Cold Chain Managers
Unlock practical project management strategies tailored for Cold Chain Managers, enhancing productivity and driving project success.
Importance of Customized Project Management
Project management in the cold chain industry isn't merely a matter of following a standardized process. Instead, it requires a highly tailored approach that addresses the industry’s unique demands. Unlike traditional logistics, where goods can tolerate some deviations in environmental conditions, cold chain operations often involve products that must be kept within a specific temperature range to prevent spoilage or degradation. This necessitates a customized project management strategy that prioritizes temperature control and compliance with regulatory requirements.
For instance, in the pharmaceutical industry, vaccines and biologics are highly sensitive to temperature fluctuations. According to the World Health Organization, nearly 50% of vaccines globally are wasted each year due to improper temperature management. This staggering statistic highlights the critical need for customized project management strategies that can prevent such losses. By developing tailored strategies that account for the specific requirements of cold chain logistics, managers can enhance efficiency, reduce waste, and ensure compliance with industry regulations.
Customized project management involves setting clear objectives that align with both the unique requirements of the cold chain and the broader organizational goals. It also requires a keen understanding of the resources available, including personnel, technology, and transportation options. By leveraging data-driven insights and advanced technologies, Cold Chain Managers can optimize resource allocation, improve decision-making, and ultimately achieve greater control over their operations. Furthermore, a customized approach to project management allows managers to proactively identify and mitigate risks, ensuring the continuity and reliability of the cold chain.
In summary, the importance of customized project management in the cold chain industry cannot be overstated. By tailoring strategies to meet the unique demands of temperature-sensitive logistics, Cold Chain Managers can not only enhance operational efficiency but also safeguard the integrity of the products under their care.
Objectives of This Guide
This guide aims to serve as an invaluable resource for Cold Chain Managers seeking to excel in project management within the cold chain industry. By providing a comprehensive toolkit of strategies, insights, and best practices, this guide empowers managers to navigate the complexities of their operations with confidence and precision. The objectives of this guide are multifaceted, focusing on enhancing project management skills, optimizing resource allocation, leveraging technology, and effectively managing risks.
One of the primary objectives is to equip Cold Chain Managers with the skills needed to set clear and attainable project objectives. This involves aligning project goals with broader organizational objectives, ensuring that each project contributes to the company's overall success. By setting well-defined objectives, managers can create a roadmap for their projects that guides decision-making and prioritizes key activities.
Another key objective is to provide strategies for optimizing resource allocation and scheduling. In the cold chain industry, efficient use of resources is critical to maintaining operational efficiency and minimizing disruptions. This guide offers insights into how managers can effectively allocate personnel, technology, and transportation resources to achieve optimal outcomes.
Leveraging technology is also a central focus of this guide. In an era where technological advancements are rapidly transforming the logistics landscape, Cold Chain Managers must stay abreast of the latest tools and technologies available. This guide highlights essential software and applications that can streamline operations, improve data accuracy, and enhance decision-making.
Finally, this guide aims to empower managers with robust risk management strategies. Given the high stakes involved in cold chain logistics, proactive risk management is essential to ensuring the continuity and reliability of operations. This guide provides tools for identifying potential risks, developing mitigation plans, and preparing for unforeseen challenges.
In essence, the ultimate goal of this guide is to empower Cold Chain Managers with the knowledge and skills needed to drive success in their operations. By integrating advanced project management methodologies and cutting-edge technologies, managers can achieve greater control, predictability, and success in their projects.
Turn Project Chaos Into a Visual and Structured Plan
Fundamental principles of project management
Core Project Management Concepts
At the heart of successful project management are core principles that serve as the foundation for planning, executing, and closing projects. For Cold Chain Managers, understanding these principles is crucial to managing the unique challenges of the cold chain industry. The key pillars of project management include scope, time, cost, quality, and risk management, each playing a vital role in ensuring project success.
Scope management involves defining the project's boundaries and deliverables. For Cold Chain Managers, this means identifying what is included in the project and what is not, ensuring that all stakeholders have a clear understanding of the project's objectives. A well-defined scope helps prevent scope creep, where additional tasks are added without corresponding adjustments in time, cost, or resources.
Time management is critical in the cold chain industry, where delays can have significant consequences. Effective time management involves creating detailed schedules that outline the timeline for each phase of the project. This includes setting milestones, deadlines, and dependencies to ensure that the project stays on track. Gantt charts and critical path analysis are useful tools for visualizing project timelines and identifying potential bottlenecks.
Cost management is equally important, as it involves budgeting and controlling the project's financial resources. Cold Chain Managers must accurately estimate costs related to transportation, storage, personnel, and equipment to ensure that the project remains financially viable. Cost management also involves monitoring expenditures and making adjustments as needed to prevent budget overruns.
Quality management focuses on ensuring that the project's deliverables meet the required standards and specifications. In the cold chain industry, this means maintaining strict temperature controls and adhering to regulatory requirements to ensure product integrity. Quality assurance and control processes are essential for verifying that the project meets these standards throughout its lifecycle.
Risk management involves identifying, assessing, and mitigating potential risks that could impact the project's success. For Cold Chain Managers, this means proactively identifying vulnerabilities within the supply chain, such as temperature fluctuations, transportation delays, or regulatory changes. By developing contingency plans and implementing risk mitigation strategies, managers can minimize the impact of these risks.
By mastering these core project management concepts, Cold Chain Managers can establish a strong foundation for their projects, ensuring that they are well-planned, efficiently executed, and successfully completed.
Adapting Principles to Suit Cold Chain Managers
While the core principles of project management provide a solid foundation, they must be adapted to address the unique challenges faced by Cold Chain Managers. The cold chain industry requires specialized strategies that account for the complexities of temperature-sensitive logistics and regulatory compliance. By customizing these principles, managers can improve project outcomes and achieve greater success in their operations.
One way to adapt scope management for cold chain projects is by incorporating detailed temperature control specifications into the project scope. This ensures that all stakeholders understand the critical importance of maintaining the correct temperature range throughout the supply chain. Additionally, Cold Chain Managers can conduct thorough risk assessments during the scope definition phase to identify potential areas of concern and establish mitigation strategies early in the project.
Time management can be adapted by incorporating buffer times into project schedules to account for potential delays, such as transportation disruptions or customs clearance issues. Cold Chain Managers can also use advanced scheduling software to optimize routes and minimize transit times, ensuring that temperature-sensitive products reach their destinations promptly.
In terms of cost management, Cold Chain Managers can adapt traditional budgeting approaches by factoring in the costs associated with specialized equipment, such as refrigerated containers or temperature monitoring systems. By conducting a cost-benefit analysis, managers can determine the most cost-effective solutions for maintaining temperature integrity while minimizing unnecessary expenditures.
Quality management can be customized by implementing robust quality assurance processes that focus on maintaining temperature controls and documenting compliance with industry regulations. Cold Chain Managers can conduct regular audits and inspections to ensure that quality standards are consistently met throughout the supply chain.
Adapting risk management involves developing tailored risk assessments that focus on the specific vulnerabilities of cold chain logistics. Cold Chain Managers can use predictive analytics and real-time monitoring technologies to identify potential risks and respond proactively. By developing detailed contingency plans, managers can ensure that they are prepared to address unforeseen challenges and maintain the continuity of the supply chain.
In conclusion, by adapting standard project management principles to address the unique demands of the cold chain industry, managers can enhance their project's success and ensure the safe and efficient transportation of temperature-sensitive products.
Click here to explore our expertly curated top project templates!
Planning phase for cold chain managers
Setting Goals and Objectives
In the planning phase of a cold chain project, setting clear and attainable goals and objectives is paramount. This process involves aligning project goals with broader organizational objectives, ensuring that every project contributes to the company's overall success. For Cold Chain Managers, this means defining specific targets for temperature control, compliance, and efficiency while considering the unique challenges of the cold chain industry.
The first step in setting goals and objectives is to conduct a thorough needs assessment. This involves analyzing the current state of the cold chain operations, identifying areas for improvement, and determining the key objectives that the project aims to achieve. For example, a pharmaceutical company may set a goal to reduce vaccine spoilage by 20% through improved temperature monitoring and control.
Once the key objectives are identified, Cold Chain Managers can establish specific, measurable, achievable, relevant, and time-bound (SMART) goals. SMART goals provide a clear framework for setting objectives that are both realistic and attainable. For instance, a SMART goal might be to implement a new temperature monitoring system within six months, with the aim of reducing temperature deviations by 15%.
It's also important to align project goals with the organization's strategic priorities. This ensures that the project not only meets its specific objectives but also contributes to the company's long-term success. For example, a company with a strategic focus on sustainability might set a goal to reduce the carbon footprint of its cold chain operations by optimizing transportation routes and reducing energy consumption.
In addition to setting goals and objectives, Cold Chain Managers should also identify the key performance indicators (KPIs) that will be used to measure the project's success. These metrics provide a way to track progress and evaluate the project's impact. Common KPIs in the cold chain industry include temperature compliance rates, transportation efficiency, and cost savings.
Overall, setting clear and attainable goals and objectives is a critical component of the planning phase for Cold Chain Managers. By aligning project goals with organizational priorities and establishing measurable targets, managers can create a roadmap for success that guides decision-making and prioritizes key activities.
Resource Allocation and Scheduling
Effective resource allocation and scheduling are critical components of the planning phase for Cold Chain Managers. In the cold chain industry, where maintaining operational efficiency and minimizing disruptions are paramount, managers must optimize the use of personnel, technology, and transportation resources to achieve project objectives.
Resource allocation involves identifying and assigning the necessary resources needed to complete the project successfully. This includes personnel, such as logistics coordinators, warehouse staff, and transportation providers, as well as equipment, such as refrigerated containers and temperature monitoring devices. Cold Chain Managers must carefully assess the availability of these resources and allocate them in a way that maximizes efficiency and minimizes waste.
One strategy for optimizing resource allocation is to conduct a thorough resource needs assessment. This involves analyzing the project's requirements and identifying any gaps in resources that need to be addressed. For example, if a project requires additional personnel to manage increased demand during peak seasons, managers can hire temporary staff or reallocate existing resources to meet the need.
Scheduling is another critical aspect of resource allocation, as it involves creating a detailed timeline for the project's activities. Cold Chain Managers must consider the specific requirements of temperature-sensitive products and ensure that transportation routes and delivery schedules are optimized to minimize transit times and maintain temperature integrity.
Advanced scheduling software can be a valuable tool for Cold Chain Managers, allowing them to create dynamic schedules that can be adjusted in real-time based on changing conditions. These tools can also help managers identify potential bottlenecks and optimize transportation routes to reduce transit times and fuel consumption.
In addition to optimizing resource allocation and scheduling, Cold Chain Managers should also develop contingency plans to address potential disruptions. This involves identifying potential risks, such as transportation delays or equipment malfunctions, and developing strategies to mitigate their impact. For example, managers can establish backup transportation providers or implement redundant temperature monitoring systems to ensure continuity in case of equipment failure.
In summary, effective resource allocation and scheduling are essential for Cold Chain Managers to achieve project objectives and maintain the integrity of temperature-sensitive products. By optimizing the use of personnel, technology, and transportation resources, managers can ensure the efficient and reliable operation of the cold chain.
Execution phase for cold chain managers
Leading Teams in Cold Chain Projects
Leadership is a critical component of the execution phase in cold chain projects. Cold Chain Managers must inspire and coordinate their teams to achieve project objectives with precision and accountability. Effective leadership involves understanding the unique dynamics of the cold chain industry and employing leadership styles and techniques that foster collaboration and innovation.
One key aspect of leading teams in cold chain projects is establishing a clear vision and communicating it effectively to all team members. This involves articulating the project's goals and objectives, as well as the specific roles and responsibilities of each team member. By providing a clear direction, Cold Chain Managers can align their teams' efforts with the project's objectives and foster a sense of ownership and accountability.
Another important leadership skill is the ability to inspire and motivate team members. Cold Chain Managers can achieve this by recognizing and rewarding individual and team achievements, providing opportunities for professional development, and creating a positive work environment that encourages open communication and collaboration. By fostering a supportive and inclusive culture, managers can boost team morale and drive higher levels of performance.
In the cold chain industry, where precision and accuracy are paramount, Cold Chain Managers must also be adept at problem-solving and decision-making. This involves analyzing complex data, evaluating multiple options, and making informed decisions that prioritize the project's objectives. By leveraging data-driven insights and advanced analytics, managers can make more accurate predictions and optimize project outcomes.
Effective communication is another critical leadership skill for Cold Chain Managers. This involves maintaining open lines of communication with team members, stakeholders, and external partners to ensure that everyone is informed and aligned with the project's goals. Regular team meetings, progress updates, and feedback sessions can help managers address any issues or concerns and ensure that the project stays on track.
In conclusion, leading teams in cold chain projects requires a combination of vision, motivation, problem-solving, and communication skills. By employing effective leadership techniques, Cold Chain Managers can inspire their teams to achieve project objectives with precision and accountability.
Monitoring and Controlling Project Progress
Monitoring and controlling project progress is a critical aspect of the execution phase for Cold Chain Managers. Effective monitoring and control ensure that cold chain projects stay on course, meet their objectives, and maintain the integrity of temperature-sensitive products. This involves utilizing performance metrics, setting benchmarks, and implementing corrective actions to address any deviations from the project plan.
One key strategy for monitoring project progress is to establish a set of key performance indicators (KPIs) that provide a clear picture of the project's status. These metrics can include temperature compliance rates, transportation efficiency, cost savings, and other relevant indicators. By regularly tracking these KPIs, Cold Chain Managers can identify any areas of concern and take corrective actions as needed.
In addition to monitoring KPIs, Cold Chain Managers should also conduct regular project reviews to assess the project's progress and identify any potential risks or challenges. These reviews can involve analyzing project data, evaluating the effectiveness of risk management strategies, and assessing the impact of any changes to the project scope or timeline. By conducting thorough project reviews, managers can ensure that the project stays on track and meets its objectives.
Another important aspect of monitoring and controlling project progress is implementing corrective actions to address any deviations from the project plan. This involves identifying the root cause of any issues and developing strategies to mitigate their impact. For example, if a transportation delay threatens to disrupt the supply chain, Cold Chain Managers might adjust delivery schedules, reroute shipments, or engage additional transportation providers to ensure continuity.
Advanced technologies, such as real-time monitoring systems and predictive analytics, can also play a vital role in monitoring and controlling project progress. These tools provide Cold Chain Managers with real-time data and insights, enabling them to make informed decisions and respond proactively to changing conditions. By leveraging these technologies, managers can enhance their ability to track project progress and ensure the successful completion of cold chain projects.
In summary, monitoring and controlling project progress is essential for Cold Chain Managers to ensure that their projects stay on course and meet their objectives. By using performance metrics, conducting regular reviews, and implementing corrective actions, managers can maintain the integrity of temperature-sensitive products and achieve project success.
Click here to explore our expertly curated top project templates!
Tools and technologies for cold chain managers
Essential Tools for Enhancing Efficiency
In the cold chain industry, where precision and efficiency are paramount, leveraging the right tools and technologies can significantly enhance project management capabilities. Cold Chain Managers must stay abreast of the latest innovations and solutions available to streamline operations, improve data accuracy, and enhance decision-making. This section highlights essential tools and technologies that are particularly beneficial for Cold Chain Managers seeking to optimize their projects.
One of the most valuable tools for Cold Chain Managers is advanced project management software. These platforms provide a centralized hub for planning, executing, and monitoring projects, allowing managers to streamline workflows and improve collaboration among team members. Features such as task management, resource allocation, and real-time reporting enable managers to keep track of project progress and make data-driven decisions.
Temperature monitoring systems are another critical tool for Cold Chain Managers. These systems use sensors and IoT (Internet of Things) technology to provide real-time data on temperature levels throughout the supply chain. By continuously monitoring temperature conditions, managers can ensure compliance with industry standards and prevent product spoilage. Some systems even offer automated alerts and notifications, enabling managers to respond promptly to any deviations from the desired temperature range.
In addition to temperature monitoring, Cold Chain Managers can benefit from route optimization tools that enhance transportation efficiency. These tools use algorithms and data analytics to identify the most efficient routes for transporting temperature-sensitive products, minimizing transit times and fuel consumption. By optimizing transportation routes, managers can reduce costs and improve the reliability of the supply chain.
Data analytics platforms are also essential for Cold Chain Managers seeking to enhance decision-making capabilities. These platforms provide advanced analytics and visualization tools that enable managers to analyze large volumes of data and extract actionable insights. By leveraging predictive analytics and machine learning, managers can identify trends, forecast demand, and optimize resource allocation.
Furthermore, blockchain technology is emerging as a powerful tool for enhancing transparency and traceability in the cold chain. By providing a secure and immutable record of transactions, blockchain can help Cold Chain Managers verify the authenticity and integrity of products throughout the supply chain. This technology also facilitates compliance with regulatory requirements and provides greater visibility into the supply chain.
In conclusion, by leveraging essential tools and technologies, Cold Chain Managers can enhance efficiency, improve data accuracy, and optimize decision-making in their projects. These tools provide valuable insights and capabilities that enable managers to navigate the complexities of the cold chain with greater precision and efficacy.
Integrating New Technologies
Integrating new technologies into cold chain operations can be a game-changer for Cold Chain Managers, offering opportunities to enhance efficiency, improve data accuracy, and streamline workflows. However, successful integration requires careful planning and execution to ensure smooth adoption and implementation. This section provides strategies for Cold Chain Managers to seamlessly integrate new technologies into their projects and operations.
The first step in integrating new technologies is to conduct a thorough needs assessment to identify the specific areas of the cold chain operation that could benefit from technological enhancements. This involves analyzing current processes, identifying pain points, and determining the desired outcomes of the technology implementation. By understanding the unique needs of the operation, Cold Chain Managers can select the most appropriate technologies for their projects.
Once the technology is selected, Cold Chain Managers must develop a comprehensive implementation plan that outlines the steps needed to integrate the technology into existing processes. This plan should include timelines, resource requirements, and key milestones to ensure a smooth transition. Managers should also engage key stakeholders and team members early in the process to gain buy-in and support for the technology implementation.
Training and support are critical components of successful technology integration. Cold Chain Managers should provide comprehensive training to team members to ensure they are comfortable and proficient with the new technology. This may involve conducting workshops, webinars, and hands-on training sessions to familiarize team members with the technology's features and functionalities.
Overcoming resistance to change is another important consideration when integrating new technologies. Cold Chain Managers should address any concerns or apprehensions team members may have about the technology and emphasize the benefits it brings to the operation. By fostering a culture of innovation and continuous improvement, managers can encourage team members to embrace new technologies and contribute to the success of the implementation.
Finally, Cold Chain Managers should establish a system for monitoring and evaluating the performance of the new technology. This involves tracking key performance indicators (KPIs) and gathering feedback from team members to assess the technology's impact on operations. By continuously evaluating the technology's performance, managers can identify areas for improvement and make necessary adjustments to optimize its effectiveness.
In summary, integrating new technologies into cold chain operations requires careful planning, training, and support to ensure successful adoption and implementation. By following these strategies, Cold Chain Managers can enhance efficiency, improve data accuracy, and achieve greater success in their projects.
Risk management strategies for cold chain managers
Identifying Potential Risks
In the cold chain industry, where temperature-sensitive products are at risk of spoilage or degradation, identifying potential risks is a critical component of effective project management. Cold Chain Managers must proactively assess vulnerabilities within the supply chain to develop strategies for mitigating risks and ensuring the continuity and reliability of operations.
One effective technique for identifying potential risks is conducting a comprehensive risk assessment. This involves analyzing every aspect of the supply chain, from procurement and transportation to storage and distribution, to identify areas of vulnerability. Cold Chain Managers can use tools such as SWOT (Strengths, Weaknesses, Opportunities, and Threats) analysis and risk matrices to systematically evaluate potential risks and prioritize them based on their likelihood and impact.
Predictive analytics and real-time monitoring technologies are also valuable tools for identifying potential risks in cold chain projects. By leveraging data analytics and machine learning, Cold Chain Managers can analyze historical data and trends to predict potential issues before they arise. Real-time monitoring systems provide continuous data on temperature conditions, transportation routes, and other critical factors, enabling managers to identify deviations and respond proactively.
Another important consideration in risk identification is compliance with industry regulations and standards. Cold Chain Managers must stay abreast of the latest regulatory requirements and assess the potential risks of non-compliance. This involves conducting regular audits and inspections to ensure that processes and procedures align with industry standards.
In addition to internal risks, Cold Chain Managers must also consider external risks that could impact the supply chain, such as natural disasters, geopolitical events, or changes in market demand. By conducting scenario planning and developing contingency plans, managers can prepare for potential disruptions and minimize their impact on operations.
In conclusion, identifying potential risks is a critical component of risk management for Cold Chain Managers. By conducting comprehensive risk assessments, leveraging predictive analytics, and considering both internal and external risks, managers can proactively address vulnerabilities and ensure the continuity and reliability of the cold chain.
Mitigation and Contingency Plans
Mitigating risks and preparing contingency plans are essential strategies for Cold Chain Managers to ensure the continuity and reliability of operations. Given the high stakes involved in cold chain logistics, proactive risk management is crucial to minimizing the impact of disruptions and safeguarding the integrity of temperature-sensitive products.
One effective strategy for mitigating risks is developing robust mitigation plans that outline specific actions to address identified risks. This involves identifying the root causes of potential issues and implementing measures to prevent them from occurring. For example, if a risk assessment identifies transportation delays as a potential threat, Cold Chain Managers might engage multiple transportation providers or optimize routing schedules to ensure timely delivery.
Contingency planning is another critical component of risk management for Cold Chain Managers. This involves developing backup plans and strategies to respond to unforeseen challenges and disruptions. By establishing contingency plans, managers can quickly and effectively respond to emergencies, minimizing their impact on operations. For example, a contingency plan might outline steps to take in the event of equipment failure, such as deploying backup temperature monitoring systems or engaging alternative storage facilities.
Risk transfer is another strategy that Cold Chain Managers can use to mitigate risks. This involves transferring some of the risks to third parties, such as insurance providers or logistics partners. By securing insurance coverage for potential losses or partnering with reliable logistics providers, managers can reduce the financial impact of disruptions and enhance the resilience of the supply chain.
It's also important for Cold Chain Managers to conduct regular reviews and updates of their risk management strategies. This involves evaluating the effectiveness of mitigation and contingency plans, gathering feedback from team members, and making necessary adjustments to improve their efficacy. By continuously monitoring and evaluating risk management strategies, managers can ensure that they remain relevant and effective in addressing evolving challenges.
In summary, mitigating risks and preparing contingency plans are essential strategies for Cold Chain Managers to ensure the continuity and reliability of operations. By developing robust mitigation plans, establishing contingency plans, and conducting regular reviews, managers can proactively address potential disruptions and safeguard the integrity of temperature-sensitive products.
Click here to explore our expertly curated top project templates!
Examples of cold chain project management
Example 1: implementing a temperature monitoring system
Example 1: implementing a temperature monitoring system
Implementing a temperature monitoring system is a critical project for Cold Chain Managers, as it enhances the ability to maintain temperature integrity and compliance throughout the supply chain. This case study provides a detailed look at the challenges, solutions, and outcomes of implementing a temperature monitoring system in a pharmaceutical distribution company.
The pharmaceutical company faced significant challenges in maintaining temperature compliance for its vaccine supply chain. Frequent temperature deviations during transportation and storage led to product spoilage and financial losses. The company recognized the need for a robust temperature monitoring system to address these issues and ensure the safe and efficient delivery of its products.
The first step in the project was to conduct a comprehensive needs assessment to identify the specific requirements of the temperature monitoring system. This involved analyzing the existing supply chain processes, identifying critical control points, and determining the desired features and functionalities of the system. The company selected a solution that provided real-time temperature monitoring, automated alerts, and data analytics capabilities.
Once the system was selected, the company developed an implementation plan that outlined the steps needed to integrate the technology into its operations. This included installing temperature sensors in transportation vehicles and storage facilities, configuring the software platform, and providing training to team members on how to use the system.
One of the key challenges faced during implementation was ensuring seamless integration with existing systems and processes. The company worked closely with the technology provider to address any compatibility issues and conducted thorough testing to ensure the system's accuracy and reliability.
The implementation of the temperature monitoring system resulted in significant improvements in temperature compliance and product integrity. The company was able to reduce temperature deviations by 30%, leading to a decrease in product spoilage and financial losses. The system also provided valuable data insights that enabled the company to optimize transportation routes and improve overall supply chain efficiency.
In conclusion, implementing a temperature monitoring system is a critical project for Cold Chain Managers seeking to enhance temperature compliance and product integrity. By conducting a thorough needs assessment, developing a comprehensive implementation plan, and addressing integration challenges, managers can achieve significant improvements in their cold chain operations.
Example 2: reducing transportation delays in cold chain logistics
Example 2: reducing transportation delays in cold chain logistics
Reducing transportation delays is a key priority for Cold Chain Managers, as timely delivery is critical to maintaining the integrity of temperature-sensitive products. This case study examines a project focused on reducing transportation delays through enhanced scheduling and route optimization for a global food distribution company.
The company faced significant challenges in meeting delivery schedules due to transportation delays caused by traffic congestion, customs clearance issues, and inefficient routing. These delays resulted in increased transit times and compromised the quality of temperature-sensitive food products.
To address these challenges, the company embarked on a project to optimize its transportation scheduling and routing processes. The first step was to conduct a thorough analysis of the existing transportation network, identifying bottlenecks and areas for improvement. The company leveraged advanced data analytics and route optimization tools to develop more efficient transportation schedules and optimize delivery routes.
One of the key strategies employed in the project was the use of real-time traffic data and predictive analytics to adjust delivery schedules based on current and projected traffic conditions. This allowed the company to avoid congested routes and minimize delays.
The company also collaborated with customs authorities to streamline the clearance process and reduce delays at border crossings. By implementing electronic documentation and pre-clearance procedures, the company was able to expedite the customs clearance process and reduce transit times.
The project resulted in significant improvements in transportation efficiency and delivery reliability. The company was able to reduce transportation delays by 25%, leading to improved product quality and customer satisfaction. The optimized routing and scheduling processes also resulted in cost savings and reduced fuel consumption.
In conclusion, reducing transportation delays is a critical project for Cold Chain Managers seeking to maintain the integrity of temperature-sensitive products. By leveraging data analytics, route optimization tools, and collaboration with customs authorities, managers can achieve significant improvements in transportation efficiency and delivery reliability.
Example 3: enhancing compliance with regulatory standards
Example 3: enhancing compliance with regulatory standards
Ensuring compliance with regulatory standards is a top priority for Cold Chain Managers, as non-compliance can result in significant financial and reputational risks. This case study examines a project aimed at enhancing compliance with industry regulations for a global pharmaceutical company.
The company faced challenges in maintaining compliance with regulatory standards due to complex and evolving requirements in different markets. Non-compliance resulted in delays, fines, and potential risks to product quality and patient safety.
To address these challenges, the company embarked on a project to enhance its compliance processes and procedures. The first step was to conduct a comprehensive review of existing compliance practices and identify areas for improvement. The company engaged regulatory experts and consultants to provide guidance on best practices and ensure alignment with industry standards.
One of the key strategies employed in the project was the implementation of a comprehensive compliance management system. This system provided centralized access to regulatory requirements, automated compliance tracking, and real-time reporting capabilities. By centralizing compliance data and processes, the company was able to ensure consistency and accuracy in its compliance efforts.
Training and education were also critical components of the project, as the company sought to enhance the compliance knowledge and awareness of its team members. The company conducted regular training sessions and workshops to ensure that all team members were well-versed in the latest regulatory requirements and best practices.
The project resulted in significant improvements in compliance and regulatory adherence. The company was able to achieve a 95% compliance rate across its operations, reducing the risk of fines and delays. The centralized compliance management system provided greater visibility and control over compliance processes, enabling the company to respond proactively to regulatory changes.
In conclusion, enhancing compliance with regulatory standards is a critical project for Cold Chain Managers seeking to mitigate risks and ensure product quality. By implementing a comprehensive compliance management system, engaging regulatory experts, and providing training and education, managers can achieve significant improvements in compliance and regulatory adherence.
Turn Project Chaos Into a Visual and Structured Plan
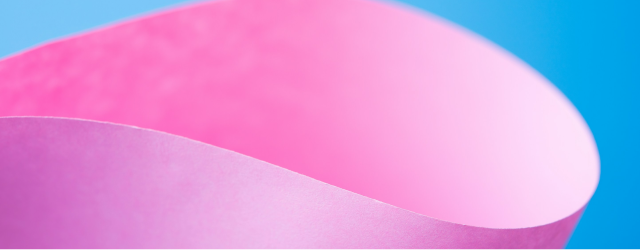
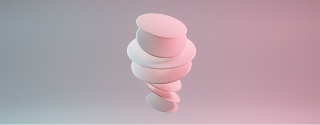
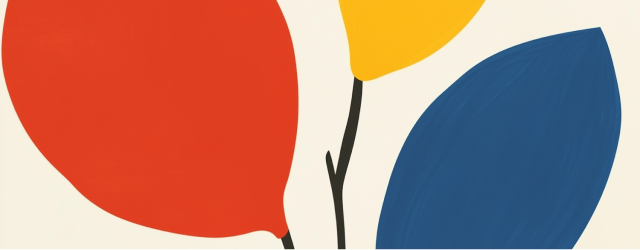
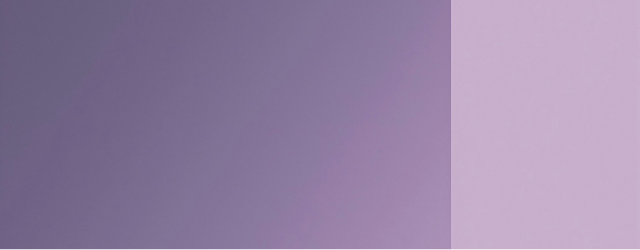
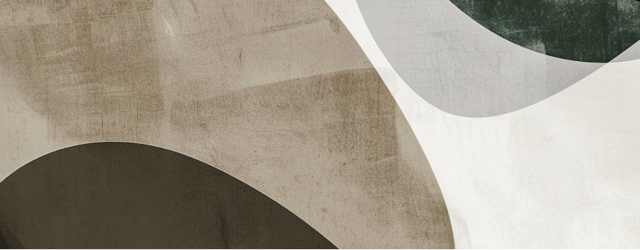
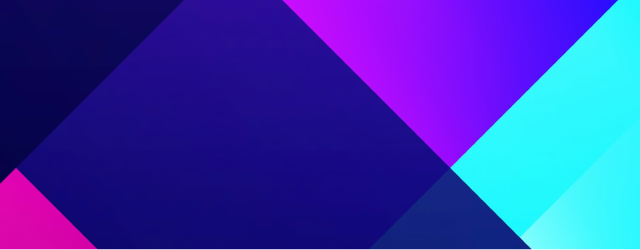
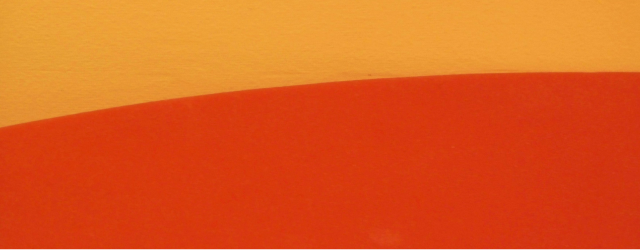
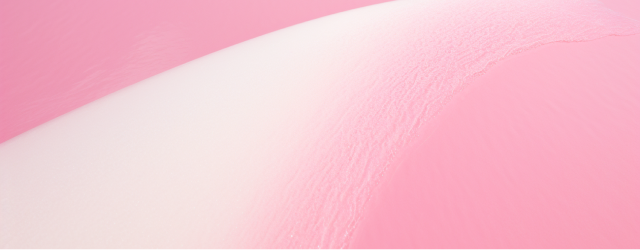