Value Stream Mapping
Streamline your supply chain operations with our expert insights on Value Stream Mapping, providing you with the know-how to boost efficiency and effectiveness.
Background of Value Stream Mapping
Value Stream Mapping is a methodological approach employed to visualize and analyze the flow of materials and information throughout the supply chain. Originating from lean manufacturing principles, VSM is a critical component of the Toyota Production System, which revolutionized the way manufacturing processes were conducted. The goal of VSM is to identify and eliminate waste, thus enhancing value creation for both the business and its customers. By mapping out the current state of a process, organizations can pinpoint inefficiencies and develop a future state map that represents an ideal, streamlined process.
In the supply chain ecosystem, VSM serves as a powerful tool for identifying bottlenecks, redundancies, and non-value-adding activities. The technique involves creating a visual representation of the entire production or service process, from raw material acquisition to the delivery of the final product. This visualization allows stakeholders to understand the interconnectedness of various processes, facilitating informed decision-making and strategic improvements.
Importance in Today’s Market
In today's rapidly changing business environment, the importance of VSM cannot be overstated. Supply chains face mounting pressures to enhance efficiency, minimize waste, and swiftly respond to market fluctuations. VSM addresses these challenges by providing a structured approach to process improvement. By identifying areas of waste and inefficiency, businesses can implement targeted solutions that lead to significant cost savings and improved customer satisfaction.
Furthermore, in a technology-driven landscape, businesses must be agile and responsive to maintain a competitive edge. VSM supports these objectives by offering a clear view of the entire supply chain, enabling organizations to adapt quickly to changes in demand, regulatory requirements, and industry trends. The integration of VSM into supply chain strategies is not merely an option but a necessity for businesses aiming to thrive in today's market. As organizations continue to embrace digital transformation, the application of VSM becomes even more relevant, offering a bridge between traditional process improvement methodologies and modern technological advancements. By leveraging VSM, businesses can optimize their operations and position themselves for long-term success in a competitive and ever-evolving marketplace.
Navigate supply chain management with Meegle. Sign up for free and see the difference!
Historical development
Origins of Value Stream Mapping
The concept of Value Stream Mapping has its roots deeply embedded in the principles of lean manufacturing, particularly within the renowned Toyota Production System (TPS). Developed in the mid-20th century, TPS introduced innovative concepts aimed at minimizing waste while maximizing efficiency in manufacturing processes. VSM was a cornerstone of this system, offering a method for visualizing and analyzing the flow of materials and information in a production setting. This innovative approach enabled Toyota to significantly enhance production efficiency, reduce lead times, and improve product quality, setting a new standard in manufacturing excellence.
The early adoption of VSM in manufacturing allowed organizations to gain unprecedented insights into their processes, identifying waste and inefficiencies that were previously hidden. By mapping the current state of their operations, businesses were able to develop future state maps that represented an ideal, waste-free process. This approach not only improved operational efficiency but also fostered a culture of continuous improvement, where employees at all levels were engaged in identifying and implementing process enhancements. As a result, VSM became a fundamental tool in the arsenal of lean practitioners, driving significant improvements in manufacturing performance.
Evolution Over Time
Over the years, the application of VSM has extended far beyond its manufacturing origins. As businesses across various industries recognized the value of visualizing and optimizing processes, VSM found its way into sectors such as healthcare, logistics, and service industries. This expansion was driven by the realization that the principles of lean manufacturing could be applied to any process involving the flow of materials or information, regardless of industry. By adapting VSM to suit their unique needs, organizations were able to achieve similar improvements in efficiency and value delivery.
In the context of global and digital supply chains, VSM has evolved to address the complex challenges associated with managing operations across multiple geographies and digital platforms. As supply chains become more interconnected and reliant on digital technologies, the ability to visualize and optimize these processes becomes increasingly critical. VSM has adapted to meet these demands, incorporating advanced tools and technologies to enhance its effectiveness. For example, the integration of data analytics and Internet of Things (IoT) technologies has enabled organizations to gain deeper insights into their supply chain operations, facilitating more informed decision-making and strategic improvements.
The evolution of VSM continues as businesses explore new ways to leverage its capabilities in a rapidly changing landscape. As organizations embrace digital transformation and strive for greater sustainability, VSM is poised to play an even more significant role in shaping the future of supply chain management. By continuously adapting to the needs of modern businesses, VSM remains a vital tool for driving efficiency, reducing waste, and enhancing value across all aspects of supply chain operations.
Click here to read our expertly curated top picks!
Core concepts
Defining Value Stream Mapping
To fully grasp the utility of Value Stream Mapping (VSM), one must start by understanding its fundamental definition. At its core, VSM is a lean-management technique used to visualize and analyze the flow of materials and information required to bring a product or service to a consumer. The primary purpose of VSM is to identify and eliminate waste, thereby enhancing the overall efficiency and effectiveness of the supply chain. A typical VSM consists of several components, including processes, value-adding activities, and non-value-adding activities, providing a comprehensive view of the entire value stream.
In the context of VSM, a "process" refers to any operation or series of actions involved in the production or delivery of a product or service. These processes are broken down into individual steps, each of which is assessed for its contribution to value creation. Value-adding activities are those that directly enhance the product or service in a way that the customer is willing to pay for, such as assembly or quality testing. Conversely, non-value-adding activities are those that do not contribute to the ultimate value of the product and are often targets for elimination or improvement. By differentiating between these activities, VSM provides a clear framework for identifying inefficiencies and prioritizing improvement efforts.
Notable Features
Several key features distinguish VSM from other process analysis tools, contributing to its effectiveness in optimizing supply chain operations. One of the most notable features of VSM is its visual nature. By creating a visual map of the entire value stream, VSM enables stakeholders at all levels of an organization to gain a clear and intuitive understanding of the processes involved. This visualization facilitates communication and collaboration, ensuring that everyone is aligned in their efforts to improve efficiency and reduce waste.
Another defining feature of VSM is its focus on eliminating waste. In lean manufacturing, waste is classified into several categories, including defects, overproduction, waiting, and transportation, among others. VSM provides a structured approach for identifying and addressing these forms of waste, driving significant improvements in process efficiency and value creation. By reducing waste, organizations can lower costs, shorten lead times, and enhance customer satisfaction.
VSM also plays a critical role in fostering a culture of continuous improvement. By regularly conducting VSM exercises, organizations can maintain an ongoing focus on process optimization, ensuring that improvements are sustained over time. This commitment to continuous improvement is essential in today's dynamic business environment, where organizations must be agile and responsive to remain competitive. By embedding VSM into the fabric of their operations, businesses can cultivate a culture of innovation and efficiency, positioning themselves for long-term success.
Strategic implementation
Planning and Execution
Effective implementation of Value Stream Mapping (VSM) within a supply chain context requires careful planning and execution. The first step in this process is assembling a cross-functional team that includes representatives from various departments involved in the value stream. This diverse team approach ensures a comprehensive understanding of the processes being analyzed and fosters collaboration and buy-in from all stakeholders. Once the team is assembled, it is important to clearly define the scope of the VSM initiative, including the specific processes or areas to be mapped and analyzed.
Data collection is a critical component of the planning phase, as accurate and comprehensive data is essential for creating an effective value stream map. This data may include information on process flow, lead times, inventory levels, and resource utilization, among other variables. The team should work together to gather and analyze this data, identifying key areas of focus for the VSM exercise. It is also important to establish clear objectives and goals for the initiative, aligning the efforts of the team with the strategic priorities of the organization.
The execution phase involves creating the current state map, which visually represents the existing flow of materials and information within the supply chain. This map serves as a baseline for identifying inefficiencies and opportunities for improvement. Once the current state map is completed, the team can work collaboratively to develop a future state map that represents an ideal, streamlined process. This future state map serves as a roadmap for implementing targeted improvements and achieving the strategic objectives of the VSM initiative.
Best Practices
To maximize the effectiveness of VSM implementation, several best practices should be observed. Engaging cross-functional teams is essential, as it ensures a holistic understanding of the value stream and facilitates collaboration across different departments. Maintaining open and transparent communication with all stakeholders is also important, as it fosters buy-in and support for the initiative. Regular updates and progress reports can help keep stakeholders informed and engaged throughout the process.
Focusing on actionable insights is another best practice for successful VSM implementation. The goal of VSM is not only to identify inefficiencies but also to develop concrete solutions that can be implemented to drive improvements. By prioritizing actionable insights, organizations can ensure that their VSM efforts lead to tangible results and meaningful enhancements in supply chain performance.
Continuous monitoring and adaptation are also key to the success of VSM initiatives. The dynamic nature of supply chains means that processes and conditions are constantly changing, requiring ongoing attention and adjustment. By regularly reviewing and updating value stream maps, organizations can maintain a focus on continuous improvement and ensure that their supply chain operations remain optimized and aligned with strategic objectives.
Related:
Cashier-Less Store TechnologyClick here to read our expertly curated top picks!
Technological integration
Tools and Technologies
The integration of modern tools and technologies has significantly enhanced the capabilities and effectiveness of Value Stream Mapping (VSM). In today's digital landscape, a range of software applications and data analytics tools are available to facilitate the mapping and analysis process, providing organizations with deeper insights into their supply chain operations. These tools allow for more accurate data collection, visualization, and analysis, enabling businesses to make informed decisions and implement targeted improvements with greater precision.
Software applications designed for VSM offer features such as automated data collection, real-time process monitoring, and advanced visualization capabilities. These tools enable organizations to create detailed value stream maps quickly and efficiently, reducing the time and effort required for manual mapping exercises. Additionally, data analytics tools provide valuable insights into process performance, allowing businesses to identify trends, patterns, and opportunities for optimization that may not be immediately apparent through traditional analysis methods.
The Internet of Things (IoT) is another technology that has revolutionized VSM by providing real-time data on supply chain operations. IoT devices can monitor and report on various aspects of the value stream, such as inventory levels, machine performance, and transportation status. This real-time data allows organizations to gain a comprehensive and up-to-date view of their supply chain, facilitating more responsive and agile decision-making. By leveraging these technologies, businesses can enhance the accuracy and effectiveness of their VSM efforts, driving significant improvements in efficiency and value creation.
Impact of Digital Transformation
Digital transformation initiatives are reshaping the adoption and evolution of VSM, offering new opportunities and challenges for organizations seeking to optimize their supply chain operations. As businesses increasingly embrace digital technologies, the integration of VSM into digital supply chain strategies becomes a critical component of success. Digital transformation enables organizations to leverage advanced tools and technologies to enhance the effectiveness of their VSM efforts, providing deeper insights and more informed decision-making.
One of the primary benefits of integrating VSM into digital supply chain strategies is the ability to gain real-time visibility into operations. Digital tools and technologies provide up-to-date data and insights, allowing organizations to respond quickly to changes in demand, supply chain disruptions, and other challenges. This real-time visibility enhances agility and responsiveness, enabling businesses to maintain a competitive edge in a rapidly changing market.
However, digital transformation also presents challenges for VSM adoption. The complexity and scale of digital supply chains require organizations to adapt their VSM methodologies to accommodate new technologies and data sources. Additionally, the integration of digital tools and technologies into VSM efforts requires careful planning and execution to ensure compatibility and alignment with existing processes and systems. By addressing these challenges and leveraging the opportunities presented by digital transformation, organizations can enhance the effectiveness of their VSM efforts, driving significant improvements in supply chain performance and value creation.
Case studies and real-world applications
Successful implementations
Successful implementations
Example 1: Automotive Industry
In the automotive industry, a leading company utilized Value Stream Mapping (VSM) to streamline its production processes and significantly reduce lead times. By applying VSM, the company was able to identify critical bottlenecks in its assembly line, particularly in the areas of parts supply and machine setup times. The current state map revealed that the waiting times for parts and frequent machine downtimes were the primary contributors to delays. By analyzing this data, the company implemented targeted improvements, such as enhanced supplier coordination and predictive maintenance for machinery. As a result, the company achieved a 20% reduction in lead times and a 15% increase in production efficiency, demonstrating the powerful impact of VSM on operational performance.
Example 2: Retail Giant
A major retail giant applied VSM to enhance its logistics and distribution network, aiming to improve delivery speed and reduce costs. The company mapped its entire logistics process, from order placement to final delivery, identifying inefficiencies in transportation scheduling and warehouse management. The VSM exercise revealed that suboptimal routing and excessive inventory holding were significant sources of waste. By introducing real-time route optimization software and implementing just-in-time inventory practices, the company was able to reduce transportation costs by 25% and improve delivery times by 30%. This successful implementation of VSM not only improved operational efficiency but also enhanced customer satisfaction by ensuring timely deliveries.
Example 3: Healthcare Provider
In the healthcare sector, a prominent provider used VSM to improve patient care processes and reduce waste. The organization faced challenges in managing patient flow and resource allocation, leading to extended wait times and inefficiencies in service delivery. By conducting a VSM exercise, the healthcare provider identified key areas for improvement, such as streamlined patient intake processes and optimized staffing schedules. The future state map focused on reducing non-value-adding activities, such as redundant paperwork and unnecessary patient transfers. As a result, the provider achieved a 40% reduction in patient wait times and a 20% improvement in staff productivity, demonstrating the effectiveness of VSM in enhancing service delivery and patient outcomes.
Click here to read our expertly curated top picks!
Future trends
Emerging Developments
As the business landscape continues to evolve, Value Stream Mapping (VSM) is poised to adapt and expand in response to emerging trends and technological advancements. One of the most significant developments in the field of VSM is the increased focus on sustainability. As organizations strive to reduce their environmental impact and promote sustainable practices, VSM is being leveraged to identify and eliminate waste that contributes to resource depletion and pollution. By integrating sustainability metrics into VSM exercises, businesses can enhance their environmental performance and align their operations with broader sustainability goals.
Another emerging trend in VSM is the integration of artificial intelligence (AI) and predictive analytics. These technologies offer new opportunities for enhancing the capabilities of VSM, enabling organizations to gain deeper insights into their supply chain operations and make more informed decisions. AI-powered algorithms can analyze vast amounts of data to identify patterns and trends, providing valuable predictions and recommendations for process optimization. By incorporating predictive analytics into VSM efforts, businesses can proactively address potential challenges and opportunities, enhancing their agility and responsiveness in a dynamic market.
Digital transformation continues to influence the future trajectory of VSM, with organizations increasingly incorporating digital tools and technologies into their supply chain strategies. The integration of IoT devices, data analytics platforms, and advanced software applications is reshaping the way businesses conduct VSM exercises, offering greater accuracy, efficiency, and real-time visibility. As digital technologies continue to advance, the potential for innovation in VSM is vast, providing organizations with new avenues for optimizing their supply chain operations and enhancing value creation.
Predictions and Projections
Looking ahead, experts predict that Value Stream Mapping will continue to play a pivotal role in shaping the future of supply chain management. As businesses face increasing pressures to enhance efficiency, reduce costs, and improve sustainability, VSM will remain a critical tool for achieving these strategic objectives. The ongoing integration of digital technologies is expected to drive further innovations in VSM, providing organizations with more sophisticated tools and techniques for process optimization.
In the coming years, the adoption of VSM is likely to become even more widespread, extending into new industries and sectors that have not traditionally employed lean methodologies. As organizations recognize the value of VSM in driving operational excellence and enhancing customer satisfaction, the demand for skilled professionals with expertise in VSM is expected to grow. To remain competitive in this evolving landscape, businesses will need to continuously adapt their VSM practices, embracing new technologies and methodologies to stay ahead of the curve.
As VSM continues to evolve, its role in fostering a culture of continuous improvement and innovation will become increasingly important. By embedding VSM into their strategic initiatives, organizations can cultivate a mindset of efficiency and resilience, positioning themselves for long-term success in a rapidly changing business environment. The future of VSM is bright, offering endless possibilities for enhancing supply chain performance and value creation.
Click here to read our expertly curated top picks!
Do's and dont's for value stream mapping
Do's | Dont's |
---|---|
Engage cross-functional teams | Ignore stakeholder input |
Clearly define the scope and objectives | Overcomplicate the mapping process |
Focus on actionable insights for improvement | Neglect continuous monitoring and adaptation |
Commonly asked questions of value stream mapping
What is the primary purpose of Value Stream Mapping?
The primary purpose of Value Stream Mapping (VSM) is to visualize and analyze the flow of materials and information throughout a supply chain. By creating a visual representation of the entire production or service process, VSM enables organizations to identify inefficiencies, eliminate waste, and enhance value creation. The ultimate goal of VSM is to streamline operations, reduce costs, and improve customer satisfaction by optimizing the flow of resources and information.
How does VSM differ from other process mapping techniques?
VSM differs from other process mapping techniques in several key ways. One of the most notable distinctions is its focus on the entire value stream, rather than individual processes or departments. By providing a holistic view of the entire production or service process, VSM facilitates cross-functional collaboration and alignment. Additionally, VSM places a strong emphasis on identifying and eliminating waste, driving continuous improvement and value creation. Unlike traditional process mapping methods, VSM offers a visual and intuitive approach to process analysis, enabling stakeholders at all levels to understand and contribute to optimization efforts.
What are common challenges faced during VSM implementation?
Common challenges faced during VSM implementation include resistance to change, lack of stakeholder engagement, and insufficient data collection. Resistance to change can arise when employees are hesitant to adopt new processes or methodologies. To overcome this challenge, organizations can foster a culture of continuous improvement and emphasize the benefits of VSM in enhancing efficiency and value creation. Ensuring stakeholder engagement is also critical, as it fosters collaboration and buy-in from all parties involved. Finally, accurate and comprehensive data collection is essential for effective VSM, as insufficient data can hinder the identification of inefficiencies and opportunities for improvement.
How can small businesses benefit from VSM?
Small businesses can benefit from Value Stream Mapping (VSM) by enhancing their operational efficiency and competitiveness. By visualizing and analyzing their processes, small businesses can identify inefficiencies and opportunities for optimization, leading to cost savings and improved customer satisfaction. VSM also fosters a culture of continuous improvement, enabling small businesses to adapt quickly to market changes and maintain a competitive edge. The intuitive and visual nature of VSM makes it accessible to small businesses, regardless of their industry or scale, providing a valuable tool for driving operational excellence and growth.
How does VSM contribute to sustainability in supply chains?
VSM contributes to sustainability in supply chains by identifying and eliminating waste that contributes to resource depletion and environmental impact. By optimizing processes and enhancing efficiency, VSM reduces the consumption of raw materials, energy, and other resources, promoting sustainable practices. Additionally, VSM enables organizations to incorporate sustainability metrics into their process analysis, aligning their operations with broader environmental goals. By fostering a focus on sustainability, VSM supports organizations in reducing their carbon footprint and enhancing their environmental performance, contributing to a more sustainable and responsible supply chain.
Related:
Process Flow DiagramClick here to read our expertly curated top picks!
Conclusion
Summing Up
In conclusion, Value Stream Mapping (VSM) is a powerful tool for optimizing supply chain operations and enhancing value creation. By providing a visual and comprehensive view of the entire value stream, VSM enables organizations to identify inefficiencies, eliminate waste, and implement targeted improvements. Throughout this article, we have explored the historical development and core concepts of VSM, as well as its strategic implementation and technological integration. We have also examined real-world case studies and future trends, highlighting the significance of VSM in today's dynamic business environment.
Final Thoughts
As businesses strive to maintain a competitive edge in a rapidly changing marketplace, adopting VSM as a part of their continuous improvement strategy is essential. By fostering a culture of efficiency and innovation, VSM supports organizations in achieving their strategic objectives and enhancing customer satisfaction. Whether you are new to the concept or looking to refine your existing practices, the insights and guidance provided in this article will equip you with the knowledge required to harness the full potential of VSM. Embrace VSM as a strategic tool for driving operational excellence and positioning your organization for long-term success in a competitive and ever-evolving landscape.
Navigate supply chain management with Meegle. Sign up for free and see the difference!
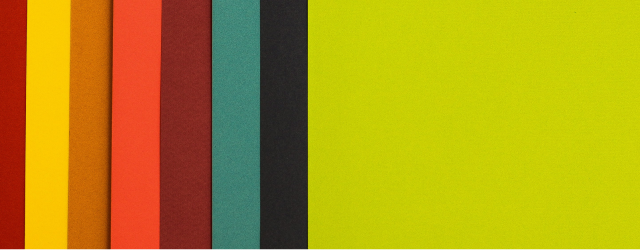
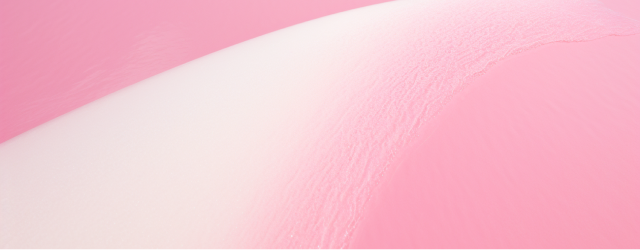
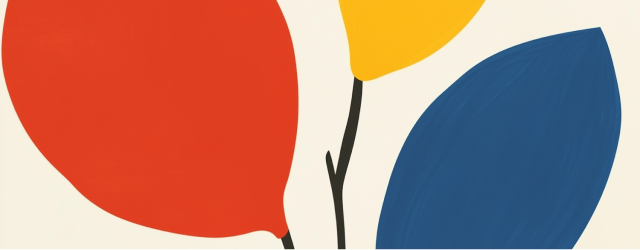
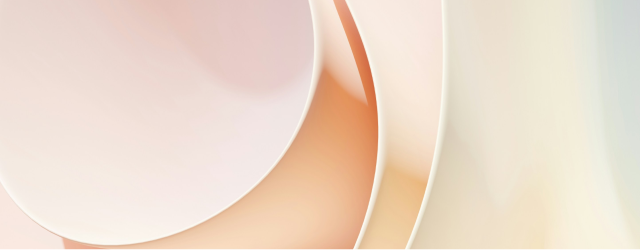
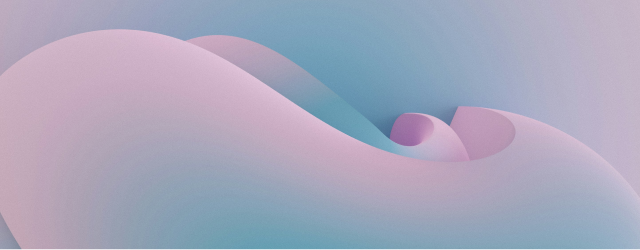
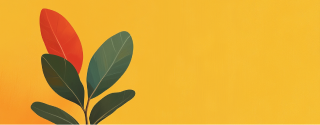
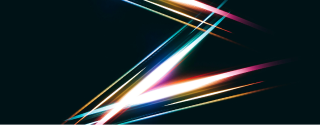
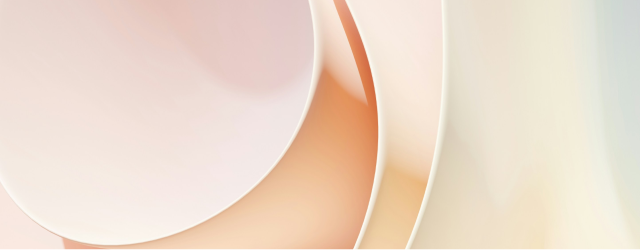