Condition Monitoring
Enhance industry performance and operational intelligence with Condition Monitoring, a key component in the realm of Digital Twin technology.
Definition and Significance
Condition Monitoring is a proactive approach that involves the continuous or periodic assessment of equipment condition to identify potential failures before they occur. By employing a range of technologies such as sensors, data analytics, and the Internet of Things (IoT), Condition Monitoring enables industries to shift from traditional reactive maintenance practices to more predictive and condition-based strategies. This shift is pivotal in enhancing operational efficiency, extending asset lifespan, and minimizing unplanned downtimes. The significance of Condition Monitoring extends beyond predictive maintenance, as it also plays a critical role in operational efficiency by allowing timely interventions, thereby preventing costly disruptions.
Digital Twin Enhancement
While Condition Monitoring itself offers significant advantages, its integration with Digital Twin technology further amplifies its potential. Digital Twins are digital replicas of physical systems that simulate real-world performance, enabling industries to visualize and analyze equipment behavior under various conditions. This integration provides a dynamic platform where data from Condition Monitoring is fed into Digital Twins, allowing for more accurate predictive analysis and improved decision-making. The synergy between these two technologies empowers industries to not only predict failures but also simulate corrective actions, thus optimizing maintenance schedules and resource allocation. This complementary relationship is crucial for industries seeking to achieve superior operational performance and strategic advantages in a competitive market.
Experience a New Level of Productivity in Meegle
Concept and definition
Understanding Condition Monitoring
Condition Monitoring encompasses a broad spectrum of practices and technologies aimed at assessing the health and performance of equipment in real-time or through periodic checks. At its core, Condition Monitoring relies on data collected from sensors that are strategically placed on critical components of machinery. These sensors continuously gather information on parameters such as vibration, temperature, pressure, and noise, which are then analyzed using advanced data analytics and IoT platforms. The primary goal is to detect anomalies and trends indicative of potential failures. By doing so, industries can schedule maintenance activities based on the actual condition of equipment rather than following arbitrary time-based schedules, thereby reducing downtime and maintenance costs. This approach not only enhances asset reliability but also extends their operational lifespan, offering significant cost savings.
Integration with Digital Twin Framework
Digital Twin technology serves as a powerful complement to Condition Monitoring by creating a virtual counterpart of physical assets. These digital replicas simulate the behavior of machinery under various scenarios, allowing industries to conduct what-if analyses and evaluate the impact of different operational strategies. By integrating Digital Twins with Condition Monitoring data, industries can achieve a more comprehensive understanding of equipment performance. This integration enables predictive analytics that goes beyond simply predicting failures; it allows industries to test corrective strategies and optimize maintenance plans in a virtual environment before implementing them in the real world. The synergy between Condition Monitoring and Digital Twin technology enhances decision-making processes and supports proactive maintenance approaches that lead to improved efficiency and reduced operational risks.
Historical development
Evolution of Condition Monitoring
The evolution of Condition Monitoring has been marked by significant milestones and technological advancements that have reshaped industrial maintenance strategies. Traditionally, maintenance activities were reactive, addressing equipment failures only after they occurred, leading to costly downtimes and increased operational risks. However, the advent of Condition Monitoring introduced a paradigm shift towards predictive and condition-based maintenance. This transition was driven by the development of sensors and data analytics technologies that enabled real-time monitoring of equipment health. The integration of IoT further revolutionized Condition Monitoring by facilitating seamless data collection and analysis across interconnected systems, enhancing predictive capabilities and enabling industries to anticipate potential failures.
Key Milestones and Innovations
Several key milestones have defined the trajectory of Condition Monitoring advancements. The introduction of vibration analysis marked a significant breakthrough, allowing industries to detect misalignments and imbalances in rotating machinery. As technology evolved, the integration of artificial intelligence (AI) and machine learning further enhanced Condition Monitoring by enabling more sophisticated data analysis and anomaly detection. Notable case studies demonstrate the transformative impact of these innovations. For instance, the aerospace industry has leveraged Condition Monitoring to optimize aircraft maintenance schedules, reducing costs and enhancing safety. The digital transformation of industries has accelerated the adoption of Condition Monitoring, with predictive maintenance becoming a cornerstone of modern industrial strategies.
Core applications
Industry-specific applications
Industry-specific applications
Condition Monitoring finds diverse applications across various industrial sectors, each with its own unique set of challenges and requirements. In the manufacturing sector, Condition Monitoring is employed to ensure optimal performance of production machinery, minimizing downtime and maximizing throughput. The energy sector, particularly in wind farms, utilizes Condition Monitoring to enhance the reliability and efficiency of wind turbines, predicting failures before they lead to costly disruptions. In the transportation industry, Condition Monitoring plays a crucial role in ensuring the safety and efficiency of rail networks and fleets. In the healthcare sector, critical equipment such as MRI machines and ventilators benefit from Condition Monitoring, ensuring uninterrupted service and patient safety. These examples illustrate how Condition Monitoring is tailored to meet specific industry needs, delivering tangible benefits and enhancing operational performance.
Real-world impact and outcomes
Real-world impact and outcomes
The real-world impact of Condition Monitoring is evident through numerous case studies that showcase tangible business improvements. For instance, a global manufacturing company implemented a Condition Monitoring system on its production line, resulting in a 20% reduction in unplanned downtimes and substantial cost savings. Metrics such as Mean Time Between Failures (MTBF) and Mean Time to Repair (MTTR) are commonly used to measure the success of Condition Monitoring implementations. By reducing the frequency and duration of equipment failures, industries can achieve long-term strategic advantages, including enhanced operational efficiency, improved asset utilization, and increased competitiveness. The ability to make informed, data-driven decisions empowers industries to optimize resource allocation and achieve sustainable growth.
Benefits and advantages
Operational and Financial Benefits
The adoption of Condition Monitoring offers a wide range of operational and financial benefits that contribute to improved efficiency and profitability. One of the most significant advantages is the reduction in maintenance costs, as Condition Monitoring allows for timely interventions and minimizes the need for costly emergency repairs. By extending the operational lifespan of assets, industries can achieve substantial cost savings and optimize their capital investments. Additionally, the ability to predict and prevent equipment failures enhances overall operational efficiency, reducing unplanned downtimes and maximizing productivity. Condition Monitoring also supports more strategic resource allocation, enabling industries to allocate maintenance efforts where they are most needed and mitigate risks effectively.
Comparative Analysis
When compared to traditional maintenance practices, Condition Monitoring emerges as a transformative approach that offers numerous advantages. Traditional maintenance often relies on fixed schedules, leading to unnecessary maintenance activities and increased downtime. In contrast, Condition Monitoring provides a data-driven approach that allows industries to perform maintenance only when necessary, based on actual equipment conditions. Success stories abound, illustrating the transformative effect of Condition Monitoring on operations. For example, a leading automotive manufacturer adopted Condition Monitoring to predict and prevent breakdowns on its assembly line, resulting in a 30% increase in production efficiency. By overcoming challenges such as unplanned downtimes and excessive maintenance costs, industries can gain a competitive edge and achieve long-term operational excellence.
Integration strategies
Effective System Integration
Integrating Condition Monitoring into existing systems requires a strategic approach to ensure seamless implementation and maximize benefits. The integration process involves several key steps and best practices. Firstly, a comprehensive assessment of existing systems and infrastructure is essential to identify potential integration points and requirements. Collaboration between IT and operational teams is crucial to align objectives and ensure a holistic approach. Industries should leverage tools and platforms that facilitate data integration and interoperability, enabling real-time data sharing and analysis across systems. An effective integration strategy also involves training staff and ensuring stakeholder buy-in to drive successful implementation.
Challenges and Considerations
Despite its benefits, integrating Condition Monitoring into existing systems can present several challenges and considerations. Common barriers include resistance to change, data security concerns, and the complexity of integrating diverse technologies. To overcome resistance, industries should focus on educating stakeholders about the value and benefits of Condition Monitoring. Data security is a critical consideration, as the integration process involves the collection and transmission of sensitive data. Industries must implement robust security measures to protect data integrity and privacy. Additionally, risk management strategies should be developed to address potential system failures and ensure business continuity.
Click here to read our expertly curated top picks!
Future trends and predictions
Technological Advancements
The future of Condition Monitoring is promising, with several emerging trends and technological advancements poised to shape its evolution. The integration of AI and machine learning is set to enhance predictive capabilities, enabling more accurate anomaly detection and predictive maintenance strategies. Big data analytics will play a crucial role in processing and analyzing large volumes of data collected from Condition Monitoring systems, providing deeper insights and actionable intelligence. The development of edge computing will enable real-time data processing at the source, reducing latency and enhancing decision-making. These advancements will drive the adoption of Condition Monitoring across industries, further enhancing its value proposition.
Industry Impacts and Applications
As Condition Monitoring continues to evolve, new applications and industries are poised to benefit from its capabilities. Industries such as agriculture and logistics are exploring the potential of Condition Monitoring to optimize equipment performance and improve operational efficiency. The integration of Condition Monitoring with emerging technologies such as blockchain is expected to enhance data security and transparency, particularly in supply chain management. Evolving business models and market dynamics will also be influenced by Condition Monitoring, as industries seek to leverage its capabilities to drive innovation and competitiveness. Strategic insights and foresight will be essential for businesses to stay ahead in the Condition Monitoring landscape and capitalize on emerging opportunities.
Use cases and case studies
Successful Implementations
-
Automotive Industry: In the automotive sector, a leading manufacturer implemented a Condition Monitoring system to predict and prevent breakdowns on its assembly line. By leveraging real-time data from sensors installed on critical machinery, the company achieved a 30% increase in production efficiency and reduced unplanned downtimes, resulting in substantial cost savings and improved competitiveness.
-
Energy Sector: In the energy sector, a wind farm operator employed Condition Monitoring to enhance the efficiency and reliability of its wind turbines. By continuously monitoring key parameters such as vibration and temperature, the operator was able to identify potential failures and optimize maintenance schedules, leading to a 25% increase in energy output and reduced operational costs.
-
Healthcare Equipment: In the healthcare industry, a hospital integrated Condition Monitoring into its critical medical equipment, including MRI machines and ventilators. This approach ensured uninterrupted service and patient safety by predicting equipment failures and scheduling timely maintenance. The hospital reported a significant improvement in equipment uptime and reliability, ultimately enhancing patient care outcomes.
Tips for successful condition monitoring
Do's | Don'ts |
---|---|
Invest in quality sensors and technology. | Don’t ignore data security and privacy issues. |
Regularly update and maintain systems. | Don’t rely solely on automated systems; human oversight is crucial. |
Train staff and encourage cross-functional collaboration. | Don’t overlook the importance of stakeholder engagement. |
Use data analytics for informed decision-making. | Don’t neglect to set clear KPIs and success metrics. |
Conclusion
In conclusion, Condition Monitoring represents a transformative force in modern industries, offering a proactive approach to maintenance that enhances operational efficiency and reduces downtime. The integration of Digital Twin technology further amplifies its potential by enabling predictive analysis and decision-making. As industries continue to embrace Condition Monitoring, they unlock strategic advantages that drive sustainable growth and competitiveness. By capitalizing on technological advancements and emerging trends, businesses can stay ahead in the evolving landscape of Condition Monitoring, ensuring continued success and innovation.
Experience a New Level of Productivity in Meegle
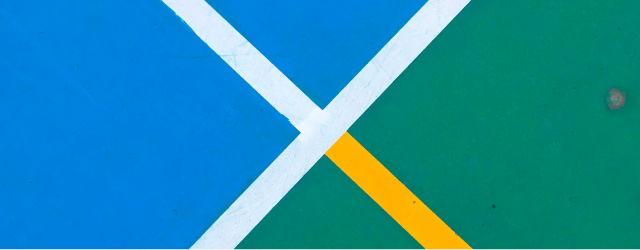
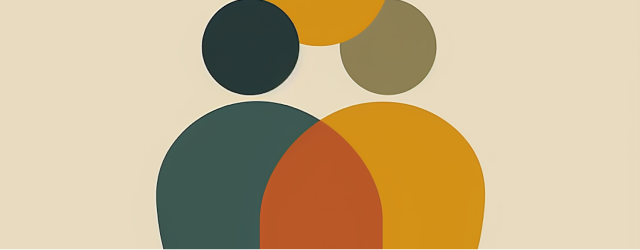
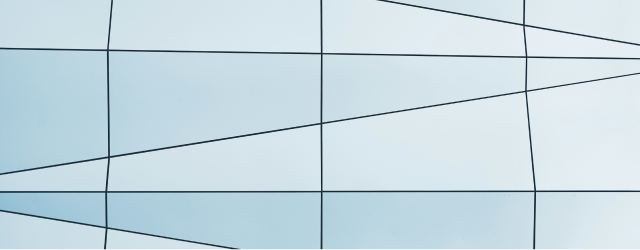
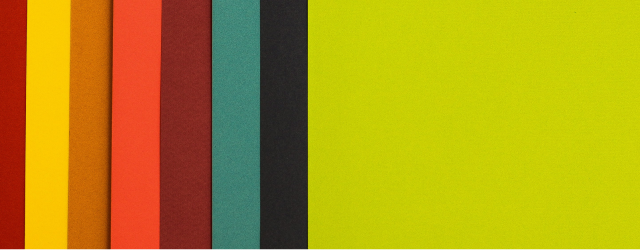
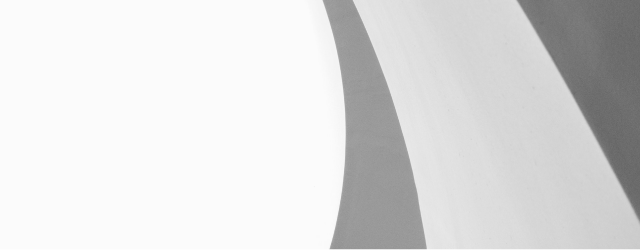
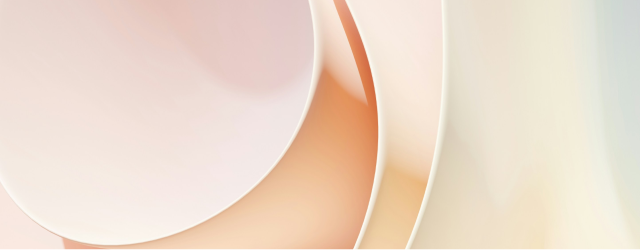
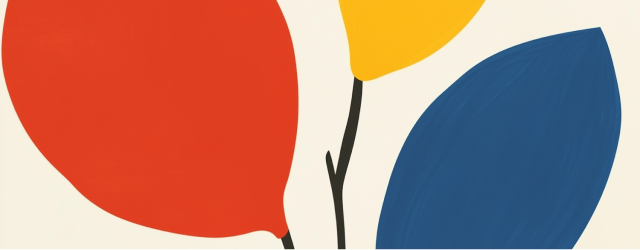
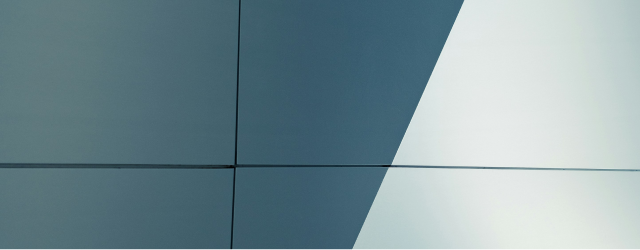