Surface Finishing Processes
Dive into our expertly crafted article exploring Surface Finishing Processes, where you'll get in-depth insights, practical applications, and industry best practices tailored for hardware enthusiasts and professionals.
In the realm of modern manufacturing, surface finishing processes stand as a pivotal axis upon which product quality and durability pivot. These processes, often the unsung heroes behind the polished exterior of a product, play a critical role in determining not only the aesthetic appeal but also the functional longevity of manufacturing outputs. From enhancing corrosion resistance to providing the final cosmetic touches, surface finishing is integral to optimizing product performance across a broad spectrum of industries. As we delve into this comprehensive guide, both seasoned professionals and aspiring project managers will uncover the nuanced intricacies of these processes and how they can be harnessed to drive technological and operational advancements within their organizations.
The significance of mastering surface finishing processes cannot be understated. For instance, in the automotive industry, these processes are essential in improving the lifespan and appearance of vehicle components. In aerospace, they ensure parts withstand extreme conditions, thereby enhancing safety and reliability. This article is structured to equip you with a deep understanding of the different facets of surface finishing. We will explore its historical evolution, current applications, and the challenges it presents, accompanied by strategic solutions. Additionally, we will provide insights into best practices and future trends, ensuring you stay ahead in an ever-evolving industry landscape. By the end, you will have a well-rounded perspective, poised to implement these processes to boost your manufacturing efficiency and product excellence. Join us on this journey to mastering the art and science of surface finishing, where innovation meets practical application.
Experience the next level of project management today!
Understanding surface finishing processes
Defining the Core Principles
At its core, surface finishing processes involve a series of operations designed to alter the surface of a manufactured part to achieve desired properties, such as smoothness, gloss, or resistance to wear and corrosion. These processes can be classified into mechanical, chemical, and electrochemical treatments. Mechanical finishing includes techniques like grinding and polishing, which physically remove material to improve surface texture. Chemical finishing, such as anodizing, uses chemical reactions to modify the surface properties, often for enhanced corrosion resistance. Electrochemical treatments, like electroplating, deposit a metal layer onto a surface to provide a protective or decorative coating.
Historical Context and Technological Evolution
Surface finishing has a rich history, evolving significantly with technological advancements. Initially, these processes were rudimentary, relying heavily on manual labor and simple tools. The Industrial Revolution marked a turning point with the introduction of machinery that automated many finishing techniques, thus improving consistency and efficiency. In the 20th century, the advent of electrochemistry revolutionized surface finishing, enabling precise control over coating thickness and composition. Today, with advancements in digital technology and materials science, surface finishing processes have become highly sophisticated, employing computer-controlled machinery and eco-friendly practices to meet modern manufacturing demands.
Achieving Specific Product Finishes
The importance of surface finishing lies in its ability to achieve specific product finishes and textures that meet both functional and aesthetic requirements. For instance, a medical device may require a biocompatible coating to ensure patient safety, while a consumer electronic device might need a smooth, glossy finish for visual appeal. Surface finishing processes are meticulously selected based on the type of material, desired properties, and end-use conditions. By understanding these principles and historical context, manufacturers can leverage surface finishing to produce high-quality products that stand the test of time.
Applications of surface finishing processes
Insights into industry applications
Insights into industry applications
Surface finishing processes find critical applications across various industries, each with unique requirements and benefits. In the automotive industry, surface finishing is essential for components that endure harsh environmental conditions. Processes like electroplating and painting offer corrosion protection and enhance aesthetic appeal. In the aerospace sector, anodizing and shot peening are widely used to increase wear resistance and fatigue life of components exposed to extreme pressures and temperatures. Meanwhile, the electronics industry relies on surface finishing for both functional and decorative purposes. Techniques like powder coating ensure durability and provide an appealing finish to consumer electronic devices.
Case studies in surface finishing
Case studies in surface finishing
To illustrate the tangible impact of surface finishing, consider the case of a leading car manufacturer that implemented electroplating for its exhaust systems. By utilizing this process, the company was able to extend the lifespan of its products by over 30%, while simultaneously reducing warranty claims related to corrosion. Another notable example is in aerospace, where a major aircraft producer adopted advanced anodizing techniques to enhance the durability of its wing components, resulting in a significant reduction in maintenance costs and improvement in safety records.
Real-world benefits and improvements
Real-world benefits and improvements
The application of surface finishing processes yields substantial improvements in manufacturing outcomes. These benefits include:
Related:
Agile Unified Process (AUP)Click here to read our expertly curated top picks!
Challenges and solutions in surface finishing
Overcoming Common Challenges
While surface finishing processes offer numerous benefits, they also present a set of challenges that manufacturers must overcome. One common challenge is adhering to environmental regulations, as many traditional finishing processes involve hazardous chemicals and generate waste. This necessitates the implementation of sustainable practices and the adoption of eco-friendly materials and technologies. Another challenge is cost management, where the complexity and variety of finishing techniques can lead to increased production costs. Manufacturers must balance achieving desired surface qualities with maintaining cost-effectiveness. Technical limitations, such as achieving uniform finishes on complex geometries, also pose significant challenges.
Strategic Solutions and Methodologies
To address these challenges, manufacturers can implement strategic solutions and methodologies. For environmental concerns, investing in technology such as closed-loop systems can significantly reduce waste and emissions. Process optimization, through techniques like lean manufacturing, can streamline operations and reduce costs. Additionally, innovation in materials science can lead to the development of advanced coatings that are both effective and environmentally friendly. By adopting a comprehensive approach to problem-solving, manufacturers can successfully navigate the complexities of surface finishing processes.
Maintaining Quality Control and Compliance
Quality control is paramount in surface finishing, as inconsistencies can lead to product failures and damage to brand reputation. Implementing robust quality assurance protocols ensures that each component meets the specified standards. This includes regular inspections, testing, and process audits. Compliance with industry regulations is equally important and requires staying updated with evolving standards. Manufacturers can achieve this by fostering a culture of continuous improvement, investing in staff training, and leveraging technology to enhance monitoring and reporting capabilities.
By understanding and addressing these challenges with strategic solutions, manufacturers can enhance their surface finishing processes, ensuring high-quality outcomes that meet both regulatory and customer expectations.
Best practices for surface finishing processes
Industry-Recommended Practices
To optimize surface finishing processes, manufacturers should adhere to industry-recommended best practices. These practices not only improve process efficiency but also enhance product quality and consistency. One such practice is the implementation of comprehensive process documentation. This involves maintaining detailed records of process parameters, materials used, and quality control measures, which facilitates troubleshooting and continuous improvement efforts. Additionally, adopting a collaborative approach where cross-functional teams work together can lead to innovative solutions and process enhancements.
Expert Tips and Tricks
Experts in the field offer valuable insights for enhancing surface finishing processes. For instance, regularly calibrating equipment and tools ensures precision and consistency in finishes. Utilizing advanced simulation software can also aid in predicting outcomes and optimizing process parameters. Another expert recommendation is to invest in regular training and development programs for staff. This ensures that the workforce is knowledgeable about the latest techniques and technologies, leading to improved process execution and innovation.
Guidelines for Continuous Improvement
Continuous improvement is a cornerstone of successful surface finishing processes. Establishing a feedback loop where process outcomes are regularly reviewed and analyzed can drive incremental improvements. This can be achieved through techniques such as Six Sigma, which focuses on reducing variability and defects. Encouraging a culture of innovation, where employees are empowered to propose new ideas and solutions, can also lead to significant advancements. By embracing these best practices, manufacturers can sustain a competitive edge and consistently deliver high-quality products.
Click here to read our expertly curated top picks!
Software and tools for enhanced surface finishing
Overview of Cutting-Edge Tools
The landscape of surface finishing processes has been revolutionized by the advent of cutting-edge software and tools that enhance accuracy, efficiency, and sustainability. Computer-Aided Design (CAD) software enables precise modeling of surface finish requirements, allowing manufacturers to simulate and optimize processes before actual implementation. Additionally, tools like digital microscopes and profilometers provide detailed surface analyses, ensuring quality control and consistency. These technologies not only streamline operations but also reduce waste and improve yield.
Benefits of Advanced Software
Each software tool offers distinct benefits that contribute to the enhancement of surface finishing processes. For example, the use of CAD software allows for the detailed planning and visualization of complex geometries, reducing the risk of errors during production. Digital microscopes provide high-resolution imagery for surface inspection, enabling the detection of defects that might otherwise go unnoticed. These technologies also facilitate data-driven decision-making, leading to more informed process adjustments and optimizations.
Tips for Selecting the Right Technology
Selecting the right technology for surface finishing requires careful consideration of specific manufacturing needs and goals. Manufacturers should evaluate the compatibility of software tools with existing systems and processes, ensuring seamless integration and operation. Additionally, prioritizing user-friendly interfaces and robust customer support can enhance the adoption and effectiveness of these technologies. Assessing the scalability of tools is also crucial, allowing for future expansion and adaptation as manufacturing requirements evolve.
By leveraging the right software and tools, manufacturers can significantly enhance their surface finishing processes, achieving greater precision, efficiency, and innovation.
Future outlook on surface finishing processes
Emerging Trends and Innovations
The future of surface finishing processes is poised for exciting advancements, driven by emerging trends and innovations that promise to reshape the manufacturing landscape. One significant trend is the increasing adoption of automation and robotics, which streamline finishing operations and improve precision. Additionally, the development of nanotechnology is opening new possibilities for surface modification at an atomic level, leading to enhanced material properties and performance. Sustainable practices are also gaining traction, with eco-friendly materials and processes becoming more prevalent as manufacturers seek to reduce environmental impact.
The Role of Technology and Automation
Technology and automation are playing pivotal roles in shaping the future of surface finishing. Automated systems equipped with artificial intelligence (AI) and machine learning algorithms can optimize process parameters in real-time, leading to improved efficiency and reduced waste. Advanced robotics are being employed to handle complex tasks with precision and consistency, minimizing human error and enhancing safety. These technological advancements are not only enhancing current processes but also paving the way for innovative solutions that further elevate manufacturing capabilities.
Strategies for Staying Competitive
To remain competitive in this evolving landscape, manufacturers must adopt proactive strategies that embrace these emerging trends. This includes investing in research and development to stay at the forefront of technological advancements. Collaborating with industry partners and academic institutions can also foster innovation and knowledge sharing. Additionally, manufacturers should focus on building a skilled workforce that is adept at leveraging new technologies and methodologies. By staying agile and continuously adapting to industry changes, manufacturers can maintain a competitive edge and drive future success.
Click here to read our expertly curated top picks!
Examples of surface finishing processes
Example 1: electroplating in the automotive industry
Example 1: electroplating in the automotive industry
Electroplating is a widely used surface finishing process in the automotive industry, known for its ability to enhance corrosion resistance and improve the aesthetic appeal of vehicle components. This process involves the application of a metal coating onto a substrate through an electrochemical reaction. For instance, a major automotive manufacturer implemented electroplating for its exhaust systems, resulting in a significant increase in durability and a reduction in corrosion-related warranty claims. By providing a protective layer, electroplating helps extend the lifespan of components, ensuring they withstand harsh environmental conditions.
Example 2: anodizing in aerospace manufacturing
Example 2: anodizing in aerospace manufacturing
Anodizing is a critical surface finishing process in aerospace manufacturing, where it plays a vital role in enhancing the wear resistance and surface hardness of components exposed to extreme environments. This electrochemical process involves the conversion of the metal surface into a durable and corrosion-resistant oxide layer. A leading aircraft manufacturer adopted advanced anodizing techniques for its wing components, resulting in improved safety records and reduced maintenance costs. By increasing the surface hardness and resistance, anodizing ensures that aerospace parts meet the stringent demands of the industry.
Example 3: powder coating in consumer electronics
Example 3: powder coating in consumer electronics
Powder coating is a popular surface finishing process in the consumer electronics industry, offering a durable and protective finish for electronic devices. This process involves the application of a dry powder that is cured under heat to form a solid, durable coating. A renowned electronics company utilized powder coating for its range of consumer devices, achieving a uniform and scratch-resistant finish that enhances both the durability and visual appeal of its products. Powder coating not only provides protection but also offers a wide range of colors and textures, allowing manufacturers to create distinctive and attractive electronic products.
Click here to read our expertly curated top picks!
Do's and don'ts of surface finishing processes
Do's | Don'ts |
---|---|
Regularly assess process efficiency and outcomes. | Neglect routine maintenance and quality checks. |
Invest in staff training and development. | Overlook the environmental impact of processes. |
Stay updated with technological advancements. | Ignore customer feedback on product finishes. |
Related:
Gaming API IntegrationClick here to read our expertly curated top picks!
Conclusion
Mastering the intricate art of surface finishing processes is crucial for enhancing manufacturing efficiency and product quality. Throughout this comprehensive guide, we have explored the various facets of surface finishing, from understanding its core principles and applications to overcoming challenges and implementing best practices. By understanding the significance of these processes and leveraging cutting-edge tools and technologies, manufacturers can achieve superior outcomes that meet the evolving demands of the industry.
As advancements in technology and automation continue to shape the future of surface finishing, it is essential for project managers and manufacturing professionals to stay informed and proactive. Implementing these strategies not only improves product durability and aesthetic appeal but also enhances cost efficiency and regulatory compliance. By fostering a culture of continuous improvement and innovation, manufacturers can maintain a competitive edge and drive future success.
We encourage project managers to leverage the insights and strategies shared in this guide to implement effective surface finishing processes and elevate their manufacturing capabilities. With a commitment to excellence and adaptability, the possibilities for improvement and advancement in surface finishing are boundless.
Further resources
- Explore additional readings and research articles on surface finishing through platforms like ScienceDirect and the Journal of Manufacturing Processes.
- Consider enrolling in courses and training programs offered by institutions such as the Manufacturing Institute and Coursera for further learning and skill enhancement.
- Join professional bodies like the Society of Manufacturing Engineers and online forums such as LinkedIn groups to connect with experts and peers for networking and advice.
Experience the next level of project management today!
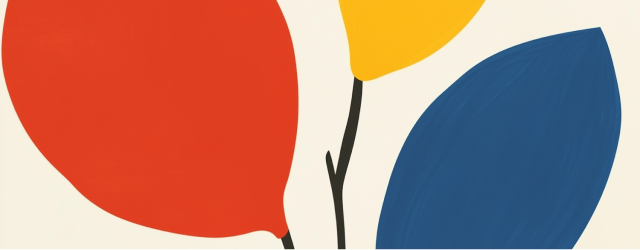
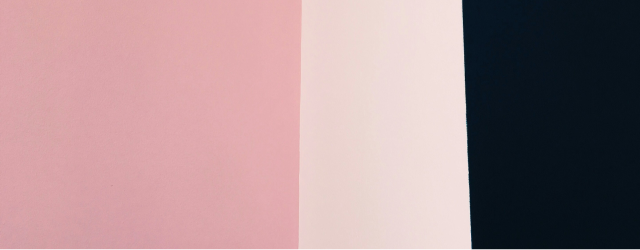
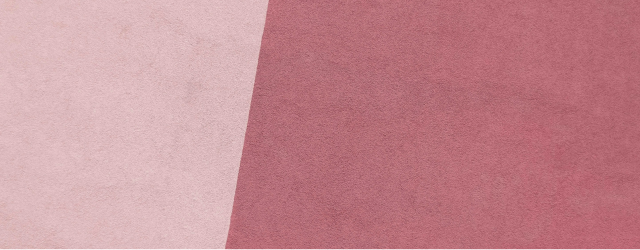
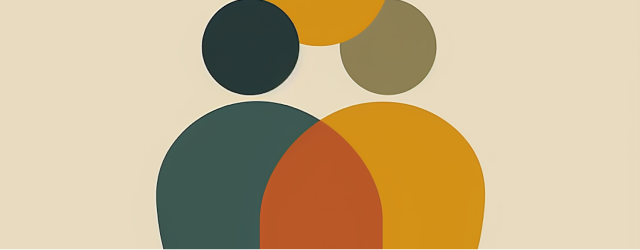
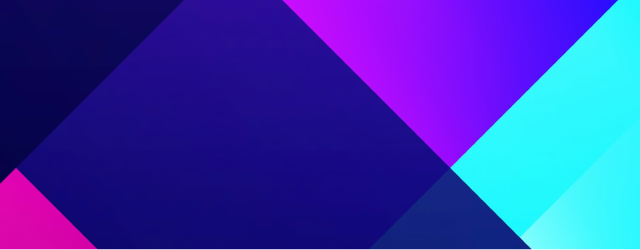
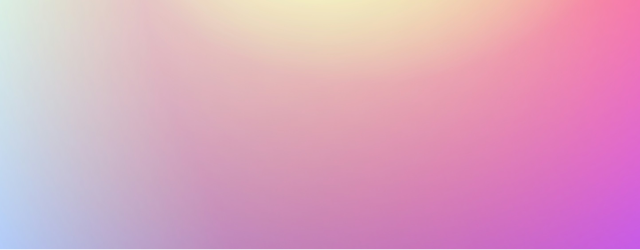
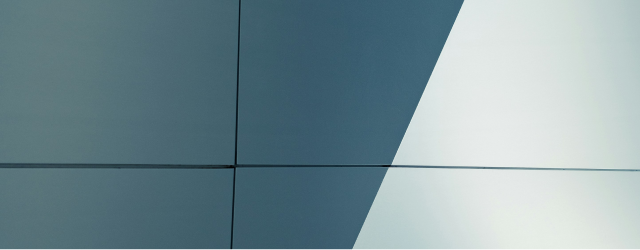
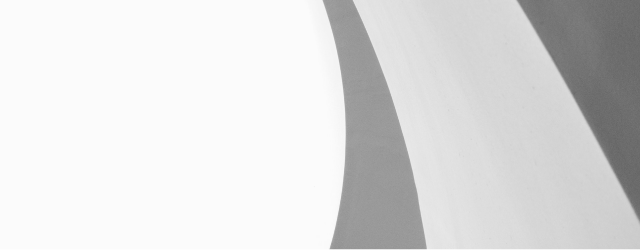