Automotive Hardware Production
Dive into our expertly crafted article exploring Automotive Hardware Production, where you'll get in-depth insights, practical applications, and industry best practices tailored for hardware enthusiasts and professionals.
Automotive hardware production stands as a cornerstone in modern manufacturing, shaping the way vehicles are produced and influencing global supply chains. With the automotive industry valued at over $2 trillion, the production of automotive hardware is significant for car manufacturers and the myriad of sectors that support this industry, such as electronics, materials, and logistics. The purpose of this article is to delve into the complexities and nuances of automotive hardware production, providing a comprehensive guide for professionals and aspiring project managers in this field. This article will explore the myriad challenges and opportunities within the industry, offering insights into efficient production techniques, technological advancements, and strategic solutions for common hurdles.
The challenges within automotive hardware production are numerous, ranging from supply chain disruptions to the need for stringent quality controls. However, these challenges come with equal opportunities for innovation and improvement. As technology evolves, so do the methods of production, offering new tools and strategies to enhance efficiency and effectiveness. The target audience for this article includes seasoned professionals looking to refine their processes and aspiring project managers eager to make their mark in the automotive sector. By integrating the insights provided herein, readers can expect to enhance their understanding and operational capabilities, ultimately transforming their manufacturing processes for peak efficiency. This resource serves as a roadmap for those navigating the dynamic landscape of automotive hardware production, equipping them with the knowledge and strategies to stay competitive and forward-thinking.
Experience the next level of project management today!
Understanding automotive hardware production
Definition and Key Components
Automotive hardware production involves the manufacturing of various physical components that make up a vehicle. This includes everything from engine parts and transmission systems to smaller elements like nuts and bolts. Each component plays a crucial role in the overall functionality and safety of a vehicle. The production process typically encompasses a range of activities, including design, material selection, manufacturing, assembly, and quality assurance. In contemporary manufacturing, this process is heavily reliant on precision engineering and advanced technology to meet the high standards of performance and safety expected in the automotive industry.
Processes Involved
The processes involved in automotive hardware production are complex and multifaceted. They often begin with the design phase, where engineers create detailed blueprints of each component. This is followed by the selection of suitable materials, considering factors like durability, weight, and cost. The manufacturing phase involves various methods such as casting, forging, machining, and welding, each chosen based on the component's specifications. Assembly lines are commonly used for mass production, ensuring efficiency and consistency across units. Once assembled, each component undergoes rigorous testing and quality checks to ensure it meets industry standards and regulations.
Historical Context and Evolution
The history of automotive hardware production is rich with innovation and evolution. In the early days of car manufacturing, components were manually crafted, leading to high costs and limited availability. The introduction of assembly lines by Henry Ford revolutionized the industry, making mass production feasible and affordable. Over the years, technological advancements have further transformed automotive hardware production. Computer-aided design (CAD) and computer-aided manufacturing (CAM) have streamlined the design and manufacturing processes, allowing for greater precision and efficiency. Recent developments in automation and robotics have further enhanced production capabilities, reducing human error and increasing output. The evolution of automotive hardware production continues as new materials, such as lightweight alloys and composites, are developed to meet the demands of modern vehicles for fuel efficiency and performance.
Applications of automotive hardware production
Diverse manufacturing scenarios
Diverse manufacturing scenarios
Automotive hardware production is integral to numerous manufacturing scenarios beyond traditional car manufacturing. It plays a pivotal role in sectors such as electric vehicles, aerospace, and even consumer electronics, where precision-engineered components are essential. The versatility of automotive hardware production methods allows them to be adapted to a wide range of applications, meeting the specific needs of different industries. This adaptability is a key strength, enabling manufacturers to diversify their offerings and explore new markets.
Key sectors benefiting from hardware production
Key sectors benefiting from hardware production
Several key sectors within the automotive industry benefit significantly from advancements in hardware production. For instance, the electric vehicle (EV) market relies heavily on precision hardware components to ensure the performance and safety of battery systems and electric drivetrains. Similarly, the aerospace industry benefits from automotive hardware production techniques to manufacture lightweight, durable components that withstand extreme conditions. The push for sustainability and efficiency in these sectors has driven further innovation in automotive hardware production, leading to the development of new materials and manufacturing processes.
Example of a leading car manufacturer
Example of a leading car manufacturer
Consider the case of Toyota, a leading automotive manufacturer renowned for its commitment to production efficiency and quality. Toyota's implementation of the "Toyota Production System" (TPS) is a testament to the power of effective hardware production. TPS emphasizes lean manufacturing principles, minimizing waste while maximizing productivity. This system has enabled Toyota to maintain high standards of quality and efficiency, setting a benchmark for the industry. The company utilizes advanced manufacturing techniques, such as robotics and automation, to streamline production processes and ensure consistent quality across its product lines.
Case of a mid-sized company
Case of a mid-sized company
A mid-sized company like Magna International has leveraged its expertise in automotive hardware production to gain a competitive advantage. By focusing on innovation and adaptability, Magna has successfully expanded its operations to supply components for electric and autonomous vehicles. This strategic move has positioned the company as a leader in the automotive supply chain, demonstrating the potential for mid-sized enterprises to thrive through effective hardware production.
A startup's innovative approach
A startup's innovative approach
In the startup realm, companies like Rivian have taken an innovative approach to automotive hardware production. Rivian's focus on sustainable and efficient manufacturing processes aligns with the growing demand for eco-friendly vehicles. By integrating cutting-edge technology and sustainable practices, Rivian has successfully carved out a niche in the competitive automotive market. This example highlights how startups can leverage innovative hardware production methods to differentiate themselves and capture market share.
Related:
Gaming API IntegrationClick here to read our expertly curated top picks!
Challenges and solutions in automotive hardware production
Common Challenges
Implementing automotive hardware production comes with its fair share of challenges. One of the most pressing issues is the complexity of supply chains, which can lead to disruptions and delays. The global nature of automotive manufacturing means that components often have to be sourced from different parts of the world, making them susceptible to geopolitical tensions and logistical issues. Additionally, maintaining stringent quality control is crucial to ensure that all components meet safety and performance standards. This requires robust testing and inspection processes, which can be resource-intensive. Moreover, balancing cost and resource optimization is a constant challenge, as manufacturers strive to keep production costs low while maintaining high quality.
Addressing Supply Chain Disruptions
To mitigate supply chain disruptions, manufacturers can adopt several strategic approaches. One effective strategy is to diversify suppliers, reducing reliance on a single source and minimizing the risk of disruption. Implementing advanced supply chain management software can also provide real-time visibility into supply chain operations, allowing for proactive identification and resolution of potential issues. Additionally, building strong relationships with suppliers can foster collaboration and flexibility, enabling swift responses to changes in demand or supply.
Ensuring Quality Control and Standard Compliance
Quality control and standard compliance are non-negotiable in automotive hardware production. Manufacturers can enhance quality assurance by implementing rigorous testing protocols and leveraging data analytics to monitor production processes. The use of automation and robotics can also improve precision and consistency, reducing the likelihood of defects. Regular audits and inspections are essential to ensure compliance with industry standards and regulations. Training employees on quality control best practices can further reinforce a culture of excellence within the organization.
Managing Cost and Resource Optimization
Cost and resource optimization are critical for maintaining competitiveness in the automotive industry. Manufacturers can achieve this by adopting lean manufacturing principles, which focus on minimizing waste and maximizing efficiency. Implementing advanced manufacturing technologies, such as 3D printing and automation, can also reduce production costs and resource consumption. Additionally, embracing a culture of continuous improvement can drive ongoing optimization efforts, enabling manufacturers to remain agile and responsive to market changes.
Best practices for automotive hardware production
Maximizing Benefits through Best Practices
To fully realize the benefits of automotive hardware production, manufacturers should adopt a set of best practices that enhance productivity and efficiency. These practices encompass various aspects of the production process, from design and material selection to manufacturing and quality control. By adhering to these best practices, manufacturers can ensure that their operations are streamlined, cost-effective, and aligned with industry standards.
Expert Tips for Enhanced Productivity
Industry experts recommend several tips for enhancing productivity in automotive hardware production. One key strategy is to invest in employee training and development, ensuring that the workforce is skilled and knowledgeable about the latest production techniques and technologies. This can lead to increased efficiency and reduced error rates. Another tip is to implement predictive maintenance for machinery and equipment, minimizing downtime and extending the lifespan of assets. Additionally, fostering a culture of innovation and collaboration can encourage employees to contribute ideas for process improvements and new product developments.
Maintaining Quality and Safety Standards
Maintaining high standards of quality and safety is paramount in automotive hardware production. Manufacturers can achieve this by establishing comprehensive quality management systems that encompass all stages of production. Regular audits and inspections should be conducted to identify potential areas for improvement and ensure compliance with industry regulations. Safety protocols must also be rigorously enforced to protect employees and prevent accidents. By prioritizing quality and safety, manufacturers can build a reputation for reliability and trustworthiness, enhancing their competitiveness in the market.
Click here to read our expertly curated top picks!
Software and tools enhancing automotive hardware production
Overview of Essential Software and Tools
In today's technologically advanced manufacturing landscape, software and tools play a crucial role in enhancing automotive hardware production. These tools facilitate various aspects of the production process, from design and planning to execution and quality control. By leveraging the right software and tools, manufacturers can streamline operations, improve accuracy, and boost overall efficiency.
Benefits of Recommended Software and Tools
Several types of software and tools are essential for optimizing automotive hardware production. Computer-aided design (CAD) software is indispensable for creating detailed and precise component designs. This software allows engineers to visualize and modify designs easily, reducing the time and cost associated with prototyping. Manufacturing execution systems (MES) provide real-time visibility into production processes, helping manufacturers monitor and control operations effectively. These systems can lead to significant improvements in productivity and quality. Additionally, enterprise resource planning (ERP) software integrates various functions within the organization, facilitating seamless communication and collaboration across departments.
Choosing the Right Software
When selecting software or tools for automotive hardware production, manufacturers should consider several factors. The software's compatibility with existing systems and processes is crucial to ensure a smooth integration. Scalability is another important consideration, as manufacturers may need to expand their operations in the future. It's also essential to evaluate the software's user-friendliness and the level of support and training provided by the vendor. By carefully assessing these factors, manufacturers can choose the right software that aligns with their specific manufacturing needs.
Future outlook of automotive hardware production
Examination of Future Trends
The future of automotive hardware production is poised for exciting developments, driven by technological advancements and changing market demands. One significant trend is the increasing adoption of automation and robotics, which are set to revolutionize production processes. These technologies can enhance precision, reduce labor costs, and increase production capacity. Additionally, the rise of electric and autonomous vehicles is expected to shape the landscape of automotive hardware production, necessitating the development of new components and manufacturing techniques.
Technological Advancements and Impacts
Technological advancements, such as artificial intelligence (AI) and the Internet of Things (IoT), are expected to have a profound impact on automotive hardware production. AI can optimize production processes through predictive analytics and machine learning, enabling manufacturers to make data-driven decisions. IoT connectivity can facilitate real-time monitoring and control of production equipment, improving efficiency and reducing downtime. These advancements can lead to significant improvements in productivity and quality, positioning manufacturers to meet the evolving needs of the automotive industry.
Strategies for Staying Competitive
To stay competitive in the future landscape of automotive hardware production, manufacturers must embrace innovation and adaptability. Investing in research and development can lead to the discovery of new materials and manufacturing processes that enhance performance and sustainability. Collaboration with technology partners and industry experts can also provide valuable insights and drive innovation. Additionally, manufacturers should focus on building a skilled and agile workforce capable of adapting to new technologies and market demands. By adopting these strategies, manufacturers can position themselves for success in the ever-evolving automotive industry.
Related:
ITILClick here to read our expertly curated top picks!
Do's and don'ts in automotive hardware production
Do's | Don'ts |
---|---|
Conduct thorough research before implementation. | Don’t overlook the importance of quality control. |
Engage with industry experts for insights. | Avoid rushing into adopting new technologies without a strategy. |
Continuously monitor and optimize processes. | Don’t ignore the importance of employee training. |
Leverage data analytics for informed decision-making. | Avoid cutting costs at the expense of safety standards. |
Related:
Game User Interface DesignClick here to read our expertly curated top picks!
Conclusion
In conclusion, mastering automotive hardware production is crucial for modern manufacturing success. This article has provided a comprehensive overview of the complexities and nuances of automotive hardware production, offering valuable insights and strategies for professionals and aspiring project managers in the field. By understanding the key components, processes, and applications of automotive hardware production, manufacturers can enhance their operational capabilities and achieve peak efficiency. Addressing common challenges and implementing best practices can lead to significant improvements in productivity, quality, and cost-effectiveness. As the automotive industry continues to evolve, embracing technological advancements and future trends will be key to staying competitive. By integrating the insights provided in this article, manufacturers can revolutionize their manufacturing processes and position themselves for success in the ever-changing automotive landscape. Implement these insights today to transform your manufacturing process and drive success in automotive hardware production!
Related:
4K GamingClick here to read our expertly curated top picks!
Further resources
- For further reading on automotive hardware production, consider exploring books and articles from industry experts and thought leaders. These resources can provide deeper insights into advanced manufacturing techniques and best practices.
- Several online courses and training programs are available to enhance your knowledge and skills in automotive hardware production. Platforms like Coursera and Udemy offer courses on advanced manufacturing technologies and industry trends.
- Joining professional organizations and online forums can provide valuable networking opportunities and access to industry insights. Organizations such as the Society of Automotive Engineers (SAE) and the Automotive Industry Action Group (AIAG) offer resources and events for professionals in the field.
Experience the next level of project management today!
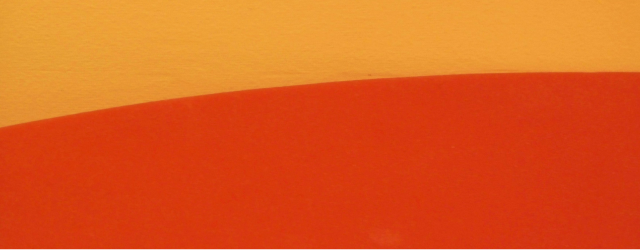
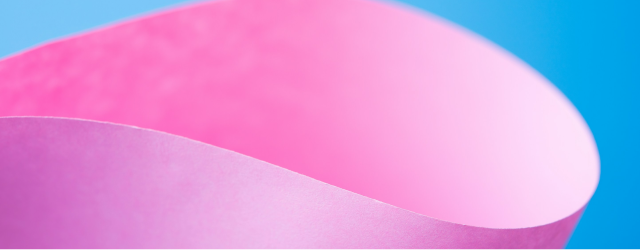
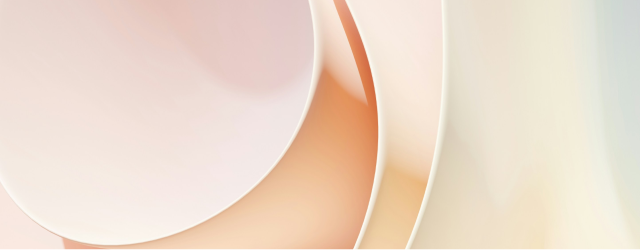
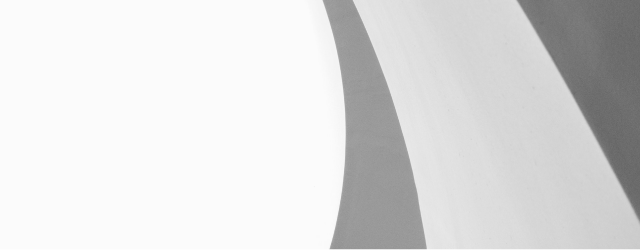
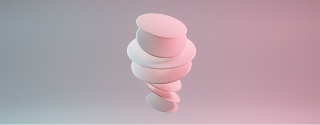
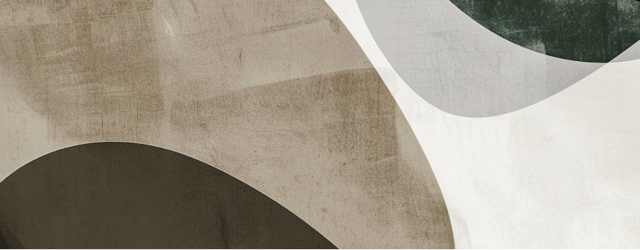
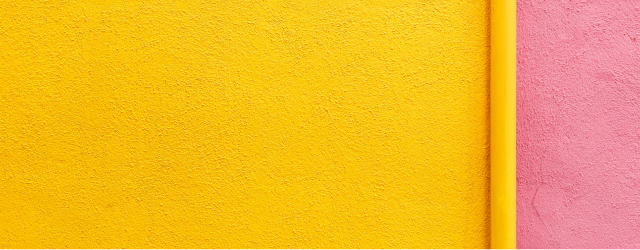
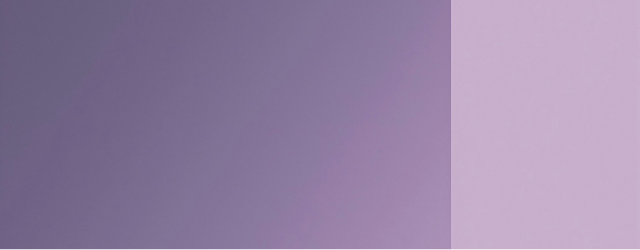