Production Line Workers
Discover how effective workflow management can transform efficiency and productivity for Production Line Workers, driving stronger business outcomes.
Understanding Workflow Management
Workflow management refers to the systematic organization of tasks and processes to improve efficiency and productivity. For production line workers, effective workflow management is crucial to minimize downtime and maximize output. At its core, workflow management involves designing processes that can handle tasks seamlessly with minimal interruptions. For instance, consider a production line responsible for assembling automotive parts. If the sequence of operations is not well-organized, it might lead to bottlenecks, with some workers idling while waiting for components from a previous stage. This inefficiency not only affects productivity but also can escalate costs and reduce employee morale. By understanding and implementing workflow management principles, production line workers can achieve a higher degree of coordination and quality in their outputs, leading to more consistent and reliable product delivery.
The Importance of Workflow Management in Manufacturing
For production line workers, workflow management is not just about efficiency; it's about creating an environment where every component of the production process is aligned and optimized. In manufacturing, where precision and timeliness are paramount, the importance of streamlined workflows cannot be overstated. Effective workflow management directly contributes to operational excellence by reducing errors, cutting costs, and improving production timelines. For example, a study by McKinsey & Company found that manufacturers who optimized their workflows saw a 30% improvement in production efficiency. By aligning tasks and processes, workers can focus on high-value activities, enhancing their skill set and job satisfaction. Moreover, companies with well-managed workflows tend to have a competitive advantage, as they can deliver quality products faster and more consistently. In a global market where speed and accuracy are differentiators, robust workflow management is key to maintaining a competitive edge.
Turn Project Chaos Into a Visual and Structured Plan
Key components of effective workflow management
Process Mapping Techniques
Process mapping is a visual representation of the workflow process. It helps identify bottlenecks and inefficiencies, allowing production line workers to streamline operations. To create an effective process map, begin by outlining every step in the production process, from raw material intake to finished product output. This can be done through flowcharts or diagrams that depict the sequence of tasks. For instance, in a food processing plant, a process map might illustrate the journey of ingredients from receiving to cooking, packaging, and shipping. By visualizing these steps, production line workers can pinpoint areas where delays occur or where resources are underutilized. Companies like Toyota have famously used process mapping as part of their lean manufacturing strategy, leading to significant efficiency gains. Implementing process mapping on the shop floor can empower workers to propose improvements and optimize their workflows for better productivity.
Automation of Repetitive Tasks
Automation plays a critical role in eliminating manual, repetitive tasks, freeing up time for more strategic activities. By incorporating technology such as robotic process automation (RPA), production line workers can focus on tasks that require human insight and creativity. For instance, in an electronics assembly line, robots can handle soldering tasks, which are repetitive and require precision, while humans focus on quality control and troubleshooting. Automation not only increases output but also improves consistency and quality. According to the International Federation of Robotics, industries that have adopted robotics have seen a productivity increase of up to 30%. Automation can also enhance safety by taking over hazardous tasks, reducing the risk of workplace injuries. However, successful adoption requires careful planning—identifying which tasks can be automated, selecting suitable technologies, and ensuring seamless integration with existing systems. With the right approach, automation can be a powerful tool in optimizing production line workflows.
Click here to explore our expertly curated top project templates!
Planning and setting up workflows for production line workers
Conducting Initial Workflow Assessments
To set up effective workflows, it's essential to start with a thorough assessment of current processes. Conducting a workflow assessment involves closely examining each stage of the production line to identify inefficiencies and areas for improvement. This can be done through direct observation, data analysis, and feedback from line workers. For example, in a textile manufacturing plant, an assessment might reveal that delays occur during the dyeing stage due to equipment downtime. By identifying this bottleneck, management can prioritize maintenance schedules or invest in more reliable machinery. Engaging production line workers in this assessment process is crucial, as they often have valuable insights into the day-to-day operations and challenges. This collaborative approach not only helps in identifying issues but also builds a sense of ownership and responsibility among workers, fostering a culture of continuous improvement.
Designing Custom Workflows for Manufacturing
Every production line has unique needs and challenges. Designing custom workflows involves tailoring processes to fit these specific requirements. This step is about creating bespoke solutions that address the distinct demands of production line work, enhancing both efficiency and worker satisfaction. For example, a pharmaceutical company might design a workflow that incorporates strict quality control checks at multiple stages to comply with regulatory standards. In contrast, a furniture manufacturer may focus on streamlining the assembly process to reduce lead times. Custom workflows should be flexible enough to adapt to changes in production volumes or product types. Incorporating worker feedback during the design phase ensures that the workflows are practical and feasible. By aligning processes with the specific goals and constraints of the production environment, companies can achieve higher efficiency and create a more engaging work atmosphere for their employees.
Implementation strategies for enhanced workflow management
Integrating New Workflows with Existing Systems
Successful implementation of new workflows requires seamless integration with existing manufacturing systems. This involves aligning new processes with current technologies and practices to ensure continuity in production. For example, if a new inventory management system is introduced, it must be compatible with the existing supply chain software to prevent disruptions. Integration might also involve upgrading or replacing outdated equipment to match the capabilities of new processes. A critical aspect of integration is ensuring that data flows smoothly across systems, enabling real-time tracking and decision-making. According to a report by Deloitte, manufacturers that successfully integrate new workflows with existing systems can increase their operational efficiency by up to 25%. To achieve this, it is essential to engage IT specialists and production line workers in the planning and implementation phases. By fostering collaboration across departments, companies can ensure that new workflows are effectively embedded, minimizing resistance and facilitating smoother transitions.
Training and Adoption Techniques
Adopting new workflows involves training production line workers and fostering a culture of continuous improvement. Training programs should be comprehensive, covering both the technical aspects of new workflows and the rationale behind the changes. For instance, if a new quality control protocol is implemented, training should include hands-on sessions on using the new equipment and explanations of how it enhances product quality. Engaging workers through workshops, simulations, and real-time feedback can boost confidence and competence. Moreover, fostering a culture that values continuous improvement encourages workers to embrace change and actively seek ways to enhance efficiency. This can be achieved by involving workers in decision-making processes and recognizing their contributions to workflow improvements. According to a study by the Society for Human Resource Management, companies that invest in employee training and development report a 29% increase in worker engagement. By implementing effective training and adoption techniques, production line workers can seamlessly transition to new workflows, driving operational success.
Click here to explore our expertly curated top project templates!
Monitoring and optimization of production workflows
Establishing Performance Metrics
To gauge the success of workflow changes, it's crucial to establish performance metrics. These indicators help track progress and identify areas for further improvement. Key metrics relevant to production line workers include cycle times, error rates, output quality, and worker engagement. For example, a reduction in cycle time can indicate a more efficient workflow, while a decrease in error rates may reflect improved quality control measures. Performance metrics should be specific, measurable, achievable, relevant, and time-bound (SMART) to provide clear insights into workflow effectiveness. Regularly reviewing these metrics allows production line managers to identify trends and make informed decisions about process adjustments. In a case study of a large-scale manufacturing plant, implementing a system of performance metrics led to a 20% increase in productivity within six months. By establishing and monitoring these metrics, production line workers can continuously optimize workflows and achieve sustainable improvements.
Implementing Continual Improvement Processes
Workflow management is not a one-time activity. Continual improvement processes ensure that workflows remain efficient and relevant. This involves regularly evaluating workflows, identifying opportunities for enhancement, and implementing incremental changes. Techniques such as Kaizen, which focuses on small, continuous improvements, can be highly effective in maintaining optimized workflows. For example, a company might conduct weekly review meetings to discuss recent workflow performance metrics and brainstorm potential improvements. Involving production line workers in these discussions encourages a proactive approach to problem-solving and innovation. According to a study by Harvard Business Review, organizations that embrace continual improvement practices report a 40% increase in employee satisfaction and a 30% improvement in operational efficiency. By fostering a culture of adaptability and continuous learning, production line workers can ensure that workflows evolve alongside technological advancements and market demands, maintaining high levels of productivity and quality.
Common challenges and solutions in workflow management
Overcoming Resistance to Change
Change can be challenging, especially in established production environments. Resistance to new workflows is a common hurdle that production line managers must address to ensure successful implementation. This resistance often stems from uncertainty, fear of job loss, or skepticism about the benefits of new processes. To overcome resistance, it's crucial to communicate the reasons for change clearly and transparently. Involving workers in the planning and decision-making processes can also help alleviate concerns. For example, a company planning to introduce automation might hold informational sessions where workers can ask questions and express their opinions. Demonstrating the positive impact of change, such as improved safety or reduced workload, can also encourage acceptance. According to a study by the Journal of Business Research, organizations that effectively manage resistance to change experience higher success rates in implementing new workflows. By addressing resistance proactively, production line managers can foster a supportive environment that embraces change and innovation.
Navigating Technical Hurdles
Implementing new workflows often involves technical challenges. These can range from integrating new software with existing systems to upgrading outdated equipment. Technical hurdles can disrupt production and hinder workflow optimization if not addressed promptly. To navigate these challenges, it's essential to conduct thorough technical assessments before implementing new workflows. This involves evaluating the compatibility of new technologies with existing infrastructure and identifying potential bottlenecks. Engaging IT specialists and production line workers in these assessments can provide valuable insights and ensure a smooth transition. Additionally, providing adequate training and support to workers can help them adapt to new technologies and overcome technical challenges. For example, a manufacturing plant implementing a new inventory management system might offer training sessions and on-site technical support to address any issues that arise. By proactively addressing technical hurdles, production line managers can minimize disruptions and ensure the successful integration of new workflows.
Click here to explore our expertly curated top project templates!
Examples of successful workflow management in manufacturing
Example 1: lean manufacturing implementation
Example 1: lean manufacturing implementation
Lean manufacturing principles focus on reducing waste and optimizing processes. A notable example of successful workflow management through lean manufacturing is Toyota's production system. By implementing lean practices such as just-in-time production and continuous improvement (Kaizen), Toyota significantly enhanced workflow efficiency. These practices allowed the company to reduce inventory costs, improve product quality, and shorten production lead times. As a result, Toyota became a global leader in the automotive industry, renowned for its efficient manufacturing processes and high-quality products. The success of Toyota's lean manufacturing approach demonstrates the potential benefits of optimizing workflows through waste reduction and process standardization.
Example 2: robotics integration in assembly lines
Example 2: robotics integration in assembly lines
Robotic integration can revolutionize assembly line workflows. An example of successful robotics integration is seen in the electronics manufacturing industry, where companies like Foxconn have incorporated robots to automate repetitive tasks. By using robots for tasks such as component placement and soldering, Foxconn improved production speed and reduced error rates. This automation allowed human workers to focus on quality control and complex problem-solving, enhancing overall productivity and product quality. The successful integration of robotics in Foxconn's assembly lines highlights the transformative impact of automation on workflow efficiency and quality assurance.
Example 3: real-time data utilization for process improvement
Example 3: real-time data utilization for process improvement
Utilizing real-time data can lead to better decision-making and process improvements. A case study in the pharmaceutical industry demonstrates the successful use of data analytics to optimize workflows. By implementing a real-time data monitoring system, the company was able to track production metrics such as cycle times, error rates, and equipment performance. This data provided valuable insights into workflow efficiency and identified areas for improvement. As a result, the company achieved a 25% reduction in production cycle times and a significant decrease in error rates. The use of real-time data analytics in pharmaceutical manufacturing showcases the benefits of leveraging data to drive workflow optimization and enhance operational efficiency.
Click here to explore our expertly curated top project templates!
Do's and don'ts of workflow management for production line workers
Do's | Don'ts |
---|---|
Conduct thorough assessments of current workflows. | Ignore potential bottlenecks and inefficiencies. |
Engage workers in the design and implementation process. | Implement changes without considering worker feedback. |
Utilize technology and automation to streamline tasks. | Rely solely on manual processes where automation can be beneficial. |
Continuously monitor and optimize workflows. | Neglect ongoing evaluation and improvement of workflows. |
Train workers effectively for smooth transition to new workflows. | Overlook the importance of training and worker engagement. |
Click here to explore our expertly curated top project templates!
Conclusion
Recap of Workflow Management Benefits for Production Line Workers
In conclusion, effective workflow management is essential for production line workers aiming to enhance productivity and operational success. By optimizing workflows, workers can reduce errors, improve efficiency, and achieve higher job satisfaction. The implementation of strategic workflow management practices enables seamless task coordination, leading to better quality products and reduced production costs.
Encouraging Ongoing Development and Adaptation
As manufacturing continually evolves, so should workflow management practices. Production line workers are encouraged to embrace ongoing development and adaptability, ensuring that workflows remain efficient and aligned with business needs. By fostering a culture of continuous improvement and innovation, companies can maintain a competitive edge and drive sustained success in the manufacturing industry.
Turn Project Chaos Into a Visual and Structured Plan
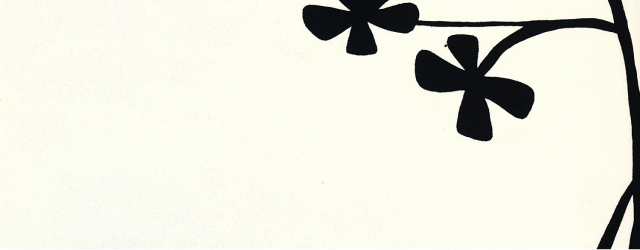
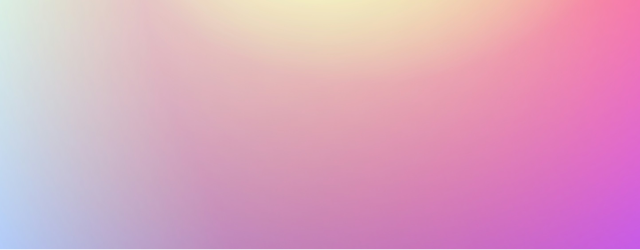
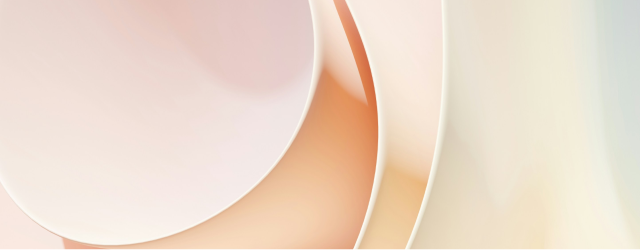
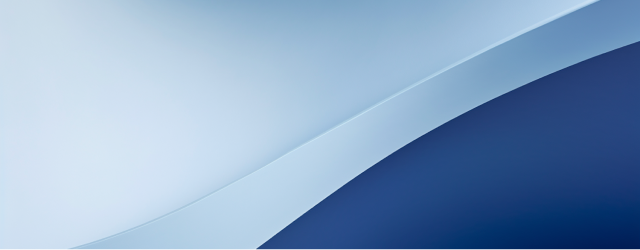
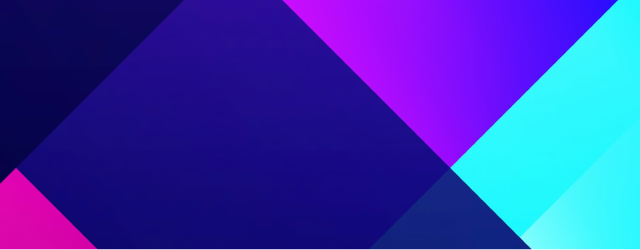
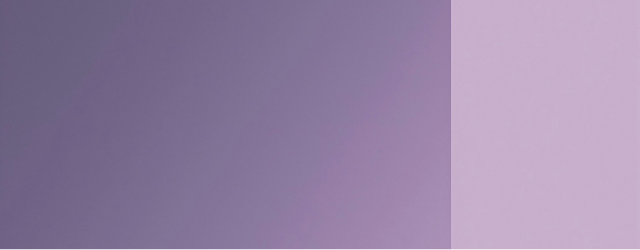
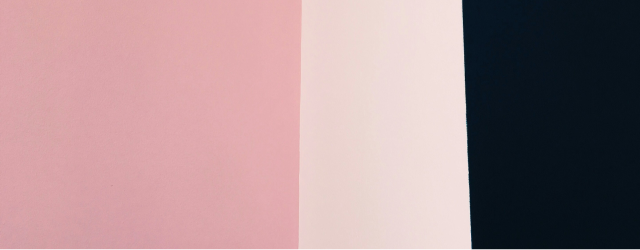
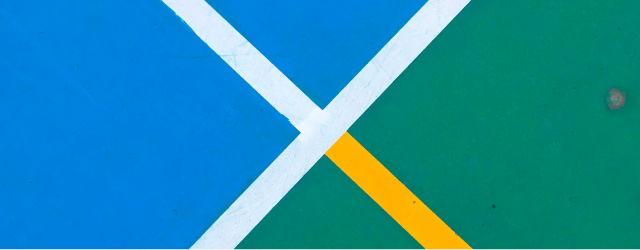