Continuous Improvement
Streamline your supply chain operations with our expert insights on Continuous Improvement, providing you with the know-how to boost efficiency and effectiveness.
Background of Continuous Improvement in Supply Chains
The concept of continuous improvement originated in the manufacturing sector, primarily through methodologies like Lean Manufacturing and Kaizen. These methods focus on iterative processes that aim to enhance efficiency, reduce waste, and optimize overall performance. In the context of supply chain management, continuous improvement involves the systematic identification and elimination of inefficiencies throughout the supply chain, from procurement to delivery. This approach prioritizes incremental changes over time, leading to significant improvements in operational effectiveness and cost savings. By applying these principles, companies can streamline their processes, enhance product quality, and respond more effectively to market demands. The adoption of continuous improvement in supply chains has become increasingly prevalent as businesses recognize its potential to drive performance and competitiveness.
Importance of Continuous Improvement in Today’s Market
In today's fast-paced, technology-driven market environment, continuous improvement is more critical than ever. As supply chains become more complex and globalized, businesses must find ways to streamline operations and enhance customer satisfaction to remain competitive. Continuous improvement provides a framework for achieving these goals by fostering a culture of ongoing learning and adaptation. By continuously evaluating and optimizing processes, companies can reduce costs, improve service delivery, and increase flexibility in responding to market changes. Furthermore, continuous improvement initiatives contribute to sustainability efforts by minimizing waste and resource consumption. In a market where customer expectations are continually evolving, businesses that embrace continuous improvement are better positioned to meet these demands and maintain a competitive edge.
Navigate supply chain management with Meegle. Sign up for free and see the difference!
Historical development of continuous improvement
Origins of Continuous Improvement Concepts
The roots of continuous improvement can be traced back to methodologies such as Kaizen and Lean Manufacturing, which emerged in the mid-20th century. Kaizen, a Japanese term meaning "change for the better," was popularized by Toyota in the 1950s as part of its production system. It emphasizes small, incremental improvements led by employees at all levels, fostering a culture of continuous enhancement. Similarly, Lean Manufacturing, developed by Toyota, focuses on eliminating waste and optimizing production processes to increase efficiency and quality. These concepts revolutionized the automotive industry and were soon adopted by other sectors globally. The success of these methodologies demonstrated the value of continuous improvement in driving operational excellence and competitive advantage, paving the way for their application in supply chain management.
Evolution of Continuous Improvement in Supply Chain Practices
As global supply chain dynamics and technological advancements have evolved, so too has the application of continuous improvement practices. In the early days, these methodologies were primarily used in manufacturing to enhance production efficiency and quality. However, as supply chains became more complex and interconnected, businesses began to recognize the potential of continuous improvement in optimizing end-to-end supply chain operations. Significant milestones in this evolution include the integration of digital technologies, such as Enterprise Resource Planning (ERP) systems, which enable real-time data collection and analysis. These technologies have enhanced the ability to identify inefficiencies and implement improvements across the supply chain. Over the decades, continuous improvement has been adapted to address challenges such as globalization, supply chain resilience, and sustainability, making it an essential tool for modern supply chain management.
Click here to read our expertly curated top picks!
Core concepts and features
Defining Continuous Improvement in Supply Chain Management
Continuous improvement in supply chain management refers to the ongoing effort to enhance processes, reduce waste, and improve overall performance through systematic and incremental changes. Key components of this approach include process optimization, waste reduction, and quality enhancement. Process optimization involves analyzing and refining each step of the supply chain to eliminate inefficiencies and maximize value. Waste reduction focuses on minimizing non-value-adding activities, such as excess inventory or unnecessary transportation, to improve cost-effectiveness and sustainability. Quality enhancement ensures that products and services meet or exceed customer expectations, contributing to increased satisfaction and loyalty. Foundational concepts supporting continuous improvement include the PDCA (Plan-Do-Check-Act) cycle, which provides a structured framework for implementing changes, and Six Sigma, a methodology that uses statistical analysis to identify and reduce defects.
Notable Features of Continuous Improvement
Several key features characterize continuous improvement in supply chain management, making it an effective approach for enhancing performance. These include systematic problem-solving, employee involvement, and data-driven decision-making. Systematic problem-solving involves using structured methodologies, such as root cause analysis, to identify and address the underlying causes of inefficiencies. Employee involvement is crucial to continuous improvement, as it empowers staff at all levels to contribute ideas and participate in improvement initiatives. This fosters a culture of collaboration and innovation, leading to more effective solutions. Data-driven decision-making leverages real-time data and analytics to inform improvement efforts, enabling businesses to make more accurate and timely decisions. By incorporating these features, companies can achieve significant improvements in efficiency, quality, and customer satisfaction, ultimately enhancing their competitive position.
Strategic implementation of continuous improvement
Planning and Execution Strategies
Effective planning and execution are critical to the success of continuous improvement initiatives in supply chain management. The first step in this process is to set clear objectives that align with the organization's strategic goals. These objectives should be specific, measurable, achievable, relevant, and time-bound (SMART) to guide the improvement efforts and assess progress. Involving stakeholders, such as employees, suppliers, and customers, is also essential to ensure buy-in and collaboration. Creating a culture of continuous learning is another key element, as it encourages openness to change and innovation. During the execution phase, it is important to prioritize initiatives based on their potential impact and feasibility, and to allocate resources accordingly. Regular monitoring and evaluation of progress are necessary to identify areas for further improvement and make necessary adjustments to the strategy. By following these steps, businesses can effectively implement continuous improvement initiatives and achieve sustained success.
Best Practices for Optimizing Continuous Improvement
To optimize continuous improvement efforts in supply chain management, businesses should adopt several best practices. First, leadership plays a vital role in driving and supporting improvement initiatives, as strong leadership commitment ensures that resources and attention are dedicated to these efforts. Team collaboration is also crucial, as cross-functional teams bring diverse perspectives and expertise to problem-solving, leading to more innovative solutions. Regular performance reviews should be conducted to assess the effectiveness of improvement initiatives and identify areas for further enhancement. Additionally, businesses should foster a culture of continuous learning, where employees are encouraged to develop their skills and knowledge continuously. This culture supports ongoing improvement and adaptation to changing market conditions. By following these best practices, companies can maximize the impact of their continuous improvement efforts and achieve long-lasting benefits.
Related:
Cashier-Less Store TechnologyClick here to read our expertly curated top picks!
Technological integration in continuous improvement
Tools and Technologies Enhancing Continuous Improvement
The integration of modern technologies plays a significant role in enhancing continuous improvement initiatives in supply chain management. Several tools and solutions facilitate these efforts by enabling real-time data collection, process automation, and predictive analytics. Enterprise Resource Planning (ERP) systems, for example, provide comprehensive visibility into supply chain operations, allowing businesses to monitor performance, identify inefficiencies, and implement improvements. The Internet of Things (IoT) is another valuable technology, as it enables the collection of real-time data from connected devices, providing insights into areas such as inventory levels, equipment performance, and transportation status. AI-driven analytics offer advanced capabilities for analyzing large volumes of data, identifying patterns, and predicting future trends, supporting more informed decision-making. By leveraging these technologies, businesses can streamline processes, reduce costs, and enhance overall supply chain performance.
Impact of Digital Transformation on Continuous Improvement
Digital transformation has had a profound impact on continuous improvement processes in supply chain management, enabling more agile, responsive, and customer-centric operations. By digitizing processes and leveraging advanced technologies, companies can achieve greater efficiency and flexibility in their supply chains. This transformation allows for real-time data collection and analysis, facilitating more accurate decision-making and faster response to changes in demand or supply conditions. Additionally, digital tools enable automation of routine tasks, freeing up resources for more strategic activities and reducing the risk of errors. Customer engagement is also enhanced through digital channels, allowing for more personalized and responsive service. As businesses continue to embrace digital transformation, the opportunities for continuous improvement will expand, driving further gains in efficiency, sustainability, and customer satisfaction.
Case studies and real-world applications
Successful implementations
Successful implementations
Example 1: Toyota's Lean Manufacturing Model
Toyota's implementation of the Lean Manufacturing Model is a prime example of successful continuous improvement. By focusing on waste elimination and process optimization, Toyota has created a culture of continuous improvement that permeates its entire organization. Key strategies include the use of Kaizen, which involves small, incremental changes led by employees, and Jidoka, which emphasizes building quality into each step of the production process. These practices have led to significant improvements in efficiency, quality, and customer satisfaction, positioning Toyota as a leader in operational excellence.
Example 2: Amazon's Supply Chain Optimization
Amazon's approach to continuous improvement in its supply chain operations is another notable example. By leveraging automation and data analytics, Amazon has optimized its supply chain to achieve faster delivery times, lower costs, and enhanced customer satisfaction. The use of advanced technologies, such as robotic automation and AI-driven analytics, enables Amazon to identify inefficiencies and implement improvements in real-time. These initiatives have contributed to Amazon's ability to meet growing customer demands and maintain a competitive edge in the e-commerce market.
Example 3: Unilever's Sustainable Supply Chain Practices
Unilever's commitment to sustainability through continuous improvement is evident in its supply chain practices. By focusing on resource efficiency and waste reduction, Unilever has implemented initiatives that reduce environmental impact and enhance sustainability. Key strategies include optimizing packaging to reduce waste, improving energy efficiency in manufacturing processes, and collaborating with suppliers to promote sustainable practices. These efforts have resulted in significant improvements in resource efficiency and environmental performance, aligning with Unilever's broader sustainability goals.
Lessons learned from real-world applications
Lessons learned from real-world applications
From these examples, several key insights and takeaways can be gleaned. A common challenge faced in continuous improvement initiatives is resistance to change, which can be overcome by fostering a culture of openness and collaboration. Leadership commitment is also crucial, as it ensures that resources and attention are dedicated to improvement efforts. Additionally, leveraging technology and data-driven decision-making enhances the effectiveness of continuous improvement initiatives, enabling businesses to identify and address inefficiencies more effectively. By learning from these experiences, companies can better navigate the challenges and opportunities of continuous improvement in supply chain management.
Click here to read our expertly curated top picks!
Future trends in continuous improvement
Emerging Developments Shaping Continuous Improvement
Several emerging trends and developments are shaping the future of continuous improvement in supply chains. One key area is sustainability, as businesses increasingly focus on reducing their environmental impact and enhancing resource efficiency. The circular economy, which emphasizes reusing and recycling materials, is gaining traction as a framework for sustainable supply chain practices. Another significant trend is Industry 4.0, which involves the integration of digital technologies and automation into manufacturing and supply chain processes. This transformation enables more agile, responsive, and customer-centric operations, supporting continuous improvement efforts. As these trends continue to evolve, businesses will have new opportunities to enhance their supply chain performance and sustainability.
Predictions and Projections for Continuous Improvement
Experts predict that continuous improvement will continue to evolve over the next decade, driven by technological advancements and changing market demands. As businesses increasingly adopt digital tools and automation, the potential for efficiency gains and cost savings will expand. Additionally, the focus on sustainability and the circular economy will drive further innovation in supply chain practices. However, challenges such as resistance to change and the need for skilled talent may pose barriers to implementation. To address these challenges, businesses will need to invest in training and development to build the necessary skills and foster a culture of continuous learning. By staying ahead of these trends and adapting to new opportunities, companies can achieve sustained success in their continuous improvement efforts.
Click here to read our expertly curated top picks!
Tips: do's and don'ts of continuous improvement
Do's | Don'ts |
---|---|
Encourage collaboration and open communication | Ignore employee feedback and involvement |
Set clear, achievable goals and metrics | Set vague or unrealistic improvement targets |
Leverage technology for data-driven insights | Rely solely on traditional methods without considering technological advancements |
Foster a culture of continuous learning and adaptation | Resist change and innovation in processes |
Regularly review and adjust improvement strategies | Implement changes without proper evaluation and monitoring |
Related:
Cashier-Less Store TechnologyClick here to read our expertly curated top picks!
Conclusion
Summing Up the Importance and Impact of Continuous Improvement
Continuous improvement plays a critical role in achieving supply chain excellence and competitiveness. By fostering a culture of ongoing learning and adaptation, businesses can streamline operations, reduce costs, and enhance customer satisfaction. The benefits of adopting a systematic approach to continuous improvement are numerous, including improved efficiency, quality, and sustainability, ultimately leading to long-term success.
Final Thoughts on Continuous Improvement Strategies
Businesses must continue to explore and integrate continuous improvement strategies to adapt to changing market demands. By staying ahead of emerging trends and leveraging technological advancements, companies can achieve sustained success in their improvement efforts. A continuous learning mindset is essential to sustaining long-term success in supply chain management, as it enables businesses to remain agile and responsive in the face of evolving challenges and opportunities.
Navigate supply chain management with Meegle. Sign up for free and see the difference!
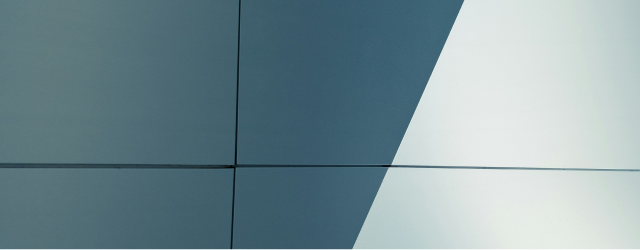
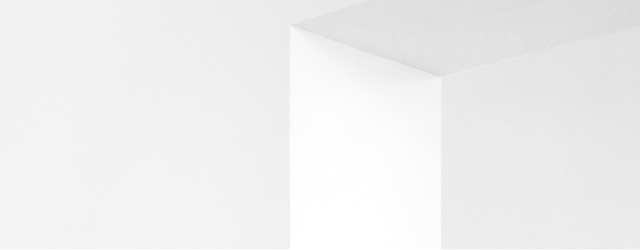
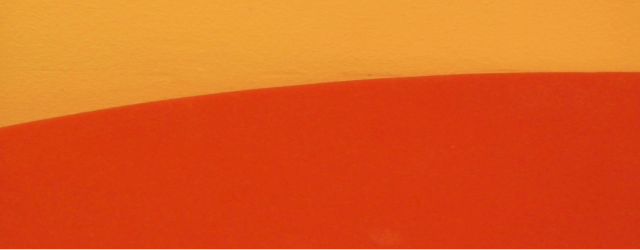
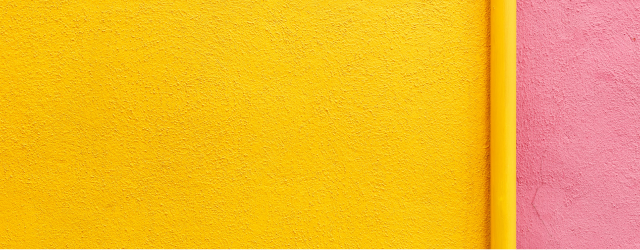
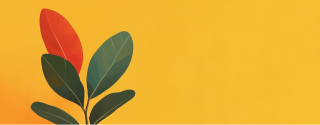
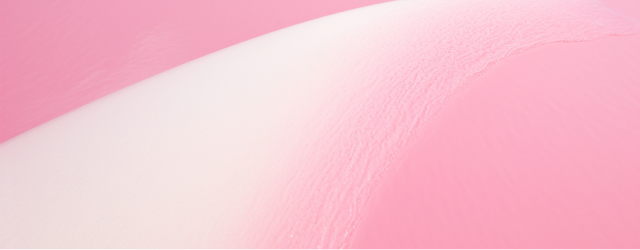
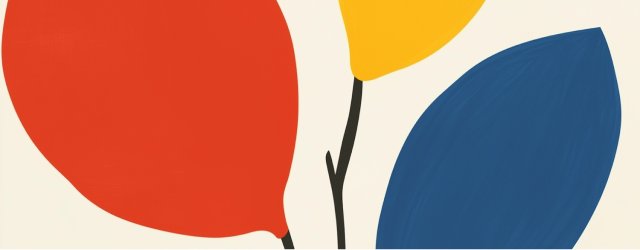