Value Stream Mapping
Gain expert insights into Value Stream Mapping, with practical how-to guides, best practices, real-world case studies, and actionable data to revolutionize your business processes.
Experience the next level of project management today!
Understanding value stream mapping
Value Stream Mapping (VSM) is a visual tool that helps businesses identify waste, streamline processes, and promote operational efficiency.
The Concept Defined
VSM is a lean-management methodology used for analyzing the current state and designing a future state for the series of events that take a product or service from the beginning of the specific process until it reaches the customer. It's a map of your material and information flows, a snapshot of reality that shows you how things are and not how you think they are.
Components of VSM
VSM consists of several key elements. First off, there's the 'Customer,' the end recipient of the product or service. Then, there's 'Supplier,' the origin of the resources needed for the process. The 'Process Steps' involve all activities that add value to the product or service. Lastly, there's 'Flow,' the movement of materials and information through the process.
Role of VSM in Business Management
VSM serves as a critical tool in business management. It helps identify bottlenecks, redundancies, and waste in the process. By visualizing these issues, it becomes easier for businesses to make informed decisions about process improvements.
The journey of value stream mapping: a historical perspective
VSM has come a long way since its inception.
The Birth and Evolution of VSM
The roots of VSM trace back to the Toyota Production System, where it was used as a tool to eliminate waste in manufacturing processes. Over the years, it evolved and found uses in other sectors, including healthcare and software development.
Key Players and Influences
Toyota has been the most significant influence on VSM. However, other players like Motorola and General Electric have also played a role in its development and application.
A detailed walkthrough: implementing value stream mapping
Implementing VSM is a meticulous process that involves various steps.
Step One: Identify the Product
The first step in VSM is to choose a product or service to map. This could be a physical product, a software, or any service provided to the customer.
Step Two: Create the Current State Map
Next, you create a 'Current State Map,' which is a visual representation of all activities involved in delivering the product or service to the customer.
Step Three: Develop the Future State Map
Once you have the current state map, the next step is to envision a 'Future State Map.' This map outlines an optimized version of the process, eliminating waste and improving efficiency.
Step Four: Develop an Action Plan
The final step is to develop an action plan to transition from the current state to the future state. This involves identifying key actions, assigning responsibilities, and setting timelines.
Tools and Technologies for Value Stream Mapping
There are numerous tools and software available for creating value stream maps, including Microsoft Visio, Lucidchart, and SmartDraw.
Unlock exclusive insights and elevate your strategies—click here to read our expertly curated top picks!
Value stream mapping best practices: the do's and don'ts
Adhering to best practices can make your VSM process more effective.
Essential Practices for Effective VSM
Do identify a clear goal for your VSM process. Do involve all stakeholders in the process. Do focus on customer value and do make data-driven decisions.
Pitfalls to Avoid in Value Stream Mapping
Don't rush the process. Don't ignore the voice of the customer. Don't neglect data and don't resist change.
Vsm in action: real-world case studies
VSM has helped numerous businesses streamline their processes and reduce waste.
Case Study 1: XYZ Manufacturing
XYZ Manufacturing, a mid-sized company, used VSM to identify bottlenecks in their production process. By eliminating these bottlenecks, they reduced lead time by 30%.
Case Study 2: ABC Healthcare
ABC Healthcare used VSM to streamline their patient admission process. They reduced the time taken for patient admission by 40%, significantly improving patient satisfaction.
Case Study 3: DEF Logistics
DEF Logistics used VSM to optimize their delivery process. By identifying and eliminating waste, they were able to reduce delivery times by 25%.
Related:
Quality AssuranceUnlock exclusive insights and elevate your strategies—click here to read our expertly curated top picks!
The power of data: quantitative insights on value stream mapping
VSM's benefits are backed by data.
Statistical Analysis Supporting VSM's Benefits
Studies have shown that businesses that adopt VSM see a significant reduction in waste and an increase in operational efficiency. For instance, a study by the Lean Enterprise Research Centre found that companies that implemented VSM saw a 45% reduction in waste.
Visual Data Illustrating VSM's Impact
Visual representations of VSM's impact, like graphs and charts, can help stakeholders understand its benefits. For instance, a bar chart comparing the time taken for a process before and after VSM implementation can illustrate the reduction in lead time.
Future gazing: upcoming trends in value stream mapping
VSM is evolving to adapt to changing business needs.
Expected Developments in VSM
With the rise of digital transformation, we can expect to see more digital tools for VSM. Additionally, AI and machine learning might play a role in automating parts of the VSM process.
Businesses and the Future of VSM
Businesses are likely to continue adopting VSM as a tool for process improvement. As businesses become more customer-focused, tools like VSM, which help align processes with customer value, will become even more critical.
Related:
Quality AssuranceUnlock exclusive insights and elevate your strategies—click here to read our expertly curated top picks!
Conclusion: embracing value stream mapping for enhanced business processes
Embracing VSM can help businesses reduce waste, improve efficiency, and deliver more value to their customers. By understanding and implementing VSM, businesses can stay competitive in today's fast-paced business environment.
Unlock exclusive insights and elevate your strategies—click here to read our expertly curated top picks!
Further reading and resources on value stream mapping
If you're interested in learning more about VSM, here are some resources.
Book Recommendations
"Learning to See: Value Stream Mapping to Add Value and Eliminate MUDA" by Mike Rother and John Shook is a must-read for anyone interested in VSM.
Relevant Websites and Articles
The Lean Enterprise Institute's website has numerous articles and resources on VSM.
Professional Courses and Certifications in VSM
Several organizations offer professional courses and certifications in VSM, including the Lean Manufacturing Institute and the American Society for Quality.
Experience the next level of project management today!
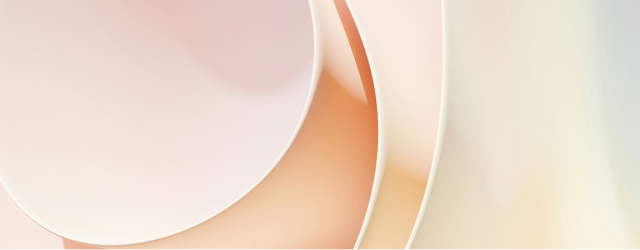
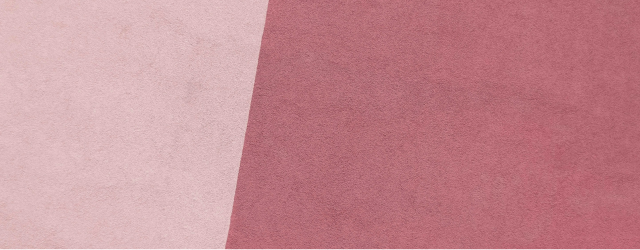
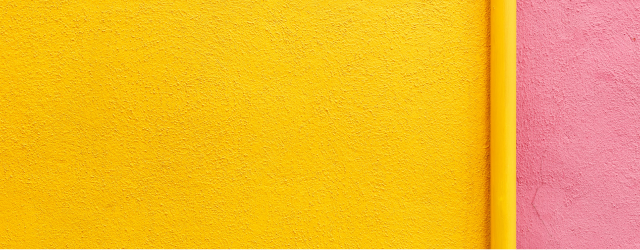
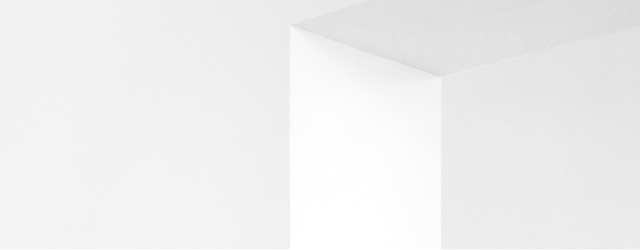
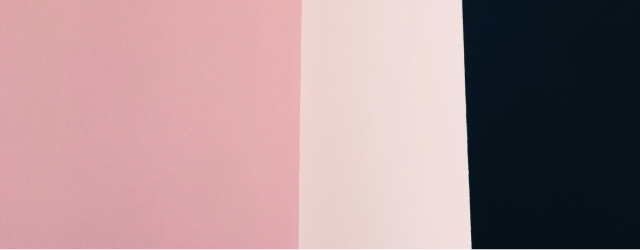
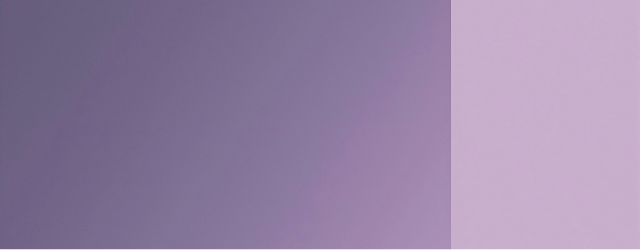
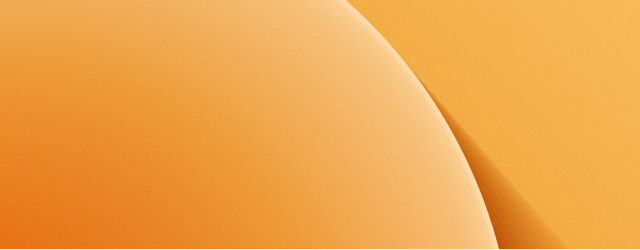
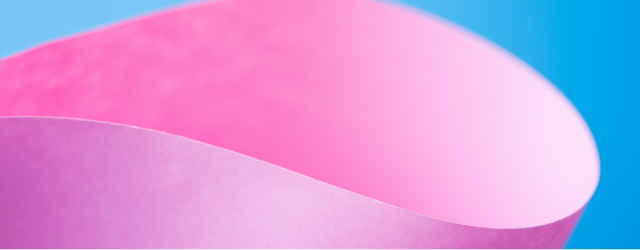