustments.
The types of data handled by robot sensors are diverse, ranging from visual and auditory information to temperature and pressure readings. This data is transmitted to the robot’s control system, where it is processed and analyzed to make informed decisions. For instance, in autonomous vehicles, data from LIDAR sensors is used to create a 3D map of the surroundings, enabling the vehicle to navigate safely and efficiently.
Understanding how robot sensors work is essential for integrating them successfully into robotic systems. By comprehending the technical aspects of sensor functionality, professionals can ensure that these components are effectively utilized to enhance the capabilities and performance of robotic systems.
Utilizing robot sensors
Maximizing the Potential of Robotic Systems with Sensor Integration
The utilization of robot sensors is crucial in maximizing the potential of robotic systems. By integrating sensors into these systems, robots can perform tasks with greater accuracy, efficiency, and adaptability. This section explores current applications across various industries, highlighting how sensors enhance performance and efficiency through detailed case studies.
Example 1: Autonomous Vehicles
Autonomous vehicles rely heavily on an array of sensors, including LIDAR, cameras, and ultrasonic sensors, to navigate and make decisions on the road. These sensors collect data about the vehicle's surroundings, enabling it to identify obstacles, traffic signals, and pedestrians, thus ensuring safe and efficient travel. The integration of these sensors allows autonomous vehicles to operate in complex environments with minimal human intervention, showcasing the transformative impact of robot sensors in the automotive industry.
Example 2: Industrial Automation
In industrial settings, robotic arms equipped with sensors like force/torque sensors are used for precision tasks such as assembling parts or handling hazardous materials. These sensors provide feedback on the force applied, allowing the robot to adjust its movements for optimal performance. For instance, in an automotive assembly line, robots use force sensors to ensure that the correct amount of pressure is applied when installing components, reducing the risk of damage and improving product quality.
Example 3: Healthcare Robotics
Robots in healthcare use sensors to assist in surgeries or monitor patient vitals. For instance, surgical robots equipped with pressure sensors can perform delicate operations with unprecedented precision, reducing human error and improving patient outcomes. Additionally, sensors in patient monitoring devices continuously track vital signs, providing real-time data to healthcare professionals for timely interventions. This application of robot sensors highlights their role in enhancing the quality and safety of healthcare services.
These examples illustrate the effective deployment of robot sensors in real-world scenarios, providing insights into their transformative impact across various industries. By understanding how sensors are utilized in different applications, professionals can leverage their capabilities to drive innovation and efficiency in their projects.
Click here to read our expertly curated top picks!
Advantages of implementing robot sensors
Enhancing Capabilities and Performance in Robotic Systems
The advantages of implementing robot sensors in robotic systems are manifold, offering significant improvements in accuracy, efficiency, and adaptability. This section discusses the tangible benefits that come with integrating robot sensors, such as improved precision in tasks, reduced operational risks, and the ability to operate in complex environments.
One of the primary advantages of robot sensors is the enhancement of task precision. Sensors provide real-time feedback that allows robots to adjust their actions based on environmental conditions. For example, in manufacturing, vision sensors enable robots to detect and correct defects in products, ensuring high-quality output. This capability reduces errors and waste, ultimately leading to increased profitability.
Another significant advantage of robot sensors is their role in reducing operational risks. In hazardous environments, robots equipped with sensors can perform tasks that would be dangerous for humans. For instance, in nuclear facilities, robots with radiation sensors can safely navigate and carry out maintenance tasks, minimizing the risk to human workers. This application of robot sensors underscores their importance in enhancing safety and reliability across various sectors.
Robot sensors also enable robots to operate in complex and dynamic environments. With the ability to perceive and interpret changes in their surroundings, robots can adapt their actions accordingly. This adaptability is crucial in applications such as autonomous vehicles, where environmental conditions can change rapidly. Sensors allow these vehicles to navigate safely and efficiently, even in challenging scenarios.
The integration of robot sensors also enhances the overall performance of robotic systems. By providing accurate and timely data, sensors enable robots to make informed decisions, improving their effectiveness and efficiency. This capability is particularly beneficial in industries such as logistics, where robots equipped with sensors can optimize inventory management and streamline operations.
Overall, the advantages of implementing robot sensors are vast, offering improvements in precision, safety, adaptability, and performance. By integrating sensors into robotic systems, professionals can enhance the capabilities of their projects, driving innovation and efficiency across various industries.
Related:
Feature Management TemplateClick here to read our expertly curated top picks!
Challenges and solutions
Navigating the Complexities of Sensor Integration
Despite their numerous benefits, the implementation of robot sensors comes with its challenges. This section elucidates common issues faced during the integration and use of robot sensors, offering practical solutions and troubleshooting tips. Understanding these challenges and how to overcome them is crucial for successful deployment.
One of the primary challenges in implementing robot sensors is ensuring compatibility with the existing robotic system. Different sensors may use different protocols and interfaces, making integration complex. To address this issue, professionals should carefully select sensors that are compatible with their system and use appropriate interfacing tools and software to facilitate communication.
Calibration is another common challenge, as inaccurate calibration can lead to erroneous data and poor system performance. To overcome this challenge, follow the manufacturer's calibration procedures and perform regular maintenance to ensure sensors remain accurate. Additionally, use automated calibration tools to streamline the process and reduce the risk of human error.
Environmental factors can also affect sensor performance, causing issues such as signal interference or data loss. To mitigate these challenges, select sensors that are suited for the specific environmental conditions in which they will operate. For example, in environments with high electromagnetic interference, use sensors with robust shielding and filtering capabilities.
Data processing and interpretation pose another challenge, particularly when dealing with large volumes of data. To address this issue, integrate advanced data processing algorithms and machine learning techniques to analyze and interpret sensor data effectively. Use cloud-based platforms and edge computing solutions to handle data processing efficiently and in real-time.
Finally, cybersecurity is a growing concern, as sensors are often connected to networks and vulnerable to attacks. To enhance cybersecurity, implement robust encryption protocols and access controls to protect sensor data. Regularly update software and firmware to address vulnerabilities and ensure the system remains secure.
By understanding these challenges and implementing practical solutions, professionals can successfully navigate the complexities of sensor integration, ensuring efficient and effective use of robot sensors in their projects.
Future prospects
Anticipating the Next Wave of Sensor Technology Innovations
The future of robot sensors promises exciting developments and innovations, with advancements in sensor technology continuing to shape the future of robotics. This section explores predictions and emerging trends, highlighting how these advancements will enhance sensor capabilities and open new applications.
One of the anticipated trends is the development of more advanced and miniaturized sensors. As technology progresses, sensors are expected to become smaller and more powerful, enabling their integration into increasingly compact and sophisticated robotic systems. This miniaturization will allow for the development of robots capable of operating in previously inaccessible environments, such as inside the human body for medical diagnostics and treatments.
Another promising trend is the integration of AI and machine learning with sensor technology. By leveraging AI algorithms, sensors will be able to process and interpret data more accurately and efficiently. This advancement will enhance the intelligence and autonomy of robotic systems, enabling them to perform complex tasks with minimal human intervention. For example, AI-driven sensors in autonomous vehicles will improve their ability to navigate and make decisions in real-time.
The development of multimodal sensors is also on the horizon. These sensors will be capable of detecting multiple types of data simultaneously, such as visual, auditory, and tactile information. This capability will enhance the perception and interaction capabilities of robots, making them more versatile and adaptable to various applications. For instance, multimodal sensors in service robots will enable them to better understand and respond to human commands and interactions.
The rise of the Internet of Things (IoT) is expected to further drive the evolution of robot sensors. As IoT devices become more prevalent, sensors will play a crucial role in connecting and communicating with these devices, enabling real-time data exchange and control. This connectivity will enhance the efficiency and responsiveness of systems, leading to more intelligent and automated processes.
Overall, the future prospects of robot sensors are vast and promising, with advancements in sensor technology continuing to drive innovation and efficiency across various industries. By staying abreast of these trends, professionals can leverage the latest sensor technologies to enhance the capabilities of their robotic projects and drive the next wave of technological advancements.
Click here to read our expertly curated top picks!
Summary and final thoughts
Reflecting on the Transformative Role of Robot Sensors
In conclusion, robot sensors are transformative components that have revolutionized the field of robotics. From their foundational role in enabling robots to perceive and interact with their environment to their application in various industries such as manufacturing, healthcare, and transportation, robot sensors have become indispensable tools for enhancing precision, efficiency, and safety.
The journey through the evolution of robot sensors highlights the continuous drive for innovation, bringing robots closer to human-like capabilities. As technology advances, the integration of sophisticated sensors is expected to further enhance the capabilities of robotic systems, making them indispensable tools in various industries.
Implementing robot sensors involves a systematic approach to ensure seamless integration and functionality. By following the outlined steps and understanding the challenges and solutions associated with sensor integration, professionals can successfully leverage the benefits of robot sensors in their projects.
Looking ahead, the future of robot sensors promises exciting developments and innovations, with advancements in sensor technology continuing to shape the future of robotics. From miniaturized sensors to AI-driven capabilities, the prospects are vast and promising, offering new opportunities for enhancing the capabilities of robotic systems.
In summary, robot sensors play a critical role in modern technology, driving innovation and efficiency across various industries. By understanding their capabilities and applications, professionals can harness the power of robot sensors to drive their projects forward and shape the future of robotics and automation.
Do's and don'ts of using robot sensors
Do's | Don'ts |
---|---|
Do integrate sensors that fit your specific application needs. | Don't ignore the calibration and maintenance of sensors. |
Do ensure proper interfacing with the robot's control system. | Don't assume all sensors work the same way across different platforms. |
Do keep abreast of the latest sensor technologies. | Don't overlook the importance of data processing and interpretation. |
Do consider environmental factors affecting sensor performance. | Don't neglect the cybersecurity aspect of data handling. |
Click here to read our expertly curated top picks!
Experience a New Level of Productivity in Meegle
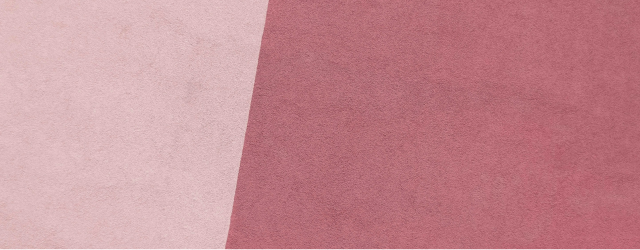
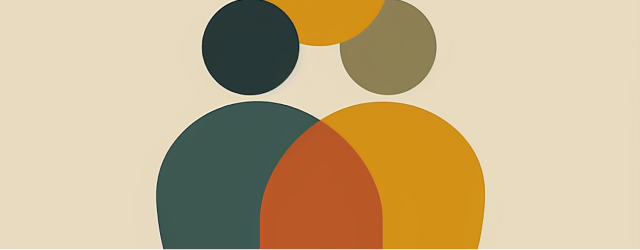
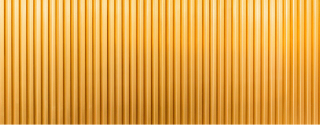
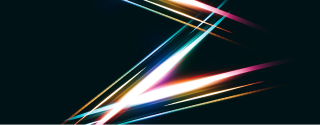
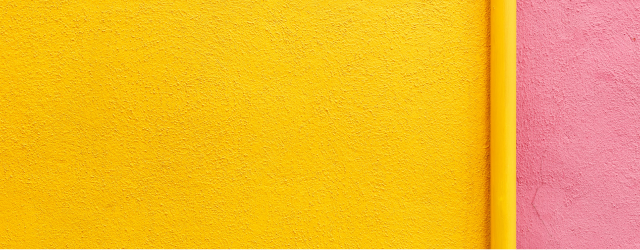
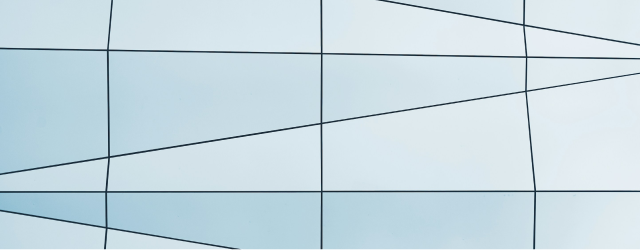
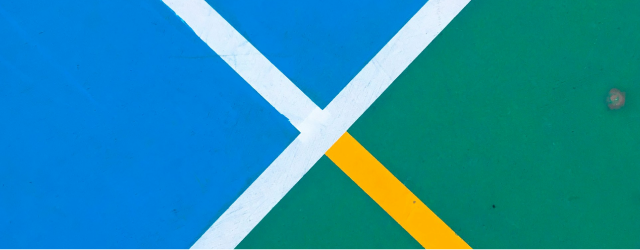
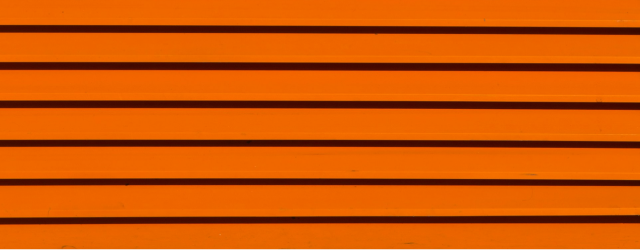