Capital Investment In Manufacturing
Dive into our expertly crafted article exploring Capital Investment in Manufacturing, where you'll get in-depth insights, practical applications, and industry best practices tailored for hardware enthusiasts and professionals.
In the rapidly evolving landscape of the manufacturing industry, capital investment plays a pivotal role in driving both efficiency and innovation. As the global economy continues to recover from recent disruptions, manufacturers are increasingly recognizing the need to invest in advanced technologies and infrastructure to remain competitive. While capital investment in manufacturing is often associated with high financial stakes, it offers substantial rewards by enhancing productivity, reducing operational costs, and facilitating the adoption of cutting-edge technologies. In fact, according to a report by the World Economic Forum, the manufacturing sector is expected to see a significant increase in capital investment, reaching approximately $1.3 trillion by 2025, highlighting its critical importance.
For project managers and industry professionals, understanding the intricacies of capital investment is essential to unlocking its full potential. This article delves into the various dimensions of capital investment in manufacturing, offering insights into effective strategies, tools, and practices that can optimize investments for maximum return. By exploring real-world case studies and expert opinions, we aim to provide a comprehensive guide for manufacturing professionals seeking to leverage capital investments to drive their organizations forward. From the definition and historical context of capital investments to the challenges and solutions faced during implementation, this article covers a broad spectrum of topics, setting the stage for a deep dive into the world of manufacturing capital investments.
At Meegle, we understand that capital investments in manufacturing aren't just about spending money but are strategic endeavors that require careful planning, execution, and evaluation. Whether you're looking to modernize your operations, implement sustainable practices, or expand into new markets, understanding how to effectively manage capital investments is crucial. Join us on this journey as we explore strategies that not only optimize financial returns but also drive innovation and foster long-term growth in the manufacturing sector.
Experience the next level of project management today!
Understanding capital investment in manufacturing
Definition and Scope of Capital Investment
Capital investment in the manufacturing sector refers to the funds allocated by a company to acquire, upgrade, or maintain physical assets such as machinery, technology, and facilities. These investments are crucial for ensuring the production processes remain efficient and competitive. Capital investments can be classified into two main categories: fixed capital investment, which includes tangible assets like buildings and machinery, and working capital investment, which pertains to the funds required for the day-to-day operations. The scope of capital investment extends beyond merely purchasing new equipment; it encompasses strategic decisions about which assets to acquire, how to finance them, and how to integrate them into existing systems.
A well-planned capital investment strategy can significantly enhance a manufacturing company's productivity and competitive edge. For instance, investing in automation technologies can streamline production processes, reduce labor costs, and improve product quality. On the other hand, upgrading to energy-efficient machinery can lower operational costs and contribute to sustainability goals. By aligning capital investments with organizational objectives, manufacturers can ensure a high return on investment and maintain a competitive position in the market.
Historical Context and Evolution
The concept of capital investment in manufacturing has evolved significantly over the decades. Historically, manufacturing relied heavily on manual labor and rudimentary machinery. However, the Industrial Revolution of the 18th and 19th centuries marked a turning point, as industries began investing in mechanized equipment to enhance productivity. This era saw an unprecedented rise in capital investments in manufacturing, laying the groundwork for modern industrial practices.
Fast forward to the 20th century, the advent of computers and digital technologies revolutionized manufacturing processes. The integration of information technology systems became a key focus of capital investments, enabling manufacturers to automate operations and improve data analytics. Today, we are witnessing the Fourth Industrial Revolution, characterized by the fusion of advanced technologies such as artificial intelligence, the Internet of Things (IoT), and additive manufacturing (3D printing). These innovations are reshaping the manufacturing landscape, prompting companies to invest heavily in digital transformation to remain competitive.
Economic and Technological Influences
Economic and technological factors play a significant role in shaping capital investment decisions in manufacturing. Economic conditions, such as interest rates, inflation, and market demand, directly influence a company's ability to invest in new assets. During periods of economic growth, manufacturers are more likely to increase capital spending to expand production capacity and explore new markets. Conversely, during economic downturns, companies may adopt a more cautious approach, focusing on maintaining existing assets and optimizing operational efficiency.
Technological advancements are another major driver of capital investment in manufacturing. The rapid pace of innovation in areas such as automation, robotics, and digitalization presents both opportunities and challenges for manufacturers. Companies must continually evaluate emerging technologies and determine how they can be integrated into their operations to enhance productivity and reduce costs. For example, the adoption of IoT solutions can provide real-time data analytics, enabling manufacturers to optimize production processes and improve decision-making.
In conclusion, understanding capital investment in manufacturing requires a comprehensive view of its definition, historical evolution, and the economic and technological factors that influence it. As manufacturing continues to evolve in response to changing market dynamics and technological advancements, capital investment will remain a critical component of strategic decision-making, driving efficiency and innovation across the industry.
Applications of capital investment in manufacturing
Modernizing manufacturing operations
Modernizing manufacturing operations
Capital investments are crucial for modernizing manufacturing operations, enabling companies to stay ahead of the competition and meet evolving customer demands. One of the primary applications of capital investment is in upgrading outdated machinery and equipment. By investing in state-of-the-art technology, manufacturers can improve production efficiency, reduce downtime, and increase output. For example, a study by Deloitte revealed that firms investing in modern manufacturing technologies experienced a 20% increase in productivity and a 15% reduction in production costs.
Another key area where capital investments are applied is in the implementation of automation technologies. Automation can streamline repetitive tasks, reduce human error, and enhance the overall quality of products. For instance, a leading automotive manufacturer invested in robotic assembly lines, which not only improved production speed but also ensured consistent quality in the manufacturing process. By automating routine tasks, companies can free up human resources to focus on more strategic and value-added activities.
Sustainable manufacturing practices
Sustainable manufacturing practices
In recent years, there has been a growing emphasis on sustainability in manufacturing, prompting companies to invest in eco-friendly technologies and practices. Capital investments in sustainable manufacturing can help reduce environmental impact, comply with regulatory standards, and enhance brand reputation. For instance, many manufacturers are investing in renewable energy sources, such as solar and wind, to power their facilities. This not only reduces carbon emissions but also lowers energy costs over the long term.
Furthermore, investments in energy-efficient machinery and waste reduction technologies can lead to significant cost savings and environmental benefits. A case in point is a consumer goods manufacturer that invested in energy-efficient production lines and waste recycling systems. As a result, the company achieved a 30% reduction in energy consumption and a 25% decrease in waste generation, demonstrating the positive impact of capital investments on sustainability.
Case studies of successful capital investment strategies
Case studies of successful capital investment strategies
To illustrate the effectiveness of capital investment strategies in manufacturing, let's explore a few real-world case studies. One notable example is a global electronics manufacturer that invested in advanced data analytics and IoT solutions to optimize its supply chain operations. By leveraging these technologies, the company achieved a 40% reduction in lead times and a 20% improvement in supply chain visibility, resulting in enhanced customer satisfaction.
Another successful case involves a pharmaceutical company that invested in additive manufacturing technologies to streamline its drug production processes. By adopting 3D printing for drug formulation, the company was able to accelerate the development of new products and reduce manufacturing costs. This investment not only improved operational efficiency but also positioned the company as an industry leader in innovation.
Related:
ITILClick here to read our expertly curated top picks!
Challenges and solutions
Common Challenges in Implementing Capital Investment Strategies
Implementing effective capital investment strategies in manufacturing is not without its challenges. One of the most common obstacles faced by companies is financial constraints. Capital investments often require substantial upfront funding, which can be a barrier for small and medium-sized enterprises (SMEs) with limited access to capital. Additionally, the long payback periods associated with certain investments can deter companies from committing to large-scale projects.
Another significant challenge is technological uncertainty. The rapid pace of technological advancements can make it difficult for manufacturers to choose the right solutions for their operations. Investing in the wrong technology or failing to adapt to new trends can lead to wasted resources and missed opportunities. Moreover, integrating new technologies into existing systems can be complex and costly, requiring careful planning and execution.
Operational challenges also arise during the implementation of capital investment strategies. These may include disruptions to production processes, the need for employee training, and resistance to change from within the organization. Managing these operational hurdles is critical to ensuring the successful execution of capital investment projects.
Solutions to Financial, Technological, and Operational Hurdles
Addressing the challenges associated with capital investment in manufacturing requires a strategic and multifaceted approach. To overcome financial constraints, companies can explore various financing options, such as leasing, government grants, and partnerships with investors. Additionally, conducting a thorough cost-benefit analysis can help identify investments with the highest potential return, allowing companies to allocate resources more effectively.
To navigate technological uncertainty, manufacturers should prioritize investments in flexible and scalable technologies that can adapt to changing market demands. Collaborating with technology providers and industry experts can provide valuable insights into emerging trends and best practices. Furthermore, companies should invest in comprehensive training programs to ensure employees are equipped with the skills needed to operate new technologies effectively.
Operational challenges can be mitigated through careful planning and change management strategies. Engaging employees in the decision-making process and communicating the benefits of capital investments can help alleviate resistance to change. Additionally, implementing pilot projects and phased rollouts can minimize disruptions to production and allow for adjustments based on real-world feedback.
Strategic Approaches to Mitigate Risks
Risk management is a crucial aspect of capital investment in manufacturing. To mitigate risks, companies should adopt a proactive approach to identifying potential challenges and developing contingency plans. This includes conducting thorough market research to assess demand and competitive dynamics, as well as evaluating the potential impact of external factors such as regulatory changes and economic fluctuations.
Furthermore, companies should diversify their investment portfolios to spread risk across multiple projects and technologies. This approach not only reduces the likelihood of significant financial losses but also increases the chances of identifying successful investment opportunities. Regularly reviewing and adjusting investment strategies based on performance metrics and market trends is essential to maintaining a competitive edge.
In conclusion, while challenges are inherent in implementing capital investment strategies in manufacturing, they can be effectively addressed through strategic planning, financial management, and risk mitigation. By adopting a comprehensive and proactive approach, manufacturers can unlock the full potential of capital investments to drive efficiency, innovation, and long-term growth.
Best practices for capital investment in manufacturing
Industry-Recommended Approaches
To optimize capital investment in manufacturing, companies should adhere to industry-recommended best practices that have been proven effective across various sectors. One such practice is aligning capital investment decisions with the company's strategic goals and objectives. By ensuring that investments support overall business priorities, manufacturers can maximize their impact and achieve a higher return on investment.
Another best practice is conducting a thorough analysis of the current market and competitive landscape before making investment decisions. This involves assessing trends, customer preferences, and emerging technologies to identify opportunities for growth and differentiation. By staying informed about industry developments, companies can make well-informed investment choices that position them ahead of the competition.
Tips from Seasoned Project Managers
Experienced project managers offer valuable insights into optimizing capital investments in manufacturing. One key tip is to involve cross-functional teams in the investment decision-making process. By engaging stakeholders from various departments, companies can gain diverse perspectives and ensure that investments address the needs and challenges of the entire organization. This collaborative approach fosters buy-in and enhances the likelihood of successful implementation.
Project managers also emphasize the importance of robust project management methodologies to oversee capital investment initiatives. This includes setting clear objectives, defining key performance indicators (KPIs), and establishing timelines and budgets. Regular monitoring and evaluation of project progress enable companies to make timely adjustments and ensure investments remain on track to deliver the desired outcomes.
Ensuring Long-Term Benefits
To ensure sustainable and long-term benefits from capital investments, manufacturers should focus on continuous improvement and innovation. This involves regularly reviewing and optimizing investment strategies based on performance data and feedback from stakeholders. By embracing a culture of continuous improvement, companies can identify areas for enhancement and implement changes that drive ongoing efficiency gains.
Additionally, manufacturers should prioritize investments in technologies that offer scalability and adaptability. As market conditions and customer demands evolve, flexible technologies can be easily adjusted to meet new requirements, ensuring that investments remain relevant and valuable over time. Building strong partnerships with technology providers and industry experts can also facilitate access to the latest innovations and best practices.
In summary, adopting best practices for capital investment in manufacturing involves aligning investments with strategic goals, engaging cross-functional teams, and leveraging robust project management methodologies. By focusing on continuous improvement and scalable technologies, manufacturers can achieve sustainable and long-term benefits that drive efficiency, innovation, and growth.
Click here to read our expertly curated top picks!
Software and tools enhancing capital investment
Overview of Essential Software and Tools
In the modern manufacturing landscape, the integration of advanced software and tools is essential to facilitate effective capital investment strategies. These technologies enable manufacturers to streamline processes, enhance decision-making, and optimize resource allocation. One critical tool is Enterprise Resource Planning (ERP) software, which provides a comprehensive platform for managing various aspects of manufacturing operations, including inventory, production, and financials. By centralizing data and providing real-time insights, ERP systems empower companies to make informed investment decisions and monitor the performance of capital assets.
Another essential tool is Manufacturing Execution Systems (MES), which bridge the gap between production planning and execution. MES solutions provide real-time visibility into production processes, enabling manufacturers to track performance, identify bottlenecks, and implement corrective actions swiftly. By optimizing production efficiency, MES systems enhance the return on capital investments and contribute to overall operational excellence.
Benefits of Integrating Advanced Technology
Integrating advanced technology with capital investment strategies offers numerous benefits for manufacturers. One of the primary advantages is improved data analytics and decision-making capabilities. Advanced analytics tools can process vast amounts of data from various sources, providing manufacturers with actionable insights into production, supply chain, and market trends. This data-driven approach enables companies to identify opportunities for optimization and make strategic investment decisions that drive efficiency and innovation.
Furthermore, integrating technology enhances flexibility and scalability in manufacturing operations. By adopting modular and adaptable solutions, manufacturers can quickly adjust to changing market conditions and customer demands. For example, IoT-enabled sensors and devices can monitor equipment performance in real-time, allowing for predictive maintenance and reducing downtime. This proactive approach ensures that capital investments are utilized efficiently and deliver maximum value.
Selecting the Right Software for Manufacturing Needs
Choosing the right software and tools is critical to maximizing the benefits of capital investments in manufacturing. Companies should consider several factors when selecting technology solutions, including their specific operational needs, budget constraints, and long-term strategic goals. Conducting a thorough needs assessment and involving key stakeholders in the selection process can help identify the most suitable solutions for the organization.
Additionally, manufacturers should prioritize software solutions that offer seamless integration with existing systems and processes. Compatibility with current infrastructure minimizes disruptions and facilitates a smooth transition to new technologies. Furthermore, companies should seek vendors with a proven track record of delivering reliable and scalable solutions, as well as comprehensive support and training services.
In conclusion, leveraging essential software and tools is crucial for enhancing capital investment strategies in manufacturing. By integrating advanced technology, manufacturers can improve decision-making, optimize resource allocation, and ensure flexibility and scalability in operations. Careful selection and implementation of the right software solutions can drive efficiency, innovation, and long-term growth in the manufacturing sector.
Future outlook on capital investment in manufacturing
Emerging Trends and Predictions
As the manufacturing industry continues to evolve, several emerging trends and predictions are shaping the future of capital investment strategies. One of the most significant trends is the increasing adoption of Industry 4.0 technologies, which encompass a range of digital innovations, including the Internet of Things (IoT), artificial intelligence (AI), and machine learning. These technologies are transforming manufacturing processes by enabling real-time data analysis, predictive maintenance, and autonomous decision-making. According to a report by McKinsey & Company, Industry 4.0 adoption could boost manufacturing productivity by up to 30%, underscoring its potential impact on capital investment.
Another trend is the growing focus on sustainability and circular economy practices. Manufacturers are increasingly investing in eco-friendly technologies and processes to reduce their environmental footprint and meet regulatory requirements. This shift towards sustainable manufacturing is driven by both consumer demand and the need to mitigate the impact of climate change. Capital investments in renewable energy, energy-efficient machinery, and waste reduction technologies are expected to increase significantly in the coming years.
Impact of Technological Advancements
Technological advancements are playing a crucial role in shaping the future of capital investment in manufacturing. The integration of AI and machine learning is revolutionizing production processes by enabling predictive analytics and intelligent automation. For example, AI-powered algorithms can analyze historical production data to identify patterns and optimize production schedules, reducing downtime and improving efficiency. This level of automation not only enhances productivity but also allows manufacturers to respond more swiftly to changing market demands.
Additionally, the rise of additive manufacturing (3D printing) is transforming the manufacturing landscape by enabling rapid prototyping, customization, and on-demand production. Capital investments in 3D printing technologies are expected to grow as manufacturers seek to leverage its benefits, including reduced lead times and material waste. The ability to produce complex and customized parts with minimal tooling is a game-changer for industries such as aerospace, automotive, and healthcare.
Preparing for the Future
To stay competitive and innovative in the future, manufacturers must proactively prepare for the evolving landscape of capital investment. This involves staying informed about emerging trends and technologies, as well as continuously assessing their potential impact on operations. Engaging with industry experts, attending conferences, and participating in collaborative networks can provide valuable insights and help companies stay ahead of the curve.
Furthermore, manufacturers should prioritize investments in flexible and scalable technologies that can adapt to changing market conditions. Building strong partnerships with technology providers and industry leaders can facilitate access to cutting-edge innovations and best practices. By fostering a culture of continuous improvement and innovation, companies can ensure that their capital investments drive long-term growth and competitiveness.
In summary, the future of capital investment in manufacturing is characterized by the adoption of Industry 4.0 technologies, a focus on sustainability, and the transformative impact of technological advancements. By preparing for these trends and investing in flexible and scalable solutions, manufacturers can position themselves for success in an increasingly dynamic and competitive industry.
Click here to read our expertly curated top picks!
Examples of capital investment in manufacturing
Implementation of automation technologies
Implementation of automation technologies
One compelling example of capital investment in manufacturing is the implementation of automation technologies by a leading automotive manufacturer. Facing rising labor costs and increased demand for high-quality vehicles, the company decided to invest in robotic assembly lines at its production facility. This strategic move not only streamlined the manufacturing process but also significantly improved product quality and consistency. By automating repetitive and labor-intensive tasks, the company was able to reduce production time by 30% and achieve a 20% increase in output capacity. This investment not only enhanced operational efficiency but also positioned the manufacturer as a leader in innovation within the automotive industry.
Sustainable manufacturing practices
Sustainable manufacturing practices
Another noteworthy example involves a consumer goods manufacturer that prioritized sustainability through capital investment. Recognizing the growing importance of environmental responsibility, the company invested in renewable energy sources and energy-efficient machinery for its production facilities. By installing solar panels and upgrading to energy-efficient equipment, the manufacturer achieved a remarkable 40% reduction in energy consumption and a 30% decrease in carbon emissions. Additionally, the company implemented waste reduction technologies, leading to a 25% reduction in waste generation. These sustainability-focused investments not only contributed to cost savings but also enhanced the company's brand reputation and compliance with environmental regulations.
Expansion into new markets
Expansion into new markets
A third example illustrates the strategic use of capital investment for market expansion. A global electronics manufacturer sought to diversify its product offerings and enter new markets. To achieve this, the company allocated significant capital towards research and development (R&D) and the establishment of new manufacturing facilities. By investing in state-of-the-art equipment and advanced technologies, the company was able to develop innovative products tailored to the specific needs of new markets. This strategic expansion resulted in a 50% increase in revenue and a strengthened global presence. The successful execution of this capital investment strategy not only enhanced the company's market share but also positioned it as a leader in product innovation.
Click here to read our expertly curated top picks!
Tips for do's and don'ts
Do's | Don'ts |
---|---|
Conduct thorough market research | Ignore the need for a detailed financial plan |
Invest in employee training | Overlook the importance of technology integration |
Regularly review and adjust investments | Set unrealistic expectations for ROI |
Related:
ITILClick here to read our expertly curated top picks!
Conclusion
In conclusion, capital investment in manufacturing is a critical driver of efficiency, innovation, and long-term growth. By strategically allocating resources towards modernization, sustainability, and market expansion, manufacturers can achieve significant improvements in productivity, cost-efficiency, and competitiveness. Throughout this article, we have explored the importance of capital investment, the challenges and solutions associated with implementation, and industry-recommended best practices for optimizing investments. By leveraging advanced technologies and tools, manufacturers can enhance decision-making, resource allocation, and flexibility, ensuring that investments deliver maximum value.
As manufacturing continues to evolve in response to changing market dynamics and technological advancements, capital investment will remain a vital component of strategic decision-making. We encourage manufacturing professionals to embrace the strategies discussed in this article and implement them to optimize their operations and drive innovation. By staying informed about emerging trends and preparing for the future, manufacturers can position themselves for success in an increasingly dynamic and competitive industry.
Further resources
For those looking to deepen their understanding of capital investment in manufacturing, several additional resources and opportunities for professional development are available. Online platforms such as Coursera, edX, and LinkedIn Learning offer courses and certifications on capital investment strategies and industry best practices. These resources provide valuable insights into the latest trends and technologies shaping the manufacturing sector.
Industry conferences and workshops offer opportunities to learn from experts and network with peers. Events such as the Manufacturing Leadership Summit and the Smart Manufacturing Experience provide valuable insights into emerging trends and innovations in capital investment. Engaging with these platforms can enhance knowledge and expertise in capital investment in manufacturing.
Professional bodies, such as the Project Management Institute (PMI) and the Association for Manufacturing Excellence (AME), offer resources, webinars, and forums for ongoing learning and development. These organizations provide a wealth of information on best practices, case studies, and industry standards, helping professionals stay informed and competitive in the field.
By leveraging these resources and opportunities for professional development, manufacturing professionals can enhance their expertise in capital investment and drive efficiency and innovation in their organizations.
Experience the next level of project management today!
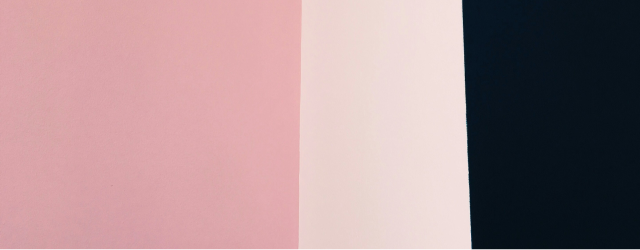
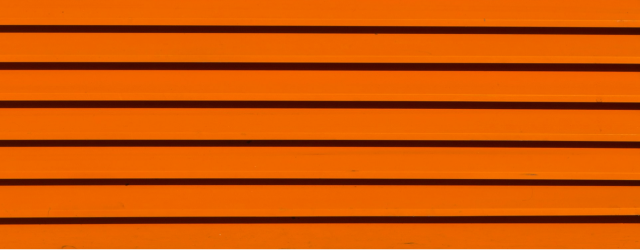
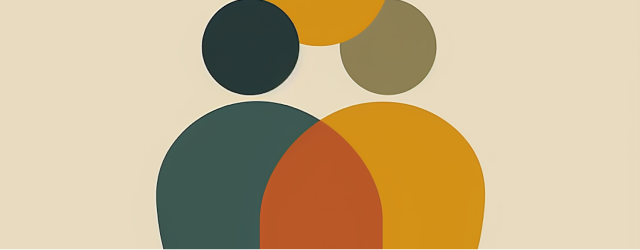
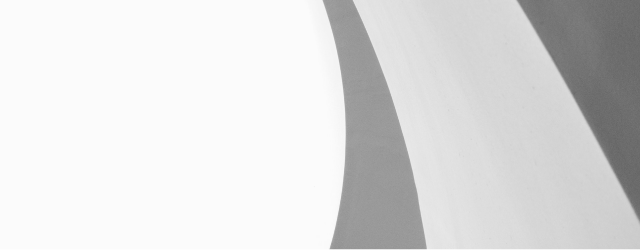
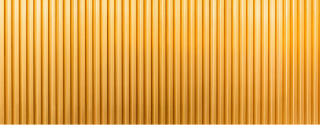
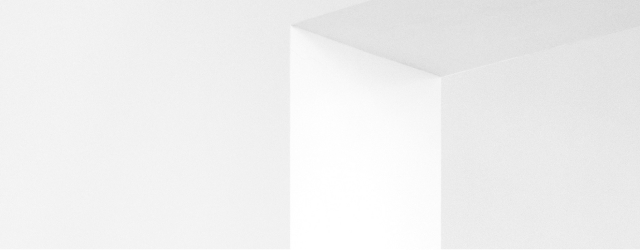
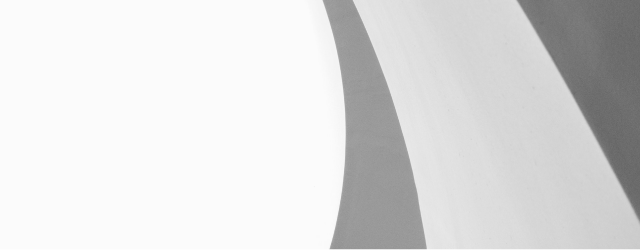
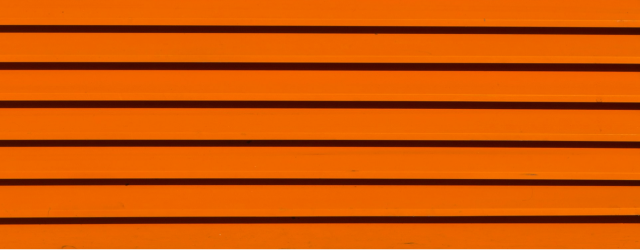