Plastic Parts Manufacturing
Dive into our expertly crafted article exploring Plastic Parts Manufacturing, where you'll get in-depth insights, practical applications, and industry best practices tailored for hardware enthusiasts and professionals.
Plastic parts manufacturing stands as a cornerstone in the modern industrial landscape, driving innovation and efficiency across numerous sectors. From automotive components to healthcare devices, the versatility and adaptability of plastic manufacturing make it an indispensable element of today's production processes. With technological advancements and evolving demands, mastering this field can provide unmatched efficiency and cost-effectiveness. This article aims to equip professionals and aspiring project managers with comprehensive insights into plastic parts manufacturing. By exploring its significance, applications, and future trends, readers will gain valuable knowledge to optimize their processes and stay competitive. In an era where adaptability and continuous improvement are key, understanding the nuances of plastic manufacturing is crucial for anyone looking to excel in the manufacturing domain. Whether you are a seasoned expert or a newcomer, the insights provided here will serve as a valuable resource for enhancing your manufacturing strategies.
Experience the next level of project management today!
Understanding plastic parts manufacturing
What is Plastic Parts Manufacturing?
Plastic parts manufacturing refers to the process of designing and producing components made from various types of plastic materials. This process involves several stages, including material selection, mold design, and the actual production, which can be achieved through methods such as injection molding, extrusion, or 3D printing. Each method offers unique benefits and challenges, depending on the specifications and requirements of the product being manufactured. For instance, injection molding is highly efficient for mass production, while 3D printing allows for greater customization and rapid prototyping. Understanding these processes is crucial for selecting the most suitable approach for a given project.
Evolution and Technological Advancements
The evolution of plastic parts manufacturing has been marked by significant technological advancements, transforming it from a rudimentary craft into a sophisticated and highly efficient industry. In the early 20th century, the development of synthetic polymers such as Bakelite paved the way for the modern plastics industry. Over the decades, innovations such as computer-aided design (CAD) and automation have further refined manufacturing processes, enabling greater precision and efficiency. Today, technologies like 3D printing and advanced robotics are pushing the boundaries of what is possible, allowing for complex designs and faster production times. These advancements not only improve product quality but also reduce costs and waste, making plastic manufacturing more sustainable and economically viable.
Relevance in Today's Industrial World
In today's industrial world, plastic parts manufacturing is indispensable due to its versatility, cost-effectiveness, and ability to meet diverse consumer demands. Plastics are used in virtually every industry, from automotive and aerospace to healthcare and consumer electronics. Their lightweight nature, durability, and ease of production make them ideal for a wide range of applications. Moreover, as industries strive for more sustainable practices, the development of biodegradable and recyclable plastics is gaining traction, further enhancing the relevance of plastic manufacturing in addressing environmental concerns. As a result, professionals in the field must stay informed about these trends and advancements to remain competitive and meet the evolving needs of the market.
Applications of plastic parts manufacturing
Industries utilizing plastic manufacturing
Industries utilizing plastic manufacturing
Plastic parts manufacturing is a critical component across various industries, each leveraging its unique benefits to meet specific needs. In the automotive industry, plastics are used for manufacturing lightweight components that improve fuel efficiency and reduce emissions. The healthcare sector relies on plastic parts for producing medical devices and equipment due to their sterility, durability, and cost-effectiveness. In consumer electronics, plastics enable the design of compact, lightweight devices with enhanced functionality. Additionally, the packaging industry uses plastics for creating versatile, durable, and attractive packaging solutions. By understanding the diverse applications of plastic manufacturing, project managers can identify opportunities for innovation and process improvement within their respective industries.
Case studies of successful implementations
Case studies of successful implementations
Examining successful implementations of plastic parts manufacturing can provide valuable insights into best practices and innovative approaches. For instance, the automotive company Ford has successfully utilized plastic manufacturing to produce lightweight car parts, reducing vehicle weight by up to 25% and improving fuel efficiency. In the healthcare sector, companies like Medtronic have leveraged plastic manufacturing to create advanced medical devices, such as insulin pumps and surgical instruments, that are both cost-effective and high-performing. Samsung, a leader in consumer electronics, has utilized plastics to design sleek, lightweight devices with enhanced performance and durability. These examples illustrate the potential of plastic manufacturing to drive innovation and efficiency across various industries.
Versatility and customization options
Versatility and customization options
One of the key advantages of plastic parts manufacturing is its versatility and ability to accommodate customization. Plastics can be molded into complex shapes and designs, allowing manufacturers to meet specific production requirements and consumer preferences. This adaptability enables industries to produce a wide range of products, from simple components to highly specialized and intricate designs. Additionally, advancements in manufacturing technologies, such as 3D printing, have further expanded the scope of customization, enabling rapid prototyping and the production of small batches with minimal tooling costs. By leveraging these capabilities, businesses can enhance their product offerings and remain competitive in an ever-evolving market.
Click here to read our expertly curated top picks!
Challenges and solutions in plastic parts manufacturing
Common Challenges in Plastic Manufacturing
Despite the numerous benefits of plastic parts manufacturing, several challenges must be addressed to ensure efficient and high-quality production. One of the primary challenges is material selection. With a wide range of plastic materials available, choosing the right one for a specific application requires careful consideration of factors such as strength, flexibility, temperature resistance, and cost. Another common challenge is maintaining quality control throughout the production process. Ensuring that each component meets the required specifications and standards is critical to avoiding defects and customer dissatisfaction. Additionally, managing production costs is a significant concern, as fluctuations in material prices and energy costs can impact profitability.
Practical Solutions and Strategic Approaches
To overcome these challenges, manufacturers can adopt various practical solutions and strategic approaches. For material selection, conducting thorough research and collaborating with material experts can help identify the most suitable plastic for a specific application. Implementing robust quality control measures, such as regular inspections and testing, can help maintain product consistency and minimize defects. To manage production costs, manufacturers can optimize their processes by investing in energy-efficient equipment and exploring cost-effective sourcing options for raw materials. Additionally, leveraging technology, such as automation and data analytics, can enhance efficiency and reduce waste, further improving cost management.
Role of Innovation and Technology
Innovation and technology play a crucial role in addressing manufacturing challenges and driving industry advancement. By embracing cutting-edge technologies, such as 3D printing, robotics, and IoT, manufacturers can streamline their operations, improve product quality, and reduce production costs. These technologies enable greater precision, faster production times, and enhanced customization capabilities, allowing businesses to meet evolving consumer demands. Additionally, ongoing research and development in the field of plastics are leading to the creation of new materials with improved properties, such as enhanced strength, flexibility, and sustainability. By staying informed about these innovations, manufacturers can adapt to changing market trends and maintain a competitive edge.
Best practices for plastic parts manufacturing
Optimizing Production Efficiency and Quality
To achieve optimal production efficiency and quality in plastic parts manufacturing, businesses must implement best practices that address key aspects of the manufacturing process. One of the primary ways to enhance efficiency is through process optimization, which involves identifying and eliminating bottlenecks, reducing waste, and improving workflow. For instance, implementing lean manufacturing principles can help streamline operations and minimize unnecessary steps, leading to faster production times and reduced costs. Additionally, maintaining a focus on quality is crucial, as producing high-quality components not only satisfies customer expectations but also reduces the likelihood of costly defects and recalls.
Insights from Industry Experts
Industry experts emphasize the importance of continuous process improvement and innovation in maintaining competitiveness in the plastic manufacturing sector. According to a study by McKinsey & Company, companies that prioritize innovation and invest in new technologies are more likely to outperform their peers in terms of efficiency and profitability. Experts also highlight the value of collaboration and knowledge sharing among industry professionals, as this can lead to the development of new ideas and strategies for overcoming manufacturing challenges. By staying informed about industry trends and best practices, businesses can stay ahead of the curve and continuously improve their processes.
Importance of Continuous Learning and Adaptation
In the dynamic world of manufacturing, continuous learning and adaptation are essential for success. As new technologies and materials emerge, businesses must be willing to adapt and evolve to stay competitive. This requires a commitment to ongoing education and professional development, both for individual employees and for the organization as a whole. Encouraging a culture of innovation and learning can lead to the development of new processes and products, ultimately driving business growth and success. By prioritizing continuous improvement and staying informed about industry advancements, manufacturers can enhance their capabilities and remain leaders in their field.
Related:
4K GamingClick here to read our expertly curated top picks!
Essential software and tools for plastic parts manufacturing
Overview of Key Software and Tools
The use of essential software and tools is critical to the success of plastic parts manufacturing. These technologies enhance precision, efficiency, and quality throughout the production process. One of the most commonly used tools is Computer-Aided Design (CAD) software, which allows designers to create detailed 3D models of plastic components. These models can then be used to simulate the manufacturing process, identify potential issues, and optimize design parameters. Additionally, simulation software is invaluable for predicting how materials will behave under different conditions, allowing manufacturers to make informed decisions about material selection and process settings.
Benefits of CAD, Simulation, and Automation
The integration of CAD, simulation, and automation tools offers numerous benefits for plastic parts manufacturing. CAD software streamlines the design process, reducing the time and effort required to create complex geometries and ensuring that components meet precise specifications. Simulation tools enable manufacturers to identify potential issues before production begins, minimizing the risk of defects and reducing trial-and-error costs. Automation technologies, such as robotic systems and machine learning algorithms, further enhance efficiency by reducing manual labor, increasing production speed, and ensuring consistent quality. By leveraging these tools, manufacturers can optimize their processes, reduce waste, and improve overall productivity.
Selecting the Right Tools for Specific Needs
Selecting the right software and tools for a specific manufacturing process requires careful consideration of various factors, including the complexity of the design, production volume, and budget constraints. Manufacturers should evaluate their specific needs and objectives to determine which tools will provide the most value. For instance, businesses with high production volumes may benefit from investing in advanced automation systems, while those focused on custom designs may prioritize CAD and simulation software. Additionally, staying informed about the latest technological advancements and industry trends can help manufacturers identify new tools and solutions that can further enhance their capabilities. By selecting the right tools, businesses can achieve greater efficiency, quality, and competitiveness in their manufacturing processes.
Future outlook of plastic parts manufacturing
Predicting Future Trends and Innovations
The future of plastic parts manufacturing is poised for exciting developments, with emerging trends and innovations set to reshape the industry. One of the most significant trends is the increasing focus on sustainability and the development of eco-friendly materials. As environmental concerns continue to gain prominence, manufacturers are investing in research and development to create biodegradable and recyclable plastics. Additionally, advancements in 3D printing technology are expected to revolutionize the manufacturing process, enabling greater customization, faster production times, and reduced material waste. The integration of artificial intelligence (AI) and machine learning is also anticipated to enhance process optimization and quality control, leading to improved efficiency and product consistency.
Impact of Sustainability and Eco-Friendly Practices
The shift towards sustainability and eco-friendly practices in plastic parts manufacturing is driven by the growing demand for environmentally responsible products. Consumers and regulatory bodies are increasingly prioritizing sustainability, prompting manufacturers to adopt greener practices and materials. This includes the use of bio-based plastics, which are derived from renewable resources and offer reduced environmental impact compared to traditional petroleum-based plastics. Additionally, implementing recycling and waste reduction initiatives can further enhance sustainability efforts. By embracing eco-friendly practices, manufacturers can not only meet consumer demands but also reduce their environmental footprint and improve their brand reputation.
Staying Competitive and Adaptive to Changes
To remain competitive and adaptive in the evolving landscape of plastic parts manufacturing, businesses must prioritize innovation and continuous improvement. This involves staying informed about industry trends, technological advancements, and consumer preferences. By investing in research and development, manufacturers can identify new opportunities for growth and innovation, ensuring their products and processes remain relevant and competitive. Additionally, fostering a culture of collaboration and knowledge sharing among employees can lead to the development of new ideas and solutions for overcoming manufacturing challenges. By embracing change and prioritizing adaptability, businesses can thrive in the dynamic world of plastic parts manufacturing.
Related:
Joint Application DevelopmentClick here to read our expertly curated top picks!
Examples of successful plastic parts manufacturing
Automotive industry - custom plastic components for enhanced vehicle efficiency
Automotive industry - custom plastic components for enhanced vehicle efficiency
In the automotive industry, plastic parts manufacturing has been instrumental in producing lightweight components that enhance vehicle efficiency. For instance, Ford has successfully utilized plastic materials to manufacture car parts that reduce vehicle weight by up to 25%, leading to improved fuel efficiency and reduced emissions. This approach not only meets regulatory requirements for fuel economy but also provides a competitive edge in the market by offering environmentally friendly vehicles. By leveraging the versatility and lightweight properties of plastics, automotive manufacturers can produce high-performance vehicles that meet consumer demands for efficiency and sustainability.
Healthcare sector - manufacturing medical devices using advanced plastic technologies
Healthcare sector - manufacturing medical devices using advanced plastic technologies
The healthcare sector relies heavily on plastic parts manufacturing for the production of medical devices and equipment. Companies like Medtronic have used advanced plastic technologies to create innovative medical devices, such as insulin pumps and surgical instruments, that are both cost-effective and high-performing. Plastics offer various advantages, including sterility, durability, and design flexibility, making them ideal for medical applications. By utilizing cutting-edge manufacturing processes, healthcare companies can produce high-quality medical devices that improve patient outcomes and meet stringent regulatory standards.
Consumer electronics - innovative plastic parts in smart device production
Consumer electronics - innovative plastic parts in smart device production
Plastic parts manufacturing plays a crucial role in the consumer electronics industry, enabling the production of innovative and compact devices. Samsung, a leader in electronics, has leveraged plastic materials to design sleek, lightweight devices with enhanced functionality and durability. Plastics allow for intricate designs and compact sizes, meeting consumer demands for portable and aesthetically pleasing products. By integrating advanced plastic manufacturing technologies, electronics companies can produce cutting-edge devices that offer superior performance and user experience, driving market growth and consumer satisfaction.
Related:
Game User Interface DesignClick here to read our expertly curated top picks!
Tips for do's and don'ts in plastic parts manufacturing
Do's | Don'ts |
---|---|
Invest in quality control systems | Overlook the importance of material selection |
Stay updated with industry trends | Ignore maintenance and equipment upgrades |
Encourage team collaboration and training | Neglect compliance with safety standards |
Click here to read our expertly curated top picks!
Conclusion
In conclusion, mastering plastic parts manufacturing is essential for professionals seeking to enhance their processes and achieve unmatched efficiency in the industry. By understanding the significance, applications, and challenges of plastic manufacturing, businesses can identify opportunities for innovation and growth. Embracing best practices, leveraging essential software and tools, and staying informed about future trends and sustainability efforts will enable manufacturers to remain competitive and adaptive in an ever-evolving landscape. As the industry continues to advance, continuous learning and adaptation are key to maintaining success and driving business growth. By applying the insights gained from this article, professionals can optimize their manufacturing processes and achieve greater efficiency and quality in their operations.
Further resources
- American Society of Manufacturing Engineers (ASME) - Comprehensive resources and training programs for manufacturing professionals.
- Plastics Industry Association - Industry insights, news, and networking opportunities for plastic manufacturers.
- Lean Manufacturing Principles - Explore lean manufacturing methodologies to enhance efficiency and reduce waste.
- Coursera Manufacturing Courses - Online courses on manufacturing processes and technologies.
Experience the next level of project management today!
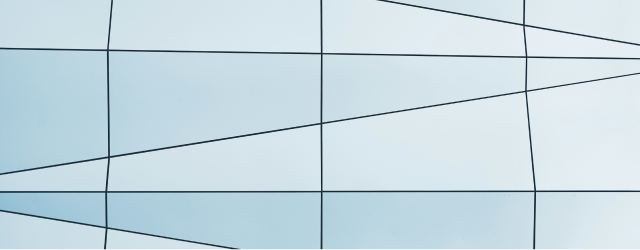
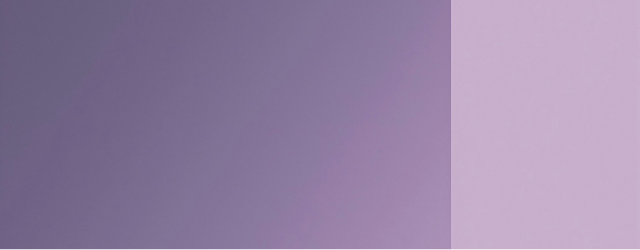
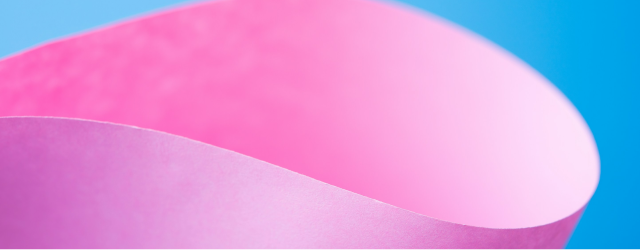
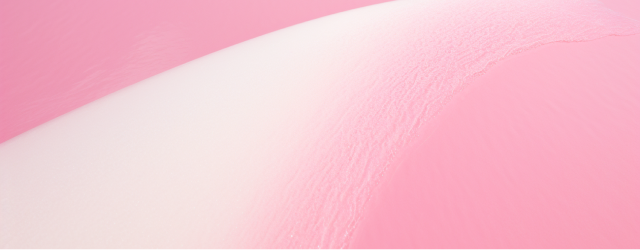
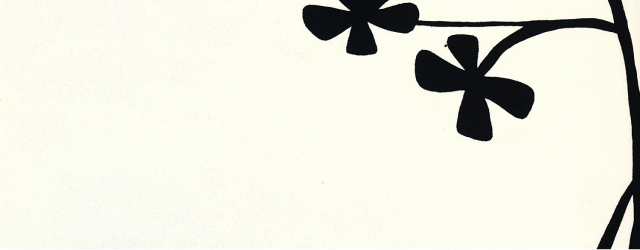
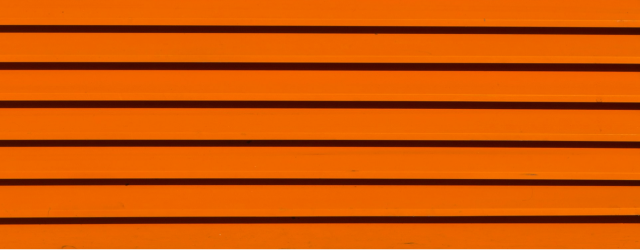
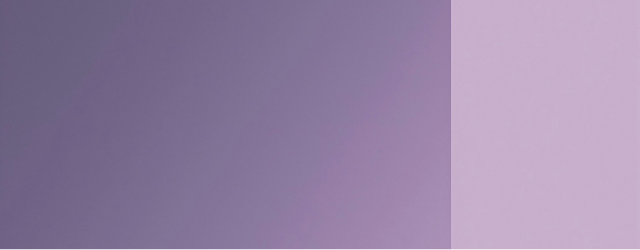
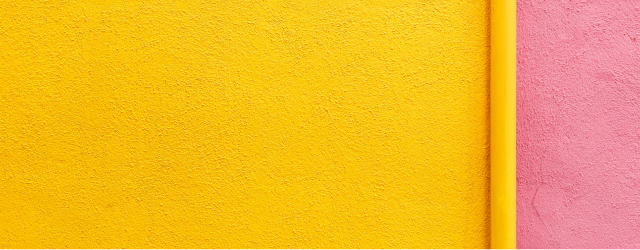