Energy Efficiency In Manufacturing
Dive into our expertly crafted article exploring Energy Efficiency in Manufacturing, where you'll get in-depth insights, practical applications, and industry best practices tailored for hardware enthusiasts and professionals.
In the rapidly evolving landscape of modern manufacturing, energy efficiency has emerged as a cornerstone for sustainable development and competitive advantage. As industries grapple with escalating energy costs and increasing regulatory pressures to reduce carbon footprints, the critical importance of adopting energy-efficient practices becomes undeniable. Energy consumption accounts for a significant portion of operational expenses in manufacturing, and inefficiencies can lead to substantial financial burdens. By optimizing energy use, manufacturers not only achieve substantial cost savings but also contribute positively to environmental conservation. The dual benefits of cost reduction and the minimization of environmental impact make energy efficiency an essential strategy for future-proofing manufacturing operations.
Moreover, the shift towards sustainability has intensified the focus on energy efficiency. Traditional manufacturing processes often rely heavily on fossil fuels, leading to considerable greenhouse gas emissions. As global awareness of climate change grows, there is a rising need for industries to transition to more sustainable practices. Implementing energy-efficient technologies and processes helps manufacturers reduce their environmental footprint, aligning with global sustainability goals and enhancing corporate responsibility. This transformation is not merely a trend but a necessary evolution, as consumers and stakeholders increasingly demand transparency and accountability in environmental stewardship.
Setting the stage for a comprehensive exploration of energy efficiency in manufacturing, this article delves into its applications, challenges, and future outlook. We will explore how energy efficiency not only supports operational excellence but also paves the way for innovation and growth. Through real-world examples, best practices, and strategic insights, this article aims to equip project managers and industry leaders with the knowledge and tools necessary to harness the full potential of energy-efficient manufacturing. By embracing energy efficiency, manufacturers can unlock new opportunities, foster sustainability, and remain resilient in a competitive global market.
Experience the next level of project management today!
Understanding energy efficiency in manufacturing
Defining Energy Efficiency in Manufacturing
Energy efficiency in the context of manufacturing refers to the optimal use of energy resources to produce goods without waste. It involves implementing processes and technologies that require less energy to accomplish the same production tasks, thereby reducing energy consumption and costs. The concept is rooted in the principles of minimizing energy loss and maximizing productivity, leading to more sustainable and profitable operations. For instance, replacing outdated machinery with modern, high-efficiency equipment can result in significant energy savings while enhancing production capacity.
Historical Evolution and Milestones
The evolution of energy efficiency in manufacturing can be traced back to the industrial revolution when energy was primarily derived from coal and steam. Over the decades, advancements in technology have introduced more efficient energy sources and processes. Significant milestones include the development of electric power, the introduction of automation, and the recent surge in digital technologies such as the Internet of Things (IoT) and artificial intelligence (AI). These innovations have enabled manufacturers to monitor and optimize energy use in real time, leading to unprecedented levels of efficiency.
Fundamental Principles and Scientific Basis
The scientific basis of energy efficiency lies in the laws of thermodynamics, which govern energy transfer and conversion. In manufacturing, energy efficiency is achieved by reducing energy input relative to output. This can be accomplished through various methods, such as improving heat recovery systems, optimizing motor performance, and minimizing idle time in production lines. The fundamental principles of energy efficiency focus on reducing energy waste and enhancing the overall energy performance of manufacturing systems.
Relevance in Modern Manufacturing
In today's manufacturing environment, energy efficiency is more relevant than ever due to several prevailing industry trends. The increasing cost of energy, coupled with stringent environmental regulations, compels manufacturers to find ways to operate more efficiently. Moreover, the shift towards sustainable practices and the growing demand for eco-friendly products have further emphasized the importance of energy efficiency. According to the International Energy Agency (IEA), improving energy efficiency could contribute to more than 40% of the emission reductions needed to meet global climate goals.
Applications of energy efficiency in manufacturing
Diverse applications across sectors
Diverse applications across sectors
Energy efficiency finds diverse applications across various manufacturing sectors, each with unique requirements and challenges. In the automotive industry, for instance, manufacturers are implementing energy-efficient lighting and climate control systems to reduce operational costs and enhance worker productivity. Similarly, in the chemical sector, energy-efficient distillation and reaction processes are crucial for minimizing energy consumption and emissions. The electronics industry, on the other hand, focuses on optimizing energy use in production facilities and data centers.
Integration of energy-efficient technologies
Integration of energy-efficient technologies
The integration of energy-efficient technologies into production lines is essential for achieving substantial energy savings. Technologies such as variable speed drives, energy-efficient motors, and advanced control systems can significantly reduce energy consumption. Additionally, the adoption of renewable energy sources, such as solar and wind, complements energy efficiency efforts by providing clean and sustainable power. For example, a manufacturing plant that integrates solar panels with energy-efficient machinery can drastically cut energy costs while reducing its carbon footprint.
Real-world success stories
Real-world success stories
Several companies have successfully implemented energy efficiency strategies, yielding impressive results. General Electric (GE), for instance, has invested in energy-efficient technologies across its manufacturing operations, resulting in a 30% reduction in energy intensity over the past decade. Similarly, Toyota's production facilities have embraced energy-efficient practices, such as the use of regenerative braking systems and optimized heating, ventilation, and air conditioning (HVAC) systems, leading to significant energy savings and enhanced production efficiency.
Benefits beyond cost savings
Benefits beyond cost savings
The benefits of energy efficiency in manufacturing extend beyond cost savings. By reducing energy consumption, manufacturers can lower their environmental impact, contributing to sustainability goals and enhancing their corporate image. Moreover, energy-efficient practices often lead to improved product quality and consistency, as optimized processes reduce defects and downtime. The competitive advantage gained through energy efficiency can also enhance customer satisfaction and loyalty, as consumers increasingly prioritize sustainability in their purchasing decisions.
Click here to read our expertly curated top picks!
Challenges and solutions
Common Challenges in Implementation
Despite its numerous benefits, implementing energy efficiency measures in manufacturing can pose several challenges. Financial constraints often top the list, as the initial investment required for energy-efficient technologies can be substantial. Additionally, technological limitations may hinder the adoption of advanced energy solutions, particularly in older facilities with outdated infrastructure. Workforce resistance to change and the complexity of integrating new systems with existing processes further complicate implementation efforts.
Overcoming Financial Barriers
Addressing financial constraints requires a strategic approach to funding and investment. Manufacturers can explore various financing options, such as energy performance contracts, where the cost savings from energy efficiency improvements are used to pay for the investment. Government incentives and grants for energy efficiency projects can also alleviate financial burdens. Moreover, conducting a thorough cost-benefit analysis and demonstrating the long-term return on investment (ROI) can help secure internal buy-in and support for energy efficiency initiatives.
Tackling Technological and Workforce Challenges
Technological limitations can be overcome by adopting a phased approach to implementation, prioritizing high-impact areas and gradually expanding energy efficiency measures. Collaborating with technology providers and industry experts can provide valuable insights and solutions for integrating advanced systems. To address workforce resistance, it is crucial to engage employees in the energy efficiency journey. Providing training and education on the benefits and importance of energy efficiency can foster a culture of sustainability and encourage employee participation in energy-saving efforts.
Successful Case Studies
Several case studies highlight successful approaches to overcoming challenges in energy efficiency implementation. A notable example is the partnership between Siemens and BASF, where advanced energy management systems were implemented to optimize energy use at BASF's chemical production facilities. This collaboration resulted in a 5% reduction in energy consumption and a significant decrease in carbon emissions. Similarly, Nestlé's energy efficiency program, which focuses on optimizing production processes and engaging employees, has led to substantial energy savings and improved operational efficiency across its manufacturing sites.
Best practices for energy efficiency in manufacturing
Comprehensive Energy Audits
Conducting comprehensive energy audits is a fundamental best practice for maximizing energy efficiency in manufacturing settings. Energy audits involve a detailed assessment of energy usage patterns and identify areas of inefficiency. By analyzing energy consumption data, manufacturers can pinpoint specific processes or equipment that require optimization. Regular energy audits ensure that energy efficiency measures remain effective and enable continuous improvement.
Industry-Leading Tips and Strategies
Industry leaders and experts offer valuable tips and strategies for enhancing energy efficiency in manufacturing. One key strategy is to prioritize energy efficiency during the design phase of new facilities or production lines. Incorporating energy-efficient technologies and processes from the outset can yield long-term benefits. Additionally, leveraging digital tools and data analytics to monitor and optimize energy use in real-time can drive significant improvements in energy performance.
Continuous Monitoring and Evaluation
Continuous monitoring and evaluation of energy performance are essential for sustaining energy efficiency efforts. Implementing energy management systems and IoT devices allows manufacturers to track energy consumption and identify deviations from optimal performance. By setting clear energy goals and key performance indicators (KPIs), manufacturers can measure progress and make data-driven decisions to enhance energy efficiency.
Role of Employee Engagement and Training
Employee engagement and training play a vital role in achieving energy efficiency goals. Involving employees in energy efficiency initiatives fosters a sense of ownership and responsibility. Training programs that educate employees on energy-saving practices and technologies empower them to contribute actively to energy efficiency efforts. Recognizing and rewarding employee contributions to energy efficiency can further motivate participation and drive positive outcomes.
Click here to read our expertly curated top picks!
Software and tools enhancing energy efficiency
Overview of Digital Tools
The digital revolution has introduced a plethora of software and tools that support the implementation of energy efficiency in manufacturing. Energy management systems (EMS) are at the forefront, providing a centralized platform for monitoring and optimizing energy use. These systems collect and analyze data from various sources, enabling manufacturers to identify energy-saving opportunities and implement corrective actions in real-time. Simulation software, on the other hand, allows manufacturers to model and assess the energy impact of different production scenarios before implementation.
Benefits of Advanced Tools
The benefits of utilizing advanced tools for energy efficiency are multifaceted. Energy management systems offer insights into energy consumption patterns, facilitating informed decision-making and proactive energy management. IoT devices, such as smart sensors and meters, provide real-time data on energy usage, enabling manufacturers to detect anomalies and prevent energy waste. Automation and smart manufacturing technologies further enhance energy efficiency by optimizing production processes and reducing idle time.
Selecting the Right Tools
Choosing the right tools for energy efficiency depends on specific manufacturing needs and priorities. Manufacturers should consider factors such as the scale of operations, existing infrastructure, and desired outcomes when selecting software and tools. Engaging with technology providers and conducting pilot tests can help assess the suitability and effectiveness of potential solutions. Additionally, integrating energy efficiency tools with existing systems ensures seamless operation and maximizes the benefits of digital technologies.
Impact of Automation and Smart Manufacturing
Automation and smart manufacturing technologies have a profound impact on energy efficiency. Automated systems reduce the need for manual intervention, minimizing human error and optimizing energy use. Smart manufacturing, powered by AI and machine learning, enables predictive maintenance and process optimization, leading to significant energy savings. By leveraging automation and smart technologies, manufacturers can achieve greater efficiency, improve product quality, and reduce operational costs.
Future outlook on energy efficiency in manufacturing
Emerging Trends and Directions
The future of energy efficiency in manufacturing is shaped by emerging trends and advancements in technology. One notable trend is the integration of renewable energy sources into manufacturing processes. The use of solar, wind, and biomass energy is gaining traction as manufacturers seek to reduce their reliance on fossil fuels and lower carbon emissions. Additionally, the development of smart grid technologies enables more efficient distribution and management of energy resources, further enhancing energy efficiency.
Advancements in Renewable Energy Integration
Renewable energy integration is set to play a pivotal role in the future of energy efficiency. Manufacturers are increasingly investing in renewable energy projects to power their operations sustainably. For example, Tesla's Gigafactory in Nevada operates entirely on renewable energy, harnessing solar and wind power to meet its energy needs. This shift towards clean energy not only reduces environmental impact but also provides long-term cost savings and energy security.
Role of Policy and Regulatory Frameworks
Policy and regulatory frameworks are instrumental in driving future developments in energy efficiency. Governments worldwide are implementing policies that incentivize energy efficiency and promote sustainable practices. Initiatives such as tax credits, grants, and subsidies encourage manufacturers to invest in energy-efficient technologies. Compliance with energy efficiency standards and regulations ensures accountability and fosters a culture of sustainability within the industry.
Strategies for Staying Competitive
To remain competitive in the evolving landscape of energy efficiency, manufacturers must adopt forward-thinking strategies. Staying informed about the latest technological advancements and industry trends is crucial for identifying new opportunities. Collaborating with industry partners, research institutions, and government agencies can provide valuable insights and resources for energy efficiency initiatives. Furthermore, fostering a culture of innovation and continuous improvement ensures that manufacturers remain at the forefront of energy efficiency advancements.
Related:
AI In Finance And BankingClick here to read our expertly curated top picks!
Examples of energy efficiency implementation
Example 1: automotive manufacturing
Example 1: automotive manufacturing
In the automotive manufacturing sector, energy-efficient lighting and machinery have been implemented to achieve significant energy savings. A notable example is Ford's Dagenham Engine Plant in the UK, which has installed energy-efficient LED lighting and optimized its production processes. As a result, the plant has achieved a 40% reduction in energy consumption, leading to substantial cost savings and a significant reduction in carbon emissions. This commitment to energy efficiency not only enhances Ford's sustainability credentials but also improves operational efficiency and product quality.
Example 2: food and beverage industry
Example 2: food and beverage industry
The food and beverage industry has embraced energy-efficient refrigeration systems to reduce energy consumption and enhance product shelf life. Nestlé, a global leader in the sector, has implemented state-of-the-art refrigeration technologies in its processing facilities. These systems are designed to minimize energy use while maintaining optimal temperatures for food preservation. The adoption of energy-efficient refrigeration has led to a 10% reduction in energy consumption across Nestlé's operations, resulting in cost savings and a lower environmental impact. Additionally, the improved efficiency of refrigeration systems has extended the shelf life of products, enhancing product quality and reducing waste.
Example 3: electronics manufacturing
Example 3: electronics manufacturing
Electronics manufacturing has witnessed significant improvements in operational efficiency and environmental impact through the adoption of smart energy management systems. Samsung's semiconductor manufacturing facilities have integrated advanced energy management solutions to monitor and optimize energy use. By leveraging IoT devices and data analytics, Samsung has achieved a 15% reduction in energy consumption, resulting in substantial cost savings and a decrease in greenhouse gas emissions. The implementation of smart energy management systems has also enhanced operational efficiency by reducing downtime and improving production processes.
Related:
ITILClick here to read our expertly curated top picks!
Do's and don'ts of energy efficiency in manufacturing
Do's | Don'ts |
---|---|
Conduct regular energy audits | Ignore employee input and feedback |
Invest in training and development | Overlook the importance of maintenance |
Monitor energy consumption continuously | Rely solely on outdated technologies |
Engage with energy efficiency consultants | Skip initial pilot testing of new strategies |
Related:
Game User Interface DesignClick here to read our expertly curated top picks!
Conclusion
Recapping the key takeaways from this article, it is evident that energy efficiency plays a pivotal role in transforming manufacturing into a sustainable and competitive industry. By optimizing energy use, manufacturers can achieve significant cost savings, reduce environmental impact, and enhance operational efficiency. The benefits of energy efficiency extend beyond financial gains, contributing to improved product quality and corporate responsibility. Emphasizing the importance of energy efficiency for sustainable manufacturing practices, this article encourages readers to implement the insights and strategies discussed to revolutionize their manufacturing processes.
Through comprehensive energy audits, the adoption of advanced technologies, and continuous monitoring, manufacturers can unlock the full potential of energy efficiency. Engaging employees and stakeholders in the energy efficiency journey fosters a culture of sustainability and drives positive outcomes. As the manufacturing landscape continues to evolve, it is crucial for industry leaders to stay informed about emerging trends and advancements in energy efficiency. By embracing innovation and continuous improvement, manufacturers can remain resilient and competitive in a global market that increasingly values sustainability.
In conclusion, the journey towards energy-efficient manufacturing is a dynamic and ongoing process. It requires commitment, collaboration, and a willingness to adapt to new challenges and opportunities. By prioritizing energy efficiency, manufacturers can contribute to a more sustainable future while reaping the benefits of cost savings, enhanced performance, and improved environmental stewardship. The call to action for continuous improvement and innovation in energy efficiency invites manufacturers to lead the way in creating a more sustainable and prosperous industry.
Further resources
For those seeking additional readings and resources to further explore energy efficiency in manufacturing, several valuable options are available. The U.S. Department of Energy's Office of Energy Efficiency and Renewable Energy (EERE) offers a wealth of information, case studies, and best practices for improving energy efficiency in industrial settings. The International Energy Agency (IEA) provides comprehensive reports and analysis on global energy trends and developments, offering insights into the future of energy efficiency.
Professional development opportunities, such as courses and training programs offered by the Association of Energy Engineers (AEE) and the Energy Institute, provide in-depth knowledge and expertise in energy management and efficiency. These programs cover a wide range of topics, from energy audits and system optimization to renewable energy integration and policy frameworks.
Additionally, joining professional bodies and online forums dedicated to energy efficiency can provide valuable networking opportunities and access to expert advice. Platforms like Energy Central and the American Society of Mechanical Engineers (ASME) offer forums and communities where professionals can share insights, discuss challenges, and collaborate on energy efficiency initiatives. Engaging with these resources can enhance understanding, support professional growth, and contribute to the successful implementation of energy efficiency in manufacturing.
Experience the next level of project management today!
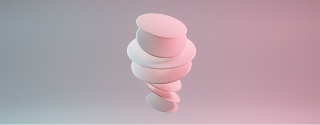
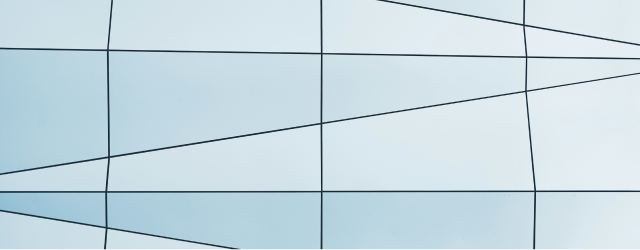
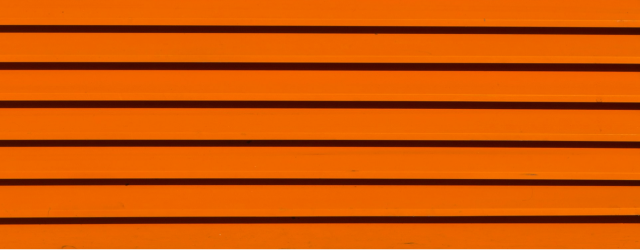
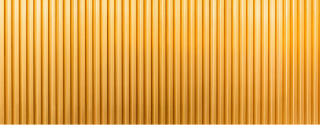
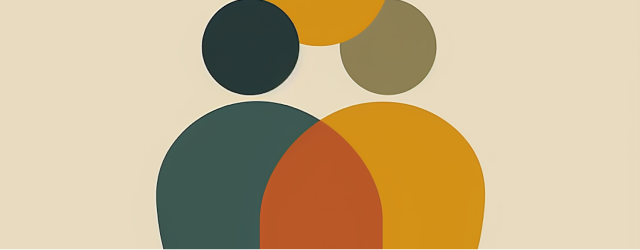
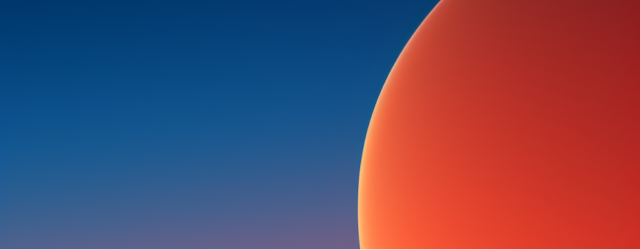
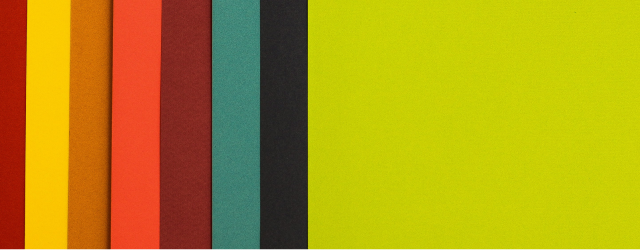
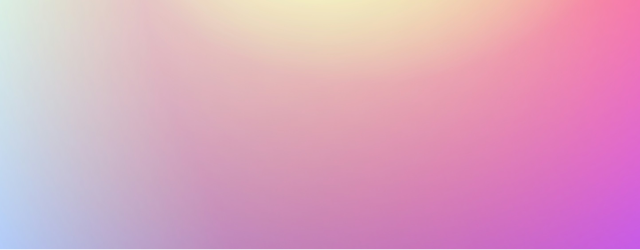