Advanced Manufacturing Technologies
Dive into our expertly crafted article exploring Advanced Manufacturing Technologies, where you'll get in-depth insights, practical applications, and industry best practices tailored for hardware enthusiasts and professionals.
Advanced Manufacturing Technologies (AMT) are redefining the landscape of modern manufacturing, providing an edge in efficiency and innovation that was unimaginable just a few decades ago. As industries face increasing pressure from global competition and rapidly evolving consumer demands, the adoption of AMT has become a pivotal strategy for staying ahead. These technologies encompass a range of cutting-edge tools and processes, from automation and robotics to the Internet of Things (IoT), each contributing to a more streamlined, productive, and adaptable manufacturing environment. For professionals and aspiring project managers, understanding and leveraging AMT is not just an option but a necessity for driving organizational success.
The importance of AMT cannot be overstated. By enhancing productivity and fostering innovation, these technologies enable manufacturers to maintain a competitive edge. For instance, according to the International Federation of Robotics, the deployment of industrial robots is expected to grow at an average annual rate of 14% between 2021 and 2025. This growth signifies a clear trend towards automation and the need for skilled professionals who can manage and optimize these systems. The ability to harness the power of AMT effectively can lead to significant cost reductions, improved product quality, and faster time-to-market, making it an indispensable tool for modern manufacturing.
This article is geared towards professionals and aspiring project managers in the manufacturing sector who are eager to harness the potential of AMT. It provides a comprehensive guide to understanding and implementing these technologies, offering insights into their applications, challenges, and future trends. Whether you're looking to enhance your current processes or embark on a transformative journey, this resource is designed to equip you with the knowledge and tools necessary to thrive in an ever-evolving industrial landscape. Dive in and discover how AMT can revolutionize your approach to manufacturing, ensuring you remain at the forefront of the industry.
Experience the next level of project management today!
Understanding advanced manufacturing technologies
Definition and Scope
Advanced Manufacturing Technologies encompass a broad array of innovative tools and processes that enhance manufacturing efficiency, quality, and flexibility. These technologies include automation, robotics, additive manufacturing (3D printing), and IoT systems, which collectively form the backbone of modern manufacturing strategies. By integrating these technologies, manufacturers can achieve unprecedented levels of precision and control, enabling the production of complex products with minimal waste. For instance, the integration of IoT in manufacturing allows for real-time monitoring and optimization of production processes, leading to significant reductions in downtime and maintenance costs.
The scope of AMT extends beyond individual technologies to encompass holistic manufacturing systems that are interconnected and adaptive. This integration enables manufacturers to respond swiftly to changes in market demand, customize products for specific customer needs, and maintain high standards of quality and efficiency. According to a report by Deloitte, smart factories—facilitated by AMT—could add as much as $500 billion to the global economy by 2025, highlighting the potential economic impact of these technologies.
Historical Context
The evolution of Advanced Manufacturing Technologies has been a gradual yet transformative journey. Initially, manufacturing was characterized by manual labor and rudimentary machinery, which limited production capabilities and consistency. The advent of the Industrial Revolution marked a significant shift, introducing mechanization and mass production techniques that revolutionized manufacturing processes. However, it wasn't until the late 20th century that the next major leap occurred with the introduction of computer-aided design (CAD) and computer-aided manufacturing (CAM), laying the groundwork for today's digital manufacturing landscape.
As technology continued to advance, the integration of robotics and automation in the 1980s and 1990s further transformed manufacturing capabilities. Today, with the advent of Industry 4.0, we are witnessing a new era where cyber-physical systems, IoT, and artificial intelligence converge to create highly automated and intelligent manufacturing environments. This evolution underscores the importance of staying abreast of technological advancements to remain competitive in the manufacturing sector.
Key Components
The core components of Advanced Manufacturing Technologies include a range of interconnected systems and innovations that collectively enhance manufacturing capabilities. Automation is a critical component, enabling the execution of repetitive tasks with precision and speed, reducing labor costs, and minimizing human error. Robotics further extends these capabilities, with collaborative robots (cobots) working alongside humans to optimize workflow and efficiency.
The Internet of Things (IoT) plays a pivotal role in modern manufacturing by facilitating the seamless exchange of data between machines, systems, and people. This connectivity allows for real-time monitoring and predictive maintenance, ensuring that production lines operate at optimal efficiency. Additionally, additive manufacturing or 3D printing enables the rapid prototyping and production of complex parts, reducing lead times and material waste.
These technologies are complemented by advanced analytics and artificial intelligence, which provide insights into production processes and enable data-driven decision-making. By leveraging these key components, manufacturers can create agile, responsive, and efficient production systems that meet the demands of today's fast-paced market.
Applications of advanced manufacturing technologies
Industry applications
Industry applications
The applications of Advanced Manufacturing Technologies span across a multitude of industries, each benefiting uniquely from these innovations. In the automotive industry, AMT enables the production of complex and lightweight vehicle components, enhancing fuel efficiency and performance. Robotics and automation streamline assembly lines, allowing for faster production cycles and improved quality control. For example, Tesla's Gigafactories utilize AMT extensively, resulting in reduced vehicle production times and increased output.
In the aerospace sector, precision is paramount. AMT facilitates the manufacturing of intricate parts with tight tolerances, ensuring safety and reliability in flight. 3D printing is particularly transformative in this industry, allowing for the production of lightweight components that reduce aircraft weight and fuel consumption. Companies like Boeing have adopted AMT to produce parts for their aircraft, achieving significant cost savings and efficiency gains.
The electronics industry also benefits from AMT, where automation and IoT play crucial roles in the assembly and testing of devices. These technologies enable the production of high-quality electronic components with minimal defects, contributing to the rapid advancement of consumer electronics. Samsung, for example, employs advanced automation in its semiconductor manufacturing processes, ensuring the production of cutting-edge chips that power modern devices.
Integration in manufacturing processes
Integration in manufacturing processes
Integrating Advanced Manufacturing Technologies into existing processes requires careful planning and execution. The key is to identify specific areas where AMT can add value, such as reducing bottlenecks, enhancing quality, or improving agility. For instance, manufacturers can begin by automating repetitive tasks that are prone to errors, allowing human workers to focus on more complex and value-added activities.
Successful integration also involves aligning AMT with organizational goals and ensuring that employees are trained to operate and manage new technologies. This may involve upskilling the workforce through training programs and workshops, fostering a culture of innovation and continuous improvement. Additionally, manufacturers must ensure that new technologies seamlessly integrate with existing systems to avoid disruptions and maximize efficiency.
Case studies
Case studies
One notable example of successful AMT implementation is General Electric's (GE) Brilliant Factory initiative. GE has invested heavily in digital manufacturing technologies, including IoT, AI, and robotics, to optimize its production processes. By leveraging real-time data and analytics, GE has achieved significant improvements in productivity, reducing manufacturing cycle times by up to 30% and increasing output by 20%.
Another case study is Siemens, which has embraced AMT to transform its manufacturing operations into smart factories. Through the integration of IoT and automation, Siemens has enhanced its production flexibility, allowing for the efficient customization of products to meet diverse customer demands. This has resulted in shorter lead times and improved customer satisfaction.
Related:
Joint Application DevelopmentClick here to read our expertly curated top picks!
Challenges and solutions
Implementation Challenges
While the benefits of Advanced Manufacturing Technologies are clear, their implementation is not without challenges. One of the most significant barriers is the cost of deploying these technologies, which can be substantial, especially for small to medium-sized enterprises (SMEs). The complexity of integrating advanced systems into existing processes can also pose difficulties, requiring significant time and expertise to ensure seamless operation.
Another challenge is the skill gap in the workforce. As AMT relies heavily on digital tools and processes, there is a growing demand for skilled professionals who can operate and maintain these systems. A report from the World Economic Forum highlights that by 2025, over half of all employees will require significant reskilling as a result of automation and technological advancements.
Strategic Solutions
To overcome these challenges, organizations can adopt a strategic and phased approach to implementing AMT. One effective strategy is to start with pilot projects that focus on specific areas of the manufacturing process. This allows companies to test the feasibility and impact of new technologies on a smaller scale before committing to full-scale deployment.
Investing in employee training and development is also crucial to bridging the skill gap. By providing continuous education and training opportunities, companies can equip their workforce with the necessary skills to leverage AMT effectively. Partnerships with educational institutions and industry experts can further enhance training programs and ensure they are aligned with the latest technological advancements.
Additionally, budget management plays a critical role in overcoming cost barriers. Organizations can explore various funding options, such as government grants and incentives, to support their AMT initiatives. By carefully managing budgets and prioritizing investments, companies can ensure a sustainable and successful implementation of advanced manufacturing technologies.
Risk Management
Risk assessment and mitigation are essential components of any AMT implementation strategy. Companies must conduct thorough risk assessments to identify potential challenges and develop strategies to address them. This may involve evaluating the impact of new technologies on existing processes, assessing cybersecurity risks, and ensuring compliance with regulatory requirements.
Developing a comprehensive risk management plan that includes contingency measures and regular monitoring is crucial to minimizing potential disruptions. Regular audits and reviews can help identify emerging risks and ensure that mitigation strategies remain effective over time. By proactively managing risks, organizations can ensure a smooth and successful transition to advanced manufacturing technologies.
Best practices
Maximizing Benefits
To maximize the benefits of Advanced Manufacturing Technologies, manufacturers should adopt a holistic approach that encompasses planning, execution, and maintenance. A well-defined implementation plan is essential, outlining clear objectives, timelines, and resource allocations. This plan should be aligned with organizational goals and involve collaboration with key stakeholders to ensure a shared understanding of the expected outcomes.
During execution, companies should focus on optimizing processes by leveraging the capabilities of AMT. This may involve reengineering workflows, automating repetitive tasks, and integrating IoT for real-time monitoring and control. By continuously monitoring performance and identifying areas for improvement, manufacturers can ensure that their AMT investments deliver maximum value.
Expert Tips
Industry experts emphasize the importance of fostering a culture of innovation and continuous learning. This involves encouraging employees to embrace new technologies and providing opportunities for skill development. Collaboration with technology partners and industry peers can also provide valuable insights and best practices, ensuring that companies stay abreast of the latest advancements in AMT.
Additionally, experts recommend adopting a flexible approach to AMT implementation, allowing for adjustments and iterations based on feedback and performance data. This agile methodology ensures that companies can respond to changing market demands and technological advancements effectively.
Continuous Improvement
In a rapidly evolving technological landscape, continuous improvement is crucial for maintaining a competitive edge. Manufacturers should regularly evaluate their AMT strategies and processes, seeking opportunities for optimization and innovation. This may involve exploring new technologies, refining existing processes, and investing in research and development.
By fostering a culture of continuous improvement and innovation, companies can ensure that they remain at the forefront of the industry, driving operational excellence and delivering superior value to customers.
Click here to read our expertly curated top picks!
Software and tools
Overview of Tools
A comprehensive suite of software and tools is available to facilitate the implementation of Advanced Manufacturing Technologies. These tools include manufacturing execution systems (MES), computer-aided design (CAD) software, enterprise resource planning (ERP) systems, and IoT platforms. Each tool serves a specific function, enabling manufacturers to streamline operations, enhance collaboration, and optimize performance.
MES, for instance, provides real-time visibility into production processes, allowing manufacturers to monitor and control operations with precision. CAD software enables the design and simulation of complex products, reducing design iterations and accelerating time-to-market. ERP systems integrate various business functions, ensuring seamless coordination and data sharing across the organization.
Tool Benefits
The benefits of these tools are manifold, contributing to enhanced efficiency, improved collaboration, and data-driven decision-making. By providing real-time insights into production processes, MES enables manufacturers to identify bottlenecks and optimize workflows, resulting in increased productivity and reduced lead times. CAD software enhances design accuracy and innovation, allowing for the rapid prototyping and testing of new products.
IoT platforms facilitate the seamless exchange of data between machines and systems, enabling predictive maintenance and reducing downtime. ERP systems streamline business operations, ensuring that resources are allocated efficiently and that production schedules are aligned with customer demands.
Selecting the Right Software
Selecting the most appropriate software is a critical decision that depends on specific manufacturing needs and goals. Manufacturers should conduct a thorough needs assessment to identify the key functionalities and features required to support their operations. This may involve evaluating the scalability, compatibility, and integration capabilities of various software options.
Collaborating with technology partners and industry experts can provide valuable insights and recommendations, ensuring that manufacturers select software that aligns with their strategic objectives. Additionally, companies should consider the total cost of ownership, including implementation, training, and maintenance costs, to ensure a sustainable investment.
Future outlook
Emerging Trends
The future of Advanced Manufacturing Technologies is characterized by rapid innovation and the emergence of new trends that promise to revolutionize the industry. One such trend is the integration of artificial intelligence (AI) and machine learning, which enables predictive analytics and autonomous decision-making. AI-powered systems can analyze vast amounts of data, identifying patterns and optimizing production processes with unparalleled accuracy.
Another emerging trend is the development of smart factories that leverage IoT and cyber-physical systems to create highly automated and interconnected production environments. These factories enable real-time collaboration between machines and humans, resulting in increased flexibility and efficiency. Furthermore, the emphasis on sustainability is driving the adoption of green manufacturing practices, where AMT plays a crucial role in reducing energy consumption and minimizing environmental impact.
Staying Competitive
To remain competitive in the future, manufacturers must adopt a proactive approach to technology adoption and innovation. This involves staying abreast of emerging trends and investing in the latest AMT solutions that align with organizational goals and market demands. Companies should also focus on building a culture of innovation and agility, encouraging employees to embrace new technologies and adapt to changing circumstances.
Collaboration with industry partners, research institutions, and technology providers can provide valuable insights and expertise, ensuring that manufacturers remain at the forefront of technological advancements. By fostering a collaborative ecosystem, companies can leverage collective knowledge and resources to drive innovation and achieve a competitive advantage.
Innovation and Adaptation
Innovation and adaptation are critical drivers of success in a rapidly evolving manufacturing landscape. Manufacturers must continuously evaluate their processes and technologies, seeking opportunities for optimization and improvement. This may involve exploring new materials, refining production techniques, and investing in research and development to drive product innovation.
By embracing a mindset of continuous learning and adaptation, manufacturers can ensure that they remain agile and responsive to changing market demands. This proactive approach enables companies to capitalize on emerging opportunities, delivering superior value to customers and sustaining long-term growth.
Click here to read our expertly curated top picks!
Detailed examples
Example 1: automotive industry
Example 1: automotive industry
The automotive industry has been at the forefront of implementing Advanced Manufacturing Technologies, particularly in the areas of robotics and automation. In assembly lines, robotics play a crucial role in assembling vehicles with precision and speed, reducing production cycle times and improving quality control. For instance, Tesla's Gigafactories utilize advanced robots to perform complex tasks, such as welding and painting, ensuring consistent quality and efficiency.
Quality control is another area where AMT has made significant advancements. Automated inspection systems utilize machine vision and AI algorithms to identify defects and ensure that vehicles meet stringent quality standards. By leveraging these technologies, automotive manufacturers can enhance product reliability and reduce the risk of recalls, resulting in increased customer satisfaction and brand reputation.
Example 2: aerospace industry
Example 2: aerospace industry
In the aerospace industry, precision engineering and material innovation are critical to ensuring safety and performance. Advanced Manufacturing Technologies have revolutionized aerospace manufacturing by enabling the production of lightweight and high-strength components. 3D printing, for example, allows for the creation of complex geometries that were previously impossible to achieve with traditional manufacturing methods.
Companies like Boeing have embraced AMT to produce aircraft parts with reduced weight and improved aerodynamics, resulting in increased fuel efficiency and reduced emissions. By leveraging advanced materials and manufacturing techniques, aerospace manufacturers can meet the stringent requirements of the industry while driving innovation and cost savings.
Example 3: electronics manufacturing
Example 3: electronics manufacturing
The electronics manufacturing industry has witnessed significant advancements with the implementation of Advanced Manufacturing Technologies. Automation plays a crucial role in the assembly and testing of electronic devices, ensuring high-quality production with minimal defects. Automated soldering and testing processes, for instance, enhance the reliability and performance of printed circuit boards (PCBs).
IoT integration further enhances electronics manufacturing by enabling real-time monitoring and control of production processes. Companies like Samsung utilize advanced automation and IoT to streamline their semiconductor manufacturing operations, ensuring the production of cutting-edge chips that power modern devices. By leveraging these technologies, electronics manufacturers can meet the growing demand for high-performance and reliable products.
Click here to read our expertly curated top picks!
Do's and don'ts of advanced manufacturing technologies
Do's | Don'ts |
---|---|
Conduct thorough research before implementation | Rush into technology adoption without a plan |
Invest in employee training and development | Neglect the importance of ongoing education |
Start with pilot projects to test feasibility | Implement full-scale projects without testing |
Continuously monitor and evaluate performance | Assume initial success guarantees long-term gains |
Collaborate with technology experts and stakeholders | Isolate technology decisions from key stakeholders |
Click here to read our expertly curated top picks!
Conclusion
In conclusion, Advanced Manufacturing Technologies are transforming the manufacturing landscape, offering unprecedented efficiency and innovation. By embracing these technologies, manufacturers can enhance productivity, reduce costs, and maintain a competitive edge in today's fast-paced market. The successful implementation of AMT requires a strategic approach, including needs assessment, technology selection, pilot testing, and continuous optimization. By following best practices and leveraging expert insights, companies can maximize the benefits of AMT and drive operational excellence.
As the manufacturing industry continues to evolve, staying ahead of emerging trends and innovations is crucial. By adopting a proactive and adaptive approach, manufacturers can ensure they remain at the forefront of technological advancements, delivering superior value to customers and sustaining long-term growth. The call to action is clear: embrace the transformative power of AMT and revolutionize your manufacturing processes for a more efficient and competitive future.
Further resources
To continue your learning journey in Advanced Manufacturing Technologies, consider exploring the following resources:
- Books: "The Fourth Industrial Revolution" by Klaus Schwab offers insights into the impact of AMT on global industries.
- Online Courses: Platforms like Coursera and edX offer courses on digital manufacturing, IoT, and AI integration.
- Professional Organizations: Joining bodies such as the Association for Manufacturing Technology (AMT) provides access to industry insights, networking opportunities, and educational resources.
- Industry Conferences: Attending events like the Smart Factory Expo and Industrial Internet of Things (IIoT) World Congress offers valuable insights into the latest trends and innovations in AMT.
By leveraging these resources, you can enhance your knowledge and skills, ensuring you remain informed and competitive in the rapidly evolving world of advanced manufacturing technologies.
Experience the next level of project management today!
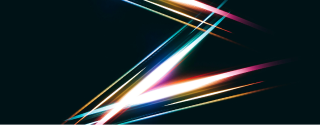
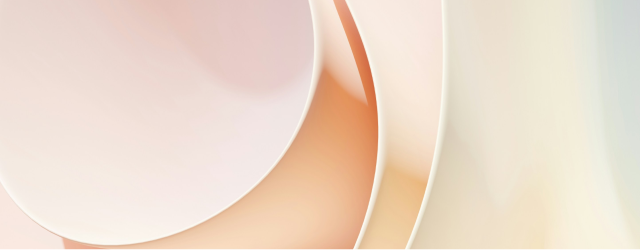
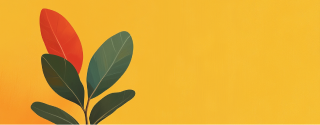
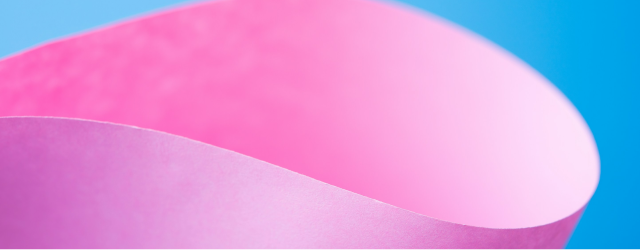
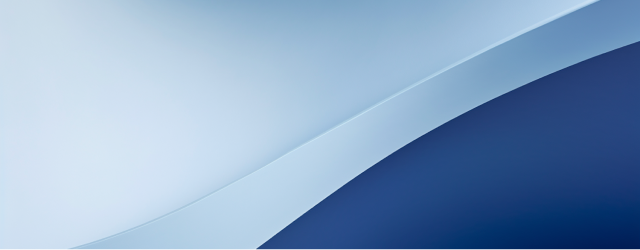
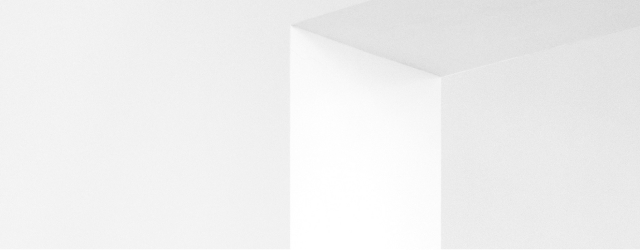
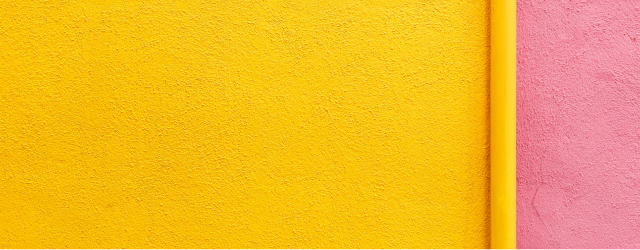