Control Systems Design
Enhance industry performance and operational intelligence with Control Systems Design, a key component in the realm of Digital Twin technology.
Introduction to Control Systems Design: Definition and Importance
Control Systems Design involves the creation of systems that manage, command, direct, or regulate the behavior of other devices or systems using control loops. It is crucial in industries where precision, reliability, and efficiency are paramount. Control Systems Design ensures that industrial processes remain within desired parameters, reducing the risk of errors and downtime. This discipline encompasses various methodologies and components, including feedback loops, sensors, and actuators, which work together to maintain optimal system performance.
Brief Overview of Digital Twin Technology
Digital Twin Technology represents a bridge between the physical and digital worlds, creating a dynamic digital counterpart of physical assets, processes, or systems. It allows for real-time monitoring and analysis, enabling industries to simulate scenarios and predict outcomes with high accuracy. By mirroring real-world operations, Digital Twins provide invaluable insights into potential inefficiencies and areas for improvement, making it an integral part of modern industrial strategy.
Discussion on the Synergy Between Control Systems Design and Digital Twin Technology
The synergy between Control Systems Design and Digital Twin Technology lies in their ability to enhance each other's capabilities. While Control Systems Design provides the foundational framework for system operations, Digital Twin Technology offers an added layer of intelligence through data-driven insights. This combination allows industries to move from reactive to proactive maintenance, improving system reliability and lifespan. The integration facilitates seamless data flow and communication between physical and digital systems, ensuring that real-time adjustments can be made to optimize performance.
Importance of Adapting These Technologies in the Current Industrial Landscape
In today’s competitive industrial environment, the adoption of advanced technologies like Control Systems Design and Digital Twin Technology is not just an option but a necessity. These technologies enable businesses to streamline operations, reduce costs, and enhance product quality and safety. Moreover, in an era where data is a critical asset, leveraging these technologies helps industries harness the power of data analytics for strategic decision-making. As industries face increasing pressure to innovate and maintain sustainability, implementing these technologies offers a clear path to achieving these goals.
Experience a New Level of Productivity in Meegle
Concept and definition of control systems design
Understanding Control Systems Design
Control Systems Design is a multidisciplinary approach that involves creating systems capable of managing or regulating the behavior of other systems. It is founded on principles from engineering, mathematics, and computer science, ensuring that systems behave predictably and efficiently. The key components of Control Systems Design include feedback loops, which are used to control the dynamics of the system; sensors, which collect data from the environment; and actuators, which make necessary adjustments based on the feedback received. Together, these components form the backbone of a control system, ensuring that processes remain stable and within desired parameters.
The methodologies employed in Control Systems Design vary depending on the complexity and requirements of the system. Common approaches include linear and non-linear control, adaptive control, and robust control, each offering unique benefits based on the application. For instance, linear control is suitable for systems that operate within a specific range, while adaptive control is ideal for environments where conditions change dynamically. By understanding these methodologies, industries can tailor their control systems to meet specific operational needs effectively.
Integrating Control Systems Design with Digital Twin Technology
Integrating Control Systems Design with Digital Twin Technology involves embedding digital twins within the control system framework to enhance its functionality. Digital Twins act as real-time data repositories, continuously updating to reflect changes in the physical environment. This integration allows for improved predictive analytics and real-time monitoring, providing a comprehensive view of system performance and potential issues. By employing Digital Twin Technology, industries can simulate various scenarios, test outcomes, and implement changes before they affect the physical system, thus minimizing risks and optimizing efficiency.
The relevance of Digital Twin Technology in Control Systems Design is evident in its ability to offer a holistic perspective on system operations. By incorporating digital twins, control systems can achieve higher accuracy in predictions and quicker response times to changes in the environment. This capability is crucial in industries where timing and precision are critical, such as aerospace, automotive, and energy. The benefits of this integration include extended system lifespan, reduced maintenance costs, and enhanced operational efficiency, making it an invaluable asset for modern industries.
Click here to read our expertly curated top picks!
Historical development of control systems design
Evolution in the Field
The field of Control Systems Design has evolved significantly since its inception, driven by technological advancements and industrial demands. Its origins can be traced back to the early 20th century, with the development of feedback control systems in the automotive and aerospace industries. These early systems laid the groundwork for modern control theory, which emerged in the mid-20th century and introduced advanced mathematical models to design more complex and efficient systems.
Key milestones in the evolution of Control Systems Design include the introduction of state-space representation in the 1960s, which provided a unified framework for analyzing dynamic systems. The advent of digital control systems in the 1970s marked another significant leap, enabling more precise and flexible system designs. By the 1980s, computer-aided design (CAD) tools revolutionized the field, allowing engineers to simulate and optimize control systems with unprecedented accuracy.
Milestones and Innovations
Over the decades, Control Systems Design has witnessed numerous innovations that have transformed its applications and capabilities. Automation, introduced in the late 20th century, brought about significant changes by replacing manual operations with automated processes, thereby increasing efficiency and reducing human error. The integration of computer-aided design tools facilitated the development of more sophisticated control systems, enabling industries to design and test systems virtually before implementation.
In recent years, artificial intelligence (AI) and machine learning have begun to play a pivotal role in Control Systems Design. These technologies allow systems to learn from data and improve their performance over time, adapting to changing conditions and optimizing operations autonomously. The combination of AI with traditional control systems has led to the emergence of intelligent control systems that can handle complex, non-linear processes with ease, further expanding the potential applications of Control Systems Design in modern industries.
Core applications and impact
Diverse industrial applications
Diverse industrial applications
Control Systems Design finds applications across a broad spectrum of industries, each benefiting from its precision and efficiency enhancements. In manufacturing, control systems are integral to automating production lines, ensuring that processes run smoothly and consistently. For example, in the automotive industry, control systems manage everything from engine performance to safety features like anti-lock braking systems, enhancing both efficiency and safety.
In the aerospace sector, Control Systems Design is critical for flight control and navigation systems, where precision and reliability are paramount. Similarly, in the energy sector, control systems optimize the generation and distribution of power, ensuring that supply meets demand efficiently while minimizing waste. These applications demonstrate the versatility of Control Systems Design, as it adapts to the specific needs of each industry to deliver operational improvements and cost savings.
Real-world examples
Real-world examples
Example 1: Control Systems in the Automotive Industry
In the automotive industry, Control Systems Design is employed extensively to enhance vehicle performance and safety. Modern vehicles are equipped with advanced control systems that manage engine dynamics, transmission, and braking systems. These systems rely on a network of sensors and actuators to monitor and adjust vehicle parameters in real-time, ensuring optimal performance under varying conditions. As a result, vehicles are not only more efficient but also safer, with features like adaptive cruise control and electronic stability control becoming standard.
Click here to read our expertly curated top picks!
Benefits and advantages
Operational Improvements
The adoption of Control Systems Design offers a multitude of operational benefits, enhancing precision, efficiency, and cost-effectiveness across industries. By automating processes and reducing human intervention, control systems minimize the risk of errors and increase productivity. This leads to significant cost savings, as processes are executed more efficiently with less waste. Moreover, control systems enable real-time monitoring and adjustments, ensuring that operations remain within optimal parameters and reducing downtime.
Case studies illustrate the transformative impact of Control Systems Design on industrial operations. For instance, in the manufacturing sector, companies that have implemented advanced control systems report increased throughput and reduced production costs. Similarly, in the automotive industry, control systems have led to more fuel-efficient vehicles and improved safety features, enhancing the overall driving experience. These examples underscore the value of Control Systems Design in driving operational excellence and achieving competitive advantage.
Comparative Analysis
When comparing traditional systems to Control Systems Design, the advantages of the latter become evident. Traditional systems often rely on manual processes and static controls, which can be inefficient and prone to errors. In contrast, Control Systems Design offers dynamic control capabilities, allowing for real-time adjustments based on feedback from the environment. This results in significant improvements in productivity, reliability, and scalability.
Quantifiable improvements demonstrate the superiority of Control Systems Design. Industries that have transitioned from traditional systems to advanced control systems report increased output and reduced operational costs. Moreover, the ability to scale and adapt to technological changes ensures that industries remain competitive in a rapidly evolving market. By leveraging Control Systems Design, businesses can achieve sustainable growth and maintain a leading position in their respective fields.
Integration strategies for control systems design
Effective Integration Techniques
Integrating Control Systems Design with existing industrial systems requires careful planning and execution. Successful integration hinges on system compatibility and seamless data integration, ensuring that new control systems operate harmoniously with legacy systems. One effective strategy involves conducting a comprehensive assessment of current systems and identifying areas where control systems can enhance performance. This may involve upgrading existing infrastructure or implementing new technologies that support seamless integration.
Cloud computing and the Internet of Things (IoT) play a crucial role in facilitating integration. By leveraging cloud-based platforms, industries can achieve centralized data management and real-time analytics, enabling more informed decision-making. IoT devices enhance connectivity between physical assets and control systems, providing valuable data for optimizing operations. Together, these technologies create a robust framework for integrating Control Systems Design into industrial operations, maximizing efficiency and effectiveness.
Challenges and Considerations
Despite the benefits of integrating Control Systems Design, industries often face several challenges during the process. Common hurdles include system compatibility issues, data integration complexities, and resistance to change from stakeholders. To overcome these challenges, industries must adopt a strategic approach that involves comprehensive planning, stakeholder involvement, and continuous training.
Solutions for overcoming integration hurdles include conducting pilot projects to test system compatibility and address potential issues early on. Engaging stakeholders throughout the integration process ensures that their concerns are addressed and fosters a sense of ownership and collaboration. Continuous training and development programs equip employees with the skills needed to operate and maintain new systems, ensuring a smooth transition and long-term success. By addressing these challenges proactively, industries can achieve successful integration and realize the full potential of Control Systems Design.
Future trends and predictions
Emerging Developments
The future of Control Systems Design and Digital Twin Technology is poised for exciting developments, driven by advancements in AI, IoT, and big data. These technologies are expected to further enhance the capabilities of control systems, enabling even more precise and intelligent operations. AI and machine learning will continue to play a significant role in automating decision-making processes, allowing control systems to adapt and optimize autonomously.
The integration of IoT devices will provide unprecedented levels of connectivity and data availability, offering real-time insights into system performance. This will enable industries to predict and prevent issues before they arise, further reducing downtime and maintenance costs. As big data analytics become more sophisticated, control systems will harness the power of vast datasets to drive continuous improvement and innovation.
Industry Impacts
The anticipated developments in Control Systems Design and Digital Twin Technology are expected to have profound impacts across various industries. In manufacturing, these technologies will enable the creation of smart factories, where processes are fully automated and optimized for efficiency. In the energy sector, control systems will enhance the management of renewable energy sources, contributing to a more sustainable energy future.
These advancements will also lead to shifts in industrial processes and workforce dynamics. As control systems become more autonomous, the demand for skilled workers who can manage and maintain these technologies will increase. Continuous learning and adaptation will be essential for industries to remain competitive and capitalize on emerging opportunities. By embracing these future trends, industries can achieve greater operational efficiency, sustainability, and innovation.
Use cases and case studies
Successful Implementations
Example 1: Manufacturing Process Optimization
In the manufacturing sector, Control Systems Design has been successfully implemented to optimize production processes. One notable case involves a leading automotive manufacturer that integrated advanced control systems to automate its assembly line. By leveraging real-time data and predictive analytics, the company achieved significant improvements in production speed and quality. The integration of control systems also reduced downtime and maintenance costs, resulting in substantial cost savings and increased profitability.
Example 2: Smart Grid Management in the Energy Sector
The energy sector has also benefited from the implementation of Control Systems Design, particularly in the management of smart grids. A major utility company employed control systems to optimize energy distribution and balance supply and demand in real-time. By integrating renewable energy sources and leveraging digital twin technology, the company enhanced grid stability and reduced carbon emissions. This successful implementation demonstrates the potential of control systems to drive sustainability and efficiency in the energy sector.
Example 3: Enhanced Supply Chain Logistics
Control Systems Design has been instrumental in enhancing supply chain logistics for a global logistics provider. By implementing dynamic control systems, the company improved its inventory management and distribution processes. The integration of IoT devices allowed for real-time tracking and monitoring of shipments, reducing delays and improving customer satisfaction. This case study highlights the value of control systems in optimizing supply chain operations and improving overall efficiency.
Lessons and Insights
Successful implementations of Control Systems Design provide valuable lessons and insights for industries looking to adopt these technologies. Key lessons include the importance of comprehensive planning and stakeholder engagement throughout the integration process. By involving stakeholders early on, industries can address potential concerns and foster a collaborative environment.
Insights into overcoming common challenges highlight the need for continuous training and development programs. Equipping employees with the skills needed to operate and maintain new systems ensures a smooth transition and long-term success. Additionally, adopting a strategic approach that involves pilot projects and rigorous testing can mitigate risks and maximize the benefits of control systems. By learning from these successful implementations, industries can achieve optimal results and drive innovation and efficiency.
Do's and don'ts of control systems design
Do's | Don'ts |
---|---|
Clearly define system objectives | Avoid neglecting stakeholder communication |
Utilize predictive analytics for optimization | Do not rush the integration process |
Ensure thorough testing and validation | Ignore cybersecurity considerations |
Invest in continuous training and development | Overlook the need for regular system updates |
Conclusion
In conclusion, Control Systems Design plays a critical role in enhancing industrial efficiency, offering numerous benefits from increased precision to cost savings. By integrating this technology with Digital Twin Technology, industries can achieve unprecedented levels of operational excellence and sustainability. The examples and case studies presented in this article demonstrate the transformative impact of these technologies across various sectors, highlighting their potential to drive innovation and growth.
As industries face increasing pressure to remain competitive, adopting Control Systems Design and Digital Twin Technology becomes essential. By following the integration strategies and best practices outlined in this article, industries can successfully implement these technologies and realize their full potential. Looking ahead, continuous learning and adaptation will be key to staying ahead of emerging trends and advancements in this dynamic field.
Experience a New Level of Productivity in Meegle
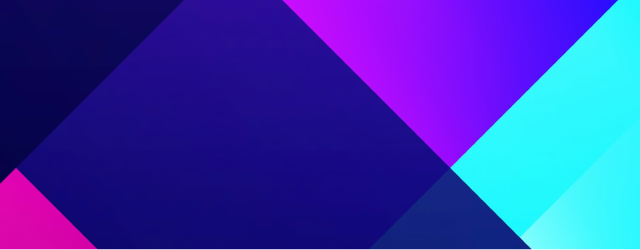
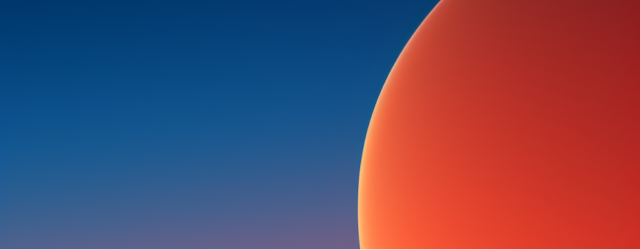
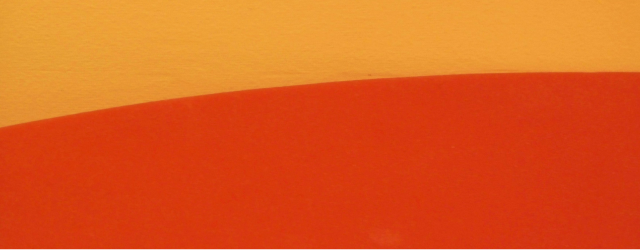
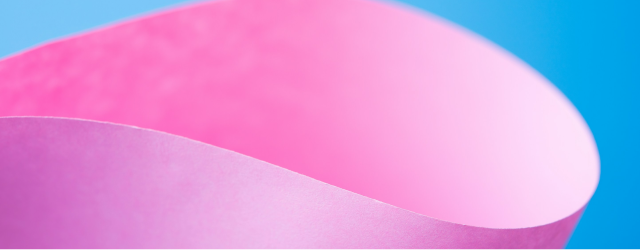
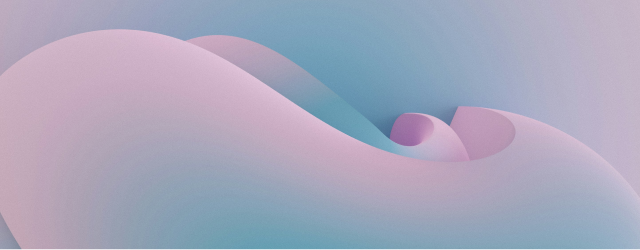
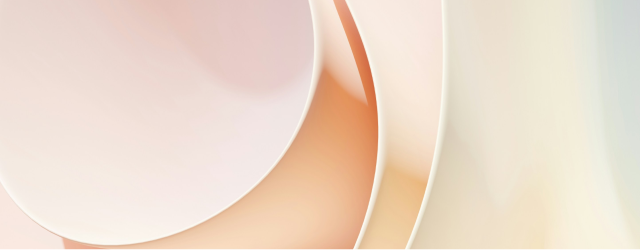
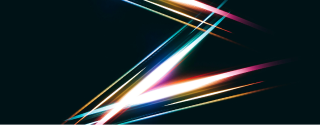
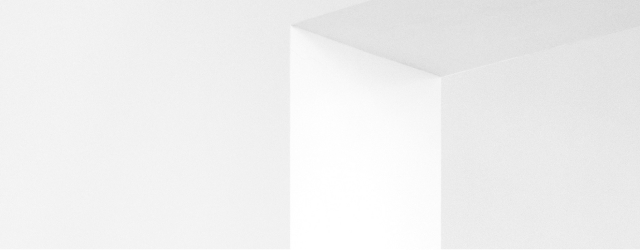