Computational Fluid Dynamics
Enhance industry performance and operational intelligence with Computational Fluid Dynamics, a key component in the realm of Digital Twin technology.
Computational Fluid Dynamics (CFD) has emerged as a transformative tool across various industries, providing comprehensive insights into fluid behaviors and interactions within different environments. As industries strive for innovation and efficiency, the need for sophisticated simulation tools has grown exponentially. CFD addresses this need by enabling precise simulations that can predict how fluids behave, thereby guiding design and operational strategies. This capability is particularly impactful when integrated into the Digital Twin ecosystem, which creates virtual models of physical systems for enhanced monitoring and analysis. These digital replicas facilitate real-time decision-making and predictive analytics, significantly enhancing operational efficiency. This article aims to explore the transformative role of CFD within the Digital Twin framework, offering insights into its applications, historical development, and future trends. It provides a roadmap for professionals looking to harness these technologies for improved outcomes.
Experience a New Level of Productivity in Meegle
Concept and definition
Detailed Definition of Computational Fluid Dynamics (CFD)
Computational Fluid Dynamics is a sophisticated tool used for simulating fluid flow and related physical phenomena. It employs mathematical models and algorithms to analyze and solve problems involving fluid motion. The primary principles of CFD are rooted in the Navier-Stokes equations, which describe the movement of fluid substances. These equations account for factors such as viscosity, pressure, temperature, and velocity, allowing for a detailed understanding of fluid dynamics. Advanced computational power and specialized software are crucial in CFD applications, as they enable the handling of complex calculations and large datasets. The importance of CFD in modern industries cannot be overstated, as it provides a virtual testing ground for designs, reducing the need for costly and time-consuming physical prototypes. By accurately predicting fluid behavior, CFD aids in optimizing design and enhancing performance across various sectors.
Integration of CFD into the Digital Twin Framework
The concept of a Digital Twin involves creating a digital replica of a physical entity, allowing for real-time monitoring and analysis. This framework comprises three core components: the physical product, the virtual representation, and the connection between them. Integrating CFD into this framework enhances the accuracy and dynamism of these digital replicas by providing detailed simulations of fluid interactions. This integration allows for sophisticated predictive analysis, enabling proactive maintenance and optimization of physical systems. The benefits are manifold, including improved efficiency, reduced downtime, and enhanced decision-making capabilities. By leveraging CFD within the Digital Twin framework, industries can achieve a higher level of operational precision and control, ultimately leading to cost savings and increased productivity.
Historical development
Evolution of Computational Fluid Dynamics
The evolution of Computational Fluid Dynamics traces back to the development of theoretical frameworks in the early 20th century. Initially, fluid dynamics were understood through analytical solutions to simplified problems. With the advent of computers in the mid-20th century, the field experienced a significant leap forward. The availability of computing power allowed for the development of numerical methods to solve complex fluid equations, leading to the creation of early CFD software. Over the decades, technological advancements, such as increased computational power and sophisticated algorithms, have propelled CFD into a crucial tool for modern engineering. Key milestones include the development of finite volume methods, turbulence modeling, and the integration of high-performance computing. These advancements have expanded the applicability of CFD across various industries, transforming it into an indispensable tool for design and analysis.
Milestones in CFD Application and Development
The application of Computational Fluid Dynamics has resulted in groundbreaking advancements across multiple industries. In aerospace, CFD has been instrumental in optimizing aerodynamics, leading to more efficient and safer aircraft designs. The automotive industry has also benefited from CFD through the enhancement of vehicle aerodynamics and thermal management systems. In the energy sector, CFD is used to maximize the efficiency of wind turbines and improve the design of natural gas pipelines. Key historical milestones include the development of commercial CFD software in the 1980s, which democratized access to these powerful tools. As CFD technology has evolved, it has set new industry standards, reshaping engineering practices and scientific exploration. The ongoing development of CFD continues to drive innovation, pushing the boundaries of what is possible in fluid dynamics simulation.
Core applications
Industry applications and functionalities of cfd
Industry applications and functionalities of cfd
Computational Fluid Dynamics finds applications across a diverse range of industries, each leveraging its capabilities to improve design, testing, and optimization processes. In the aerospace industry, CFD is used to simulate airflow over aircraft surfaces, enabling engineers to optimize designs for efficiency and performance. The automotive industry employs CFD to analyze airflow around vehicles, enhancing fuel efficiency and reducing emissions. In the energy sector, CFD plays a crucial role in optimizing the design and operation of wind turbines and solar panels. Additionally, the chemical and pharmaceutical industries use CFD to model fluid mixing and chemical reactions, improving product quality and process efficiency. Recent innovations in CFD technology, such as automated meshing and cloud-based simulations, have further enhanced its applicability, enabling more detailed and faster analyses. These advancements have solidified CFD's role as an essential tool in industry-specific applications, driving innovation and efficiency.
Real-world impact on business outcomes
Real-world impact on business outcomes
The implementation of Computational Fluid Dynamics has delivered significant improvements in business outcomes across various industries. For example, in the automotive industry, manufacturers have reported reductions in development costs and time-to-market by using CFD to virtually test and refine designs. In the aerospace sector, CFD has been credited with improving fuel efficiency by optimizing aircraft aerodynamics, resulting in significant cost savings. The energy industry has also benefited from CFD, with companies using it to enhance the efficiency of wind turbines and reduce operational costs. Case studies illustrate the tangible business benefits of CFD, including improved product performance, reduced development costs, and enhanced competitive advantage. The return on investment for businesses adopting CFD solutions is often substantial, as it enables more informed decision-making and the ability to swiftly respond to market demands. As industries continue to adopt CFD technology, the potential for improved business outcomes continues to grow.
Benefits and advantages
Operational Benefits of Computational Fluid Dynamics
The operational benefits of Computational Fluid Dynamics are manifold, offering enhancements in accuracy, efficiency, and innovation. By providing detailed insights into fluid behaviors, CFD enables engineers to make informed design decisions, reducing the likelihood of costly errors. The ability to simulate various fluid interactions in a virtual environment accelerates the design process, allowing for rapid prototyping and testing. This leads to significant time and cost savings, as physical prototypes can be minimized. Additionally, CFD enhances innovation by providing a platform for experimenting with novel designs and concepts, pushing the boundaries of what is possible. The competitive advantage gained through the adoption of CFD is evident, as companies using this technology are often at the forefront of innovation within their industries. By integrating CFD into operations, businesses can achieve higher levels of precision, efficiency, and innovation.
Comparative Analysis: Pre and Post CFD Implementation
The transformation brought by Computational Fluid Dynamics is evident when comparing processes before and after its implementation. Prior to CFD, design and testing were heavily reliant on physical prototypes, which were expensive and time-consuming to produce. The introduction of CFD allowed for virtual testing, significantly reducing the need for physical prototypes and accelerating the design process. Quantitative data showcases improvements in performance metrics, such as reduced drag in automotive designs and increased lift in aerospace applications. Qualitative benefits, such as enhanced decision-making and risk mitigation, are also apparent, as CFD provides a comprehensive understanding of fluid dynamics, enabling more informed decisions. Case studies highlight the impact of CFD on industry practices, illustrating how it has transformed processes and contributed to improved outcomes. The comparative analysis underscores the value of CFD as a transformative technology, driving efficiency and innovation in modern industry.
Integration strategies
Effective Integration of CFD with Existing Systems
Incorporating Computational Fluid Dynamics into existing systems requires a strategic approach to ensure seamless integration and maximize benefits. The first step is to conduct a thorough assessment of organizational needs and readiness for CFD implementation. This involves identifying the specific areas where CFD can add value and aligning them with business objectives. Once the needs are identified, selecting the right CFD software and tools is crucial, as they must be compatible with existing systems and workflows. Training staff and investing in skill development are essential to ensure that the team can effectively utilize these tools. Best practices for integration include establishing clear communication channels, setting realistic expectations, and continuously monitoring performance. By following these steps, organizations can effectively integrate CFD into their operations, enhancing their capabilities and driving innovation.
Challenges and Considerations in Integration
While the integration of Computational Fluid Dynamics offers numerous benefits, it also presents several challenges that must be addressed. Common obstacles include the complexity of CFD simulations, the need for specialized expertise, and the potential for data inaccuracies. To overcome these challenges, organizations should adopt a strategic approach to integration, focusing on building internal expertise and ensuring data accuracy. Risk assessment and management are crucial in the context of CFD implementation, as they help identify potential issues and develop strategies to mitigate them. It is also important to consider the impact of CFD on existing workflows and systems, ensuring that integration does not disrupt operations. By addressing these challenges and considerations, organizations can ensure successful CFD deployment and fully realize its benefits.
Future trends and predictions
Emerging Developments in CFD Technologies
The future of Computational Fluid Dynamics is poised for exciting developments, driven by advancements in technology and methodologies. One of the most significant trends is the integration of Artificial Intelligence (AI) and machine learning into CFD processes. These technologies enable more efficient data processing and analysis, leading to faster and more accurate simulations. Another emerging trend is the use of cloud-based solutions, which provide scalable computing resources and facilitate collaboration across teams. The development of real-time CFD simulations is also on the horizon, offering the potential for immediate feedback and decision-making. As these trends continue to evolve, they are expected to drive further advancements in CFD software and applications, expanding its applicability and impact across industries.
Potential Impact and Future Applications
The potential impact of Computational Fluid Dynamics in emerging industries is substantial, with opportunities for disruptive innovations and new applications. In the healthcare industry, CFD is being explored for use in medical device design and the simulation of blood flow, offering the potential to improve patient outcomes. The environmental sector is also leveraging CFD to model and predict the impact of climate change on ecosystems, providing valuable insights for conservation efforts. As industries continue to recognize the value of CFD, its role in shaping industry practices is expected to grow, driving innovation and efficiency. The future of CFD is bright, with the potential to revolutionize how industries operate and address complex challenges.
Use cases and case studies
Case Study: CFD in Automotive Industry
In the automotive industry, Computational Fluid Dynamics has played a crucial role in optimizing vehicle design and aerodynamics. A notable example is the use of CFD by a leading car manufacturer to improve the efficiency of their vehicles. By simulating airflow around different car models, the company was able to identify areas of high drag and optimize the design to reduce it. This resulted in improved fuel efficiency and reduced emissions, providing a competitive advantage in the market. The business outcomes achieved through CFD implementation were significant, with the company reporting substantial cost savings and reduced time-to-market for new models. This case study illustrates the tangible benefits of CFD in the automotive industry, highlighting its potential to enhance performance and drive innovation.
Case Study: CFD in Aerospace Engineering
Computational Fluid Dynamics has also made a significant impact in aerospace engineering, enhancing aircraft performance and safety. A leading aerospace company utilized CFD to optimize the design of their aircraft wings, improving lift and reducing drag. By simulating various flight conditions, the company was able to refine the wing shape and material selection, resulting in a more efficient and safer aircraft. The quantified benefits of this approach were substantial, with the company reporting improvements in fuel efficiency and reduced operating costs. Lessons learned from this application of CFD include the importance of accurate data and the need for continuous iteration and testing. This case study underscores the value of CFD in aerospace engineering, demonstrating its potential to drive innovation and improve outcomes.
Case Study: CFD in Renewable Energy
In the renewable energy sector, Computational Fluid Dynamics has been instrumental in optimizing the efficiency of wind turbines and solar panels. A renewable energy company used CFD to simulate airflow around wind turbines, identifying areas of turbulence and optimizing the design to capture more wind energy. This approach resulted in increased energy production and reduced costs, contributing to the company's sustainability goals. The impact of CFD on sustainability and energy production costs was significant, with the company reporting substantial improvements in efficiency and reduced environmental impact. This case study highlights the potential of CFD in the renewable energy sector, demonstrating its ability to drive innovation and contribute to a more sustainable future.
Tips for successful cfd implementation
Do's | Don'ts |
---|---|
Conduct thorough needs assessment | Skip the planning phase |
Choose the right CFD software | Underestimate the complexity of CFD |
Train staff and invest in skill development | Ignore the importance of data accuracy |
Monitor and evaluate performance regularly | Fail to integrate CFD with other systems |
Collaborate with experienced professionals | Neglect post-implementation support |
Experience a New Level of Productivity in Meegle
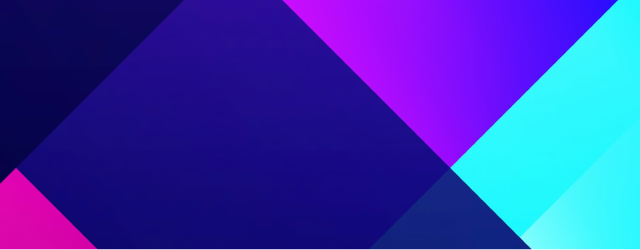
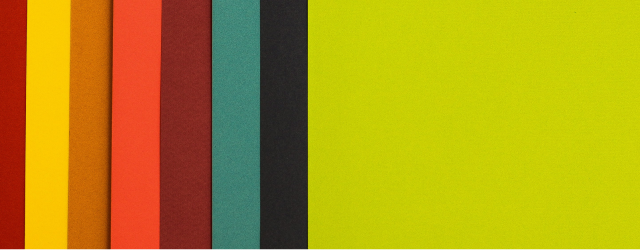
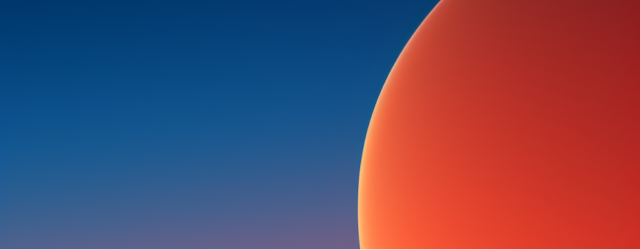
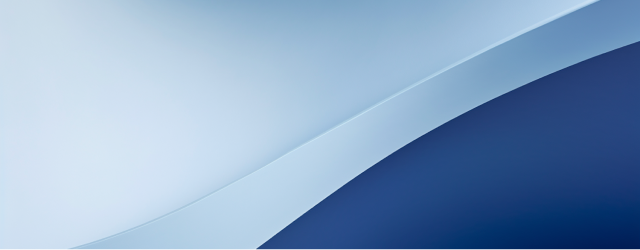
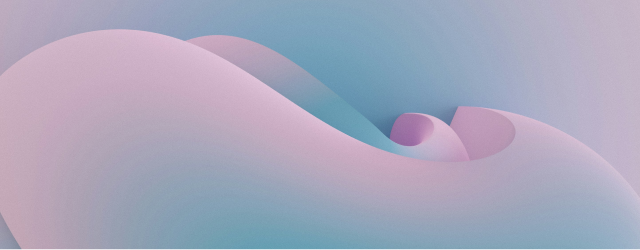
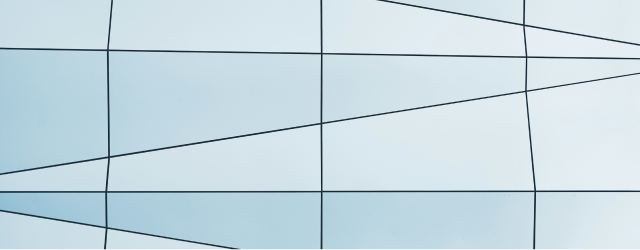
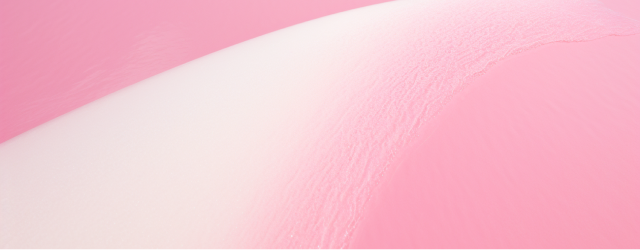
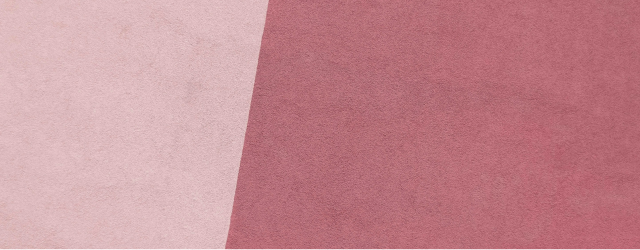