Process Improvement
Gain expert insights into Process Improvement, with practical how-to guides, best practices, real-world case studies, and actionable data to revolutionize your business processes.
Unpacking Process Improvement
Process Improvement refers to the proactive task of identifying, analyzing, and improving existing business processes within an organization to meet new standards of quality or efficiency. It involves making iterative changes to processes with the aim of reducing waste, increasing efficiency, and improving overall output quality. For instance, a manufacturing company might employ process improvement to reduce the production time of a product line while maintaining or enhancing its quality.
Process Improvement and Business Excellence
In the context of Business Excellence, Process Improvement serves as an essential lever. By optimizing operational workflows, companies can reduce costs, improve product quality, enhance customer satisfaction, and ultimately boost business performance. For example, a service-based company may streamline its customer service process to reduce response time, thereby improving client satisfaction and retaining more customers in the long run.
Experience the next level of project management today!
Journey of process improvement
Historical Development and Evolution
Process Improvement has its roots in the manufacturing industry with techniques like Lean Manufacturing and Six Sigma. These methodologies focus on reducing waste and enhancing quality, respectively. Over the years, these techniques have evolved and been adopted by various industries, leading to the development of comprehensive process improvement methodologies like Business Process Management (BPM) and Continuous Improvement (CI).
Pioneers and Shaping Forces
Notable figures like W. Edwards Deming and Joseph Juran significantly shaped Process Improvement. Deming's Plan-Do-Check-Act (PDCA) cycle and Juran's Quality Control Handbook have been instrumental in establishing the foundations of Process Improvement.
Unlock exclusive insights and elevate your strategies—click here to read our expertly curated top picks!
Best practices and tips for process improvement
Maximizing Process Improvement Effectiveness
Implementing Process Improvement effectively requires a systematic approach, clearly defined objectives, stakeholder engagement, and continuous monitoring and improvement. Using the right tools and technologies can also enhance the effectiveness of Process Improvement initiatives.
Avoiding Pitfalls and Enhancing Performance
Common challenges in Process Improvement include resistance to change, lack of clear objectives, and inadequate monitoring. Overcoming these requires effective change management, clear communication, and continuous performance tracking.
Unlock exclusive insights and elevate your strategies—click here to read our expertly curated top picks!
Process improvement in action: real-life examples
Example 1: xyz corporation
Example 1: xyz corporation
XYZ Corporation, a global manufacturing company, implemented Process Improvement to reduce machine downtime. By analyzing their machine maintenance process, they were able to identify inefficiencies and implement improvements, which significantly reduced machine downtime and increased production efficiency.
Example 2: abc enterprises
Example 2: abc enterprises
ABC Enterprises, a service-based company, employed Process Improvement to streamline their customer service process. By reengineering their process and using a CRM tool, they were able to reduce their customer response time by 50%.
Example 3: 123 industries
Example 3: 123 industries
123 Industries, a logistics company, used Process Improvement to optimize their supply chain process. By implementing a Supply Chain Management System (SCMS), they were able to reduce their delivery time and improve customer satisfaction significantly.
Analyzing process improvement: data and interpretation
Statistical Insights into Process Improvement
Numerous studies indicate the effectiveness of Process Improvement. According to McKinsey, organizations that have successfully implemented Process Improvement have seen up to a 30% increase in operational efficiency.
Visualizing Success
Graphical illustrations like process flow diagrams, control charts, and histograms can effectively depict the impact of Process Improvement on business processes.
Related:
Critical Path Method (CPM)Unlock exclusive insights and elevate your strategies—click here to read our expertly curated top picks!
Future of process improvement: trends and predictions
Innovations and Developments on the Horizon
Future trends in Process Improvement include the integration of AI and machine learning, predictive analytics, and real-time process monitoring.
Preparing for the Future
To adapt to these advancements, businesses should invest in upskilling their workforce, adopting the latest technologies, and fostering a culture of continuous improvement.
Related:
Quality AssuranceUnlock exclusive insights and elevate your strategies—click here to read our expertly curated top picks!
Conclusion
Process Improvement is not a one-time task but a continuous journey. It plays a vital role in achieving business excellence by optimizing operational efficiency, reducing costs, and improving customer satisfaction. As the business landscape evolves, businesses must continually update and improve their processes to stay competitive.
Further reading and resources
Recommended Readings
For those who want to delve deeper into Process Improvement, books like "The Lean Startup" by Eric Ries, "Lean Thinking" by James P. Womack and Daniel T. Jones, and "The Toyota Way" by Jeffrey K. Liker are great resources.
Professional Development Opportunities
Several professional development courses and certifications, like Lean Six Sigma, Certified Business Process Professional (CBPP), and Business Process Management Professional (BPMP), can help enhance skills in Process Improvement.
Experience the next level of project management today!
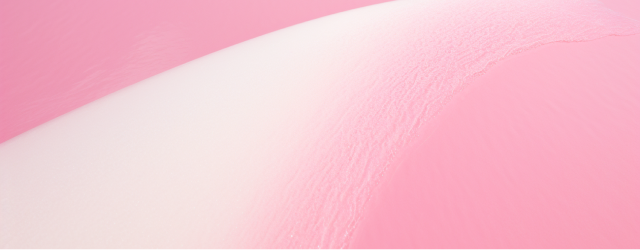
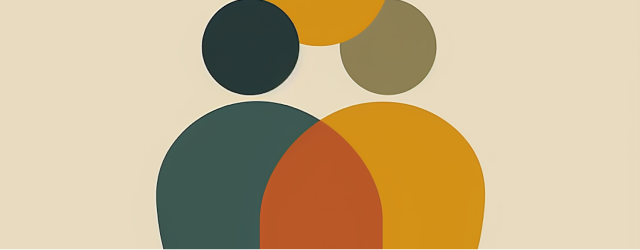
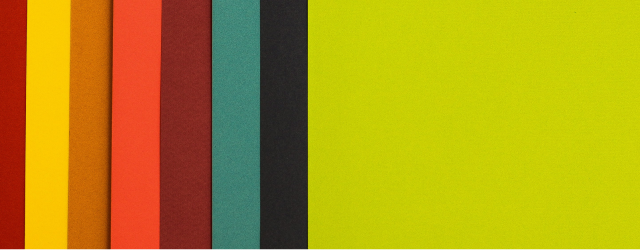
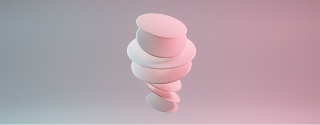
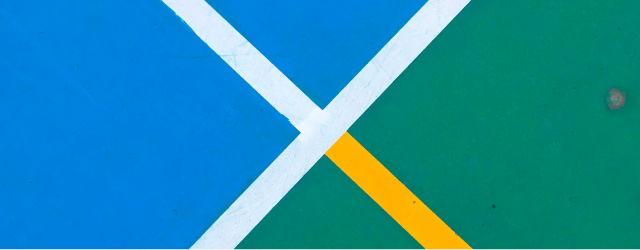
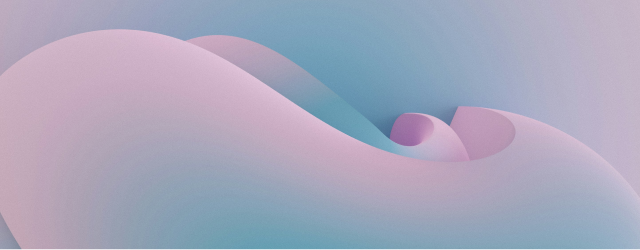
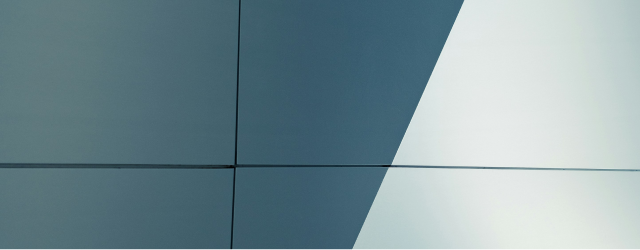
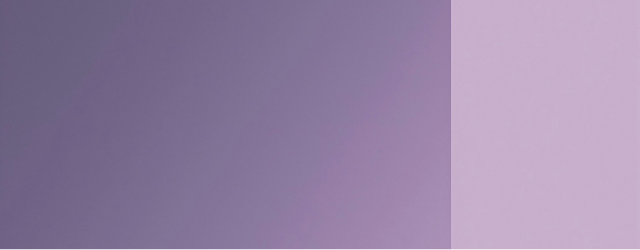