Palletization
Streamline your supply chain operations with our expert insights on Palletization, providing you with the know-how to boost efficiency and effectiveness.
Background of Palletization
Palletization is a critical process within supply chain management that involves the use of pallets to consolidate products for easier handling, storage, and transportation. Essentially, a pallet serves as a flat transport structure that supports goods in a stable manner while being lifted by forklifts, pallet jacks, or other machinery. By organizing goods onto pallets, businesses can optimize space utilization within warehouses and enable more efficient transportation of products. The role of palletization in supply chains cannot be overstated, as it facilitates the seamless movement of goods from manufacturing plants to distribution centers and ultimately to retail outlets or end consumers. This process not only simplifies the handling of goods but also enhances the speed and efficiency of operations by enabling faster loading and unloading of trucks and containers. Furthermore, palletization reduces the risk of product damage during transit, as it provides a stable platform that mitigates the impact of movement and handling.
Importance in Today’s Market
In the contemporary marketplace, the significance of palletization is amplified by the dynamics of global trade and the exponential growth of e-commerce. As businesses strive to meet the demands of a globalized economy, efficient supply chain operations become paramount. Mastering palletization is essential for businesses to achieve cost savings through reduced labor and transportation expenses. By optimizing pallet configuration and load planning, companies can maximize the use of available space in trucks and containers, leading to lower shipping costs. Additionally, effective palletization improves worker safety by minimizing the need for manual handling and reducing the risk of injuries associated with lifting heavy loads. An exemplary illustration of palletization's importance is evident in the operations of leading logistics companies, where the adoption of automated palletization systems has resulted in significant reductions in labor costs and lead times. As businesses continue to navigate the complexities of global supply chains, a thorough understanding of palletization will serve as a critical asset in ensuring operational efficiency and maintaining a competitive advantage.
Navigate supply chain management with Meegle. Sign up for free and see the difference!
Historical development
Origins of Palletization
The concept of palletization traces its origins back to the early 20th century, during the industrial era when the need for efficient handling of goods became apparent. Prior to the advent of pallets, goods were primarily transported in bulk or in crates, requiring extensive manual labor for loading and unloading. This method was not only time-consuming but also prone to product damage and inefficiencies. The introduction of wooden pallets marked a significant turning point, as they facilitated the stacking and transportation of goods in a more organized manner. The development of the forklift in the 1920s further revolutionized palletization, enabling the lifting and movement of loaded pallets with ease. As industries expanded and global trade intensified, the need for standardized pallet dimensions emerged, leading to the establishment of the first standardized pallet sizes in the mid-20th century. This standardization played a crucial role in streamlining logistics operations and enhancing interoperability between different modes of transportation.
Evolution Over Time
Over the decades, palletization has undergone significant technological and methodological advancements that have shaped its evolution within supply chains. The development of materials such as plastic and metal pallets has provided alternatives to traditional wooden pallets, offering benefits such as increased durability, ease of cleaning, and resistance to pests. Technological innovations have also played a pivotal role in enhancing palletization processes. Automation has become a cornerstone of modern palletization strategies, with automated palletizers and depalletizers being widely adopted across industries. These machines, often integrated with advanced robotics and sensors, enable the precise and efficient stacking and unstacking of goods on pallets, reducing the reliance on manual labor. Furthermore, the integration of Radio-Frequency Identification (RFID) technology and the Internet of Things (IoT) has enabled real-time tracking and monitoring of palletized goods throughout the supply chain, enhancing visibility and control. As palletization continues to evolve, it remains an indispensable element of supply chain operations, driving efficiency and innovation.
Click here to read our expertly curated top picks!
Core concepts
Defining Palletization
Palletization can be defined as the process of placing goods on pallets for the purpose of storage, handling, and transportation. It involves the strategic arrangement of products on a pallet to optimize space utilization and ensure stability during transit. The components of palletization include the pallet itself, which serves as the base platform, as well as the loading methods and stacking techniques employed to arrange the goods. There are several types of pallets used in palletization, each with distinct characteristics. Wooden pallets are the most common type, known for their affordability and availability. Plastic pallets offer advantages such as durability, resistance to moisture, and ease of cleaning, making them suitable for industries with stringent hygiene requirements. Metal pallets, although less common, provide exceptional strength and are often used for transporting heavy or hazardous goods. The choice of pallet type depends on factors such as the nature of the goods, industry regulations, and environmental considerations.
Notable Features
Effective palletization is defined by several key features that contribute to its efficacy. One of the most important features is standardization, which ensures compatibility between pallets and various transportation modes, such as trucks, ships, and aircraft. Standard pallet dimensions, such as the widely used 48x40 inch pallet in North America, facilitate efficient loading and unloading processes and enable interoperability within global supply chains. Durability is another critical feature, as pallets must withstand the rigors of handling, transportation, and storage without compromising the integrity of the goods. Adaptability is also essential, as palletization strategies must accommodate different types of products and packaging configurations. Additionally, the weight capacity of pallets is a vital consideration, as overloading can lead to structural failure and product damage. By understanding and leveraging these features, businesses can optimize their palletization processes to enhance efficiency, safety, and cost-effectiveness within their supply chains.
Strategic implementation
Planning and Execution
Integrating palletization into existing supply chain operations requires careful planning and execution to ensure alignment with overall business objectives and supply chain goals. A strategic approach begins with a comprehensive assessment of current operations to identify areas where palletization can enhance efficiency and reduce costs. This involves analyzing product types, packaging configurations, and transportation modes to determine the most suitable palletization strategies. Businesses should also consider the use of technology and automation to streamline palletization processes and improve accuracy. Once a plan is devised, execution involves implementing the chosen strategies, which may include training staff on proper pallet handling techniques and safety protocols. It is essential to monitor the performance of palletization processes continuously, using key performance indicators (KPIs) such as load efficiency, handling time, and damage rates. By regularly evaluating and refining palletization strategies, businesses can achieve optimal results and maintain a competitive edge in the market.
Best Practices
To optimize palletization processes and ensure their effectiveness, businesses should adhere to a set of best practices that encompass load planning, pallet configuration, and safety protocols. Load planning involves determining the optimal arrangement of goods on pallets to maximize space utilization and ensure stability during transit. This may include using specialized software to simulate different pallet configurations and identify the most efficient layout. Pallet configuration should take into account factors such as product dimensions, weight distribution, and stacking patterns to prevent overloading and reduce the risk of product damage. Safety protocols are paramount in palletization, as improper handling and stacking can lead to accidents and injuries. Training staff on safe pallet handling techniques, such as proper lifting and stacking methods, is crucial to maintaining a safe working environment. Additionally, businesses should prioritize sustainability by selecting eco-friendly pallet materials and exploring opportunities for pallet reuse and recycling. By implementing these best practices, businesses can enhance the efficiency, safety, and sustainability of their palletization processes.
Related:
Cashier-Less Store TechnologyClick here to read our expertly curated top picks!
Technological integration
Tools and Technologies
The integration of advanced technologies into palletization processes has revolutionized the way goods are handled, stored, and transported within supply chains. Automation is a key technological advancement that enhances palletization by reducing manual labor and improving accuracy. Automated palletizers and depalletizers, equipped with robotics and sensors, enable precise and efficient stacking and unstacking of goods on pallets. These systems can handle a wide range of product types and packaging configurations, making them versatile tools for businesses across industries. Radio-Frequency Identification (RFID) tagging is another technology that enhances palletization by enabling real-time tracking and monitoring of palletized goods throughout the supply chain. RFID tags attached to pallets provide valuable data on location, condition, and inventory levels, enhancing visibility and control. The Internet of Things (IoT) further complements palletization by facilitating seamless communication between pallets, machinery, and warehouse management systems (WMS). This integration allows for data-driven decision-making and optimization of palletization processes.
Impact of Digital Transformation
The digital transformation of supply chains has significantly influenced palletization practices, driving increased efficiency and data-driven decision-making. The adoption of digital technologies, such as artificial intelligence (AI) and machine learning, has enabled businesses to analyze vast amounts of data and gain insights into palletization processes. AI-powered algorithms can optimize pallet configurations, predict demand patterns, and identify opportunities for cost savings. Machine learning models can also enhance the accuracy of automated palletizers by learning from past performance and continuously improving stacking techniques. Digital transformation has also facilitated the development of advanced warehouse management systems (WMS) that integrate with palletization processes to streamline operations. These systems provide real-time visibility into inventory levels, order fulfillment, and transportation schedules, enabling businesses to make informed decisions and respond to changing market demands. As digital transformation continues to advance, the potential for emerging technologies to revolutionize palletization practices is vast, offering opportunities for increased efficiency, sustainability, and innovation.
Case studies and real-world applications
Successful implementations
Successful implementations
Example 1: A leading retailer, faced with the challenge of optimizing its distribution network to meet growing consumer demand, implemented an innovative palletization solution to improve efficiency. By leveraging automated palletizers and RFID technology, the retailer streamlined its loading and unloading processes, reducing handling time by 30%. This improvement not only enhanced operational efficiency but also allowed the retailer to fulfill orders more quickly and accurately, resulting in increased customer satisfaction and loyalty.
Example 2: A logistics company seeking to reduce costs and lead times turned to automated palletization as a solution. By integrating advanced robotics and sensors into its palletization processes, the company achieved a 40% reduction in labor costs and a 25% decrease in lead times. The automation allowed for precise and efficient handling of a wide range of product types, minimizing errors and enhancing the company's ability to meet tight delivery schedules.
Example 3: A manufacturing firm aiming to enhance product safety and reduce waste adopted palletization as a key strategy. By implementing standardized pallet dimensions and load planning software, the firm optimized its pallet configurations to ensure stability and minimize product damage. As a result, the firm reduced waste by 15% and improved product safety, leading to a stronger reputation for quality and reliability in the market.
Lessons learned
Lessons learned
Real-world applications of palletization offer valuable insights and lessons that can be leveraged to overcome common challenges and enhance efficiency within supply chains. One key lesson is the importance of aligning palletization strategies with overall business objectives and supply chain goals. By ensuring that palletization processes are integrated with broader operational strategies, businesses can achieve optimal results and maintain a competitive edge. Another lesson is the significance of continuous improvement and adaptation in maintaining effective palletization practices. As market demands and technological advancements evolve, businesses must remain agile and open to change to seize new opportunities and address emerging challenges. Additionally, the role of training and workforce development cannot be overlooked, as well-trained staff are essential to ensuring the safe and efficient execution of palletization processes. By embracing these lessons and prioritizing continuous improvement, businesses can enhance the effectiveness of their palletization strategies and drive success in the ever-changing landscape of supply chain management.
Related:
External Market FactorsClick here to read our expertly curated top picks!
Future trends
Emerging Developments
As the landscape of supply chain management continues to evolve, several emerging trends are set to shape the future of palletization. One key trend is the growing emphasis on sustainability and the circular economy. Businesses are increasingly prioritizing eco-friendly pallet materials and exploring opportunities for pallet reuse and recycling to reduce their environmental footprint. This shift aligns with consumer expectations for sustainable practices and regulatory requirements aimed at mitigating environmental impact. Another emerging development is the impact of global supply chain disruptions on palletization practices. The COVID-19 pandemic highlighted the vulnerabilities of global supply chains and underscored the importance of resilience and adaptability. As a result, businesses are reevaluating their palletization strategies to enhance supply chain agility and respond more effectively to disruptions.
Predictions and Projections
Expert predictions suggest that the evolution of palletization will be driven by technological advancements and changing market demands. The adoption of automation, AI, and machine learning is expected to continue, enabling businesses to optimize palletization processes and achieve greater efficiency. These technologies will facilitate data-driven decision-making and enhance the flexibility of supply chains, allowing businesses to respond to dynamic market conditions and consumer preferences. Additionally, environmental regulations and consumer expectations are likely to influence palletization practices, driving the adoption of sustainable materials and practices. The focus on sustainability is expected to extend beyond materials to encompass the entire lifecycle of pallets, from production to disposal. As businesses strive to meet these evolving demands, palletization will remain a critical component of supply chain operations, offering opportunities for innovation and competitive advantage.
Related:
Cashier-Less Store TechnologyClick here to read our expertly curated top picks!
Tips for do's and don'ts
Do's | Don’ts |
---|---|
Standardize pallet sizes and types to improve compatibility. | Don't neglect regular maintenance and inspection of pallets. |
Train staff on safe pallet handling and stacking techniques. | Avoid overloading pallets beyond their weight capacity. |
Utilize technology for tracking and managing pallet loads. | Don’t ignore the importance of a clear labeling system. |
Prioritize sustainability by choosing eco-friendly pallet materials. | Don’t disregard the impact of pallet quality on product safety. |
Continuously evaluate and enhance palletization processes. | Avoid complacency; stay updated on industry trends and innovations. |
Related:
Personal Budget ManagementClick here to read our expertly curated top picks!
Conclusion
Summing Up
In conclusion, palletization is a cornerstone of modern supply chain efficiency, driving operational effectiveness and cost savings across industries. Its historical development and evolution highlight the transformative impact of technological advancements and strategic innovation. By understanding the core concepts and strategic implementation of palletization, businesses can optimize their logistics operations and maintain a competitive edge in the market.
Final Thoughts
As the landscape of supply chain management continues to evolve, professionals and aspiring project managers must remain vigilant in adapting to advancements in palletization. By embracing emerging trends, leveraging technology, and prioritizing sustainability, businesses can enhance the efficiency and resilience of their supply chains. Continuous learning and improvement will be key to maintaining a competitive advantage and achieving success in the dynamic world of supply chain management.
Navigate supply chain management with Meegle. Sign up for free and see the difference!
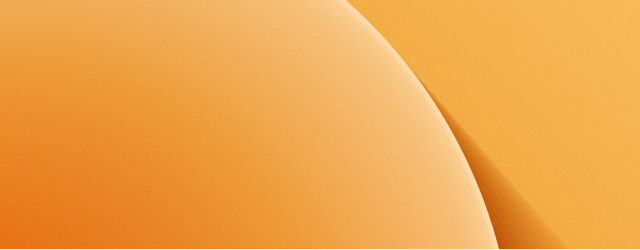
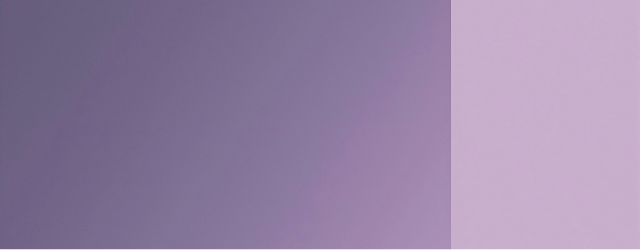
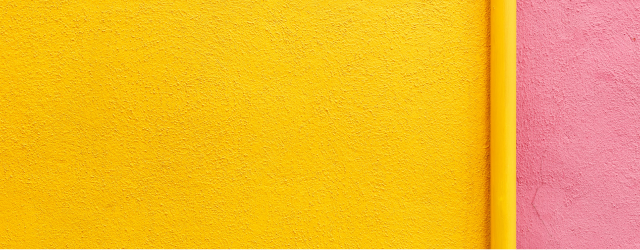
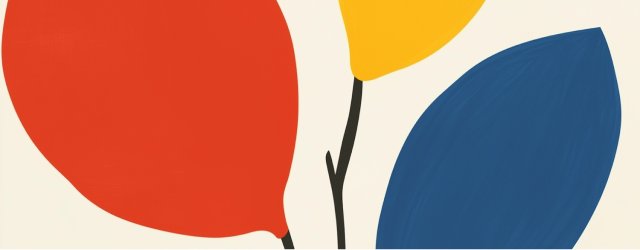
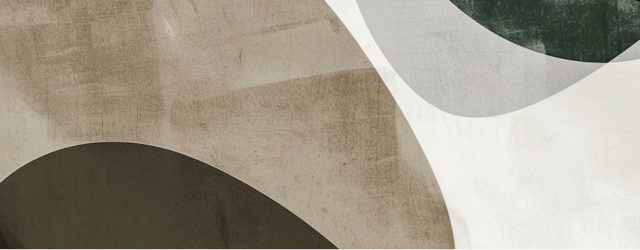
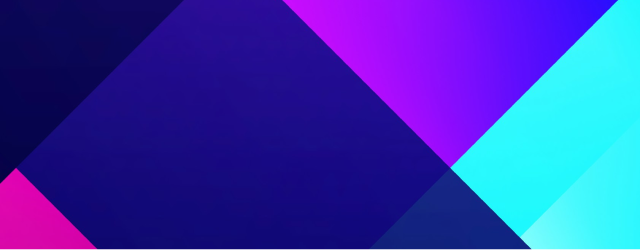
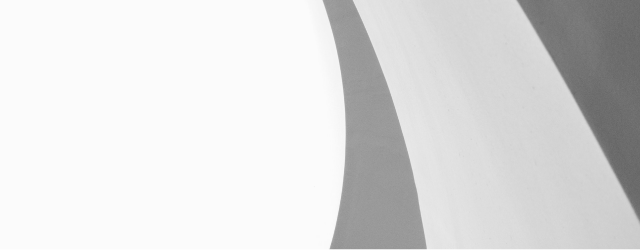
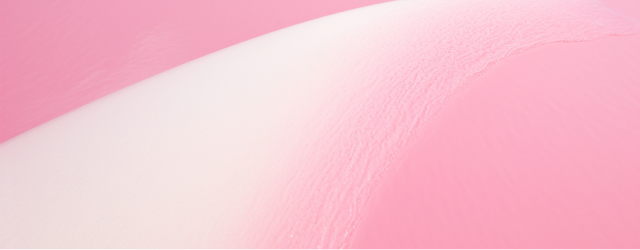