Process Analysis
Gain expert insights into Process Analysis, with practical how-to guides, best practices, real-world case studies, and actionable data to revolutionize your business processes.
Understanding the Fundamentals of Process Analysis
Process analysis is a pivotal component of business process management, focusing on the examination of various processes within an organization to improve efficiency and effectiveness. It involves a detailed study of workflows, identifying bottlenecks, redundancies, and areas of improvement. By dissecting each step of a process, businesses can pinpoint inefficiencies and implement strategic changes that enhance overall performance. This approach not only optimizes operational efficiency but also provides strategic benefits by aligning processes with long-term business objectives.
The role of process analysis in business cannot be overstated. It is an essential tool that aids in decision-making by providing a clear understanding of how processes function and their impact on organizational goals. For instance, a manufacturing firm might use process analysis to reduce production time, thereby lowering costs and increasing output. Similarly, a retail company might analyze customer service processes to enhance customer satisfaction and loyalty. These strategic benefits make process analysis an invaluable asset for businesses seeking to improve their operations.
Aligning Process Analysis with Organizational Goals
One of the significant advantages of process analysis is its ability to align with organizational goals. By thoroughly understanding existing processes, businesses can ensure that their operations are in harmony with their strategic objectives. This alignment is crucial for achieving long-term success and maintaining a competitive edge in the market. For example, a company aiming to enhance its sustainability efforts may use process analysis to identify ways to reduce waste and energy consumption, thereby contributing to its sustainability goals.
In conclusion, process analysis serves as the backbone of effective business process management. It provides organizations with the tools they need to evaluate, refine, and optimize their operations, ultimately driving business excellence. By incorporating process analysis into their strategic planning, businesses can achieve a higher level of operational efficiency, improve decision-making, and ensure their processes are aligned with their goals. This alignment is crucial for ensuring long-term success and maintaining a competitive edge in today's dynamic business landscape.
Experience the next level of project management today!
Defining process analysis
A Comprehensive Overview
Process analysis is a systematic approach to studying and improving business processes. It involves breaking down complex workflows into smaller, manageable components to understand how they function and identify areas for improvement. The primary goal of process analysis is to enhance operational efficiency by streamlining processes, reducing costs, and increasing productivity. To achieve this, organizations must consider several key elements and components that constitute effective process analysis.
Key elements of process analysis include process mapping, data collection, analysis, and evaluation. Process mapping involves visually representing the workflow to understand each step and its relationship with other processes. Data collection involves gathering relevant information about the process, such as time, cost, and resources required. Analysis and evaluation involve examining the data to identify bottlenecks, redundancies, and inefficiencies that hinder performance. By addressing these issues, businesses can implement changes that lead to improved efficiency and effectiveness.
Distinctive Features of Process Analysis
Process analysis differs from other process improvement frameworks in several ways. While methods like Six Sigma and Lean focus on eliminating defects and reducing waste, process analysis is more comprehensive, examining the entire workflow and its impact on organizational goals. It provides a holistic view of business operations, allowing organizations to make informed decisions that align with their strategic objectives. Furthermore, process analysis is an ongoing process, emphasizing continuous improvement rather than one-time fixes.
The impact of process analysis on business process management is profound. It enables organizations to identify inefficiencies, streamline workflows, and optimize performance. By focusing on continuous improvement, process analysis helps businesses adapt to changing market conditions and maintain a competitive edge. Additionally, it fosters a culture of innovation and collaboration, encouraging employees to contribute ideas for process improvement. This collaborative approach ensures that organizations remain agile and responsive to new challenges and opportunities.
In summary, process analysis is a powerful tool that enables organizations to optimize their operations and achieve business excellence. By understanding the key elements and components of process analysis, businesses can implement effective strategies that enhance efficiency, reduce costs, and improve overall performance. This comprehensive approach to process improvement ensures that organizations remain competitive and aligned with their strategic objectives, ultimately driving long-term success.
Unlock exclusive insights and elevate your strategies—click here to read our expertly curated top picks!
Evolution of process analysis
Historical Context and Developments
The concept of process analysis has undergone significant evolution over the years, shaped by technological advancements and changing business needs. Historically, process analysis can be traced back to the early industrial era when organizations sought to optimize production processes to increase efficiency and reduce costs. Pioneers like Frederick Taylor and Henry Ford played a crucial role in developing early methods of process analysis, emphasizing standardization and efficiency in manufacturing processes.
As the business landscape evolved, so did the principles of process analysis. In the mid-20th century, the rise of quality management frameworks like Total Quality Management (TQM) and Six Sigma introduced new methodologies that emphasized continuous improvement and defect reduction. These frameworks provided organizations with structured approaches to analyze and improve processes, laying the groundwork for modern process analysis techniques.
Technological Advancements and Their Impact
The advent of technology in the late 20th and early 21st centuries has significantly influenced the evolution of process analysis. The introduction of digital tools and software solutions has revolutionized the way organizations approach process analysis. Today, businesses can leverage advanced analytics, artificial intelligence, and machine learning to gain deeper insights into their processes and make data-driven decisions.
For example, process mining tools allow organizations to visualize and analyze complex workflows, identifying bottlenecks and inefficiencies with unprecedented accuracy. Similarly, AI-powered analytics enable businesses to predict process outcomes and optimize performance proactively. These technological advancements have made process analysis more accessible, efficient, and effective, empowering organizations to achieve significant improvements in their operations.
Adapting to Changing Business Needs
As technology continues to advance, process analysis will continue to evolve to meet the changing needs of businesses. Organizations must adapt their process analysis methodologies to leverage new tools and techniques effectively. This adaptability is crucial for staying competitive in a rapidly changing market and ensuring that processes remain aligned with organizational goals.
In conclusion, the evolution of process analysis reflects the ongoing quest for efficiency and excellence in business operations. From its early roots in industrial manufacturing to its modern-day applications in advanced analytics and AI, process analysis has continually adapted to meet the needs of organizations. By embracing new technologies and methodologies, businesses can harness the full potential of process analysis to drive operational efficiency, optimize performance, and achieve business excellence.
How-to guide: implementing process analysis
Step 1: Identifying and Mapping Current Processes
The first step in implementing process analysis is to identify and map existing processes within the organization. This involves documenting each step of the workflow to create a visual representation of the process. Process mapping tools like flowcharts and diagrams are invaluable in this stage, providing a clear overview of how processes function and their interdependencies.
To begin, gather input from key stakeholders and process owners to ensure all relevant information is captured. This collaborative approach ensures that the process map accurately reflects the current state of operations. Once the processes are mapped, review them to identify any gaps, redundancies, or inefficiencies that may hinder performance.
Step 2: Analyzing Process Efficiency and Effectiveness
After mapping the processes, the next step is to analyze their efficiency and effectiveness. This involves examining data related to each process, such as time, cost, and resource utilization. Use data analytics tools to identify patterns and trends that indicate areas of improvement. For example, if a particular process consistently takes longer than expected, investigate the root cause and potential solutions.
During this analysis, consider not only quantitative data but also qualitative feedback from employees and customers. This holistic approach provides a comprehensive understanding of the process's strengths and weaknesses, enabling organizations to make informed decisions about improvements.
Step 3: Designing and Implementing Improvements
Based on the analysis results, design and implement improvements to optimize the processes. This may involve redesigning workflows, reallocating resources, or introducing new technologies to enhance efficiency. Prioritize changes that align with organizational goals and have the greatest impact on performance.
When implementing improvements, involve key stakeholders to ensure buy-in and support for the changes. Communicate the benefits of the improvements and provide training to employees as needed. This collaborative approach fosters a culture of continuous improvement and encourages employees to contribute ideas for further optimization.
Step 4: Continuous Monitoring and Optimization
Process analysis is not a one-time activity but an ongoing practice. Continuously monitor processes to ensure they remain efficient and aligned with organizational objectives. Use key performance indicators (KPIs) to measure success and track progress over time. Regularly review and update process maps to reflect any changes and improvements.
Additionally, embrace a culture of continuous learning and adaptation. Encourage employees to provide feedback and suggest improvements, fostering a collaborative environment that supports ongoing optimization. By maintaining a focus on continuous improvement, organizations can ensure their processes remain agile and effective in a dynamic business landscape.
In summary, implementing process analysis involves a systematic approach to identifying, analyzing, and optimizing business processes. By following these steps, organizations can achieve significant improvements in efficiency, effectiveness, and alignment with strategic objectives. This comprehensive approach to process analysis empowers businesses to drive operational excellence and maintain a competitive edge.
Unlock exclusive insights and elevate your strategies—click here to read our expertly curated top picks!
Best practices in process analysis
Maximizing the Effectiveness of Process Analysis
To maximize the effectiveness of process analysis, organizations must adopt best practices that enhance their ability to identify inefficiencies and optimize processes. These practices involve a combination of strategic planning, stakeholder involvement, and continuous improvement. By embracing these practices, businesses can achieve remarkable improvements in their operations and drive long-term success.
One of the most critical best practices is involving key stakeholders in the process analysis journey. This includes employees, process owners, and managers who have firsthand knowledge of the processes being analyzed. By engaging these stakeholders, organizations can gather valuable insights and feedback that contribute to a comprehensive understanding of the process. Additionally, stakeholder involvement fosters a sense of ownership and commitment to process improvements, ensuring successful implementation.
Avoiding Common Pitfalls and Optimizing Performance
While process analysis offers numerous benefits, organizations must be cautious of common pitfalls that can hinder their efforts. One such pitfall is relying solely on assumptions rather than data-driven insights. To avoid this, organizations should leverage data analytics tools to gather accurate information about their processes. This data-driven approach ensures that decisions are based on evidence rather than speculation, leading to more effective process improvements.
Another common pitfall is failing to adapt to changes in the business environment. Organizations must remain agile and responsive to new challenges and opportunities. This requires a culture of continuous improvement, where employees are encouraged to provide feedback and suggest innovations. By fostering a culture of adaptability, businesses can ensure their processes remain relevant and effective in a dynamic market.
The Role of Continuous Improvement in Process Analysis
Continuous improvement is a cornerstone of effective process analysis. It involves regularly reviewing and updating processes to ensure they remain efficient and aligned with organizational goals. This ongoing practice requires a commitment to learning, innovation, and collaboration. Organizations should establish mechanisms for capturing and implementing employee suggestions for process improvements. This collaborative approach empowers employees and encourages them to contribute to the organization's success.
In conclusion, embracing best practices in process analysis is essential for maximizing its effectiveness and achieving business excellence. By involving stakeholders, avoiding common pitfalls, and fostering a culture of continuous improvement, organizations can optimize their processes and drive long-term success. These practices ensure that process analysis remains a powerful tool for enhancing operational efficiency, aligning with strategic objectives, and maintaining a competitive edge in the business landscape.
Real-world case studies
Process Analysis in a Manufacturing Firm
A manufacturing firm faced challenges with production delays and increased costs, impacting its ability to meet customer demands. By implementing process analysis, the firm identified bottlenecks in its production line and areas where resources were underutilized. Through process mapping and data analysis, the company redesigned its workflows, reallocating resources to optimize production efficiency. As a result, the firm reduced production time by 25% and achieved significant cost savings, enhancing its ability to compete in the market.
Streamlining Operations in a Retail Environment
A retail company sought to improve customer satisfaction by streamlining its inventory management and checkout processes. Through process analysis, the company identified inefficiencies in its supply chain and checkout procedures, leading to long wait times and stockouts. By implementing data-driven improvements, such as automated inventory tracking and optimized checkout workflows, the company reduced customer wait times by 30% and increased sales by 15%. These improvements not only enhanced customer satisfaction but also boosted the company's profitability.
Enhancing Service Delivery in a Healthcare Institution
A healthcare institution aimed to improve patient care by optimizing its service delivery processes. Through process analysis, the institution identified areas where patient care was delayed due to inefficient workflows and resource allocation. By redesigning processes and implementing digital solutions for patient scheduling and records management, the institution reduced patient wait times and improved overall service quality. As a result, patient satisfaction scores increased by 20%, and the institution's reputation for quality care improved significantly.
Unlock exclusive insights and elevate your strategies—click here to read our expertly curated top picks!
Quantitative data and analysis
Supporting Benefits with Quantitative Data
Quantitative data plays a crucial role in demonstrating the benefits of process analysis and its impact on business operations. By analyzing numerical data, organizations can gain valuable insights into their processes and measure the success of their improvement efforts. This data-driven approach provides concrete evidence of the effectiveness of process analysis and helps organizations make informed decisions.
For example, a study by McKinsey & Company found that organizations that effectively leverage process analysis can achieve a 20-30% improvement in operational efficiency. This improvement translates to significant cost savings, increased productivity, and enhanced customer satisfaction. Additionally, organizations that embrace process analysis as part of their continuous improvement efforts often experience a 10-15% increase in revenue, as streamlined processes lead to faster delivery times and improved customer experiences.
Key Performance Indicators (KPIs) for Measuring Success
To measure the success of process analysis, organizations should establish key performance indicators (KPIs) that align with their strategic objectives. These KPIs provide a clear framework for evaluating process performance and identifying areas for further improvement. Common KPIs in process analysis include cycle time, cost per process, error rates, and customer satisfaction scores.
-
Cycle Time: Measures the time taken to complete a process from start to finish. A reduction in cycle time indicates improved efficiency.
-
Cost per Process: Evaluates the expenses associated with executing a process. Lower costs signify optimized resource utilization.
-
Error Rates: Tracks the frequency of errors or defects in a process. A decrease in error rates reflects improved accuracy and quality.
-
Customer Satisfaction Scores: Provides insights into customer experiences and perceptions of service quality. Higher scores indicate enhanced customer satisfaction.
By tracking these KPIs, organizations can assess the impact of process analysis on their operations and make data-driven decisions to optimize performance further.
In conclusion, quantitative data and KPIs are essential tools for measuring the success of process analysis. By leveraging this data, organizations can demonstrate the tangible benefits of process analysis and make informed decisions to drive continuous improvement. This data-driven approach ensures that process analysis remains a powerful tool for enhancing operational efficiency and achieving business excellence.
Future trends in process analysis
Anticipating Developments and Innovations
As the business landscape continues to evolve, new trends and innovations are shaping the future of process analysis. Organizations must stay informed about these developments to remain competitive and capitalize on emerging opportunities. One of the key trends in process analysis is the increasing integration of digital tools and technologies, enabling businesses to gain deeper insights into their processes and make data-driven decisions.
For example, the rise of process mining tools allows organizations to visualize and analyze complex workflows with unprecedented accuracy. These tools use data from enterprise systems to create detailed process maps, identifying bottlenecks and inefficiencies in real time. Additionally, the integration of artificial intelligence (AI) and machine learning (ML) in process analysis is revolutionizing the way organizations approach optimization. AI-powered analytics can predict process outcomes, recommend improvements, and automate routine tasks, enhancing efficiency and effectiveness.
The Impact of AI and Machine Learning
AI and ML are transforming the landscape of process analysis by providing organizations with powerful tools to optimize their operations. AI-driven analytics can process vast amounts of data quickly, identifying patterns and trends that may not be apparent through traditional analysis methods. This capability allows organizations to make proactive decisions and anticipate changes in the market, ensuring their processes remain agile and responsive.
Moreover, AI-powered predictive analytics enable businesses to forecast process outcomes and identify potential risks before they occur. This foresight allows organizations to implement preventive measures and mitigate disruptions, enhancing overall process resilience. As AI and ML technologies continue to evolve, their impact on process analysis will only grow, offering new opportunities for optimization and innovation.
Preparing for Future Trends
To prepare for future trends in process analysis, organizations must adopt a forward-thinking approach that embraces technology and innovation. This involves investing in digital tools and training employees to leverage new technologies effectively. Additionally, organizations should foster a culture of continuous learning and adaptation, encouraging employees to stay informed about emerging trends and contribute to process improvements.
In conclusion, the future of process analysis is shaped by technological advancements and the increasing integration of AI and ML. By staying informed about these trends and embracing new tools and methodologies, organizations can optimize their processes and achieve business excellence. This proactive approach ensures that businesses remain competitive and agile, ready to capitalize on emerging opportunities and navigate the challenges of a dynamic market.
Related:
Critical Path Method (CPM)Unlock exclusive insights and elevate your strategies—click here to read our expertly curated top picks!
Tips: do's and dont's in process analysis
Do's | Dont's |
---|---|
Engage stakeholders | Ignore feedback |
Use data-driven insights | Rely solely on assumptions |
Continuously monitor processes | Set and forget processes |
Adapt to changes | Resist new technologies |
Engaging Stakeholders
Engaging stakeholders is essential for successful process analysis. By involving employees, process owners, and managers, organizations can gather valuable insights and ensure buy-in for process improvements.
Using Data-Driven Insights
Relying on data-driven insights is crucial for effective decision-making in process analysis. This approach ensures that process improvements are based on evidence rather than assumptions.
Continuously Monitoring Processes
Continuous monitoring is vital for maintaining process efficiency and alignment with organizational goals. Regularly reviewing processes and KPIs ensures ongoing optimization and improvement.
Adapting to Changes
Adapting to changes and embracing new technologies are critical for staying competitive in a dynamic market. Organizations must foster a culture of innovation and readiness to capitalize on emerging opportunities.
Unlock exclusive insights and elevate your strategies—click here to read our expertly curated top picks!
Conclusion
Recap of Key Points and Encouragement
In this article, we have explored the significance of process analysis in optimizing business operations and achieving excellence. We discussed the fundamental concepts of process analysis, its evolution, implementation, and best practices that drive operational efficiency. By leveraging process analysis, organizations can identify inefficiencies, streamline workflows, and make data-driven decisions that align with their strategic objectives.
Final Thoughts on Process Analysis
Process analysis is a powerful tool that empowers businesses to enhance their operations and maintain a competitive edge. By embracing continuous improvement and adapting to technological advancements, organizations can optimize their processes and achieve long-term success. The insights and strategies presented in this article provide a comprehensive framework for mastering process analysis and driving operational excellence.
Encouragement for Adoption
We encourage businesses to adopt process analysis as part of their strategic planning and operational management. By doing so, organizations can achieve significant improvements in efficiency, cost savings, and customer satisfaction. This commitment to process excellence ensures that businesses remain agile and responsive to new challenges and opportunities in today's dynamic market.
Further reading and resources
Recommended Books and Articles
- "Business Process Management: Concepts, Languages, Architectures" by Mathias Weske
- "The Ultimate Guide to Business Process Management" by Theodore Panagacos
- "Lean Six Sigma For Dummies" by John Morgan and Martin Brenig-Jones
Websites and Tools
- APQC (American Productivity & Quality Center) - apqc.org
- BPM Institute - bpminstitute.org
- Process Street - process.st
Professional Courses and Certifications
- Certified Business Process Professional (CBPP) by ABPMP
- Six Sigma Certification by ASQ (American Society for Quality)
- Lean Six Sigma Green Belt by IASSC
These resources offer valuable insights and tools to deepen your understanding of process analysis and enhance your ability to drive business excellence. By exploring these materials, professionals can gain the knowledge and skills needed to master process analysis and achieve remarkable improvements in their organization's operations.
Experience the next level of project management today!
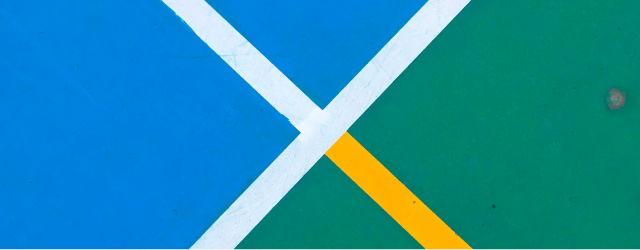
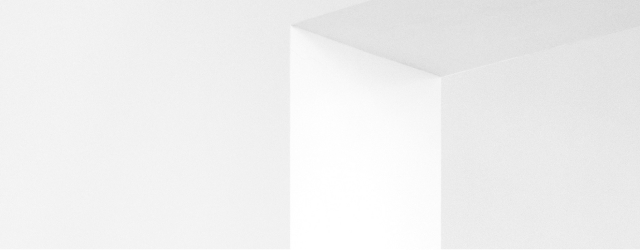
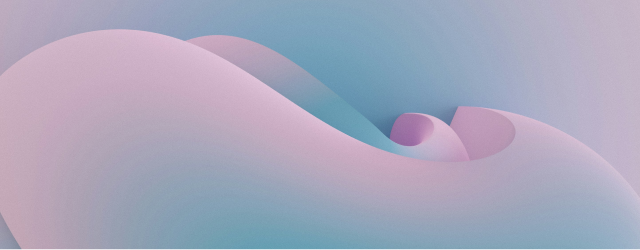
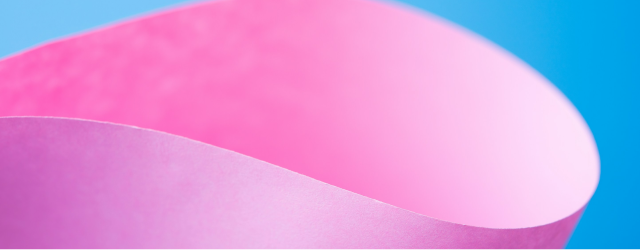
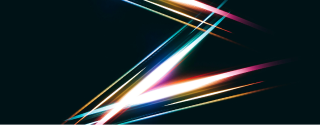
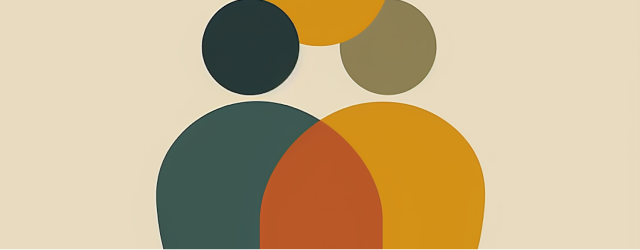
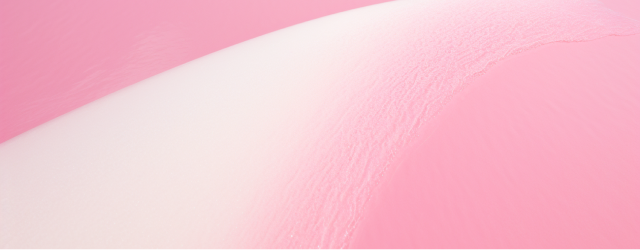
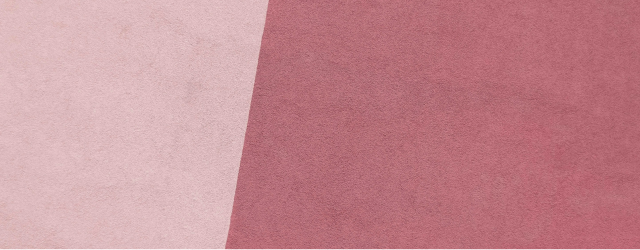