Process Flow Diagram
Gain expert insights into Process Flow Diagram, with practical how-to guides, best practices, real-world case studies, and actionable data to revolutionize your business processes.
In the buzzing hive of modern business, Process Flow Diagrams (PFDs) have emerged as strategic tools that can offer clear, concise visual representations of complex operational workflows. These diagrams break down the intricate web of tasks, responsibilities, and decision points, turning them into easily digestible, actionable insights. They have proven themselves to be invaluable resources for project managers and business strategists alike, acting as compasses that guide organizations towards optimal operational efficiency.
Beyond mere simplification, PFDs serve as mirrors reflecting the current state of business processes - revealing bottlenecks, inefficiencies, and potential avenues for improvement. With this understanding, businesses can streamline their processes, reducing waste, improving productivity, and ultimately, boosting profitability.
Experience the next level of project management today!
Understanding process flow diagrams
At its core, a Process Flow Diagram is a roadmap of a business process. It employs standardized symbols and arrows to represent different stages, the flow of tasks, and the sequence of operations. This helps in illustrating the start and end points, the direction of the process, the various tasks involved, and the decision points along the way.
In essence, PFDs are pivotal in business process management, as they provide a clear, visual understanding of operational workflows. They allow project managers to get a bird's-eye view of the process, identify areas of concern, and devise strategic interventions to enhance efficiency. By mapping out the process, businesses can ensure that all stakeholders understand their roles, responsibilities, and the sequence of actions they need to follow.
Tracing the evolution of process flow diagrams
Process Flow Diagrams are not a recent phenomenon. They have evolved over the years, with their roots tracing back to the Industrial Revolution, when manufacturers started using them to understand assembly line operations.
Over time, pioneers like Henry Gantt and Frank Gilbreth refined and expanded the use of these diagrams. The advent of computers and digital technologies further revolutionized PFDs. Today, we have advanced software tools that not only assist in creating detailed PFDs, but also enable real-time tracking, collaboration, and analysis - making PFDs more dynamic and effective than ever.
Related:
Risk ManagementUnlock exclusive insights and elevate your strategies—click here to read our expertly curated top picks!
Practical guide to implementing process flow diagrams
Implementing PFDs involves a series of organized steps. It starts with defining the process to be mapped and identifying the key stakeholders. The next step involves documenting the process, step-by-step, from start to finish. Once the process is mapped, it is then validated by all stakeholders to ensure accuracy.
There are several modern tools and technologies available today that aid in creating and managing PFDs. From simple tools like Microsoft Visio to more advanced software like Lucidchart and SmartDraw, these digital solutions make it easier to design, share, and update PFDs.
Do's and don'ts of process flow diagrams
When it comes to creating and using PFDs, there are certain best practices to follow and pitfalls to avoid. It's crucial to keep the diagram simple and clear, avoiding unnecessary details that may confuse the user. It's also important to involve all stakeholders in the process of creating the PFD to ensure accuracy and buy-in.
On the other hand, one common pitfall is to make the PFD too complex or cluttered. This can make it difficult to understand and use effectively. Also, failing to update the PFD as processes change is another mistake that can lead to miscommunication and errors.
Related:
Critical Path Method (CPM)Unlock exclusive insights and elevate your strategies—click here to read our expertly curated top picks!
Case studies: success with process flow diagrams
There are numerous real-life examples where businesses have used PFDs to drive operational efficiency and business success. Companies like Toyota and Amazon have used process flow diagrams to streamline their manufacturing and delivery processes, resulting in improved productivity and customer satisfaction.
By analyzing these success stories, businesses can gain insights into how to effectively implement PFDs in their own operations, learning from the strategies and techniques that have proven successful in the past.
Data-driven approach: quantifying the impact of process flow diagrams
Data plays a crucial role in substantiating the benefits of PFDs. Studies have shown that businesses that use PFDs report significant improvements in operational efficiency, with reductions in process time and costs.
By analyzing and visualizing this data, businesses can clearly see the impact of PFDs on their bottom line, making it easier to justify the time and resources spent on creating and maintaining these diagrams.
Related:
Kanban BoardUnlock exclusive insights and elevate your strategies—click here to read our expertly curated top picks!
Future of process flow diagrams
As business processes become more complex and digital transformation continues to sweep across industries, the role of PFDs is set to become even more crucial. Advancements in AI and machine learning are likely to make these diagrams more dynamic and predictive, enabling businesses to anticipate potential bottlenecks and inefficiencies before they occur.
Related:
Risk ManagementUnlock exclusive insights and elevate your strategies—click here to read our expertly curated top picks!
Conclusion
Process Flow Diagrams are powerful tools that can help businesses improve their operational efficiency and profitability. By providing a visual representation of the process, they allow businesses to identify and eliminate bottlenecks and inefficiencies, streamline their operations, and improve productivity.
Further reading and resources
For those interested in delving deeper into the world of PFDs, there are numerous resources available. Books like "Process Mapping and Management" by Sue Conger and "The Basics of Process Mapping" by Robert Damelio provide comprehensive insights into PFDs. Websites like Lucidchart, SmartDraw, and Microsoft Visio offer online tools for creating PFDs. Also, professional courses or certifications like Lean Six Sigma can help deepen understanding and practical application of PFDs.
Experience the next level of project management today!
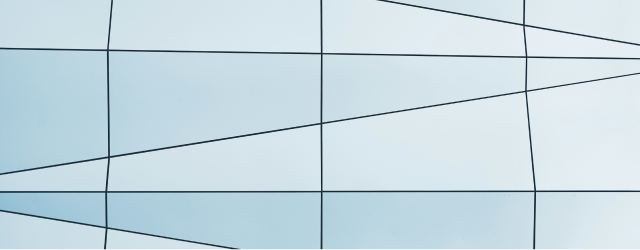
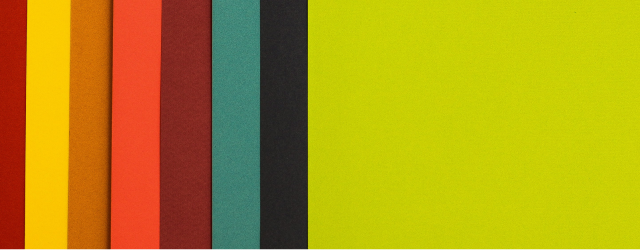
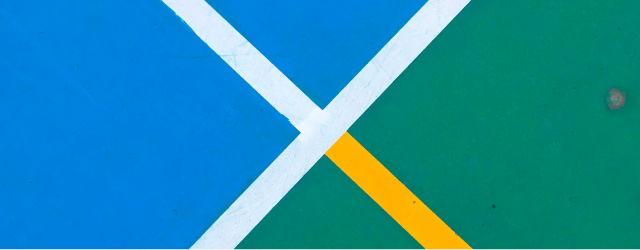
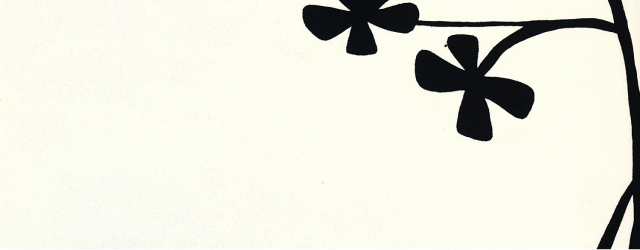
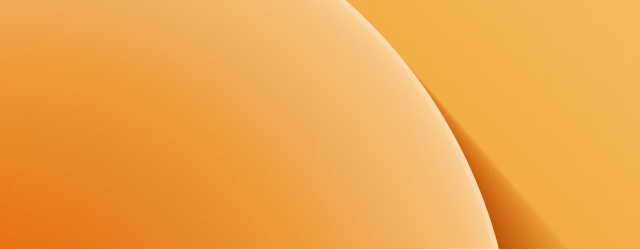
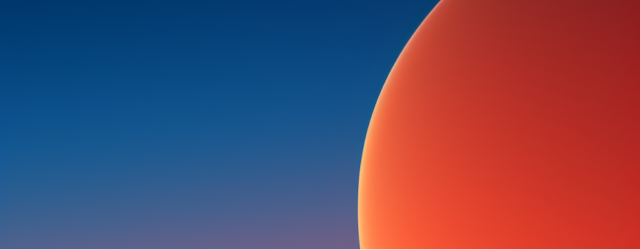
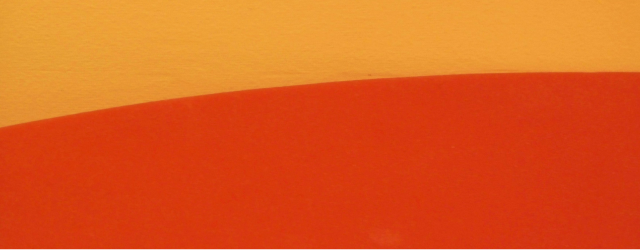