Cost-Reduction Strategies In Manufacturing
Dive into our expertly crafted article exploring Cost-Reduction Strategies in Manufacturing, where you'll get in-depth insights, practical applications, and industry best practices tailored for hardware enthusiasts and professionals.
In the fast-paced world of manufacturing, cost-reduction strategies have emerged as a critical component of maintaining competitive advantage and ensuring long-term sustainability. The manufacturing sector is a cornerstone of global economies, contributing significantly to employment and GDP. However, with increasing globalization, competition has intensified, pushing manufacturers to seek new ways of reducing costs without compromising on quality. This environment has propelled cost-reduction strategies to the forefront of operational priorities. By effectively managing costs, manufacturers can not only improve their profit margins but also reinvest in technology and innovation, thereby further enhancing their competitive edge. This article provides an in-depth exploration of cost-reduction strategies in manufacturing, highlighting their transformative potential and offering actionable insights for industry professionals.
Experience the next level of project management today!
Understanding cost-reduction strategies in manufacturing
Defining Cost-Reduction Strategies
Cost-reduction strategies in manufacturing encompass a range of systematic efforts aimed at decreasing the expenses associated with production processes. These strategies are designed to enhance efficiency across the supply chain, minimize wastage, improve resource utilization, and ultimately, reduce the cost per unit of production. At their core, these strategies challenge existing processes and encourage a culture of continuous improvement.
Historical Context and Evolution
Historically, cost-reduction strategies in manufacturing have evolved alongside industrial advancements. The dawn of the industrial revolution marked the beginning of formalized manufacturing processes, where the primary focus was on maximizing output. As industries matured, the emphasis shifted toward optimizing processes to reduce costs. The introduction of the assembly line by Henry Ford in the early 20th century is a seminal example of cost reduction through process innovation. Ford's method drastically cut down manufacturing time and costs, setting a precedent for future strategies.
Principles and Modern Relevance
The fundamental principles of cost-reduction strategies involve simplifying processes, eliminating waste, and enhancing productivity. In today’s economy, these strategies have gained more relevance due to rising raw material costs, labor shortages, and increasing competition. By implementing cost-reduction strategies, manufacturers can mitigate these challenges, ensuring they remain agile and responsive to market demands. Moreover, the advent of digital technologies and Industry 4.0 has provided manufacturers with new tools to enhance cost-efficiency through data analytics, automation, and real-time monitoring.
Key elements of cost-reduction strategies
Lean Manufacturing
Lean manufacturing is a pivotal element of cost-reduction strategies, focusing on minimizing waste within manufacturing systems while simultaneously maximizing productivity. Originating from the Japanese automotive industry, particularly Toyota, lean manufacturing involves principles such as Just-In-Time (JIT) production, where materials are only ordered and received as they are needed in the production process. This reduces inventory costs and minimizes waste. By adopting lean manufacturing, companies can streamline operations, reduce lead times, and improve overall efficiency.
Waste Reduction
Waste reduction is another crucial element in cost-reduction strategies. Waste in manufacturing can take many forms, including excess inventory, overproduction, defects, and inefficient processes. Implementing systematic approaches like the 5S methodology—Sort, Set in order, Shine, Standardize, and Sustain—helps in organizing the workplace, which reduces waste and enhances productivity. Furthermore, using tools like Value Stream Mapping (VSM) enables manufacturers to visualize waste and optimize the flow of materials and information.
Process Optimization and the Role of Technology
Process optimization involves refining manufacturing processes to achieve the most efficient outcomes. This can include re-engineering workflows, integrating advanced technologies, and automating routine tasks. The role of technology in cost-reduction is significant. Automation and robotics can handle repetitive tasks with greater accuracy and efficiency, reducing labor costs and minimizing errors. Additionally, digital twins and predictive analytics offer insights into process efficiencies and potential bottlenecks, enabling proactive adjustments that can lead to substantial cost savings.
Related:
4K GamingClick here to read our expertly curated top picks!
Applications of cost-reduction strategies in manufacturing
Implementation across manufacturing scenarios
Implementation across manufacturing scenarios
Cost-reduction strategies can be effectively applied across a wide array of manufacturing scenarios, each with its unique set of challenges and opportunities. By customizing these strategies to fit specific industry needs, manufacturers can achieve significant cost savings while maintaining high-quality standards.
Case study: lean manufacturing at toyota
Case study: lean manufacturing at toyota
A classic example of successful cost-reduction implementation is Toyota's adoption of lean manufacturing. By focusing on eliminating waste and optimizing processes, Toyota has consistently reduced production costs and improved efficiency. This approach, known as the Toyota Production System (TPS), emphasizes continuous improvement and respect for people, creating a culture of efficiency and innovation that has become a benchmark in the automotive industry.
Adaptability across different sectors
Adaptability across different sectors
Cost-reduction strategies are not limited to any single industry. For instance, in the pharmaceutical sector, companies have implemented lean principles to streamline operations and reduce manufacturing cycle times, resulting in lower costs and faster time-to-market for new products. Similarly, in the consumer electronics industry, manufacturers have leveraged waste reduction techniques to enhance production efficiency and reduce e-waste, aligning cost savings with environmental sustainability.
Detailed examples of cost-reduction strategies
Example 1: lean manufacturing in automotive industry
Example 1: lean manufacturing in automotive industry
Lean manufacturing has revolutionized the automotive industry, with companies like Ford and Toyota leading the charge. By adopting lean principles, automotive manufacturers have significantly reduced costs and improved efficiency. For instance, Ford's assembly line innovations decreased the time required to build a car from over 12 hours to just 93 minutes. This dramatic reduction in production time translated into substantial cost savings, allowing Ford to offer vehicles at a lower price point while maintaining profit margins. The lean approach also emphasizes quality, ensuring that cost reductions do not compromise vehicle safety or performance.
Example 2: waste reduction in electronics manufacturing
Example 2: waste reduction in electronics manufacturing
In the electronics manufacturing sector, waste reduction strategies have yielded significant environmental and economic benefits. Companies like Apple have set ambitious goals to eliminate waste from their production processes. By implementing closed-loop supply chains, Apple recycles materials from old devices to create new products, reducing the need for raw materials and minimizing waste. This approach not only cuts costs but also enhances environmental sustainability, a critical factor as consumers increasingly prioritize eco-friendly products. The cost savings achieved through waste reduction have enabled electronics manufacturers to invest in innovation, further driving industry growth.
Example 3: process optimization in food processing
Example 3: process optimization in food processing
The food processing industry has embraced process optimization techniques to enhance efficiency and reduce costs. Companies like Nestlé have implemented advanced manufacturing technologies to streamline production and improve resource utilization. For example, Nestlé's use of predictive analytics allows for precise control over production processes, minimizing waste and reducing energy consumption. These optimizations have resulted in significant cost savings, enabling companies to offer competitive pricing while maintaining product quality. By leveraging technology for process optimization, food manufacturers can efficiently scale operations to meet rising consumer demand.
Related:
4K GamingClick here to read our expertly curated top picks!
Challenges and solutions
Common Challenges in Implementing Cost-Reduction Strategies
Implementing cost-reduction strategies in manufacturing is not without its challenges. One common hurdle is organizational resistance to change. Employees and management may be reluctant to adopt new processes or technologies, fearing disruptions to established workflows. Additionally, the initial costs associated with implementing new strategies, such as investing in advanced technologies or training personnel, can be a deterrent for some companies.
Practical Solutions and Strategic Approaches
To overcome these challenges, it is essential to adopt a strategic approach. Engaging all stakeholders in the planning and implementation process fosters buy-in and support from employees and management alike. Training programs and workshops can help demystify new processes, alleviating fears and building confidence in their effectiveness. Furthermore, presenting a clear ROI for cost-reduction initiatives can justify the initial investment, demonstrating long-term benefits for the organization.
Addressing Organizational Resistance
Organizational resistance can be mitigated through effective change management practices. By communicating the benefits of cost-reduction strategies and involving employees in decision-making, companies can create a culture of continuous improvement. Encouraging feedback and suggestions from employees can also foster a sense of ownership and accountability, driving successful implementation of cost-reduction efforts.
Best practices for implementing cost-reduction strategies
Recommended Best Practices
To maximize the benefits of cost-reduction strategies, it is crucial to follow best practices that align with industry standards. One key practice is to focus on long-term savings rather than short-term gains. This involves investing in technologies and processes that offer sustainable cost reductions over time. Additionally, engaging all stakeholders in the implementation process ensures that cost-reduction efforts are comprehensive and effective.
Insights from Industry Experts
Industry experts emphasize the importance of continuous monitoring and evaluation of cost-reduction strategies. By regularly assessing performance metrics and making adjustments as needed, companies can ensure that their strategies remain aligned with business objectives. Moreover, fostering a culture of innovation and adaptability enables organizations to respond to changing market conditions and emerging trends, further enhancing cost-efficiency.
Continuous Improvement and Sustainability
Sustainability is a key component of successful cost-reduction strategies. By adopting a mindset of continuous improvement, companies can refine processes and identify new opportunities for cost savings. This approach not only enhances operational efficiency but also supports environmental sustainability, aligning with the growing demand for eco-friendly manufacturing practices.
Related:
Critical Path Method (CPM)Click here to read our expertly curated top picks!
Software and tools for cost-reduction
Overview of Software and Tools
In the digital age, software and tools play a crucial role in the successful implementation of cost-reduction strategies. These technologies enable manufacturers to streamline operations, optimize resource utilization, and enhance decision-making processes. Popular tools include Enterprise Resource Planning (ERP) systems, which integrate various business functions and provide real-time data for efficient management.
Benefits of Recommended Software
ERP systems offer several benefits for cost-reduction efforts, including improved data accuracy, enhanced collaboration, and streamlined processes. By providing a comprehensive view of operations, ERP systems enable manufacturers to identify inefficiencies and implement targeted improvements. Additionally, predictive analytics tools can forecast demand patterns, optimize inventory levels, and reduce excess stock, further contributing to cost savings.
Tips for Choosing the Right Software
When selecting software for cost-reduction, it is important to consider specific manufacturing needs and objectives. Factors such as scalability, ease of integration, and user-friendliness should be evaluated to ensure the chosen software aligns with the organization's goals. Consulting with industry experts and conducting thorough research can also aid in making informed decisions that drive successful cost-reduction outcomes.
Related:
Game User Interface DesignClick here to read our expertly curated top picks!
Do's and don'ts of cost-reduction strategies
Do's | Don'ts |
---|---|
Focus on long-term savings | Sacrifice quality for cost |
Engage all stakeholders | Ignore employee feedback |
Continuously monitor progress | Set and forget strategies |
Future outlook of cost-reduction strategies in manufacturing
Future Trends in Cost-Reduction
As manufacturing continues to evolve, future trends in cost-reduction are anticipated to be driven by emerging technologies and changing consumer preferences. The integration of artificial intelligence (AI) and machine learning is expected to revolutionize cost-reduction efforts by enhancing predictive capabilities and optimizing resource allocation. Additionally, the rise of the Internet of Things (IoT) will enable real-time data collection and analysis, further improving operational efficiency.
Influence of Emerging Technologies
Emerging technologies such as blockchain and additive manufacturing (3D printing) are poised to impact cost-reduction strategies significantly. Blockchain technology offers enhanced transparency and traceability in supply chains, reducing the risk of fraud and inefficiencies. Meanwhile, additive manufacturing allows for on-demand production and customization, minimizing waste and reducing inventory costs.
Staying Updated and Competitive
To stay competitive in the future, manufacturers must remain agile and adaptable, continuously updating their cost-reduction strategies to align with industry advancements. Investing in employee training and development ensures that the workforce is equipped with the skills needed to leverage new technologies effectively. By fostering a culture of innovation and continuous improvement, companies can maintain a competitive edge in the ever-evolving manufacturing landscape.
Click here to read our expertly curated top picks!
Conclusion
In conclusion, cost-reduction strategies are a vital component of achieving manufacturing excellence and maintaining competitive advantage in today's dynamic business environment. By understanding and implementing these strategies, manufacturers can optimize processes, reduce waste, and enhance efficiency, leading to substantial cost savings. The integration of advanced technologies and continuous improvement practices further amplifies the impact of cost-reduction efforts. As the manufacturing landscape continues to evolve, staying updated on emerging trends and fostering a culture of innovation will be key to sustaining success. Embrace these insights and take action to revolutionize your manufacturing process for a brighter, more efficient future.
Related:
AI In Finance And BankingClick here to read our expertly curated top picks!
Experience the next level of project management today!
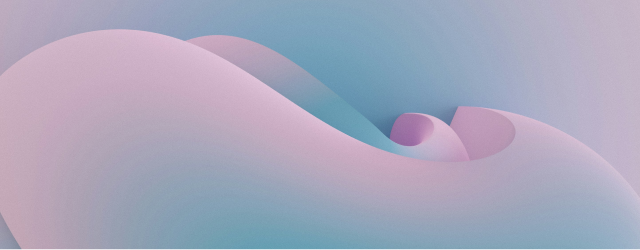
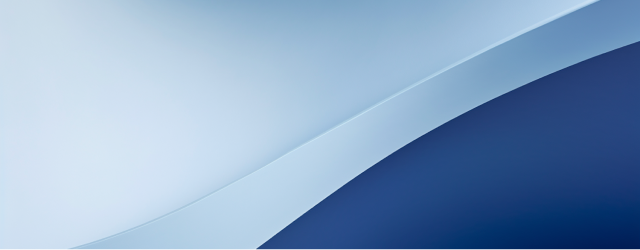
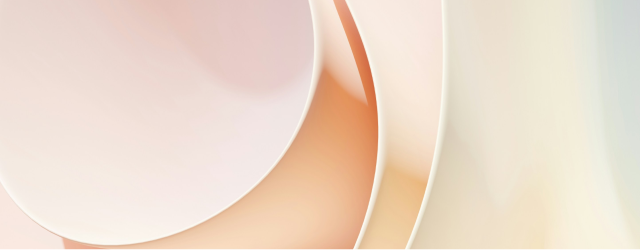
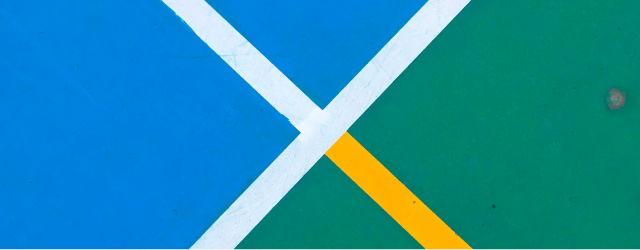
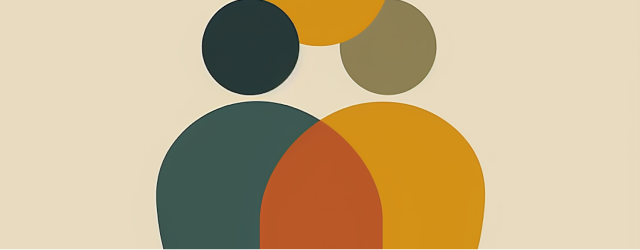
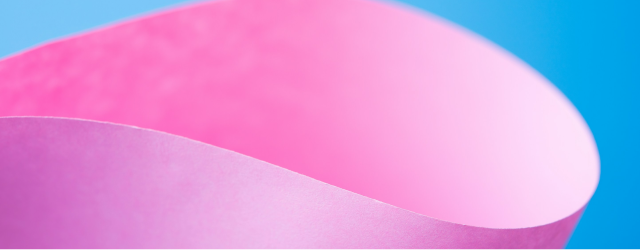
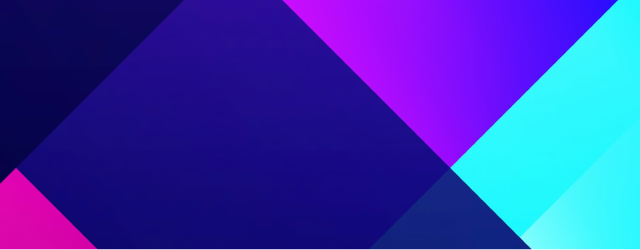
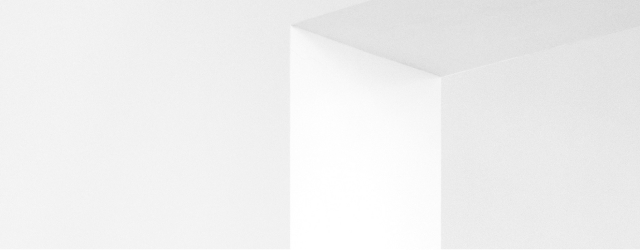