Virtual Testing
Enhance industry performance and operational intelligence with Virtual Testing, a key component in the realm of Digital Twin technology.
In the modern industrial landscape, the emphasis on efficient and cost-effective testing solutions has never been greater. Virtual testing stands out as a transformative tool, enabling industries to preemptively address potential challenges and optimize outcomes. Unlike traditional methods that often require physical prototypes and lengthy trial periods, virtual testing allows businesses to simulate real-world scenarios in a controlled digital environment. This shift not only reduces time and expense but also enhances the precision and reliability of testing processes. As industries seek to stay competitive, the integration of virtual testing into their workflows provides a significant advantage, facilitating innovation and improving product quality. By embracing this technology, companies can effectively address the increasing demand for robust testing solutions while driving forward their strategic objectives.
Experience a New Level of Productivity in Meegle
Concept and definition
Understanding Virtual Testing
Virtual testing is a sophisticated process that leverages computer simulations to evaluate the performance, reliability, and safety of products or systems before they reach the physical testing stage. This technology employs advanced modeling and simulation tools to replicate real-world conditions, allowing engineers to test various scenarios without the need for physical prototypes. The process involves creating a detailed virtual model of the product, which is then subjected to a series of simulated tests to assess its behavior under different conditions. This approach not only saves time and resources but also provides valuable insights into the product's performance, enabling engineers to make informed decisions and optimize designs. By utilizing virtual testing, companies can significantly reduce the risk of failure, improve product quality, and accelerate time-to-market.
Integration with Digital Twin Technology
Integrating virtual testing with digital twin technology enhances the accuracy and effectiveness of the testing process. A digital twin is a virtual replica of a physical object or system that continuously collects data from sensors and other sources to provide real-time insights into its performance. By combining virtual testing with a digital twin, businesses can simulate and analyze the behavior of their products or systems in real-world conditions with unprecedented precision. This synergy allows for more comprehensive testing, enabling engineers to identify potential issues early in the development process and make necessary adjustments before physical production begins. The integration of these technologies not only improves the reliability and performance of products but also streamlines the development process, reducing costs and time-to-market. As industries increasingly adopt digital twin technology, the benefits of virtual testing are becoming more apparent, providing a significant competitive advantage in today's fast-paced market.
Click here to read our expertly curated top picks!
Historical development
Evolution of Virtual Testing
The evolution of virtual testing has been marked by significant advancements in computational power, software capabilities, and data analytics. Initially, virtual testing was limited to basic simulations due to computational constraints. However, with the advent of more powerful computers and sophisticated software tools, the scope and accuracy of virtual testing have expanded dramatically. In the early stages, virtual testing was primarily used in industries like aerospace and automotive, where the cost and risk of physical testing were prohibitively high. Over time, as the technology matured, virtual testing has become more accessible and applicable across a wide range of industries. Today, it is a critical component of the product development process, enabling companies to test complex systems and products in a virtual environment with unparalleled precision and efficiency.
Key Milestones
Several key milestones have shaped the development and application of virtual testing. The introduction of finite element analysis (FEA) in the 1960s marked a significant breakthrough, allowing engineers to simulate and analyze complex structures and systems with unprecedented accuracy. The development of computer-aided design (CAD) software in the 1970s further revolutionized the field, enabling engineers to create detailed virtual models of their products. In the 1990s, the advent of powerful simulation software tools, such as ANSYS and MATLAB, expanded the capabilities of virtual testing, allowing for more comprehensive and accurate simulations. The rise of digital twin technology in the 2000s further enhanced the effectiveness of virtual testing by providing real-time data and insights into the performance of products and systems. These milestones have not only improved the accuracy and efficiency of virtual testing but have also expanded its applicability across various industries, providing a significant competitive advantage in today's fast-paced market.
Core applications
Industry applications of virtual testing
Industry applications of virtual testing
Virtual testing finds diverse applications across multiple industries, each benefiting uniquely from its capabilities. In the automotive sector, virtual testing is used extensively for crash simulations, enabling manufacturers to assess vehicle safety without the need for physical prototypes. This approach not only reduces costs but also accelerates the development process, allowing companies to bring safer vehicles to market more quickly. In the aerospace industry, virtual testing is used for structural analysis and flight simulations, providing valuable insights into aircraft performance and safety. Additionally, the healthcare industry utilizes virtual testing for the development of medical devices and surgical procedures, allowing for safer and more efficient patient care. By leveraging virtual testing, industries can optimize product design, improve safety, and reduce costs, ultimately enhancing their competitive edge in the market.
Real-world impact
Real-world impact
The real-world impact of virtual testing is evident in the numerous success stories across various industries. For instance, a major automotive manufacturer implemented virtual crash testing to evaluate the safety of their vehicles. By simulating crash scenarios in a virtual environment, the company was able to identify potential safety issues early in the development process and make necessary adjustments before production. This approach not only improved vehicle safety but also reduced development costs and time-to-market, providing a significant competitive advantage. In the aerospace industry, virtual flight simulations have revolutionized pilot training, enabling pilots to practice and refine their skills in a safe and controlled environment. This not only enhances pilot proficiency but also reduces the risk of accidents and improves overall flight safety. These examples highlight the transformative impact of virtual testing, demonstrating its potential to improve safety, efficiency, and performance across a wide range of industries.
Benefits and advantages
Operational Benefits
The operational benefits of virtual testing are profound, offering industries a means to improve processes and product outcomes substantially. One of the primary advantages is the significant reduction in costs associated with physical prototyping. By simulating real-world scenarios in a digital environment, companies can forego the expensive and time-consuming process of creating physical prototypes, leading to substantial cost savings. Additionally, virtual testing accelerates the development process, enabling companies to bring products to market more quickly. This speed not only enhances competitiveness but also allows companies to respond more rapidly to market demands and changes. Moreover, virtual testing provides valuable insights into product performance and reliability, enabling engineers to optimize designs and improve quality. By leveraging these operational benefits, companies can enhance efficiency, reduce costs, and improve product quality, ultimately gaining a significant competitive advantage in the market.
Comparative Analysis
A comparative analysis of pre and post-virtual testing implementation reveals significant improvements in project outcomes and timelines. Before the introduction of virtual testing, companies relied heavily on physical prototypes and testing, leading to longer development cycles and higher costs. Additionally, the lack of accurate simulation tools limited the ability to identify and address potential issues early in the development process. With the implementation of virtual testing, companies can now simulate and analyze product performance in a digital environment, enabling them to identify and address potential issues before physical production begins. This approach not only reduces development costs and time-to-market but also improves product quality and reliability. By comparing the outcomes of projects before and after the implementation of virtual testing, it becomes evident that this technology provides significant benefits, improving efficiency, reducing costs, and enhancing product quality and reliability.
Integration strategies
Effective Integration Techniques
Successfully integrating virtual testing into existing systems requires careful planning and execution. Companies must first conduct a thorough assessment of their current processes and identify areas where virtual testing can provide the most significant benefits. Once the potential applications have been identified, companies can select appropriate virtual testing tools and technologies that align with their specific needs and requirements. It is essential to involve key stakeholders throughout the integration process to ensure alignment and support. Additionally, companies should conduct pilot testing to validate the effectiveness of the chosen tools and methodologies before full-scale implementation. By following these effective integration techniques, companies can ensure a smooth transition and maximize the benefits of virtual testing.
Challenges and Considerations
While the benefits of virtual testing are significant, there are also challenges and considerations that companies must address to ensure successful adoption. One of the primary challenges is the initial cost of implementing virtual testing tools and technologies, which can be substantial for some companies. Additionally, there may be a learning curve associated with adopting new tools and methodologies, requiring training and support for employees. Companies must also consider the need for accurate data and models to conduct effective virtual testing, as the quality of the results depends heavily on the accuracy of the input data. By addressing these challenges and considerations, companies can effectively implement virtual testing and realize its full potential.
Future trends and predictions
Emerging Developments
The future of virtual testing is bright, with several emerging developments poised to further enhance its capabilities and impact. One of the most significant trends is the increasing integration of virtual testing with other advanced technologies, such as artificial intelligence and machine learning. By leveraging these technologies, companies can automate and optimize virtual testing processes, improving efficiency and accuracy. Additionally, the rise of the Internet of Things (IoT) is providing new opportunities for virtual testing, enabling companies to collect and analyze real-time data from connected devices. This real-time data can be used to simulate and test product performance under various conditions, providing valuable insights and improving product reliability. As these and other developments continue to emerge, the capabilities and applications of virtual testing are expected to expand, providing even greater benefits to industries.
Industry Impact
The continued evolution of virtual testing is expected to have a profound impact on various industries, creating new opportunities and driving innovation. In the automotive industry, virtual testing is expected to play a critical role in the development of autonomous vehicles, enabling manufacturers to simulate and test complex scenarios in a virtual environment. Similarly, in the healthcare industry, virtual testing is expected to revolutionize the development of personalized medicine, allowing for more precise and effective treatments. As virtual testing continues to evolve and expand, its impact on industries is expected to be significant, providing new opportunities for innovation and growth.
Use cases and case studies
Automotive Industry: Virtual Crash Testing
In the automotive industry, virtual crash testing has become a critical tool for enhancing vehicle safety and reducing development costs. By simulating crash scenarios in a virtual environment, manufacturers can assess vehicle safety without the need for physical prototypes. This approach not only reduces costs but also accelerates the development process, allowing companies to bring safer vehicles to market more quickly. A notable case study involves a major car manufacturer that implemented virtual crash testing to evaluate the safety of their vehicles. By simulating crash scenarios in a virtual environment, the company was able to identify potential safety issues early in the development process and make necessary adjustments before production. This approach not only improved vehicle safety but also reduced development costs and time-to-market, providing a significant competitive advantage.
Aerospace Sector: Virtual Flight Simulation
The aerospace sector has embraced virtual flight simulation as a powerful tool for enhancing pilot training and aircraft design. By simulating flight scenarios in a virtual environment, pilots can practice and refine their skills in a safe and controlled environment. This not only enhances pilot proficiency but also reduces the risk of accidents and improves overall flight safety. A notable case study involves an aerospace company that implemented virtual flight simulation to enhance pilot training and aircraft design. By simulating flight scenarios in a virtual environment, the company was able to provide pilots with a realistic training experience, improving their skills and reducing the risk of accidents. Additionally, the company was able to optimize aircraft design, improving performance and safety.
Healthcare: Virtual Surgical Training
In the healthcare industry, virtual surgical training has emerged as a valuable tool for improving surgical outcomes and training efficiency. By simulating surgical procedures in a virtual environment, surgeons can practice and refine their skills without the need for live patients. This not only enhances surgical proficiency but also reduces the risk of complications and improves patient outcomes. A notable case study involves a healthcare organization that implemented virtual surgical training to improve surgical outcomes and training efficiency. By simulating surgical procedures in a virtual environment, the organization was able to provide surgeons with a realistic training experience, improving their skills and reducing the risk of complications. This approach not only improved surgical outcomes but also enhanced training efficiency, providing a significant benefit to the organization and its patients.
Tips for success: do's and don'ts
Do's | Don'ts |
---|---|
Conduct thorough needs assessment | Rush the integration process |
Engage stakeholders throughout the process | Overlook training needs |
Use pilot testing for initial rollouts | Neglect iterative improvements |
Keep abreast of technology trends | Ignore feedback from end-users |
Conclusion
In conclusion, virtual testing, when integrated with digital twin technology, offers a powerful tool for enhancing industrial performance. By simulating real-world scenarios in a digital environment, companies can significantly improve efficiency, reduce costs, and enhance product quality. The synergy between virtual testing and digital twin technology provides valuable insights and real-time data, enabling businesses to make informed decisions and optimize their processes. As industries increasingly adopt this technology, the benefits of virtual testing are becoming more apparent, providing a significant competitive advantage in today's fast-paced market. By implementing effective strategies for integration and addressing potential challenges, companies can successfully adopt virtual testing and realize its full potential, ultimately driving innovation and growth.
Experience a New Level of Productivity in Meegle
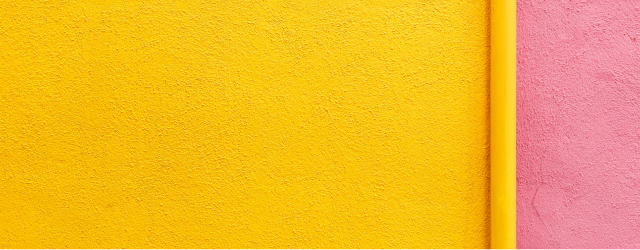
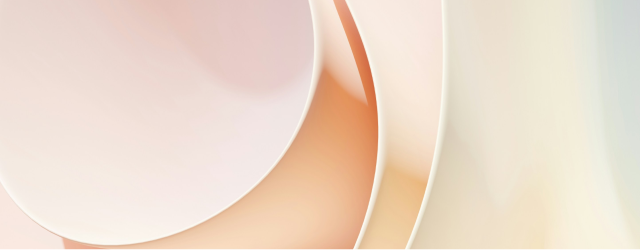
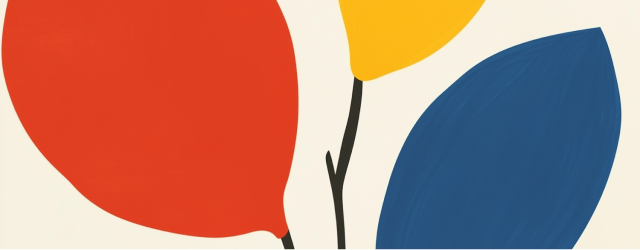
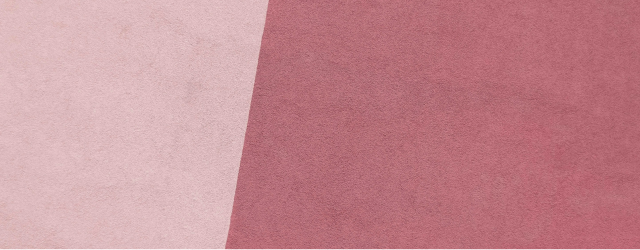
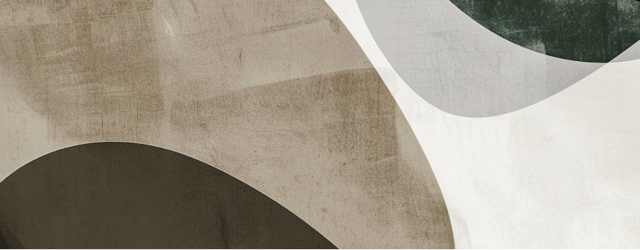
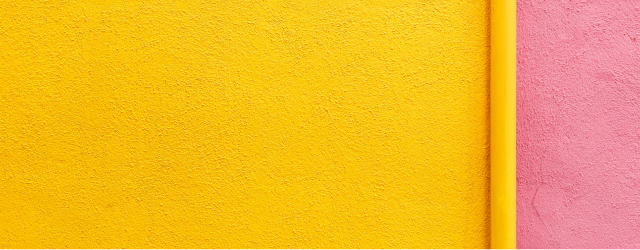
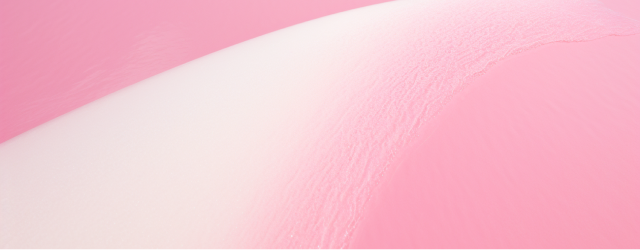
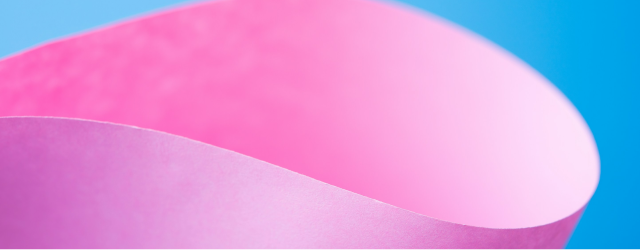