Energy Sector Operators
Discover how effective workflow management can transform efficiency and productivity for Energy Sector Operators, driving stronger business outcomes.
What is Workflow Management?
Workflow management in the context of the energy sector refers to the orchestrated and repeatable pattern of business activities specifically tailored to improve operational efficiency. It involves a comprehensive system of organizing, monitoring, and optimizing processes that encompass tasks, resources, and time management. In essence, workflow management is about creating a structured framework within which tasks are executed efficiently, ensuring that resources are allocated optimally, schedules are adhered to, and monitoring is continuous for any necessary adjustments. In the energy sector, this means managing everything from the daily operations of an oil refinery to the complex logistics of a wind farm. By applying workflow management principles, companies can streamline their operations, reduce waste, and enhance productivity. This systematic approach allows for the identification and elimination of inefficiencies, ultimately leading to improved performance and reduced costs.
Importance for Energy Sector Operators
The pivotal role of workflow management in the energy sector cannot be overstated. It directly impacts an operator’s ability to enhance productivity, ensure regulatory compliance, support agile decision-making, and foster innovation. By streamlining processes, operators can reduce operational costs and improve safety standards, which are paramount in an industry where the margin for error is minimal. For instance, energy companies can use workflow management to enhance their maintenance strategies, reducing downtime and extending the life of critical equipment. Moreover, efficient workflows enable better resource allocation, ensuring that human and capital resources are utilized where they are most needed, thus maximizing returns. In a sector characterized by rapid technological advancements and regulatory changes, workflow management provides the agility necessary to adapt quickly. By embedding flexibility into workflows, operators can swiftly respond to market fluctuations, regulatory updates, and technological innovations.
Turn Project Chaos Into a Visual and Structured Plan
Key components of effective workflow management
Process Mapping
Process mapping is a foundational practice in effective workflow management, serving as a visual representation of the sequence of actions or steps in a process. For energy sector operations, this involves detailing each step in production, from resource extraction to distribution, and identifying the roles responsible for each task. Through process mapping, operators can identify bottlenecks, redundancies, and inefficiencies that may be hindering productivity. Best practices for creating detailed process maps include using flowchart software tools that allow for easy adjustments and visualization. For example, a process map in an oil refinery might start with crude oil receipt and end with distribution, detailing every intermediate step like distillation, conversion, treatment, and storage. By laying out the process in a visual format, operators can more easily pinpoint areas where time, resources, or costs can be saved. Furthermore, process mapping aids in training new employees by providing a clear, visual understanding of operations, thus accelerating onboarding.
Task Automation
Automation of repetitive tasks is a game-changer in the energy sector, freeing up valuable human resources for more strategic activities. Automation can be applied to various facets of energy operations, from predictive maintenance to data entry. For instance, in predictive maintenance, sensors and software can predict when equipment will fail, allowing for proactive maintenance rather than reactive repairs. This not only reduces downtime but also extends equipment life and enhances safety. Similarly, automating data entry tasks can reduce errors and free up staff to focus on more critical decision-making processes. Automation also plays a crucial role in energy production, where it can optimize production schedules and monitor energy outputs in real-time, ensuring maximum efficiency. By implementing automated systems, energy companies can achieve significant cost savings and operational improvements. The key advantage of automation in workflow management is its ability to handle large volumes of data and tasks quickly and accurately, something that would be infeasible for human operators alone.
Click here to explore our expertly curated top project templates!
Planning and setting up workflows for energy sector operators
Initial Assessment
Before setting up workflows, conducting an initial assessment is crucial to understand the existing processes and identify opportunities for improvement. This involves evaluating both the strategic and operational levels of energy operations. Techniques such as SWOT analysis, which stands for Strengths, Weaknesses, Opportunities, and Threats, can be instrumental in providing a comprehensive view of the current operational landscape. Additionally, stakeholder interviews can provide insights into workflow inefficiencies and areas needing enhancement. For instance, interviewing plant managers and field workers could reveal bottlenecks or redundant steps that are not immediately obvious at the management level. By gathering input from various stakeholders, operators can ensure that the newly designed workflows align with the actual needs and challenges faced on the ground. This initial assessment sets the stage for informed decision-making, ensuring that subsequent workflow developments are targeted and effective.
Designing Custom Workflows
Designing custom workflows involves creating processes that specifically address the unique challenges and requirements of the energy sector, such as regulatory compliance and environmental impact considerations. Custom workflows must incorporate flexibility and scalability to adapt to changing regulations and market demands. For example, a custom workflow in a solar energy company might include steps for panel maintenance scheduling based on weather patterns and energy production forecasts. This ensures that resources are allocated efficiently and that maintenance activities do not interfere with peak production times. It is also essential to embed compliance checks within the workflows to ensure all operations meet industry standards and regulations. By tailoring workflows to meet specific needs, energy sector operators can achieve greater operational efficiency and effectiveness. Custom workflows should also be scalable to accommodate future growth and technological advancements, ensuring long-term sustainability and competitiveness.
Implementation strategies
Integration with Existing Systems
Integrating new workflows with existing IT systems is a crucial step in ensuring seamless operations. This involves establishing interoperability between different software platforms and ensuring data flows smoothly across the organization. Challenges such as API integration and data migration must be addressed to avoid disruptions. For instance, an energy company might need to integrate a new workflow management tool with its existing SCADA (Supervisory Control and Data Acquisition) system. This requires careful planning and execution to ensure that data from various sensors and controllers is accurately captured and managed. Solutions may include using middleware to facilitate communication between disparate systems or conducting phased rollouts to minimize risks. Successful integration ensures that all departments have access to the same information, enabling better coordination and decision-making across the organization.
Training and Adoption
Effective training programs are essential to ensure the smooth adoption of new workflows. This includes developing comprehensive training materials that cater to the varying needs of different user groups, from operators to executives. Training should focus on demonstrating the benefits of new workflows, addressing potential concerns, and ensuring competence in using new tools and systems. Change management strategies play a critical role in promoting buy-in from all levels of the organization. This involves clear communication of the reasons for change, the benefits, and how it aligns with the organization's goals. Engaging stakeholders early and involving them in the implementation process can also reduce resistance and foster a culture of continuous improvement. By investing in training and adoption, energy sector operators can ensure that their workflow management initiatives are successful and sustainable.
Click here to explore our expertly curated top project templates!
Monitoring and optimization
Performance Metrics
Identifying key performance metrics is vital for tracking the effectiveness of workflows in the energy sector. Metrics such as cycle time, error rates, and resource utilization provide insights into workflow efficiency and areas needing improvement. Tools and software designed for real-time monitoring and data analysis can significantly enhance the ability to track these metrics. For example, an energy company might use a dashboard to monitor the cycle time of energy production processes, allowing for immediate adjustments if targets are not being met. By analyzing error rates, operators can identify and address the root causes of inefficiencies, ensuring continuous improvement. Resource utilization metrics help ensure that resources are not under or over-utilized, optimizing operational efficiency. By focusing on these key metrics, energy sector operators can make informed decisions to enhance workflow performance.
Continual Improvement Processes
Ongoing evaluation and refinement of workflows are essential components of effective workflow management. Methods such as feedback loops and iterative testing allow for continuous assessment and improvement of processes. The Plan-Do-Check-Act (PDCA) cycle, a well-known management tool, can be particularly beneficial in the energy sector. This cycle involves planning a change, implementing it, checking the results, and acting on what has been learned to make further improvements. For example, a utility company might implement a new billing process, monitor its effectiveness, and make adjustments based on customer feedback and error rates. By embedding continual improvement processes into workflow management, energy sector operators can ensure that their operations remain efficient, competitive, and aligned with industry standards. This proactive approach fosters a culture of innovation and adaptability, essential for long-term success in the dynamic energy sector.
Common challenges and solutions
Addressing Resistance to Change
Resistance to change is a common challenge when implementing new workflows in any organization, including the energy sector. Strategies to overcome this resistance include effective communication, stakeholder engagement, and demonstrating clear benefits of the change. For example, operators can hold workshops and presentations to explain the benefits of new workflows, such as increased efficiency and reduced costs. By involving employees in the change process and addressing their concerns, operators can foster a sense of ownership and commitment. Demonstrating quick wins and tangible benefits can also help in gaining buy-in from skeptical stakeholders. By proactively managing resistance to change, energy sector operators can ensure smoother transitions and more successful implementations.
Solving Technical Hurdles
Technical challenges, such as legacy system compatibility and data security concerns, can pose significant hurdles during workflow implementation. Solutions to these challenges include conducting thorough system assessments, investing in compatible technologies, and ensuring robust data security measures. For instance, an energy company might need to upgrade its IT infrastructure to support new workflow management tools. This could involve investing in new hardware, software, or cloud solutions that offer better integration capabilities. Additionally, implementing strong data encryption and access control measures can address security concerns. By addressing these technical hurdles, energy sector operators can ensure that their workflow management initiatives are not only effective but also secure and sustainable.
Click here to explore our expertly curated top project templates!
Practical examples of workflow management in the energy sector
Example 1: refining operations in an oil & gas company
Example 1: refining operations in an oil & gas company
An oil and gas company faced challenges in streamlining its refining operations and improving safety compliance. By implementing workflow management strategies, the company was able to map out its refining processes, identify bottlenecks, and automate repetitive tasks. This led to a significant reduction in operational downtime and improved safety standards. For instance, predictive maintenance workflows were implemented, allowing the company to address potential equipment failures before they occurred, thereby reducing the risk of accidents and production halts. The integration of workflow management tools also enabled better resource allocation, ensuring that the right personnel and equipment were available when needed. As a result, the company achieved higher operational efficiency, reduced costs, and enhanced safety compliance.
Example 2: renewable energy plant optimization
Example 2: renewable energy plant optimization
A renewable energy plant sought to enhance its energy production efficiency and reduce downtime. By utilizing workflow automation, the plant was able to optimize its maintenance schedules and monitor energy outputs in real-time. Automated sensors and data analytics tools were employed to predict maintenance needs and adjust production schedules accordingly. This proactive approach allowed the plant to minimize downtime and maximize energy output. Additionally, the implementation of custom workflows enabled the plant to quickly adapt to changing weather conditions and energy demands. As a result, the plant achieved higher energy production efficiency and improved its overall operational performance.
Example 3: utility company customer service enhancement
Example 3: utility company customer service enhancement
A utility company aimed to improve its customer service workflow to enhance response times and customer satisfaction. By restructuring its customer service processes, the company was able to streamline communication channels and automate routine tasks. Workflow management tools were employed to route customer inquiries to the appropriate departments and track response times. This resulted in faster resolution of customer issues and improved overall satisfaction. The integration of customer feedback loops also allowed the company to continuously refine its customer service processes. By focusing on workflow management, the company was able to enhance its customer service capabilities and strengthen its reputation in the market.
Click here to explore our expertly curated top project templates!
Tips for effective workflow management
Do's | Don'ts |
---|---|
Engage stakeholders early in the process | Ignore feedback from end-users |
Continuously monitor and optimize workflows | Overlook scalability and future needs |
Invest in training and development | Rely solely on automated solutions |
Align workflows with regulatory requirements | Neglect the importance of data security |
Click here to explore our expertly curated top project templates!
Conclusion
Recap of Benefits
Implementing effective workflow management strategies in the energy sector offers numerous benefits, including increased productivity, cost savings, and improved compliance. By streamlining processes, operators can reduce operational costs and enhance safety standards, ensuring a competitive edge in the marketplace. Moreover, efficient workflows enable better resource allocation and agile decision-making, essential for adapting to regulatory changes and market demands.
Encouraging Ongoing Development
To keep pace with industry changes and demands, energy sector operators must embrace continuous improvement and innovation in workflow management. By fostering a culture of adaptability and leveraging the latest technologies, operators can ensure their workflows remain efficient, competitive, and aligned with industry standards. Embracing ongoing development not only enhances operational performance but also positions companies for long-term success in the dynamic energy sector.
Turn Project Chaos Into a Visual and Structured Plan
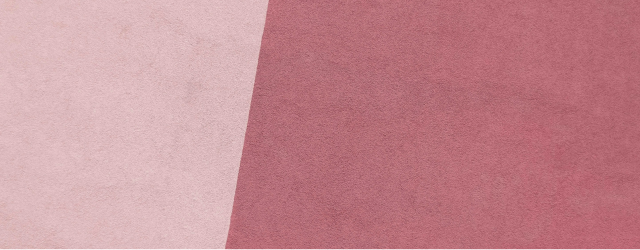
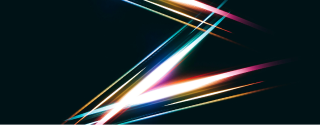
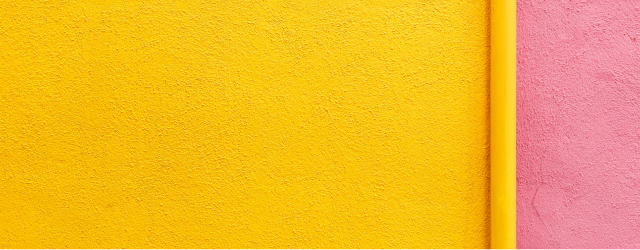
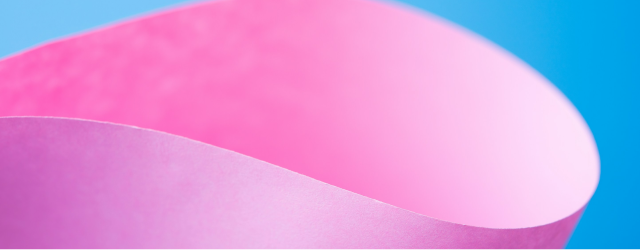
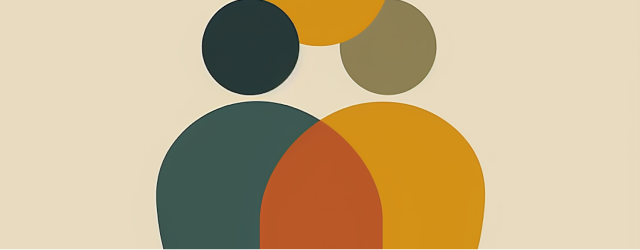
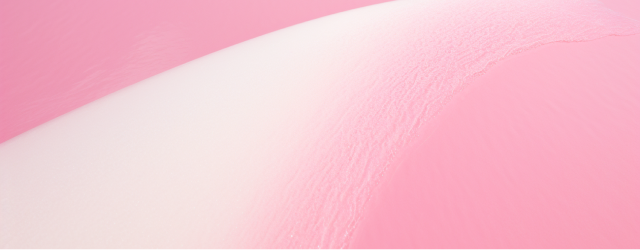
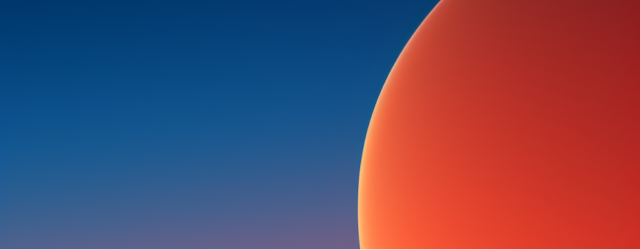
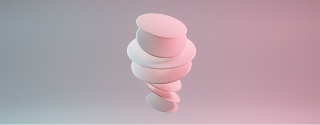