Predictive Maintenance In Manufacturing
Dive into our expertly crafted article exploring Predictive Maintenance in Manufacturing, where you'll get in-depth insights, practical applications, and industry best practices tailored for hardware enthusiasts and professionals.
Predictive maintenance is a significant advancement in manufacturing, enabling operators to foresee potential machinery breakdowns and act proactively to prevent them. Leveraging technologies like the Internet of Things (IoT), data analytics, and machine learning, predictive maintenance can drastically reduce unexpected downtime, boost operational efficiency, and increase cost savings. This guide explores the concept, practical applications, challenges, best practices, tools, future trends, and a comprehensive step-by-step guide for implementing predictive maintenance in manufacturing settings.
Experience the next level of project management today!
Understanding predictive maintenance in manufacturing
Definition and Concept
Predictive maintenance is a strategy that utilizes data analysis and predictive modeling to anticipate when an equipment failure might occur. This proactive approach enables manufacturers to schedule maintenance activities optimally and prevent unexpected equipment failures and related downtime, critical for maintaining a competitive edge in today's fast-paced manufacturing landscape.
Evolution of Predictive Maintenance in Manufacturing
Over the years, predictive maintenance has evolved from a novel idea to a strategic imperative. Early solutions relied on basic sensors and manual data analysis. Today, advancements in IoT, cloud computing, artificial intelligence, and machine learning have revolutionized predictive maintenance, enabling manufacturers to leverage vast amounts of data and sophisticated algorithms to predict machinery failure with unprecedented accuracy.
Practical applications of predictive maintenance in manufacturing
Scenario 1: automotive manufacturing
Scenario 1: automotive manufacturing
In automotive manufacturing, predictive maintenance can monitor critical parameters like temperature, vibration, and noise levels in real-time to identify anomalies that might indicate an impending equipment failure. For example, a sudden increase in machine vibration could signal a potential issue with a bearing, allowing preventive action to be taken before the problem escalates.
Scenario 2: electronics manufacturing
Scenario 2: electronics manufacturing
In electronics manufacturing, predictive maintenance can help prevent costly defects and improve product quality. By predicting potential issues in the production process, manufacturers can take corrective action in advance, preventing defects that would lead to product recalls or customer dissatisfaction.
Scenario 3: food and beverage manufacturing
Scenario 3: food and beverage manufacturing
In the food and beverage industry, predictive maintenance can help ensure safety and compliance. Sensors can monitor temperatures, pressures, and flow rates to ensure they stay within safe and legal limits, alerting operators if they start to deviate.
Related:
ITILClick here to read our expertly curated top picks!
Challenges and solutions in predictive maintenance in manufacturing
Major Challenges
Implementing predictive maintenance can present a number of challenges, including the need for significant upfront investment, the complexity of integrating new technologies with existing systems, and the need for skilled personnel to interpret and act on the information provided by predictive maintenance systems.
Practical Solutions
To overcome these challenges, manufacturers can start by identifying a specific area or piece of equipment where predictive maintenance could have a high impact. They can also invest in training to equip their staff with the necessary skills, and seek advice from experts or vendors to ensure a smooth integration of the new technologies.
Best practices for predictive maintenance in manufacturing
Implementing predictive maintenance is not a one-size-fits-all process. Each manufacturer will have unique needs and constraints. However, some recommended practices include starting small with a pilot project, investing in training and upskilling, and regularly reviewing and refining the predictive maintenance strategy based on feedback and results.
Click here to read our expertly curated top picks!
Tools and software for predictive maintenance in manufacturing
Overview of Tools and Software
A variety of tools and software are available to support predictive maintenance initiatives. These range from sensors and data loggers to collect data, to cloud-based platforms and machine learning algorithms to analyze the data and generate predictive insights.
Choosing the Right Software
Selecting the right tools and software for predictive maintenance can be a complex task. Manufacturers should consider factors such as ease of integration with existing systems, scalability, cost, and the level of support offered by the vendor.
Future trends in predictive maintenance in manufacturing
Predictive maintenance is set to play an increasingly crucial role in manufacturing. Future trends could include more sophisticated algorithms for predicting equipment failure, integration with other Industry 4.0 technologies like digital twins and augmented reality, and a growing emphasis on predictive maintenance as part of a broader shift towards smart manufacturing.
Related:
Agile Unified Process (AUP)Click here to read our expertly curated top picks!
Step-by-step guide to implementing predictive maintenance
Implementing predictive maintenance typically involves steps like defining the scope and objectives of the initiative, selecting the right tools and software, integrating the new technologies with existing systems, training staff, and continuously monitoring and refining the strategy.
Do’s and don’ts in predictive maintenance in manufacturing
Adopting a strategic approach to predictive maintenance can maximize its benefits. Some key do's and don'ts include:
- Do start with a pilot project and scale up gradually
- Don't overlook the importance of training and upskilling
- Do regularly review and refine the predictive maintenance strategy
- Don't expect immediate results - predictive maintenance is a long-term strategy
Related:
ITILClick here to read our expertly curated top picks!
Conclusion
Predictive maintenance is a powerful tool for improving operational efficiency and reducing costs in manufacturing. By understanding its principles and best practices, and by leveraging the right tools and software, manufacturers can stay ahead of the competition and ensure the longevity and reliability of their equipment.
Click here to read our expertly curated top picks!
Further resources
For more information on predictive maintenance, consider checking out the following resources:
- Society for Maintenance & Reliability Professionals (SMRP)
- Coursera and Udemy online courses
- Vendor resources and webinars
- Industry conferences and networking events.
Experience the next level of project management today!
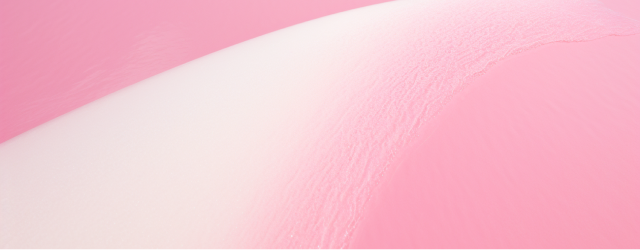
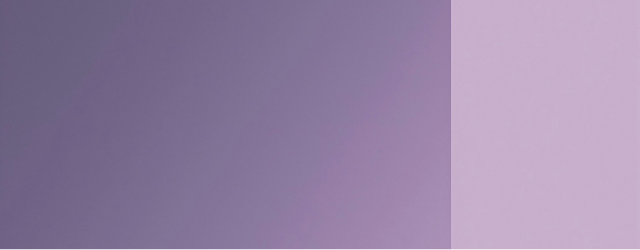
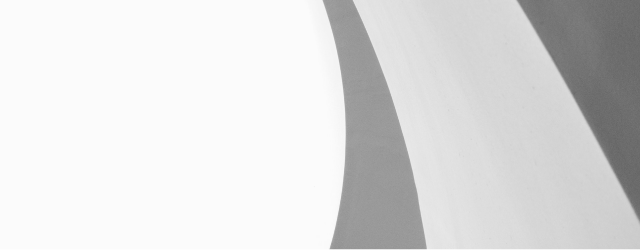
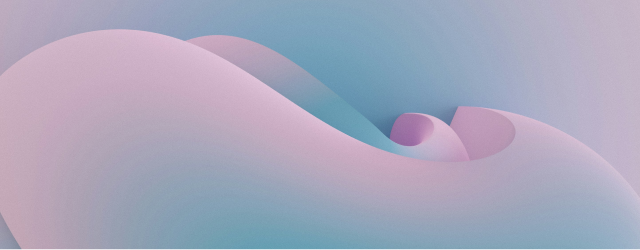
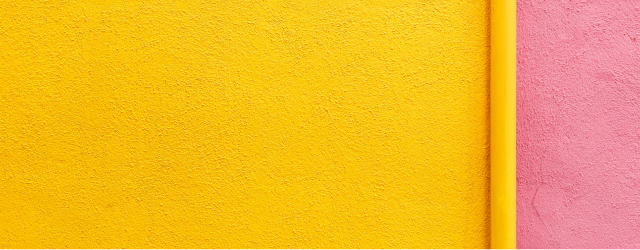
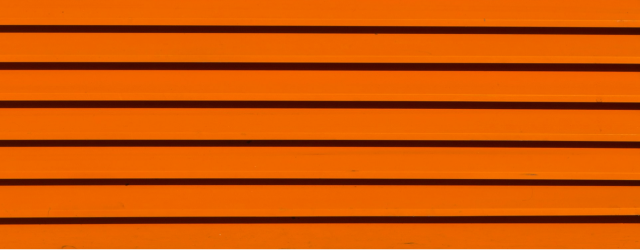
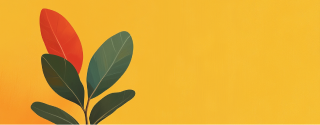
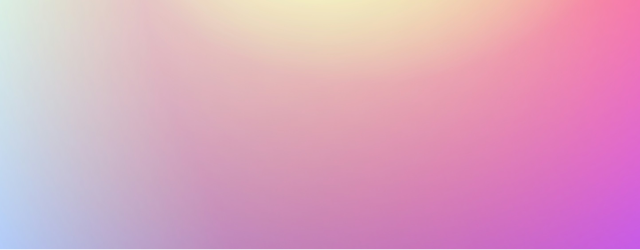