How to Implement Kanban in Automotive
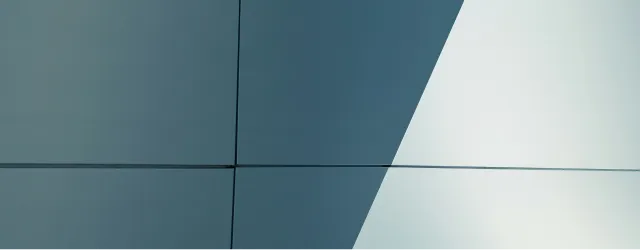
Kanban, originally developed in the manufacturing world by Toyota, is a powerful tool used to visualize workflows, limit work-in-progress (WIP), and optimize production processes. In the automotive industry, Kanban is particularly useful for improving manufacturing efficiency, streamlining supply chains, and managing vehicle maintenance and repair. As automotive manufacturers and service teams move towards more agile and lean methods, Kanban provides a way to continuously improve, minimize waste, and meet customer demands with better precision.
Implementing Kanban in automotive processes involves applying its principles to the unique needs of the industry. This article will guide you through the fundamental concepts of Kanban, its benefits, and the steps to successfully implement it in your automotive operations.
Understanding the Kanban Method
Kanban is a visual management method that helps teams track workflows and ensure smooth operations by controlling the flow of work. In automotive manufacturing, this can be applied to both the production line and the parts supply chain. The central idea of Kanban is that work should only proceed when there is capacity to handle it—this minimizes bottlenecks and maximizes efficiency.
Kanban uses a simple yet effective system of visual signals to manage workflows. These signals (often in the form of cards or digital tools) indicate when an action needs to be taken, whether that’s replenishing stock, moving parts to the next phase, or adjusting production schedules.
Dive into our expertly crafted article exploring Automotive Hardware Production, where you'll get in-depth insights, practical applications, and industry best practices tailored for hardware enthusiasts and professionals.
Benefits of Kanban in the Automotive Industry
The automotive industry deals with complex processes, ranging from high-volume manufacturing to vehicle maintenance and customer service. Kanban provides several advantages:
- Improved Efficiency: By visualizing workflows, Kanban helps identify inefficiencies and bottlenecks in the production process. This leads to smoother operations and reduced downtime.
- Reduced Lead Times: With Kanban, components are only replenished when needed, allowing manufacturers to respond quickly to demand changes and avoid excess inventory.
- Better Capacity Management: Limiting WIP ensures that teams are not overburdened, allowing them to focus on quality work and prevent production delays.
- Enhanced Communication: With visual boards, teams can easily communicate task statuses, identify problems, and address issues before they escalate.
Meegle's intuitive dashboard can help automotive companies visualize their workflows, identify inefficiencies, and streamline processes with real-time updates on inventory and production.
Key Principles of Kanban
There are several core principles that make Kanban an effective tool for the automotive industry:
- Visualizing Work: Creating a clear picture of the tasks at hand helps identify bottlenecks and improve decision-making.
- Limiting WIP: By setting WIP limits, you ensure that only a certain number of tasks are worked on at a time. This reduces multitasking and increases focus.
- Managing Flow: Keeping work flowing smoothly throughout the production process helps reduce lead time and prevents delays.
- Making Process Policies Explicit: Defining and communicating the rules that guide the work process ensures consistency and transparency.
- Improving Collaboratively: Continuous improvement (kaizen) is at the heart of Kanban. Regularly reviewing processes allows for incremental improvements in workflow and quality.
Visualization of Workflow
Visualizing the workflow is a key element of Kanban, and it’s particularly useful in automotive operations, where multiple teams are involved in different stages of the production process.
- Kanban Boards: A Kanban board visually represents the workflow. Each task is moved across the board as it progresses through different stages, such as “To Do,” “In Progress,” and “Completed.”
- Swimlanes: To improve clarity, Kanban boards often include swimlanes. These horizontal lanes categorize different processes or teams within the workflow, helping teams prioritize work and track progress.
- Kanban Cards: Each task or work item is represented by a card. These cards contain all necessary information, such as work details, assigned personnel, and deadlines. When the work is complete, the card is moved to the next column on the board.
By using tools like Meegle, automotive companies can implement custom Kanban boards that are tailored to their specific processes, improving communication and visibility across the team.
Work-in-Progress (WIP) Limits
One of the main principles of Kanban is limiting the amount of work in progress (WIP). This ensures that teams aren’t overburdened and helps maintain steady, uninterrupted flow.
For automotive manufacturers, setting appropriate WIP limits helps reduce bottlenecks and allows for faster response times to changing demand. It also prevents overproduction, which can tie up resources and lead to excess inventory.
Choosing the Right Kanban Tools
To implement Kanban effectively in automotive operations, the right tools are essential. There are several software tools available, such as KanBo and Meegle, which can help automotive businesses visualize, track, and optimize their Kanban boards.
Meegle offers customizable templates that help automotive companies create Kanban boards suited to their unique workflows, giving them an easy-to-use tool for tracking progress and managing production schedules.
Customizing Kanban Boards
The automotive industry involves various tasks, such as assembling parts, testing vehicles, managing inventories, and coordinating logistics. Each of these tasks can be represented on a Kanban board to ensure smooth operations.
To customize Kanban for automotive processes, consider the following steps:
- Identify Key Stages: The production process in automotive manufacturing often includes stages such as assembly, testing, quality control, and delivery. Define these stages clearly on your Kanban board.
- Assign Tasks to Teams: Use Kanban boards to assign tasks to specific teams or departments, ensuring that each group knows what needs to be done.
- Create Visual Cues: Use color coding or icons on your Kanban cards to represent different priorities or task types, making it easier for teams to identify critical tasks.
Setting Up Your Kanban System
When setting up a Kanban system in automotive operations, it’s crucial to:
- Define Workflow Stages: Clearly outline the steps that tasks go through in your process, from raw materials to finished products.
- Create Explicit Policies: Define what actions trigger the next step in the process. For example, when should an item be moved from “In Progress” to “Quality Control”?
- Monitor and Adjust: Constantly monitor your Kanban board to identify issues and make improvements. As with any agile method, the key is continuous improvement.
Managing Flow in Automotive Processes
Kanban helps automotive companies maintain smooth workflows, which is crucial in an industry where delays can result in significant costs. By visualizing each stage of production, teams can see where delays occur and make adjustments as needed.
For instance, if a component is delayed in the “Quality Control” stage, the Kanban system allows the team to identify this problem quickly and take corrective action.
Identifying and Implementing Feedback Loops
In Kanban, feedback loops are essential for continuous improvement. In automotive manufacturing, feedback loops can be used to assess quality control, monitor production rates, and improve efficiency.
Feedback should be gathered regularly to address any issues and adjust production processes. Kanban’s visual system makes it easy for managers to spot bottlenecks and work with teams to find solutions.
Balancing Demand and Capacity
Kanban’s pull system ensures that production is based on demand, not forecasts. This is especially beneficial in the automotive industry, where customer demand can fluctuate. By balancing production with demand, companies can avoid excess inventory and reduce storage costs.
Overcoming Challenges in Implementation
While Kanban is a powerful tool, implementing it in automotive manufacturing can come with challenges. These may include resistance to change, lack of training, or difficulty in transitioning from traditional manufacturing methods.
To address these challenges, ensure that all team members are adequately trained and that the transition to Kanban is well communicated. It’s also helpful to start small, testing Kanban with a specific section of the production process before expanding it to the entire operation.
Continuous Improvement with Kanban
Kanban is rooted in the philosophy of continuous improvement. To maintain success, it’s important to regularly review your Kanban system and make adjustments. This could involve refining WIP limits, improving workflows, or adopting new tools like Meegle’s custom templates for further optimization.
Regular Review and Adjustments
Constant evaluation is key to improving your Kanban system. Regularly assess your Kanban boards to see if you’re meeting your production goals and if there are any bottlenecks in the system. Meegle’s tracking and feedback features allow managers to measure performance, helping to identify areas for further improvement.
Read more: IoT In Automotive
Unlock Continuous Improvement and Efficiency with Meegle
Implementing Kanban in automotive manufacturing can streamline your production processes, minimize waste, and improve communication across teams. By visualizing workflows, setting WIP limits, and fostering a culture of continuous improvement, you can address key inefficiencies and drive better performance.
Meegle’s customizable Kanban templates and intuitive tools make it easier than ever to adopt and scale Kanban across your automotive operations. With real-time tracking and optimized workflows, Meegle ensures that your business continuously adapts and thrives in a competitive market.
Try Meegle for free and see how it can optimize your manufacturing processes!
The world’s #1 visualized project management tool
Powered by the next gen visual workflow engineRead More
Check All BlogsStart creating impactful work today
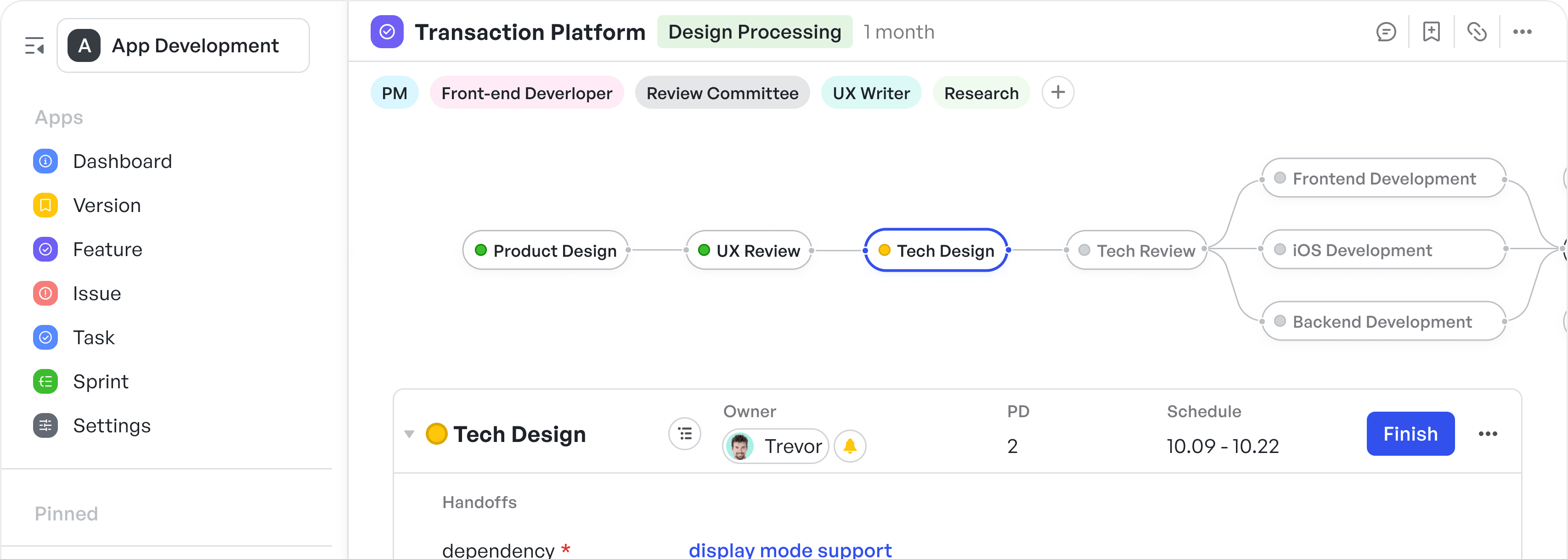