Activity-Based Costing
Streamline your supply chain operations with our expert insights on Activity-Based Costing, providing you with the know-how to boost efficiency and effectiveness.
Background of Activity-Based Costing
In the late 20th century, Activity-Based Costing emerged as a groundbreaking development in the field of cost accounting. Unlike traditional methods that allocate costs based on volume-produced, ABC assigns costs to products and services based on the actual activities and resources consumed. This new methodology offers a granular perspective of cost dynamics, which is particularly useful in the complex environment of modern supply chains. By focusing on activities, ABC highlights inefficient processes and supports optimal resource allocation, enabling supply chain managers to refine operations significantly. With supply chains becoming more intricate, understanding ABC is pivotal for professionals seeking to boost operational efficiency and make informed strategic decisions.
Importance in Today’s Market
In an era where technological advancements and rapid market shifts are commonplace, the ability to trace costs accurately and comprehend the financial implications of operational activities is crucial. ABC plays an integral role by providing insights that enable businesses to refine pricing strategies, enhance product profitability, and streamline processes. For instance, companies like Procter & Gamble have applied ABC to improve cost accuracy, leading to more strategic pricing and product line decisions. In a competitive marketplace where businesses must adapt to changing consumer demands and maintain their competitive edge, the significance of ABC in strategic planning and cost management is undeniable. By offering a detailed breakdown of activity-based costs, ABC aids managers in identifying opportunities for efficiency gains and improved profitability.
Navigate supply chain management with Meegle. Sign up for free and see the difference!
Historical development
Origins of Activity-Based Costing
The origins of Activity-Based Costing can be traced back to the manufacturing sector in the late 20th century. During this period, traditional accounting methods, primarily based on direct labor hours or machine hours, fell short in capturing the nuanced cost dynamics of manufacturing processes. As industries grew more complex, these traditional systems proved inadequate for accurately reflecting the true cost of production, especially for products with diverse production requirements. To address these inefficiencies, ABC was developed. It emphasized the need to account for costs associated with specific activities, providing more precise insights into how resources were utilized and costs incurred. This innovative approach quickly gained traction, as it allowed managers to pinpoint inefficiencies and enhance overall resource allocation.
Evolution Over Time
Since its inception, Activity-Based Costing has evolved significantly to meet the dynamic needs of global supply chains. Initially confined to the manufacturing sector, ABC's utility has expanded across various industries, including services and logistics. For example, the financial services and healthcare sectors have adopted ABC to better understand the cost implications of their operations, ultimately improving service delivery and financial performance. This evolution underscores ABC's versatility and its essential role in cost management across diverse sectors. Technological advancements have further propelled the effectiveness of ABC. With the advent of data analytics and sophisticated ABC software, companies can now perform more precise cost allocations and real-time analysis, making ABC not just a tool for cost management, but a strategic asset in supply chain optimization.
Click here to read our expertly curated top picks!
Core concepts
Defining Activity-Based Costing
At its essence, Activity-Based Costing is a method that involves identifying all significant activities within an organization and assigning costs based on the resources these activities consume. This involves breaking down overhead costs into distinct activity cost pools and then allocating these costs to products or services using specific cost drivers. Unlike traditional costing methods, which tend to rely heavily on volume-based metrics, ABC considers the actual consumption of resources. For instance, in a manufacturing setting, the costs associated with machine maintenance, setup, and quality inspections are factored into the cost of producing each unit, providing a more accurate representation of cost distribution. By linking costs directly to activities, ABC provides a precise understanding of cost allocation, thereby supporting more informed decision-making and strategic financial planning.
Notable Features
Activity-Based Costing is distinguished by several notable features that set it apart from traditional costing methods. Firstly, it provides a comprehensive breakdown of indirect costs, enabling managers to identify areas of inefficiency and waste. This aspect of ABC is particularly valuable in complex supply chains, where hidden costs can significantly impact overall profitability. Secondly, ABC enhances decision-making by linking cost data directly to business activities. This linkage aids in strategic planning, performance evaluation, and budgeting, as managers can align costs with organizational objectives more effectively. Additionally, ABC supports continuous improvement by highlighting cost variances and promoting cost control across the supply chain. By offering detailed insights into cost dynamics, ABC empowers organizations to optimize resource allocation, streamline processes, and ultimately enhance profitability.
Strategic implementation
Planning and Execution
Implementing Activity-Based Costing within an organization requires a strategic approach that encompasses meticulous planning and execution. The initial step involves identifying critical activities that drive costs within the organization. This requires cross-functional collaboration to ensure a comprehensive understanding of processes and resource allocation. Once activities are identified, appropriate cost drivers must be selected, which accurately reflect the consumption of resources. For example, in a manufacturing firm, machine hours, labor hours, and material usage might serve as cost drivers. Accurate data collection is paramount to the success of ABC implementation, as it forms the basis for cost allocation. Additionally, engaging stakeholders from various departments and providing continuous training is crucial to ensure all team members understand the methodology and its implications. A well-executed ABC plan not only aligns costs with organizational objectives but also enhances decision-making and performance evaluation.
Best Practices
To maximize the benefits of Activity-Based Costing, organizations should adhere to established best practices. Maintaining data accuracy is critical, as accurate data forms the foundation of effective cost allocations. Regularly reviewing and updating cost drivers is also essential to ensure they accurately reflect changes in business processes and resource consumption. Integrating ABC insights into broader business strategies can further enhance decision-making and strategic planning. Leveraging technology, such as ABC software and data analytics tools, can streamline the process and improve the accuracy of cost allocations. These tools offer automated data collection, real-time analysis, and user-friendly interfaces, making ABC implementation more efficient and impactful. By following these best practices, organizations can optimize their supply chains, identify cost-saving opportunities, and achieve a competitive advantage in the marketplace.
Related:
Ethics In EntrepreneurshipClick here to read our expertly curated top picks!
Technological integration
Tools and Technologies
The integration of technology has revolutionized Activity-Based Costing, offering tools that significantly enhance precision and efficiency. Modern ABC software solutions provide automated data collection, real-time cost analysis, and intuitive interfaces, making it easier for managers to implement and utilize ABC effectively. These tools allow organizations to capture detailed cost data and perform complex analyses, enabling more accurate cost allocations and insights. The advent of cloud-based platforms has further streamlined ABC implementation, providing scalability, flexibility, and accessibility. Additionally, the integration of big data analytics and machine learning algorithms enables more comprehensive cost evaluations and predictive modeling. These technological advancements allow organizations to harness the full potential of ABC, transforming cost management into a strategic asset for supply chain optimization.
Impact of Digital Transformation
Digital transformation is reshaping supply chain management, and Activity-Based Costing is no exception. The influx of digital technologies facilitates faster data processing, improved accuracy, and greater flexibility in cost analysis. As supply chains become more interconnected and data-driven, the integration of ABC with digital platforms allows for real-time monitoring and agile decision-making. This transformation empowers organizations to respond swiftly to market changes, optimize resource allocation, and enhance overall efficiency. For instance, a retail giant may integrate ABC with its digital inventory management system to track costs in real-time, enabling timely adjustments and strategic decision-making. As digital transformation continues to evolve, the role of ABC in supply chain management will become increasingly significant, paving the way for more responsive and efficient operations.
Case studies and real-world applications
Successful implementations
Successful implementations
Several companies have successfully implemented Activity-Based Costing to enhance their supply chain operations. For instance, a leading consumer goods manufacturer leveraged ABC to identify high-cost production processes. By analyzing activity-based costs, the company was able to pinpoint inefficiencies and implement targeted cost reduction initiatives. This led to increased profitability and improved product margins. Similarly, a global logistics provider used ABC to optimize routing and scheduling. By analyzing costs associated with various delivery activities, the company identified opportunities for cost savings and improved service delivery. As a result, the logistics provider achieved significant cost reductions and enhanced operational efficiency, demonstrating the power of ABC in transforming supply chain management.
Lessons learned
Lessons learned
From these real-world examples, several key lessons can be drawn. Firstly, the importance of accurate data cannot be overstated; successful ABC implementation hinges on reliable and comprehensive data collection. Without accurate data, cost allocations may be skewed, leading to incorrect insights and decisions. Secondly, cross-functional collaboration is vital, as ABC impacts multiple areas of the supply chain. By involving stakeholders from various departments, organizations can ensure a holistic approach to cost management and decision-making. Finally, continuous monitoring and adaptation are crucial to ensure that ABC remains aligned with organizational goals and evolving market conditions. Regularly reviewing and refining cost allocations allows organizations to adapt to changes and maintain the relevance of ABC insights.
Related:
Youth And EntrepreneurshipClick here to read our expertly curated top picks!
Future trends
Emerging Developments
The future of Activity-Based Costing in supply chain management is shaped by several emerging trends. The integration of artificial intelligence and machine learning is poised to revolutionize cost analysis, enabling predictive modeling and enhanced decision support. These technologies allow organizations to anticipate cost fluctuations, identify trends, and make data-driven decisions. Additionally, as sustainability becomes a core focus for many companies, ABC is evolving to incorporate environmental cost factors. This development enables organizations to evaluate the environmental impact of their operations and make more sustainable choices. By integrating financial and environmental cost data, ABC helps companies achieve both financial and ecological objectives, aligning with the growing emphasis on corporate social responsibility.
Predictions and Projections
Experts predict that Activity-Based Costing will continue to evolve, driven by technological advancements and changing business priorities. As supply chains become more transparent and accountable, the adoption of ABC is expected to increase. Companies are increasingly seeking to demonstrate responsible cost management practices, and ABC provides the tools to achieve this. Furthermore, as businesses face mounting pressure to optimize operations and reduce costs, ABC will play a critical role in identifying inefficiencies and enhancing profitability. As these trends unfold, ABC will remain a vital tool for professionals aiming to navigate the complexities of modern supply chains effectively.
Related:
Personal Budget ManagementClick here to read our expertly curated top picks!
Examples of activity-based costing in action
Example 1: manufacturing efficiency
Example 1: manufacturing efficiency
A multinational electronics manufacturer used Activity-Based Costing to identify and eliminate bottlenecks in its production line. By analyzing activity-based costs, the company was able to pinpoint inefficiencies in its processes and implement targeted improvements. This led to a 15% reduction in production costs and enhanced product quality. By reallocating resources and optimizing workflows, the manufacturer achieved significant cost savings and improved operational efficiency.
Example 2: logistics optimization
Example 2: logistics optimization
A leading logistics company implemented Activity-Based Costing to analyze and optimize its delivery routes. By examining costs associated with various delivery activities, the company identified opportunities for cost savings and improved service delivery. This resulted in a 20% reduction in fuel consumption and enhanced delivery times, demonstrating the power of ABC in transforming logistics operations. By optimizing routing and scheduling, the logistics provider achieved significant cost reductions and improved customer satisfaction.
Example 3: service industry application
Example 3: service industry application
A global consulting firm adopted Activity-Based Costing to better understand the cost dynamics of its projects. By analyzing activity-based costs, the firm gained insights into project profitability and adjusted its pricing strategies accordingly. This allowed the firm to improve client satisfaction and boost profit margins by 10%. By aligning costs with project objectives, the consulting firm achieved significant financial gains and enhanced its competitive position in the marketplace.
Do's and don'ts of activity-based costing
Do's | Don'ts |
---|---|
Ensure accurate data collection | Rely solely on traditional cost metrics |
Engage cross-functional teams | Implement ABC in isolation |
Continuously monitor and adapt | Ignore technological advancements |
Align ABC with strategic objectives | Overcomplicate the ABC model |
Invest in training and development | Neglect stakeholder engagement |
Click here to read our expertly curated top picks!
Commonly asked questions of activity-based costing
What is Activity-Based Costing and how does it differ from traditional costing methods?
Activity-Based Costing (ABC) allocates costs based on activities that drive expenses, whereas traditional costing often relies on volume-based metrics, which can lead to less accurate cost allocations. ABC provides a more detailed view of cost distribution by linking costs directly to resource consumption.
How can Activity-Based Costing benefit my supply chain management?
ABC provides detailed insights into cost structures, enabling managers to identify inefficiencies, optimize processes, and improve profitability. By offering a granular view of costs, ABC aids in strategic decision-making and performance evaluation.
What are the main challenges of implementing Activity-Based Costing?
Challenges include ensuring accurate data collection, selecting appropriate cost drivers, and maintaining stakeholder engagement throughout the process. Successful ABC implementation requires cross-functional collaboration and continuous monitoring to align with business objectives.
Can small businesses also benefit from Activity-Based Costing?
Yes, ABC can be scaled to fit businesses of all sizes, providing valuable insights into cost management and operational efficiency. By understanding the cost dynamics of their operations, small businesses can achieve cost savings and enhance profitability.
How does technology impact the implementation of Activity-Based Costing?
Technology enhances ABC by facilitating accurate data collection, real-time analysis, and seamless integration with existing business systems. Modern ABC software solutions provide automated data capture, intuitive interfaces, and advanced analytics, making ABC implementation more efficient and impactful.
Conclusion
Summing Up
Activity-Based Costing stands as a transformative tool in modern supply chain management, offering unparalleled insights into cost dynamics and operational efficiency. By understanding and leveraging ABC, professionals can drive strategic improvements, enhance profitability, and maintain a competitive edge in an ever-evolving market landscape. With its focus on activity-based cost allocations, ABC empowers organizations to optimize resource allocation, streamline processes, and achieve financial and operational excellence.
Final Thoughts
As we move towards a future defined by digital transformation and sustainability, the importance of mastering Activity-Based Costing will only grow. Professionals and aspiring project managers are encouraged to continuously learn and adapt ABC methodologies, ensuring they remain at the forefront of supply chain innovation and excellence. By embracing ABC, organizations can navigate the complexities of modern supply chains and unlock new opportunities for growth and success.
Navigate supply chain management with Meegle. Sign up for free and see the difference!
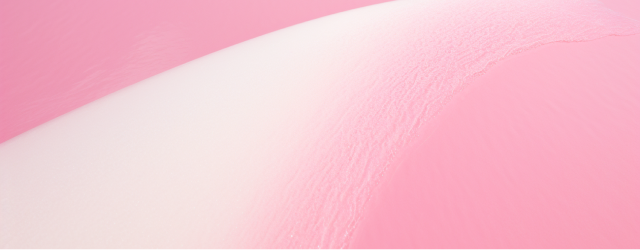
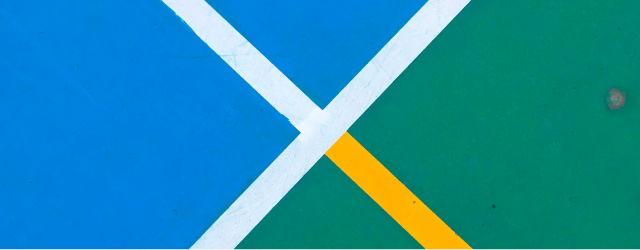
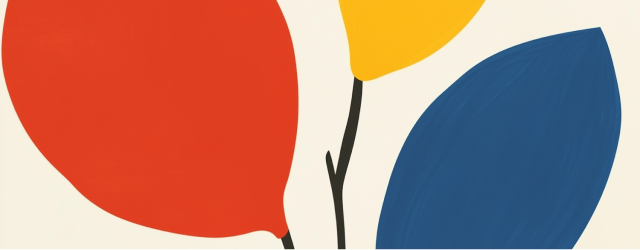
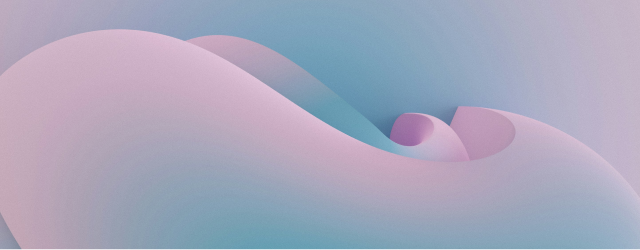
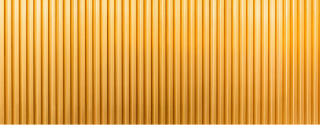
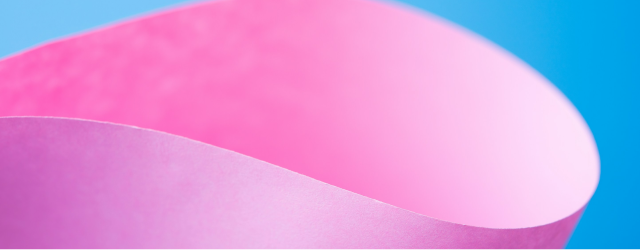
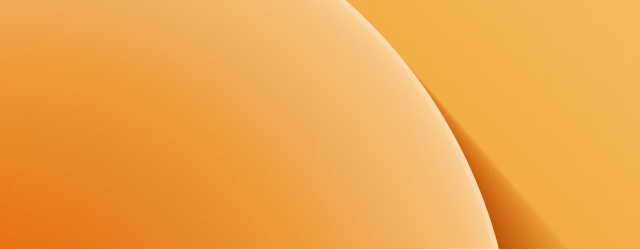
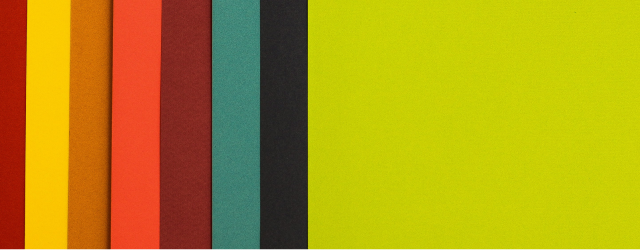