SOP For Cleaning Procedures
Learn practical guidelines and expert tips to effectively implement SOP for cleaning procedures for improved operational efficiency.
Definition and Importance
Standard Operating Procedures (SOPs) are detailed, written instructions designed to achieve uniformity in the performance of specific functions. In the context of cleaning, SOPs are vital as they provide a framework that standardizes cleaning tasks, ensuring consistency and quality control. They serve as a guide for employees to follow, ensuring that every aspect of the cleaning process is executed uniformly. This standardization is imperative, particularly in sectors where hygiene and cleanliness are critical, such as healthcare facilities where SOPs help in reducing infection rates by up to 40%, according to a study published in the Journal of Hospital Infection.
Context and Value
The value of meticulously crafted SOPs extends beyond mere cleanliness; they are pivotal in enhancing organizational efficiency and ensuring compliance with stringent health regulations. Consider the hospitality industry: here, SOPs in cleaning ensure that guests receive consistent quality, directly impacting customer satisfaction and loyalty. In manufacturing, SOPs can prevent cross-contamination and ensure product safety, adhering to industry regulations. Moreover, they promote a safe working environment, reducing the risk of accidents and health hazards. By streamlining operations, SOPs can save businesses time and resources, minimizing waste and maximizing productivity.
Experience a New Level of Productivity in Meegle
Planning and preparation for sops
Laying the Groundwork
Successful SOPs are not crafted overnight; they require a deliberate and structured approach that begins with understanding the fundamental components. These include defining the scope, which outlines the range of tasks covered by the SOP, and setting objectives that align with organizational goals. Identifying stakeholders is crucial as they provide insights and feedback pivotal in shaping effective SOPs. This phase also involves a comprehensive assessment of existing cleaning standards and organizational needs, ensuring that the SOPs are tailored to meet specific operational requirements.
Key Considerations
As you embark on developing SOPs, several factors must be considered to ensure their success. Regulatory compliance is paramount; SOPs must adhere to local and international standards to avoid legal repercussions. Staff training is another critical element. Without properly trained personnel, even the best SOPs can fall flat. Resource allocation, including tools and cleaning supplies, also plays a significant role; inadequate resources can hinder the effective implementation of SOPs. Lastly, involving team members in the SOP development process can mitigate resistance, fostering a sense of ownership and accountability.
Preparation Steps
To facilitate the creation of effective SOPs, it is important to follow a structured approach. Begin with a needs assessment to identify the specific cleaning requirements of your organization. Engaging stakeholders early in the process ensures that diverse perspectives are considered, leading to more comprehensive SOPs. Drafting the SOP framework involves outlining the procedures in a clear and concise manner, focusing on simplicity and understandability. This framework serves as the foundation upon which detailed SOPs are built, setting the stage for successful implementation.
Click here to read our expertly curated top picks!
Executing sops for cleaning effectively
Step-by-Step Implementation
Implementing SOPs is a meticulous process that requires attention to detail and systematic execution. Writing the SOP should involve clear, concise language that leaves no room for ambiguity. After drafting, testing the SOP in a controlled environment allows for the identification and rectification of potential issues. Launching the SOP requires effective communication to ensure that all stakeholders are informed and understand the new procedures. Documentation is crucial throughout this process, providing a reference point and ensuring consistency in implementation.
Tips for Streamlining
Streamlining SOP implementation can significantly enhance efficiency. Consider utilizing technology to automate routine tasks, such as digital checklists and scheduling software, which can reduce manual errors and save time. Maintaining flexibility in SOPs is also important; they should be adaptable to accommodate changes in regulations or organizational needs. Regular reviews and updates ensure that the SOPs remain relevant and effective. Open communication channels allow for continuous feedback, enabling ongoing improvements and optimizations.
Diverse Use Cases
SOP implementation varies across different sectors, each presenting unique challenges and requirements. In hospitals, sanitation protocols are meticulously designed to prevent the spread of infections, involving specific cleaning agents and methods for different areas. Hotels implement housekeeping SOPs to ensure rooms are cleaned to consistent standards, impacting guest satisfaction and operational efficiency. Manufacturing plants follow equipment cleaning SOPs to comply with industry regulations and ensure product safety. Each of these examples illustrates the adaptability and importance of SOPs across diverse settings.
Tools and resources for sops
Recommended Tools
The development and management of SOPs are greatly facilitated by a variety of tools and resources. Digital checklists are an effective way to ensure that all cleaning tasks are completed consistently, providing real-time updates and accountability. SOP management platforms offer centralized storage and easy access to SOP documents, streamlining updates and revisions. Additionally, e-learning modules can enhance staff training, providing interactive and engaging learning experiences that improve comprehension and retention. Leveraging these tools can significantly enhance the effectiveness of SOPs and drive operational excellence.
Click here to read our expertly curated top picks!
Challenges and solutions in sop implementation
Common Challenges
Despite their benefits, implementing SOPs can present several challenges. Staff resistance is a common hurdle; employees may be hesitant to adopt new procedures, fearing increased workload or changes to routine tasks. Compliance issues can arise if SOPs are not aligned with applicable regulations, leading to legal ramifications. Resource limitations, including insufficient tools or cleaning supplies, can impede the effective execution of SOPs. Recognizing these challenges is the first step toward developing effective solutions.
Solutions
Addressing these challenges requires a proactive and strategic approach. Change management strategies, such as involving employees in the SOP development process and providing clear explanations of the benefits, can help mitigate resistance. Continuous training programs ensure that staff remain informed and proficient in the new procedures. Iterative SOP reviews promote ongoing improvement, allowing organizations to adapt to changing needs and regulations. By implementing these solutions, businesses can overcome obstacles and fully realize the benefits of SOPs.
Measuring success of sops
Evaluation Methods
Evaluating the effectiveness of SOPs is crucial to ensure they deliver the desired outcomes. Both quantitative and qualitative methods can be employed to assess SOP performance. Auditing involves a systematic review of cleaning processes to ensure compliance with SOP requirements. Feedback mechanisms, such as surveys and focus groups, provide insights into employee experiences and areas for improvement. Performance metrics, such as cleaning time efficiency and quality scores, offer tangible measures of success, guiding ongoing enhancements.
Key Performance Indicators (KPIs)
Key Performance Indicators (KPIs) are invaluable tools for measuring the success of cleaning SOPs. Compliance rates indicate the extent to which procedures are followed, highlighting areas that require additional training or resources. Cleaning time efficiency measures the time taken to complete tasks, identifying opportunities for streamlining processes. Quality scores assess the cleanliness of spaces, providing a benchmark for continuous improvement. By monitoring these KPIs, organizations can ensure that their SOPs remain effective and aligned with operational goals.
Click here to read our expertly curated top picks!
Detailed examples of sops in action
Hospital sanitation sop
Hospital sanitation sop
In the healthcare sector, maintaining a sterile environment is critical to patient safety. A hospital’s sanitation SOP typically includes detailed instructions for cleaning different areas, such as operating rooms, patient wards, and common spaces. For instance, operating rooms may require the use of specific disinfectants and techniques to eliminate pathogens. Regular training and audits ensure compliance and effectiveness, reducing infection rates and enhancing patient outcomes. This example underscores the importance of tailored SOPs in achieving health and safety objectives.
Hotel housekeeping sop
Hotel housekeeping sop
In the hospitality industry, guest satisfaction is closely linked to cleanliness. A hotel’s housekeeping SOP outlines the procedures for cleaning guest rooms and public areas, ensuring consistent quality. Tasks may include bed making, bathroom cleaning, and replenishing amenities, each with specific instructions and standards. By adhering to these SOPs, hotels can enhance guest experiences, resulting in improved reviews and increased bookings. This example highlights the pivotal role of SOPs in maintaining operational excellence in hospitality.
Manufacturing plant sop
Manufacturing plant sop
In manufacturing, cleaning SOPs are essential for ensuring product safety and compliance with industry standards. A manufacturing plant’s equipment cleaning SOP may include detailed procedures for cleaning machinery, preventing cross-contamination, and maintaining production quality. Regular inspections and audits ensure adherence to SOPs, minimizing the risk of product recalls or regulatory penalties. This example illustrates the critical importance of SOPs in maintaining safety and compliance in manufacturing operations.
Click here to read our expertly curated top picks!
Do's and don'ts of sops for cleaning procedures
Do's | Don'ts |
---|---|
Clearly define roles and responsibilities | Overlook staff training |
Regularly review and update SOPs | Ignore feedback from staff |
Utilize technology to track performance | Neglect regulatory compliance |
Engage stakeholders throughout the process | Rely solely on manual processes |
Provide comprehensive training programs | Resist adapting SOPs to new challenges |
Experience a New Level of Productivity in Meegle
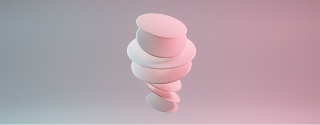
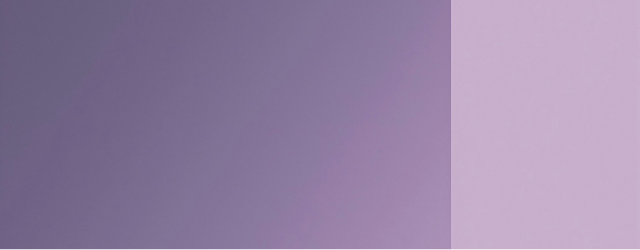
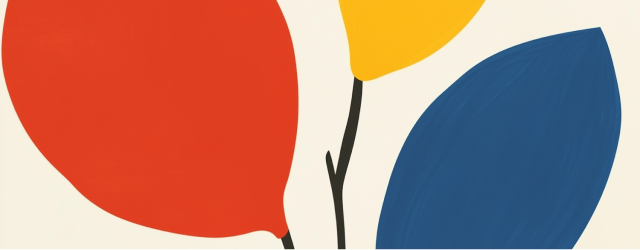
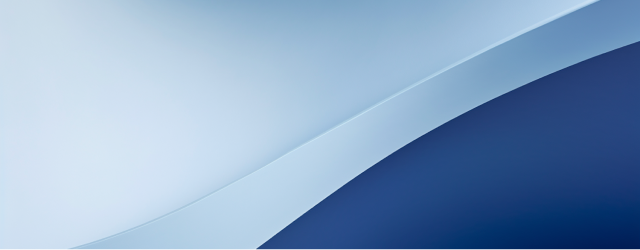
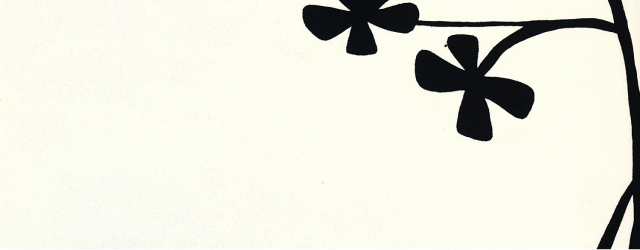
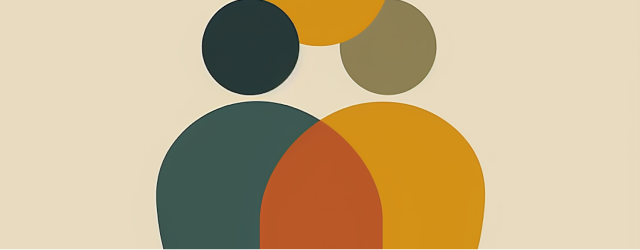
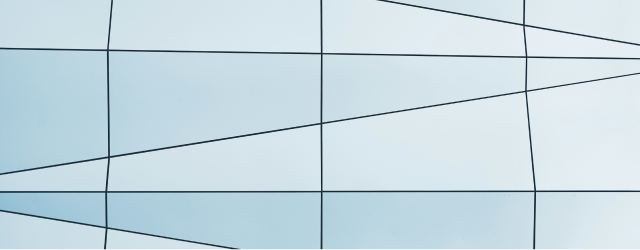
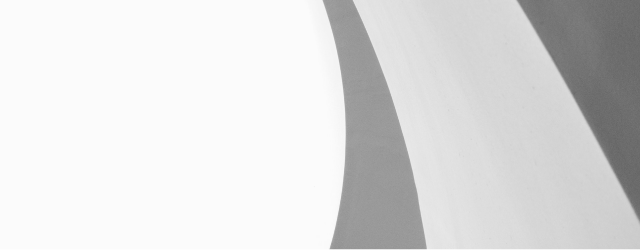