Total Quality Management (TQM)
Gain expert insights into Total Quality Management (TQM), with practical how-to guides, best practices, real-world case studies, and actionable data to revolutionize your business processes.
Total Quality Management (TQM) is a strategic approach in business process management that emphasizes quality as a pivotal factor in achieving operational excellence. In a world where consumer demands continually evolve, understanding and implementing TQM can be the differentiator between a thriving business and one that struggles to keep pace. By focusing on enhancing productivity and ensuring customer satisfaction, TQM provides a comprehensive framework for businesses to streamline their operations effectively.
The role of TQM extends beyond mere compliance or quality control; it is about embedding quality into the DNA of the organization. This involves every level of the organization, from top management to frontline employees, working in unison towards a common goal—excellence in quality. For industries ranging from manufacturing to services, TQM offers a structured approach to problem-solving, thereby reducing errors and increasing efficiency.
For today's businesses, the importance of TQM cannot be overstated. It not only aligns with the strategic goals of the organization but also ensures that the business remains competitive in a rapidly changing marketplace. By instilling a culture of continuous improvement, TQM helps businesses adapt to new challenges and seize opportunities for growth. As we explore the various facets of TQM in this article, it becomes evident that mastering this management approach is essential for sustained success.
Experience the next level of project management today!
Defining total quality management (tqm)
To truly understand Total Quality Management (TQM), one must delve into its core principles and components. At its essence, TQM is a management philosophy aimed at embedding awareness of quality in all organizational processes. The comprehensive definition of TQM encompasses a holistic approach to long-term success through customer satisfaction.
Core Principles of TQM
The core principles of TQM revolve around four main components:
-
Customer Focus: TQM recognizes that the customer's needs are paramount. It ensures that processes are designed and managed to meet customer expectations consistently.
-
Continuous Improvement: Central to TQM is the philosophy of never-ending improvement. This means that organizations must constantly evaluate and enhance their processes and systems to achieve better quality.
-
Employee Involvement: TQM views employees as vital resources in the quality improvement process. Their involvement, from the ground up, is crucial for generating innovative ideas and fostering a sense of ownership.
-
Process-Centric Approach: TQM emphasizes a focus on processes rather than results. By understanding and optimizing processes, organizations can drive efficiency and eliminate variations that lead to defects.
Impact on Business Processes
The impact of TQM on business processes is profound. By implementing TQM, businesses can streamline operations, reduce waste, and improve overall quality. For example, a manufacturing firm might adopt lean principles as part of TQM to minimize material waste and increase production efficiency. Similarly, in the service industry, TQM practices might involve enhancing customer service protocols to improve client satisfaction.
One notable case is Toyota's implementation of TQM, which led to the development of its renowned Toyota Production System (TPS). This approach not only revolutionized automotive manufacturing but also set the standard for quality and efficiency across various sectors. By focusing on continuous improvement and employee involvement, Toyota was able to reduce production costs and enhance product quality significantly.
In essence, TQM is not just a set of tools or techniques; it's a mindset that permeates every aspect of the organization. By embracing TQM, businesses can achieve lasting improvements in quality, productivity, and customer satisfaction.
Related:
Risk ManagementUnlock exclusive insights and elevate your strategies—click here to read our expertly curated top picks!
Evolution of total quality management (tqm)
The evolution of Total Quality Management (TQM) is a testament to its adaptability and relevance in various business contexts. Tracing its roots from early quality control methodologies to the sophisticated practices we see today, TQM has undergone significant transformations over the decades.
Historical Development
The concept of quality management dates back to the early 20th century when quality inspection and control were first formalized in manufacturing. However, it wasn't until the post-World War II era that TQM began to take shape. Influential figures such as W. Edwards Deming, Joseph Juran, and Philip Crosby played pivotal roles in developing and promoting TQM principles.
Deming, often referred to as the father of quality management, introduced the Plan-Do-Check-Act (PDCA) cycle, which became a cornerstone of TQM practices. Juran emphasized the importance of quality planning and the need for a strategic approach to quality management. Meanwhile, Crosby advocated for the concept of "zero defects" and highlighted the cost of poor quality.
Technological Advancements and Globalization
As technology advanced and globalization took hold, TQM practices evolved to meet new challenges. The rise of computer technology in the 1980s introduced automated quality control systems, allowing for more precise data collection and analysis. This technological shift enabled businesses to implement TQM on a larger scale and integrate it with other management methodologies, such as Six Sigma and Lean.
Globalization further influenced TQM by necessitating uniform quality standards across borders. Companies operating in multiple countries needed to ensure consistent quality to maintain brand reputation and customer trust. As a result, international quality standards, such as ISO 9001, gained prominence, providing a framework for organizations to implement TQM effectively.
The evolution of TQM reflects its ability to adapt to changing business environments and technological advancements. By embracing these changes, TQM remains a vital tool for organizations seeking to achieve excellence in quality and performance. As we continue to explore the intricacies of TQM, it becomes clear that its principles are timeless, providing a roadmap for success in any industry.
How-to guide: implementing total quality management (tqm)
Implementing Total Quality Management (TQM) in a business environment requires a structured approach to ensure its effectiveness. This how-to guide will walk you through the essential steps for a successful TQM implementation, along with the tools and technologies that can facilitate the process.
Establish Management Commitment
The first step in implementing TQM is securing management's commitment. Leadership plays a crucial role in setting the tone for quality initiatives. It's essential for top management to communicate the importance of TQM and actively participate in its implementation. This commitment should be visible and consistent, reinforcing the message that quality is a priority across the organization.
Conduct a Gap Analysis
Before implementing TQM, it's vital to conduct a gap analysis to identify areas that require improvement. This involves comparing the current state of business processes against the desired quality standards. By pinpointing gaps, organizations can develop targeted strategies to bridge them, ensuring a smooth transition to TQM practices.
Develop a TQM Implementation Plan
A comprehensive implementation plan outlines the specific steps and timelines for integrating TQM into the organization. This plan should include objectives, resource allocation, and key performance indicators (KPIs) to measure progress. Involving employees in the planning process is crucial, as their insights can help identify potential challenges and opportunities for improvement.
Train Employees and Foster a Culture of Quality
Training is a fundamental component of TQM implementation. Employees must understand the principles of TQM and how they apply to their roles. Providing ongoing training and development opportunities helps build the skills necessary for continuous improvement. Additionally, fostering a culture of quality involves encouraging open communication, feedback, and collaboration among team members.
Monitor and Measure Progress
Continuous monitoring and measurement are critical to the success of TQM. Organizations should establish metrics to evaluate the effectiveness of quality initiatives and track progress over time. Regular reviews and audits help identify areas for further improvement and ensure that TQM practices remain aligned with business objectives.
Tools and Technologies
Several tools and technologies can facilitate effective TQM implementation:
-
Six Sigma: A data-driven methodology that aims to reduce defects and improve process quality.
-
Kaizen: A continuous improvement approach that focuses on small, incremental changes to enhance efficiency and quality.
-
Lean Methodologies: Techniques that aim to eliminate waste and increase value for customers.
By following these steps and leveraging the right tools, organizations can successfully implement TQM and achieve lasting improvements in quality and performance. The journey to excellence requires commitment and perseverance, but the rewards of TQM are well worth the effort.
Unlock exclusive insights and elevate your strategies—click here to read our expertly curated top picks!
Best practices in total quality management (tqm)
Implementing Total Quality Management (TQM) effectively requires adherence to best practices that maximize its benefits and align it with organizational objectives. By understanding and integrating these strategies, businesses can enhance their TQM initiatives and drive continuous improvement.
Essential Best Practices
To maximize the effectiveness of TQM, organizations should focus on several essential best practices:
-
Leadership and Vision: Strong leadership is the cornerstone of successful TQM implementation. Leaders must articulate a clear vision for quality and inspire employees to work towards common goals. By demonstrating a commitment to quality, leaders can foster a culture of excellence.
-
Customer-Centric Approach: TQM places significant emphasis on understanding and meeting customer needs. Organizations should prioritize customer feedback and use it to inform quality improvement efforts. By aligning products and services with customer expectations, businesses can enhance satisfaction and loyalty.
-
Continuous Evaluation and Adaptation: TQM is an iterative process that requires ongoing evaluation and adaptation. Regularly assessing the effectiveness of quality initiatives and making necessary adjustments ensures that TQM remains relevant and impactful.
Integrating TQM into Organizational Culture
For TQM to thrive, it must be ingrained in the organizational culture. This involves creating an environment where quality is a shared responsibility and employees are empowered to contribute to improvement efforts. Strategies for integrating TQM into the culture include:
-
Open Communication: Encouraging open communication and feedback fosters a collaborative atmosphere. Employees should feel comfortable sharing ideas and concerns, knowing that their input is valued.
-
Recognition and Rewards: Recognizing and rewarding employees for their contributions to quality improvement reinforces the importance of TQM. Celebrating successes motivates employees to continue striving for excellence.
Avoiding Common Pitfalls
While implementing TQM, organizations may encounter challenges that hinder progress. By being aware of common pitfalls, businesses can take proactive measures to avoid them:
-
Lack of Management Support: Without strong support from management, TQM initiatives may falter. Ensuring consistent leadership involvement is crucial for maintaining momentum.
-
Resistance to Change: Employees may resist changes associated with TQM. Addressing concerns through training and communication can help ease the transition.
-
Neglecting Employee Involvement: Employees play a vital role in TQM. Failing to involve them in decision-making processes can lead to disengagement and reduced effectiveness.
By adhering to these best practices and strategies, organizations can successfully implement TQM and achieve significant improvements in quality and performance. The journey to excellence is continuous, but the benefits of TQM make it a worthwhile endeavor.
Real-world case studies
Examining real-world case studies of Total Quality Management (TQM) implementation provides valuable insights into its practical applications and benefits. These examples demonstrate how TQM can drive significant improvements in quality, efficiency, and customer satisfaction across various industries.
Example 1: Manufacturing Firm Achieves Quality Improvements and Cost Reductions
A leading manufacturing firm sought to enhance product quality and reduce production costs through TQM. By adopting Six Sigma methodologies, the company identified critical areas for improvement and implemented data-driven solutions. Through rigorous process analysis and employee involvement, the firm eliminated defects and streamlined production workflows. As a result, product quality improved by 25%, and production costs decreased by 15%. This success story highlights the transformative power of TQM in manufacturing environments.
Example 2: TQM Practices Enhance Customer Satisfaction in the Service Industry
A prominent service industry company implemented TQM to enhance customer satisfaction and loyalty. By focusing on customer feedback and continuous improvement, the organization revamped its service delivery processes. The introduction of a customer-centric approach, coupled with employee training, resulted in a 30% increase in customer satisfaction scores. This case study illustrates how TQM can drive positive outcomes in service-oriented businesses by prioritizing customer needs and fostering a culture of excellence.
Example 3: Integrating TQM with Lean Management in a Tech Company
A tech company sought to streamline operations and foster innovation by integrating TQM with lean management principles. By emphasizing waste reduction and process optimization, the company achieved remarkable efficiency gains. TQM practices were embedded into project management workflows, leading to a 20% reduction in project delivery times. Additionally, the company's commitment to continuous improvement spurred innovation, resulting in the development of new products and services. This example underscores the synergy between TQM and lean methodologies in driving operational excellence and innovation.
These real-world case studies demonstrate the versatility and effectiveness of TQM across diverse industries. By leveraging TQM principles and practices, organizations can achieve significant quality improvements, cost reductions, and customer satisfaction enhancements. As businesses continue to navigate dynamic markets, TQM remains a powerful tool for driving success and maintaining a competitive edge.
Related:
Work Breakdown Structure (WBS)Unlock exclusive insights and elevate your strategies—click here to read our expertly curated top picks!
Quantitative data and analysis
Quantitative data and analysis provide a compelling demonstration of the positive impact of Total Quality Management (TQM) on business performance. By examining key performance indicators (KPIs) and statistical evidence, organizations can gain valuable insights into the tangible benefits of TQM implementation.
Statistical Data Demonstrating TQM's Impact
Studies have consistently shown that TQM can lead to substantial improvements in various aspects of business performance. According to research published by the American Society for Quality (ASQ), organizations that implement TQM report an average 20% reduction in defect rates, leading to higher product quality and customer satisfaction. Furthermore, companies practicing TQM experience a 15% increase in operational efficiency, resulting in cost savings and improved profitability.
Role of TQM in Improving Key Performance Indicators
TQM plays a pivotal role in enhancing key performance indicators (KPIs) that are critical to business success. Some of the primary KPIs positively impacted by TQM include:
-
Defect Rates: By employing continuous improvement practices, TQM reduces defects in products and processes, leading to higher quality standards.
-
Customer Satisfaction Scores: With its emphasis on customer focus, TQM helps organizations better understand and meet customer needs, resulting in improved satisfaction scores.
-
Operational Efficiency: TQM streamlines processes, eliminates waste, and optimizes resource utilization, contributing to enhanced operational efficiency.
Visual Representations of TQM Benefits
Visual representations, such as charts and graphs, can effectively illustrate the measurable benefits of TQM implementation. For example, a line graph depicting the decline in defect rates over time after TQM adoption provides a clear visual of quality improvements. Additionally, a bar chart comparing customer satisfaction scores before and after TQM implementation highlights the positive impact on customer perceptions.
By leveraging quantitative data and analysis, organizations can make informed decisions about TQM implementation and measure its success. The statistical evidence underscores the value of TQM as a strategic tool for achieving business excellence and driving sustained growth.
Future trends in total quality management (tqm)
As businesses navigate an increasingly dynamic and technology-driven landscape, Total Quality Management (TQM) continues to evolve to meet emerging challenges and opportunities. Understanding future trends in TQM is essential for organizations seeking to stay ahead of the curve and maintain a competitive edge.
Anticipated Developments and Innovations
Several anticipated developments and innovations are shaping the future of TQM. One of the most significant trends is the rise of digital tools and artificial intelligence (AI)-driven quality management systems. These technologies enable more precise data collection and analysis, allowing businesses to make data-driven decisions and optimize processes in real-time.
Integrating Emerging Technologies with TQM
The integration of emerging technologies with TQM practices presents exciting possibilities for enhancing quality management. For instance, the use of machine learning algorithms can identify patterns and anomalies in production processes, leading to predictive maintenance and reduced downtime. Additionally, the Internet of Things (IoT) can provide real-time insights into supply chain operations, facilitating more efficient inventory management and quality control.
Future Challenges and Opportunities
While the future of TQM holds great promise, it also presents challenges that organizations must address. One such challenge is the need for continuous adaptation to rapidly changing market conditions and consumer expectations. To remain relevant, businesses must embrace a culture of innovation and agility, leveraging TQM as a framework for navigating uncertainty.
On the opportunity side, the globalization of markets presents new avenues for expansion and growth. By adopting international quality standards and best practices, organizations can ensure consistent quality across borders and tap into new customer segments.
As TQM continues to evolve, its principles remain as relevant as ever. By embracing future trends and integrating emerging technologies, businesses can achieve business excellence and maintain a competitive advantage in a rapidly changing global market.
Related:
Dependency MappingUnlock exclusive insights and elevate your strategies—click here to read our expertly curated top picks!
Do's and don'ts of total quality management (tqm)
Do's | Don'ts |
---|---|
Foster a culture of continuous improvement. | Ignore employee involvement and feedback. |
Align TQM with strategic business goals. | Implement TQM without proper planning. |
Invest in training and development. | Rely solely on traditional quality metrics. |
Utilize technology to enhance TQM processes. | Resist change and innovation. |
Regularly review and adapt TQM strategies. | Underestimate the role of leadership. |
Unlock exclusive insights and elevate your strategies—click here to read our expertly curated top picks!
Conclusion
In conclusion, Total Quality Management (TQM) is a powerful framework for achieving business excellence in today's competitive landscape. By emphasizing customer satisfaction, continuous improvement, and employee involvement, TQM provides a comprehensive approach to quality management that transcends traditional practices. Throughout this article, we have explored the core principles, evolution, and best practices of TQM, offering valuable insights and practical applications for professionals seeking to drive success within their organizations. As businesses continue to face evolving challenges and opportunities, the relevance and adaptability of TQM remain paramount. By embracing TQM and integrating emerging technologies, organizations can achieve sustained growth and maintain a competitive advantage in a rapidly changing global market.
Further reading and resources
For those seeking a deeper understanding of Total Quality Management (TQM), several recommended books and articles are available:
-
"Out of the Crisis" by W. Edwards Deming offers insights into the principles of quality management and its application in business.
-
"The Quality Toolbox" by Nancy R. Tague provides practical tools and techniques for implementing TQM effectively.
Online resources and websites, such as the American Society for Quality (ASQ), offer valuable insights and updates on TQM practices and innovations. Additionally, professional courses and certifications, such as Lean Six Sigma and ISO 9001, provide opportunities for individuals to advance their knowledge and skills in TQM.
Experience the next level of project management today!
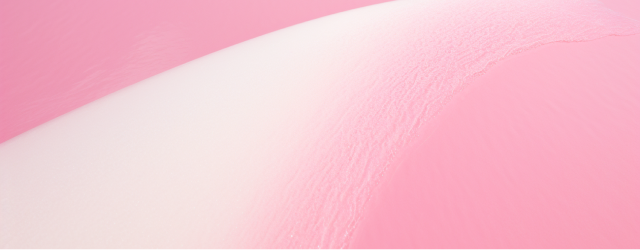
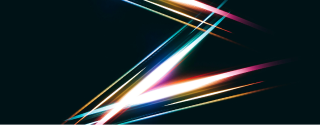
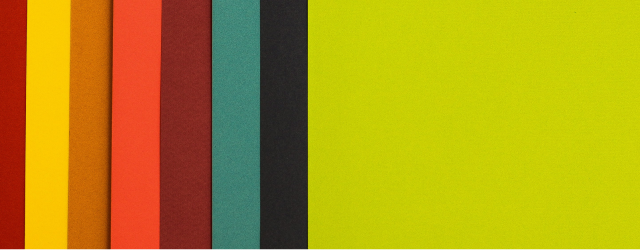
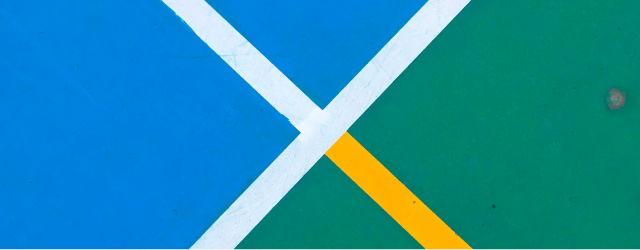
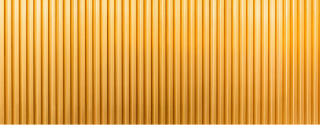
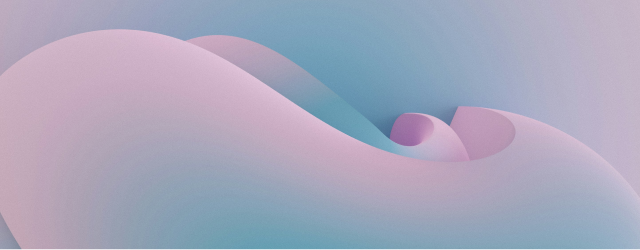
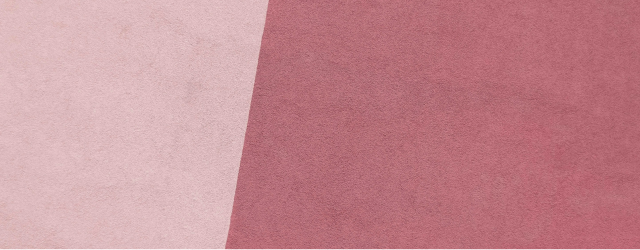
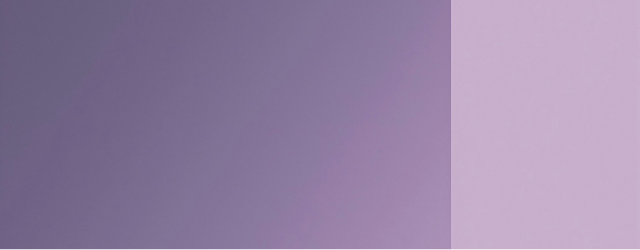