Process Monitoring
Gain expert insights into Process Monitoring, with practical how-to guides, best practices, real-world case studies, and actionable data to revolutionize your business processes.
Process monitoring, in its most fundamental form, refers to the act of observing, tracking, and analyzing the performance of business operations. While it may seem like a simple concept, process monitoring holds the potential to transform businesses by offering insights that drive improved performance, productivity, and profitability.
As businesses grapple with increasing market volatility and customer expectations, the strategic role of process monitoring cannot be overstated. The real-time visibility it provides into processes helps in identifying bottlenecks, measuring performance against KPIs, and making data-driven decisions. This guide serves as a roadmap to help businesses navigate the intricacies of process monitoring, paving the path to operational excellence and strategic advantage.
Experience the next level of project management today!
Demystifying process monitoring
While process monitoring is a broad concept, it primarily encompasses the systematic collection and analysis of process-related data. This data can range from metrics related to process efficiency, quality, and compliance, to more complex indicators like customer satisfaction and revenue generation.
Process monitoring plays a pivotal role in business process management (BPM), offering a control system that ensures processes are performing as expected. It empowers businesses to stay agile, adapt to changes swiftly, and capitalize on opportunities. By harnessing the power of process monitoring, organizations can gain a competitive edge, ensuring streamlined operations, reduced waste, and enhanced customer experience.
Related:
Earned Value Analysis (EVA)Unlock exclusive insights and elevate your strategies—click here to read our expertly curated top picks!
Tracing the evolution of process monitoring
Process monitoring is not a new concept. It has been a part of businesses since the industrial revolution, where it was used to monitor manufacturing processes. However, with the advent of advanced technologies like artificial intelligence and machine learning, the scope and capabilities of process monitoring have significantly evolved.
Key advancements like real-time monitoring tools, predictive analytics, and automation have revolutionized the way businesses monitor their processes. These technologies have not only simplified process monitoring but also made it more accurate and insightful, enabling businesses to drive continuous improvement and innovation.
Practical guide: implementing process monitoring
Implementing process monitoring is a systematic process that begins with setting clear objectives and KPIs. Once the goals are defined, appropriate monitoring tools need to be identified and deployed. These tools collect process-related data, which is then analyzed to derive actionable insights. Additionally, it's crucial to provide training to staff members to ensure they can effectively use these tools and interpret the insights.
The choice of tools is crucial. Businesses need to consider their unique needs and choose tools that offer the right mix of functionality, ease of use, and flexibility. Some popular tools include process mining software, business intelligence platforms, and automated reporting systems.
Unlock exclusive insights and elevate your strategies—click here to read our expertly curated top picks!
Best practices for process monitoring
Process monitoring is not a one-size-fits-all approach. It needs to be tailored to the unique needs and context of each business. Some best practices include setting clear, measurable KPIs, regularly reviewing and updating the monitoring system, and fostering a culture of continuous improvement.
It's also important to avoid common pitfalls like over-monitoring, which can lead to information overload, and under-monitoring, which can result in missed opportunities for improvement. By staying focused, analyzing process data objectively, and making informed decisions, businesses can maximize the benefits of process monitoring.
Process monitoring in action: case studies
Case studies serve as powerful testimonials to the benefits of process monitoring. For instance, a leading e-commerce company used process monitoring to identify bottlenecks in its order fulfillment process, leading to improved delivery times and customer satisfaction. Similarly, a manufacturing firm used process monitoring to reduce waste and improve production efficiency, resulting in significant cost savings.
These real-world examples demonstrate the transformative power of process monitoring. They offer valuable insights and lessons that can guide professionals in their process monitoring journey.
Unlock exclusive insights and elevate your strategies—click here to read our expertly curated top picks!
Insights through data: process monitoring analysis
Data is the lifeblood of process monitoring. By analyzing process data, businesses can gain valuable insights into their operations, identify trends, and make informed decisions. For instance, data from a customer service process can reveal patterns in customer complaints, helping businesses improve their products or services.
Visual representations like charts and graphs can be effective tools for presenting process data. They make the data more accessible and understandable, enabling stakeholders to grasp complex insights quickly and easily.
Future trends in process monitoring
The future of process monitoring lies in technologies like artificial intelligence, machine learning, and blockchain. These technologies are expected to bring unprecedented levels of automation, accuracy, and transparency to process monitoring, enabling businesses to reach new heights of operational excellence.
To stay ahead of the curve, businesses need to stay abreast of these trends and prepare to incorporate them into their process monitoring practices. By doing so, they can leverage these trends to their advantage, driving business success in the process.
Related:
Risk ManagementUnlock exclusive insights and elevate your strategies—click here to read our expertly curated top picks!
Faqs about process monitoring
What are the key elements for effective Process Monitoring implementation? Effective process monitoring implementation requires clear objectives, appropriate tools, trained staff, and a culture of continuous improvement.
What is the typical timeline to see results after implementing Process Monitoring? The timeline to see results can vary depending on the scope and complexity of the processes being monitored. However, many businesses start seeing results within a few months of implementation.
Can Process Monitoring be integrated with other business management tools? Yes, process monitoring can be integrated with other business management tools like ERP systems, CRM platforms, and business intelligence software.
What are the most common challenges when applying Process Monitoring and how can they be overcome? Common challenges include lack of clear objectives, inadequate tools, and resistance to change. These can be overcome by setting clear goals, choosing appropriate tools, providing training, and fostering a culture of change.
How can small businesses implement Process Monitoring cost-effectively? Small businesses can opt for cost-effective tools like open-source software and cloud-based solutions. They can also start with monitoring a few key processes and gradually expand their scope.
Conclusion
In conclusion, process monitoring is a powerful tool that can drive business success. By understanding its concept, benefits, and best practices, businesses can leverage process monitoring to improve operational efficiency, make data-driven decisions, and gain a competitive edge. As process monitoring continues to evolve, businesses that adapt and innovate will be well-positioned to thrive in the future.
Related:
Dependency MappingUnlock exclusive insights and elevate your strategies—click here to read our expertly curated top picks!
Further reading and resources
For further reading, books like "Process Monitoring and Control" by B. Wayne Bequette and "Process Control: Modeling, Design, and Simulation" by B. Wayne Bequette are excellent resources. Websites like BPM.com and Process Excellence Network offer valuable articles and insights. For those interested in deepening their understanding, certifications like the Certified Process Professional and Lean Six Sigma can be beneficial.
Experience the next level of project management today!
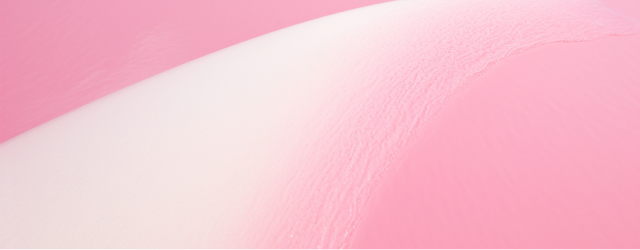
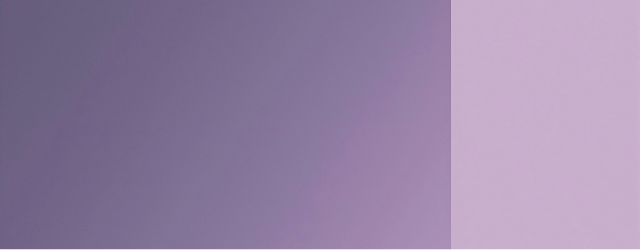
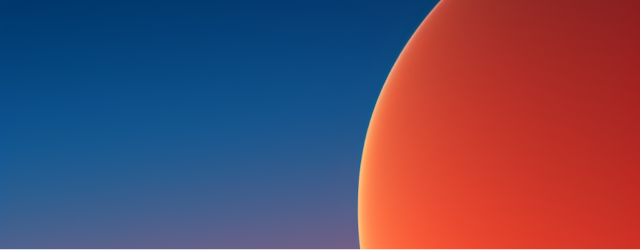
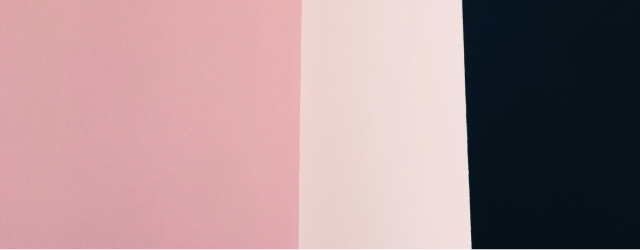
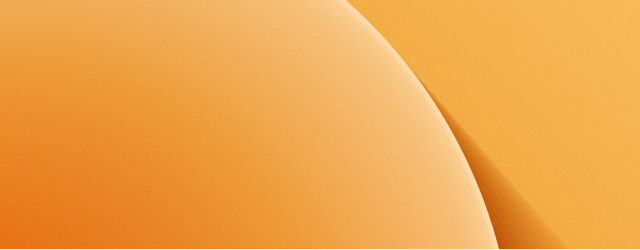
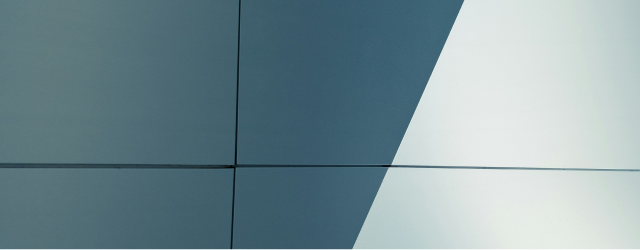
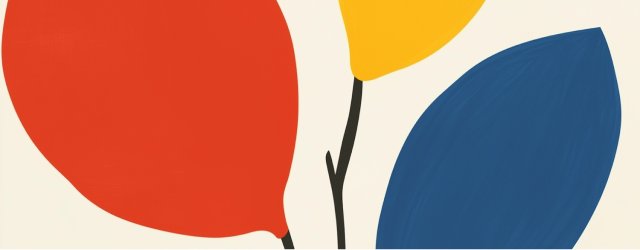
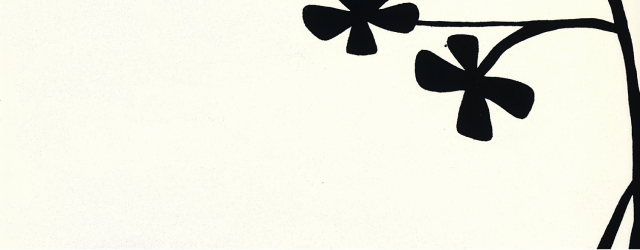