3D Printing In SCM
Streamline your supply chain operations with our expert insights on 3D Printing in SCM, providing you with the know-how to boost efficiency and effectiveness.
Background of 3D Printing in SCM
3D printing, synonymous with additive manufacturing, has significantly impacted various industries, including supply chain management. Traditionally, manufacturing relied on subtractive processes, which involved removing material to shape the final product. In contrast, 3D printing fabricates items layer by layer from a digital model, presenting a paradigm shift in production methodologies. This technology's integration into SCM offers transformative opportunities by enabling the production of complex and customized parts without the extensive tooling and setups required in conventional manufacturing. For supply chain professionals, the implications are profound. 3D printing can streamline processes, reduce lead times, and enhance product innovation, making it a powerful tool for maintaining a competitive edge. A case in point is General Electric (GE), which adopted 3D printing to produce fuel nozzles for its LEAP engines, leading to a part that was 25% lighter and five times more durable. This highlights the potential of 3D printing to revolutionize traditional manufacturing and supply chain practices, marking a significant evolution in SCM strategies.
Importance in Today’s Market
In today’s volatile and fast-paced market, characterized by globalization and complex supply networks, agility and adaptability have become crucial for success. The ability to produce goods on-demand closer to the point of use not only reduces inventory costs but also mitigates risks associated with supply chain disruptions. For instance, during the COVID-19 pandemic, many companies faced severe supply chain bottlenecks. Those who had integrated 3D printing into their operations were better positioned to adapt by producing essential components locally. According to a 2021 report by Deloitte, companies using 3D printing reported a 30% reduction in lead times and a 25% increase in market responsiveness. Additionally, the environmental benefits of 3D printing cannot be overlooked. This technology supports sustainability by minimizing waste, reducing transportation-related emissions, and allowing the recycling of materials. As supply chains become more global and intricate, embracing 3D printing strategically can lead to significant cost savings, improved sustainability, and enhanced customer satisfaction. For project managers aiming to lead in the modern supply chain landscape, mastering 3D printing is not just beneficial but essential.
Navigate supply chain management with Meegle. Sign up for free and see the difference!
Historical development
Origins of 3D Printing in SCM
The origins of 3D printing trace back to the late 20th century, with its initial application predominantly in the realm of prototyping. Initially, this technology was seen as a novel tool for creating quick design iterations in manufacturing, allowing engineers to visualize and test parts before committing to costly production runs. The transition of 3D printing from prototyping to a strategic asset in supply chain management represents a significant shift in industrial practices. The healthcare industry provides an illustrative example; early adoption of 3D printing allowed for the rapid prototyping of medical devices, which eventually led to the creation of customized implants and prosthetics tailored to individual patients. As companies began to recognize the strategic value of 3D printing, its role in SCM expanded. Businesses started exploring its potential to redefine production and logistics processes, paving the way for innovations such as on-demand manufacturing and distributed production networks. This transition marked the beginning of an era where 3D printing evolved from a novelty to an integral component of agile and responsive supply chains.
Evolution Over Time
Since its inception, 3D printing has undergone significant advancements, particularly in terms of materials, speed, and precision. These advancements have broadened its application beyond prototyping into areas such as spare parts manufacturing, custom product design, and on-demand production. For instance, the aerospace industry has embraced 3D printing for the production of complex parts that are difficult or impossible to manufacture using traditional methods. Boeing, for example, has incorporated over 60,000 3D-printed parts into its aircraft, resulting in reduced weight and improved fuel efficiency. The automotive industry has also seen similar benefits, with companies like BMW and Ford utilizing 3D printing for tooling and custom parts. These technological advancements have not only improved production capabilities but also aligned with the changing demands and practices within global SCM. According to a study by Statista, the global 3D printing market was valued at approximately $13.7 billion in 2020 and is expected to reach $63.46 billion by 2026, illustrating the technology's growing significance and integration into global supply chains. As 3D printing continues to evolve, its role in SCM is set to expand, offering innovative solutions to meet the challenges of a rapidly changing business environment.
Related:
External Market FactorsClick here to read our expertly curated top picks!
Core concepts
Defining 3D Printing in SCM
To fully appreciate the impact of 3D printing in supply chain management, it is essential to clearly define its role and function within this context. Unlike traditional manufacturing processes that often involve subtracting material to create a part, 3D printing is an additive process. It builds products layer by layer based on a digital model, allowing for the creation of complex geometries that are difficult to achieve through conventional methods. This capability revolutionizes SCM by enabling greater flexibility and customization in production. For instance, in the consumer electronics industry, companies can use 3D printing to produce custom-fit smartphone cases or prototypes for new devices, reducing time to market and enhancing product personalization. In SCM, 3D printing serves as a bridge between design and production, facilitating rapid prototyping, on-demand manufacturing, and distributed production models. This integration allows supply chain managers to optimize inventory levels, reduce transportation costs, and respond swiftly to market changes, thereby enhancing overall efficiency and competitiveness.
Notable Features
The adoption of 3D printing in SCM is largely driven by its distinct features, which offer significant advantages over traditional manufacturing methods. One of the most notable features is the reduction of waste. Traditional manufacturing methods often involve cutting away excess material, resulting in substantial waste. In contrast, 3D printing uses only the material necessary to create a part, minimizing waste and contributing to sustainability efforts. Another key feature is the accelerated production cycle. 3D printing can produce complex parts quickly and with fewer steps, reducing lead times and enabling faster responses to market demands. Additionally, the ability to create intricate geometries and highly customized products is a significant advantage. This capability is particularly beneficial in industries such as healthcare, where personalized medical devices and implants can be created to fit individual patient needs. According to a survey by PwC, 70% of manufacturers believe that 3D printing will be a key driver of innovation in their industry. These notable features underscore the strategic potential of 3D printing in optimizing supply chain operations and achieving competitive advantage.
Strategic implementation
Planning and Execution
The successful integration of 3D printing into supply chains requires meticulous planning and execution. To effectively incorporate this technology into existing SCM frameworks, organizations must first assess their strategic goals and identify areas where 3D printing can add value. This involves understanding the specific needs of the business and its customers, as well as evaluating the potential impact of 3D printing on production processes and supply chain operations. For example, an automotive company looking to reduce lead times and increase production flexibility might consider using 3D printing for the rapid prototyping of new parts or the production of custom components. Once the strategic objectives are defined, the next step is to develop a comprehensive implementation plan. This plan should outline the resources, technologies, and processes required to integrate 3D printing into the supply chain. It should also include a timeline for implementation, as well as metrics for measuring success. Effective planning and execution are critical to ensuring that the integration of 3D printing aligns with organizational goals and delivers the desired benefits.
Best Practices
Drawing from industry insights and expert recommendations, it is essential to follow best practices to optimize 3D printing processes within SCM. One of the key best practices is selecting the right materials and technologies for the specific application. Different materials and 3D printing technologies offer varying properties and capabilities, so it's crucial to choose those that best meet the needs of the business and its products. Another important practice is managing the digital workflow effectively. This involves ensuring that digital models and data are accurate, up-to-date, and securely managed throughout the production process. Additionally, investing in staff training and encouraging innovation can help organizations fully leverage the potential of 3D printing. According to a report by McKinsey, companies that invest in training and innovation are more likely to achieve successful outcomes with 3D printing. Finally, establishing clear performance metrics and continuously monitoring and optimizing processes are essential for maximizing efficiency and achieving desired outcomes. By following these best practices, organizations can harness the full potential of 3D printing in SCM and drive meaningful improvements in their supply chain operations.
Related:
Personal Budget ManagementClick here to read our expertly curated top picks!
Technological integration
Tools and Technologies
With the rapid advancement of technology, a wide array of tools and technologies are now available to enhance the application of 3D printing in supply chain management. These technologies encompass both hardware and software solutions that work in tandem to improve the efficiency and effectiveness of 3D printing processes. On the hardware front, advancements in 3D printers have led to machines that are faster, more precise, and capable of working with a broader range of materials. For instance, the development of multi-material 3D printers allows for the creation of complex parts with varying properties in a single print run. On the software side, sophisticated design and simulation tools have emerged, enabling engineers to create highly detailed and optimized digital models. These tools often integrate with other digital technologies, such as the Internet of Things (IoT) and artificial intelligence (AI), to create a seamless and efficient supply chain. For example, IoT sensors can monitor 3D printing processes in real-time, providing valuable data that can be used to optimize production and reduce downtime. By leveraging these tools and technologies, organizations can enhance the integration of 3D printing into their supply chains and unlock new opportunities for innovation and efficiency.
Impact of Digital Transformation
The ongoing digital transformation in supply chain management is reshaping the landscape, and 3D printing is a significant catalyst in this change. Digitalization involves the adoption of digital technologies and processes to improve efficiency, accuracy, and responsiveness in supply chains. 3D printing plays a crucial role in this transformation by enabling on-demand manufacturing, reducing reliance on traditional production methods, and facilitating mass customization. For instance, companies can use 3D printing to produce parts and products closer to the point of use, reducing transportation costs and lead times. This capability is particularly valuable in industries with high demand volatility, such as consumer electronics and fashion, where trends and consumer preferences can change rapidly. Moreover, the integration of 3D printing with other digital technologies, such as blockchain and AI, offers new opportunities for enhancing supply chain transparency, traceability, and security. According to a report by Accenture, digital transformation initiatives, including 3D printing, have the potential to reduce operational costs by up to 40% and increase revenue by up to 30%. This transformative impact underscores the importance of digitalization in modern supply chains and the strategic role of 3D printing in driving this change.
Case studies and real-world applications
Successful implementations
Successful implementations
Case studies provide valuable insights into the practical application of 3D printing in supply chain management. One notable example is the partnership between Adidas and Carbon, a 3D printing company, to revolutionize the production of athletic footwear. By leveraging Carbon's digital light synthesis technology, Adidas was able to produce the Futurecraft 4D midsole, a high-performance component with a unique lattice structure that enhances comfort and stability. This collaboration not only streamlined the production process but also enabled Adidas to offer customized products tailored to individual customer needs. The success of this implementation demonstrates the potential of 3D printing to drive innovation and differentiation in competitive markets. Another example is Siemens, which has integrated 3D printing into its supply chain for the production of spare parts and components for its industrial equipment. By creating digital inventories and producing parts on-demand, Siemens has significantly reduced lead times and inventory costs while improving service levels. These successful implementations highlight the tangible benefits and innovations that can be achieved through the integration of 3D printing into supply chains.
Lessons learned
Lessons learned
From these real-world applications, several lessons can be gleaned to guide future implementations of 3D printing in SCM. One key lesson is the importance of aligning 3D printing initiatives with strategic business objectives. Companies that successfully integrate 3D printing into their supply chains do so with a clear understanding of how the technology can support their goals, whether it's enhancing customer satisfaction, reducing costs, or improving product quality. Another lesson is the value of collaboration and partnerships. Many successful implementations involve collaboration with technology providers, research institutions, and other stakeholders to leverage expertise and resources. Additionally, these case studies underscore the need for continuous innovation and adaptation. As 3D printing technology continues to evolve, companies must remain agile and open to new opportunities for improving their supply chain processes. Finally, it is essential to invest in staff training and development to ensure that employees have the skills and knowledge needed to effectively use and optimize 3D printing technologies. By applying these lessons, organizations can enhance their 3D printing strategies and achieve successful outcomes in SCM.
Related:
Regenerative Business ModelsClick here to read our expertly curated top picks!
Future trends
Emerging Developments
As technology continues to advance, new developments in 3D printing are emerging that promise to further revolutionize supply chain management. One of the most exciting trends is the rise of distributed manufacturing, where 3D printing enables the production of goods closer to the point of consumption. This shift has the potential to significantly reduce transportation costs, lead times, and carbon footprints. For example, companies can set up local 3D printing hubs to produce spare parts on-demand, reducing the need for large inventories and extensive logistics networks. Another emerging trend is mass customization, where 3D printing allows for the creation of personalized products at scale. In industries such as fashion and consumer electronics, this capability offers a competitive advantage by enabling companies to meet unique customer preferences and enhance the overall consumer experience. Additionally, advancements in materials science are expanding the range of materials that can be used in 3D printing, opening up new possibilities for innovation in sectors such as healthcare, aerospace, and automotive. These emerging developments highlight the transformative potential of 3D printing and its ability to reshape the future of supply chain management.
Predictions and Projections
Drawing on expert opinions and market analysis, several predictions can be made regarding the future trajectory of 3D printing in SCM. According to a report by Grand View Research, the global 3D printing market is expected to grow at a compound annual growth rate (CAGR) of 23.3% from 2021 to 2028, reflecting the increasing adoption of this technology across various industries. Experts predict that the continued development of 3D printing technologies, coupled with advancements in digitalization and automation, will drive significant improvements in supply chain efficiency and flexibility. As a result, companies will be able to respond more quickly to changing market conditions, reduce costs, and enhance customer satisfaction. Additionally, the integration of 3D printing with other emerging technologies, such as AI and blockchain, is expected to further enhance supply chain transparency, security, and traceability. These projections offer a glimpse into how supply chains might evolve over the coming years and the role that 3D printing will play in shaping this evolution. For project managers and supply chain professionals, staying abreast of these trends and developments will be crucial for maintaining a competitive edge in the future.
Related:
Youth And EntrepreneurshipClick here to read our expertly curated top picks!
Do's and don'ts
Do's | Don'ts |
---|---|
Conduct thorough market research | Ignore the initial setup costs |
Invest in quality materials and tech | Cut corners on safety and compliance |
Train staff and encourage innovation | Overlook the importance of data security |
Establish clear performance metrics | Rely solely on 3D printing for all products |
Foster collaboration across teams | Neglect continuous improvement efforts |
Commonly asked questions on 3d printing in scm
What are the primary benefits of using 3D printing in SCM?
The primary benefits of using 3D printing in supply chain management include cost reduction, speed, and customization. By producing parts and products on-demand and closer to the point of use, companies can significantly reduce inventory and transportation costs. Additionally, the ability to create complex geometries and highly customized products enables organizations to meet unique customer needs and enhance overall satisfaction. According to a survey by Deloitte, companies that integrate 3D printing into their supply chains report a 25% increase in market responsiveness and a 30% reduction in lead times. These benefits highlight the strategic value of 3D printing in optimizing supply chain operations and achieving competitive advantage.
How does 3D printing affect inventory management?
3D printing has a significant impact on inventory management by enabling on-demand production and reducing the need for large inventories. With 3D printing, companies can produce parts and products as needed, reducing the costs and risks associated with holding excess inventory. This capability is particularly valuable in industries with high demand volatility, where trends and customer preferences can change rapidly. By adopting a just-in-time production approach, organizations can improve inventory turnover, reduce storage costs, and enhance overall supply chain efficiency. Additionally, digital inventories of 3D printable parts can be maintained, allowing for quick and flexible production in response to customer demands.
What challenges might companies face when integrating 3D printing?
While the benefits of 3D printing in SCM are substantial, companies may face several challenges when integrating this technology. One common challenge is the technical limitations of 3D printing, including limitations in speed, material properties, and the size of printable parts. Additionally, skill gaps in the workforce can pose challenges, as employees may require training and development to effectively operate and optimize 3D printing technologies. Another challenge is the initial cost of setting up 3D printing infrastructure and integrating it with existing systems. To overcome these challenges, organizations should invest in staff training, collaborate with technology providers, and conduct pilot testing to validate processes and identify potential issues. By addressing these challenges proactively, companies can successfully integrate 3D printing into their supply chains and achieve desired outcomes.
Can 3D printing contribute to sustainability in supply chains?
Yes, 3D printing can contribute to sustainability in supply chains by reducing waste, minimizing transportation-related emissions, and promoting eco-friendly practices. Unlike traditional manufacturing methods, which often involve cutting away excess material, 3D printing uses only the material necessary to create a part, resulting in less waste. Additionally, by enabling on-demand production and local manufacturing, 3D printing can reduce the environmental impact associated with transportation and logistics. For example, companies can establish local 3D printing hubs to produce parts closer to the point of use, reducing the need for long-distance shipping and associated carbon emissions. According to a report by the World Economic Forum, 3D printing has the potential to reduce material waste by up to 90% and decrease energy consumption by up to 50%. These sustainability benefits highlight the strategic value of 3D printing in promoting eco-friendly practices and achieving environmental goals.
How do I determine if 3D printing is right for my supply chain?
To determine if 3D printing is right for your supply chain, it is important to evaluate the specific needs and goals of your business. Consider factors such as the complexity and customization requirements of your products, the potential for cost savings and efficiency improvements, and the alignment with your strategic objectives. Additionally, assess the readiness of your organization to adopt 3D printing technology, including the availability of suitable materials and expertise. Conducting a comprehensive analysis of your current supply chain processes and identifying areas where 3D printing can add value can provide valuable insights into its suitability for your business. By carefully evaluating these factors, you can make an informed decision about the potential benefits and challenges of integrating 3D printing into your supply chain.
Click here to read our expertly curated top picks!
Conclusion
Summing Up
The transformative potential of 3D printing in supply chain management cannot be overstated. By offering unprecedented flexibility, customization, and efficiency, this technology has the ability to revolutionize traditional manufacturing and supply chain practices. From reducing lead times and production costs to enhancing sustainability and customer satisfaction, the benefits of 3D printing are substantial. As we have explored throughout this article, the integration of 3D printing into SCM requires careful planning, execution, and optimization. By understanding the historical development, core concepts, strategic implementation, and future trends of 3D printing, supply chain professionals and project managers can effectively leverage this technology to enhance efficiency, innovation, and competitiveness.
Final Thoughts
In a rapidly changing business environment, staying competitive requires continuous innovation and adaptation. For supply chain professionals and project managers, embracing 3D printing technologies offers a unique opportunity to drive progress and achieve strategic goals. By investing in the right tools and technologies, fostering collaboration and innovation, and continuously monitoring and optimizing processes, organizations can unlock the full potential of 3D printing and achieve meaningful improvements in their supply chain operations. As we look to the future, the role of 3D printing in shaping the evolution of supply chains is set to expand, offering new opportunities for innovation and efficiency. By staying informed and proactive, professionals can position themselves to lead the way in the modern supply chain landscape and drive lasting success.
Navigate supply chain management with Meegle. Sign up for free and see the difference!
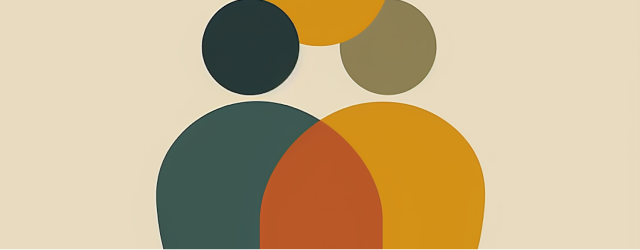
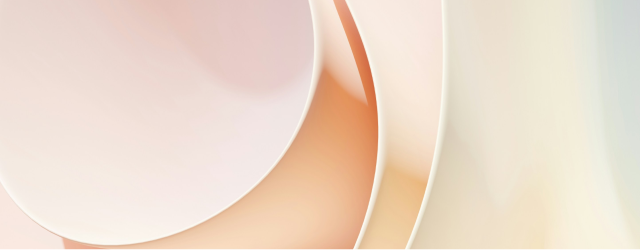
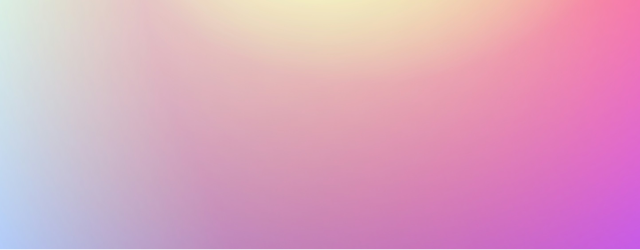
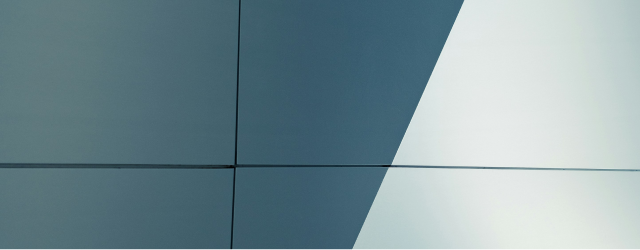
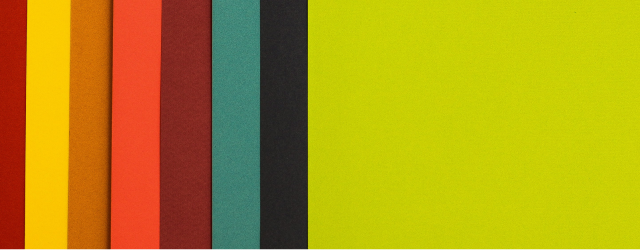
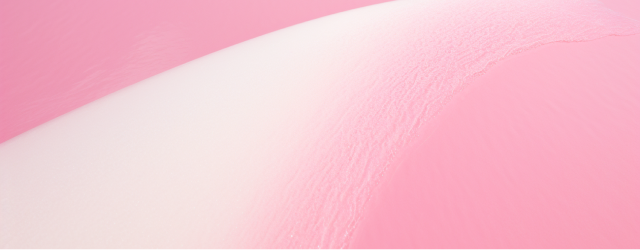
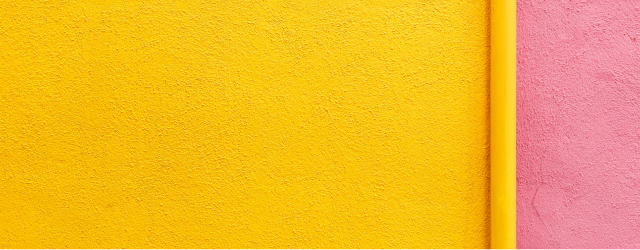
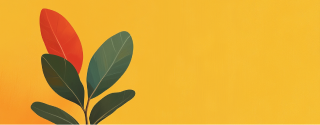