How to Implement Kanban in Manufacturing
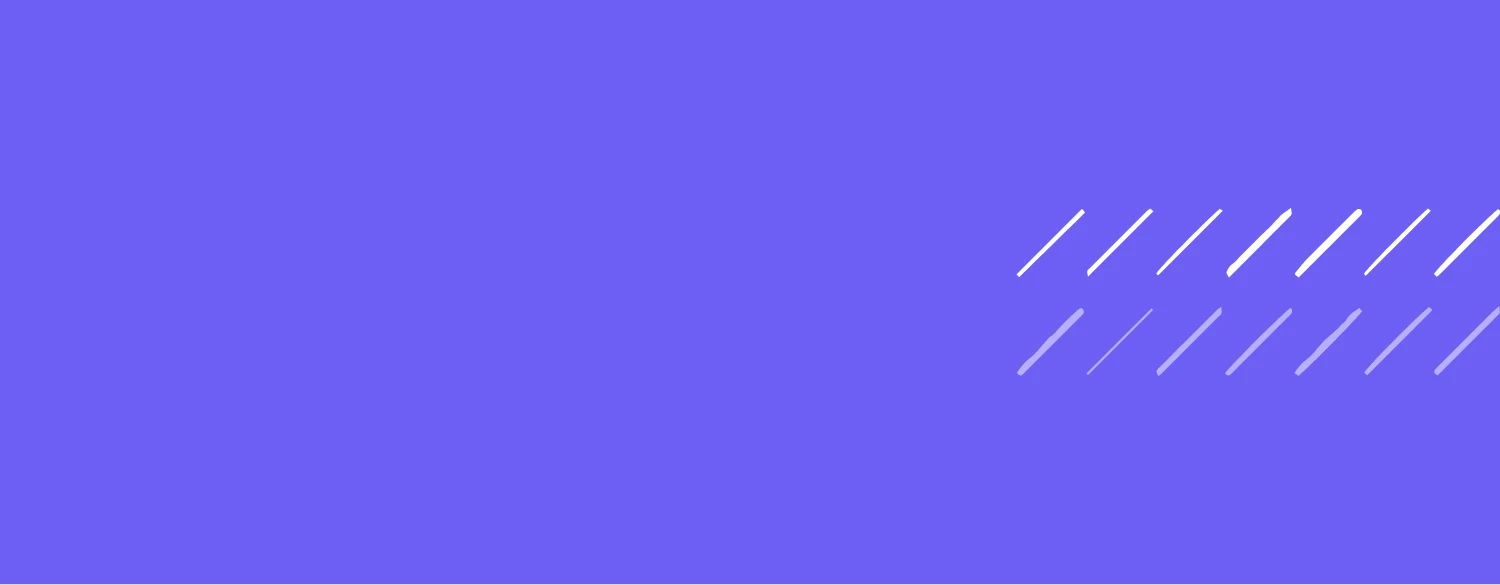
Kanban is a powerful system that originated in manufacturing but has since spread to other industries due to its effectiveness in streamlining workflows and improving efficiency. It operates on simple yet impactful principles like visualizing work, limiting work in progress (WIP), and managing flow.
The result?
Significant reductions in lead times, inventory costs, and overall process inefficiencies.
In manufacturing, Kanban offers a way to ensure production systems run smoothly, tasks are completed on time, and the right products are made when needed.
In this article, we’ll explore how to implement Kanban in manufacturing to optimize your production processes.
Understanding the Kanban System
At its core, Kanban is a visual tool designed to manage the flow of tasks or materials in a production system. It’s all about creating a more efficient production process by minimizing waste and ensuring that work moves through each stage of production at the right time.
A Kanban system works through the use of visual cues—usually cards or signals—that help track materials, parts, or tasks as they move through production. These cards are attached to items in the production process and indicate when it’s time to reorder or move materials to the next phase.
Key Types of Kanban
There are several types of Kanban that can be used in manufacturing to manage inventory and streamline processes effectively. The most common types include:
Production Kanban
This type of Kanban signals the need to produce more items. When the number of products in a specific stage or inventory drops below a predefined level, the production Kanban is used to trigger the next batch of production. This helps maintain continuous flow and prevents bottlenecks.
Withdrawal Kanban
The withdrawal Kanban is used to request parts or materials from a storage location. When an item or component is needed in a particular part of the process, the withdrawal Kanban ensures that inventory is moved and that the right materials are available at the right time.
Transportation Kanban
This Kanban type is used to move parts or materials from one location to another. For example, it could signal the movement of raw materials to the assembly line, ensuring that production can continue without delays.
Benefits of Using Kanban in Manufacturing
Implementing Kanban in manufacturing offers numerous advantages, leading to more streamlined and cost-effective operations. Some key benefits include:
Reduced Lead Times
Kanban helps manufacturers reduce lead times by providing a clear visual cue when new production is needed. This keeps production cycles moving at an optimal pace and ensures that materials are available when required.
Decreased Inventory Costs
With the use of Kanban, companies can keep inventory levels low and only order what is needed. By reducing overstocking and minimizing waste, manufacturers can lower their inventory holding costs.
Improved Productivity
By visualizing workflow and limiting WIP, Kanban helps workers focus on completing tasks before starting new ones. This minimizes delays, reduces the time spent switching between tasks, and increases overall productivity.
Step-by-Step Guide to Implementing Kanban
To successfully implement a Kanban system in manufacturing, it’s important to follow a structured approach. Here’s a step-by-step guide to help you get started:
- Map Workflow Stages
The first step in implementing Kanban is to map out the workflow stages of your production process. This will allow you to identify where bottlenecks or delays typically occur. Understanding the flow of materials and work will help you design an effective Kanban system that addresses your specific needs.
- Establish Work-in-Progress (WIP) Limits
WIP limits help ensure that your team doesn’t become overwhelmed by taking on too many tasks at once. By setting limits on the number of items in each workflow stage, you can prevent bottlenecks and improve the overall flow of work. WIP limits allow teams to focus on completing tasks before starting new ones, which reduces delays and boosts productivity.
- Design Kanban Cards
Kanban cards are the visual signals that indicate when materials or tasks need to be moved, produced, or replenished. These cards can be physical or digital, depending on your system. When designing Kanban cards, ensure that they include all necessary information, such as part numbers, quantities, and instructions. Each card should clearly show what action needs to be taken.
- Set Up Visual Management Tools
Visual management tools, like Kanban boards, play a key role in ensuring that everyone involved in the production process understands what’s happening at all times. These tools help to track the progress of tasks, inventory levels, and resource needs. Whether you use a physical board or a digital system, visual management is a crucial part of Kanban in manufacturing.
Incorporating Continuous Improvement Strategies
Kanban is based on the principle of continuous improvement, where teams regularly review and refine their processes. As you implement Kanban, focus on tracking performance and identifying opportunities for optimization.
- Kaizen: This continuous improvement strategy is often used in conjunction with Kanban. By holding regular review meetings, teams can identify areas where they can improve processes and reduce waste.
- Feedback Loops: Regular feedback from employees at every stage of production helps highlight problems early and correct them quickly, reducing the risk of delays.
Real-World Examples of Kanban Implementation
Case Study: Company A
Company A, a manufacturing company producing consumer electronics, adopted Kanban to optimize their assembly line. Before Kanban, they were struggling with high levels of inventory and frequent stockouts. By implementing a Kanban system, they managed to reduce their inventory by 30% while improving production speed by 20%. The visual boards allowed employees to track materials and progress quickly, improving communication and streamlining operations.
Case Study: Company B
Company B, a car parts manufacturer, faced challenges with long lead times and inconsistent production cycles. After implementing Kanban, they were able to better align their production schedule with demand. By using withdrawal and transportation Kanban cards, they streamlined inventory management and reduced delays by 40%. The Kanban system provided real-time visibility into production, enabling managers to make faster, more informed decisions.
Common Challenges and Solutions in Kanban Implementation
While Kanban offers many benefits, there are some challenges that organizations may encounter when implementing the system. Here are a few common obstacles and how to overcome them:
Resistance to Change
Employees may resist change, especially if they are accustomed to traditional manufacturing methods. To overcome this, provide training and communicate the benefits of Kanban clearly. Highlight how it will improve efficiency and reduce unnecessary work.
Maintaining Engagement and Adoption
For Kanban to be successful, it’s crucial that all team members stay engaged and consistently follow the system. Regular training sessions, ongoing communication, and strong leadership are key to ensuring long-term adoption.
Ineffective Board Design
An improperly designed Kanban board can lead to confusion and inefficiency. Ensure that your Kanban board is easy to understand and clearly reflects the production process. Tailor the board to your specific workflow and ensure that everyone involved knows how to use it effectively.
Maximize Your Manufacturing Efficiency with Meegle's Kanban Tools
Meegle offers powerful tools designed to help manufacturing businesses implement Kanban efficiently. With Meegle’s customizable Kanban boards, you can visualize workflows, set WIP limits, and track progress in real-time. Our platform helps streamline production processes, reduce delays, and improve team collaboration, making it easier to implement Kanban in any manufacturing environment.
Experience the Full Benefits of Kanban in Manufacturing!
The world’s #1 visualized project management tool
Powered by the next gen visual workflow engineRead More
Check All BlogsStart creating impactful work today
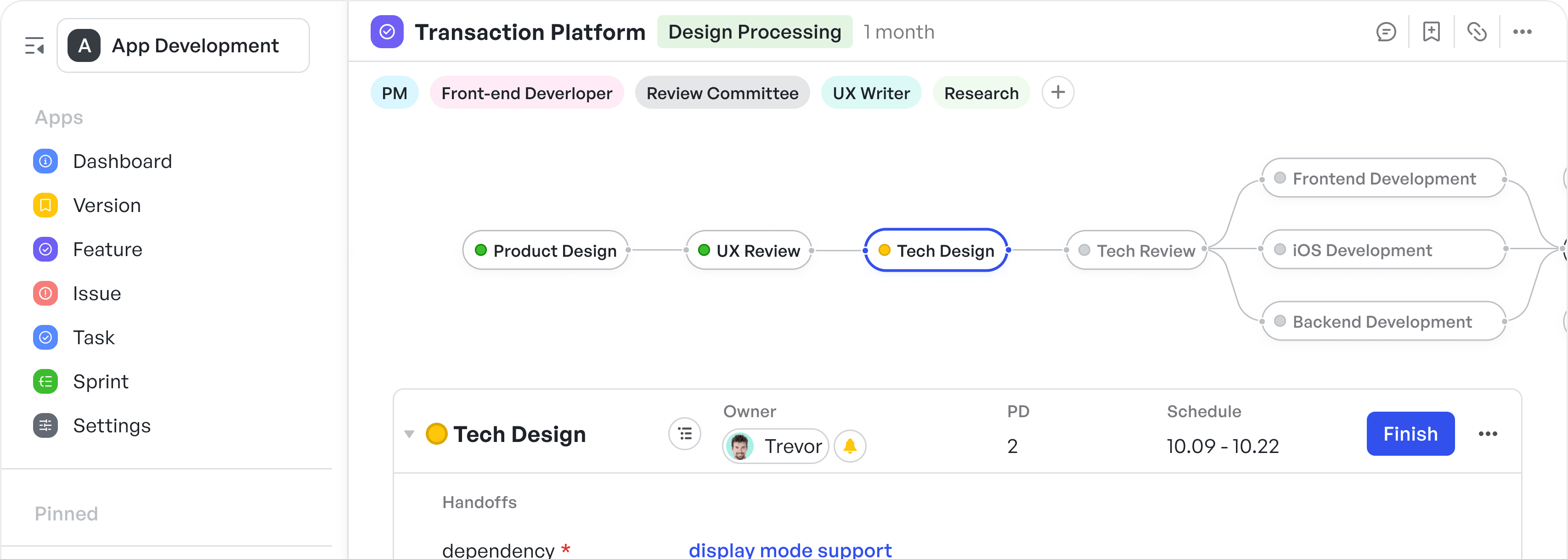