Thermal Treatments For Metals
Dive into our expertly crafted article exploring Thermal Treatments for Metals, where you'll get in-depth insights, practical applications, and industry best practices tailored for hardware enthusiasts and professionals.
In the realm of metal manufacturing, thermal treatments play an indispensable role in enhancing the properties of metals and alloys. Rigorous heat treatments can improve hardness, ductility, and resistance to wear and corrosion, thereby extending the lifespan and performance of manufactured products. This comprehensive guide aims to provide professionals and aspiring project managers with a robust understanding of thermal treatments for metals in manufacturing, their applications, challenges, best practices, as well as futuristic trends. So, let's embark on this enlightening journey and unravel the potent capabilities of thermal treatments in metal manufacturing.
Experience the next level of project management today!
Understanding thermal treatments for metals
Thermal treatment, also known as heat treatment, is a controlled process used to alter the physical and sometimes chemical properties of a material, most commonly metals and alloys. From the earliest blacksmiths to today's cutting-edge manufacturing facilities, thermal treatments have been instrumental in shaping, strengthening, and refining metals.
Historically, blacksmiths harnessed the power of fire and water to heat and cool metals, altering their properties to create durable tools and weapons. Today, we use more sophisticated methods and technologies, but the fundamental principle remains the same - changing the properties of metal through the controlled application of heat.
Thermal treatment processes generally involve three steps: heating, holding (soaking), and cooling. The heating phase involves raising the material's temperature to a specific point, while the soaking phase maintains that temperature for a set period. The cooling phase then brings the material back to room temperature at a controlled rate. Each of these phases can be manipulated to achieve different desired properties, making thermal treatment a versatile tool in the manufacturing industry.
Applications of thermal treatments for metals
Thermal treatments find widespread applications across the manufacturing landscape. In automobile manufacturing, for instance, thermal treatments are used to improve the hardness and strength of engine parts, leading to more durable and efficient vehicles.
Consider the case of Toyota Motor Corporation. To increase the longevity of their vehicle parts, Toyota implemented thermal treatments in their manufacturing process. The results were impressive, with a significant increase in the lifespan of parts and a corresponding reduction in maintenance costs.
In the aerospace industry, thermal treatments are used to increase the resistance of airplane parts to extreme temperatures and pressures. Heat-treated metals can withstand the rigorous conditions of outer space, making them an integral part of spacecraft manufacturing.
Airbus, one of the world's leading airplane manufacturers, leverages thermal treatments to enhance the robustness and durability of their aircraft. This application of thermal treatments contributes to the safety, reliability, and efficiency of Airbus planes, underscoring the importance of thermal treatments in the manufacturing process.
Related:
Agile Unified Process (AUP)Click here to read our expertly curated top picks!
Challenges and solutions in implementing thermal treatments
While thermal treatments offer numerous benefits, their implementation is not without challenges. One common problem is maintaining consistent heat treatment conditions. Variations in temperature or duration can lead to inconsistencies in the finished product, hampering quality and performance.
To overcome this issue, manufacturers can employ advanced monitoring and control systems that maintain precise control over heat treatment conditions. By ensuring consistent temperature and duration, these systems can significantly enhance the consistency and quality of the final product.
Another challenge is the energy cost associated with heat treatment processes. High energy consumption can make thermal treatments expensive and less environmentally friendly. However, implementing energy-efficient practices and technologies can mitigate this issue. For instance, using heat recovery systems can capture and reuse heat, reducing energy consumption and costs.
Maximizing efficiency: best practices for thermal treatments
To maximize the efficiency and effectiveness of thermal treatments, certain best practices are recommended. Regular equipment maintenance is crucial to ensure optimal performance and prevent breakdowns. Moreover, using high-quality materials can enhance the results of heat treatment processes, resulting in superior products.
Leading industry expert, Dr. John Baxter, emphasizes the importance of continuous learning and training in this field. He states, "Understanding the science behind thermal treatments, staying updated with new technologies, and regular personnel training can make a significant difference in the quality and efficiency of thermal treatments."
It's also vital to closely monitor and control the heat treatment process. Advanced monitoring systems that provide real-time data on temperature, duration, and other essential parameters can help maintain high-quality standards and prevent defects.
Click here to read our expertly curated top picks!
Leveraging software and tools for thermal treatments
The advent of digital technologies has introduced a range of software and tools that aid in the implementation and monitoring of thermal treatments. Software like Thermo-Calc, JMatPro, and MTData provide critical insights into the effects of different heat treatment conditions, helping manufacturers optimize their processes.
These software solutions offer a host of benefits such as accurate predictions of phase transformations, simulations of heat treatment processes, and data analysis for informed decision-making. When choosing a software solution, manufacturers should consider factors like user-friendliness, compatibility with existing systems, and the level of technical support provided.
The future of thermal treatments: trends and technologies
The future looks promising for thermal treatments in the manufacturing sector. Emerging technologies like nanotechnology and additive manufacturing are set to revolutionize the way we understand and apply heat treatments.
Nanotechnology, for instance, can enable more precise control over the heating and cooling processes, leading to superior quality products. On the other hand, additive manufacturing, often known as 3D printing, can benefit from thermal treatments to improve the properties of printed parts.
Related:
Gaming API IntegrationClick here to read our expertly curated top picks!
Faqs on thermal treatments for metals
What are the basic requirements for implementing thermal treatments?
The basic requirements include a heat source, a controlled environment for the process, and skilled personnel to manage the operation. It's also vital to have a reliable system for monitoring and controlling the process parameters.
Are thermal treatments cost-efficient?
While thermal treatments can be energy-intensive, the increased quality and lifespan of the treated products often justify the costs. Moreover, implementing energy-efficient practices can significantly reduce costs.
Can thermal treatments be integrated with existing manufacturing systems?
Yes, thermal treatments can often be integrated with existing systems. However, this requires careful planning and potentially some modifications to the existing setup.
What are common mistakes in implementing thermal treatments?
Common mistakes include inconsistent heat treatment conditions, inadequate monitoring, and lack of regular maintenance. These can be mitigated through careful planning, regular training, and the use of advanced monitoring systems.
Where can I learn more about thermal treatments for metals?
Numerous online resources, books, and courses offer in-depth knowledge on thermal treatments. Professional bodies like the American Society for Metals (ASM) also provide valuable resources and training programs.
Conclusion
In conclusion, thermal treatments for metals are a cornerstone of quality and efficiency in the manufacturing sector. By understanding and properly implementing these processes, manufacturers can improve the properties of their products, enhance their durability, and ultimately deliver more value to their customers.
Click here to read our expertly curated top picks!
Further resources
For those seeking to deepen their understanding of thermal treatments for metals, the following resources are recommended:
Experience the next level of project management today!
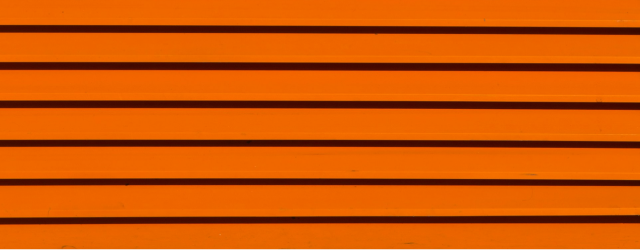
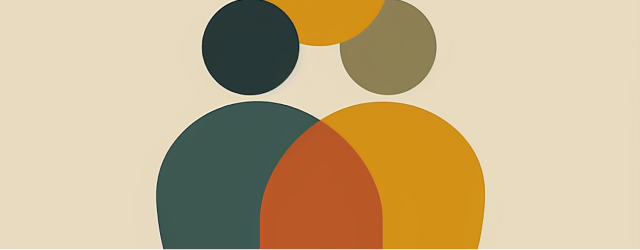
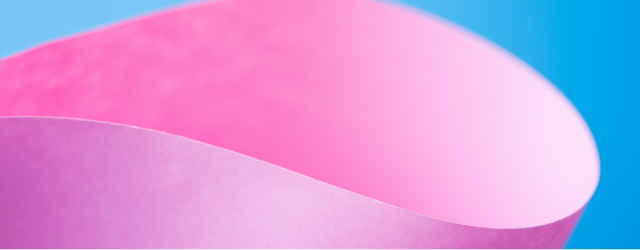
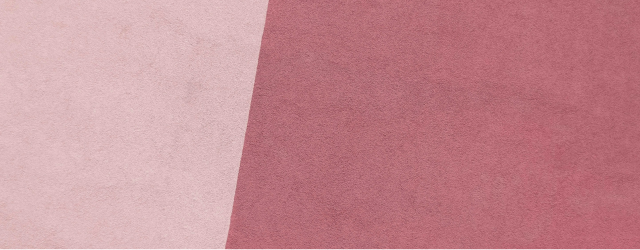
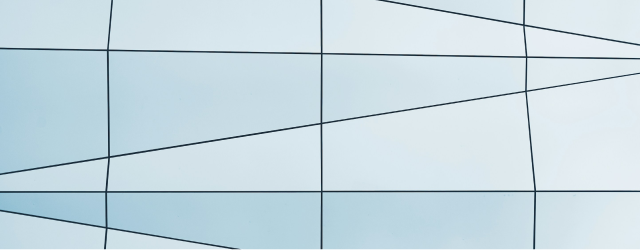
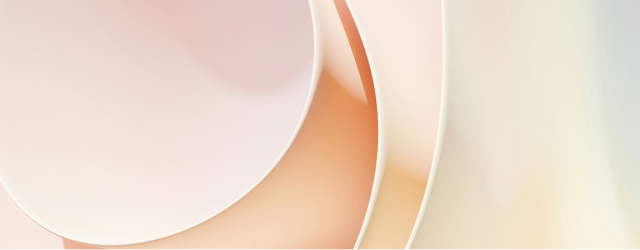
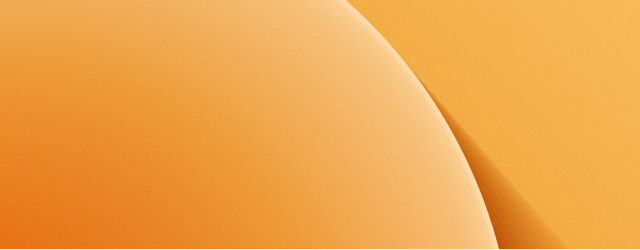