3D Printing
Gain a thorough understanding of 3D Printing in manufacturing, with insights into their application, benefits, and strategic importance in the industry.
3D printing, also known as additive manufacturing, is rapidly transforming how industries approach production. This technology enables manufacturers to create three-dimensional objects by layering materials based on digital models. It's not just about novelty but a significant shift in manufacturing processes, offering versatility, efficiency, and innovation across various sectors. Imagine a world where intricate designs once deemed impossible are now easily realized, where customization is standard, and production timelines are shortened dramatically. The potential of 3D printing in manufacturing is vast, and its impact is already being felt worldwide. This technology is reshaping traditional methodologies, from prototyping to full-scale production, and challenging the norms of manufacturing economics and logistics. As industries increasingly adopt 3D printing, it paves the way for new business models and strategies. This article explores how 3D printing is revolutionizing manufacturing, detailing its historical development, core principles, benefits, challenges, and future trends.
Overview of 3D Printing
3D printing, at its core, involves creating objects layer by layer from digital files, using various materials such as plastics, metals, or composites. Its significance in the manufacturing sector cannot be overstated. The ability to produce complex geometries and customized products with precision and efficiency marks a departure from conventional manufacturing techniques like injection molding or subtractive machining. The versatility of 3D printing lies in its adaptability to different manufacturing processes, allowing for rapid prototyping and on-demand production.
The transformative impact of 3D printing on traditional manufacturing methodologies is profound. Conventional methods often involve high initial setup costs, long lead times, and substantial waste. In contrast, 3D printing minimizes waste, reduces material usage, and offers unparalleled design freedom, which can lead to lighter, stronger, and more efficient products. For instance, the aerospace industry leverages 3D printing to produce components that are not only lighter but also integral to performance improvements. The adaptability of 3D printing extends to its ability to integrate with other technologies, such as Internet of Things (IoT) and artificial intelligence (AI), to enhance production processes further.
Role in Manufacturing Efficiency
3D printing enhances manufacturing efficiency in several notable ways. Firstly, it allows for significant improvements in product design and customization capabilities. Traditional manufacturing often limits design complexity due to tooling constraints; however, 3D printing liberates designers, enabling intricate designs and personalization tailored to specific consumer needs. This shift promotes innovation, as manufacturers are not bound by the limitations of conventional methods.
Economically, 3D printing is a game-changer in terms of cost-efficiency and waste reduction. Traditional manufacturing processes often involve substantial waste, both in materials and energy. Additive manufacturing reduces waste by using only the necessary materials to create an object, cutting down on excess and promoting sustainable practices. Additionally, the technology lowers production costs by eliminating the need for costly molds and tooling, leading to more economically viable production runs, especially for small-batch or custom items.
Moreover, 3D printing significantly shortens the time from design to production. Rapid prototyping, a key advantage of 3D printing, allows for quick iterations and testing of designs, speeding up the product development cycle. This agility enables manufacturers to respond swiftly to market demands and reduce the time-to-market for new products. As a result, industries can maintain competitive edges by adapting more quickly to changing consumer preferences and technological advancements.
Navigate Manufacturing Project Success with Meegle
Historical development of 3d printing
Origins of 3D Printing
The origins of 3D printing technology can be traced back to the early 1980s when Dr. Hideo Kodama of the Nagoya Municipal Industrial Research Institute published his account of a rapid prototyping system using photopolymers. However, it was not until 1986 that Chuck Hull of 3D Systems filed the first patent for stereolithography (SLA), marking a significant milestone in the development of 3D printing. Hull's invention laid the groundwork for creating three-dimensional objects by curing layers of photopolymer resin with ultraviolet light.
Key milestones in the development of 3D printing include the advent of selective laser sintering (SLS) and fused deposition modeling (FDM) in the late 1980s and early 1990s. These technologies expanded the range of materials and applications for 3D printing, enabling more industries to adopt the technology. Early adopters of 3D printing in manufacturing were primarily in the fields of prototyping and tooling, where the ability to quickly create and test designs was invaluable.
Pioneers like Dr. Carl Deckard and Scott Crump played crucial roles in advancing 3D printing technologies. Deckard's development of SLS opened the door to creating durable parts from powder materials, while Crump's invention of FDM allowed for the creation of objects using thermoplastic materials. These innovations laid the foundation for the widespread adoption of 3D printing across various industries, from aerospace to healthcare, and continue to influence the technology's evolution today.
Evolution Over Time
The evolution of 3D printing technology over the decades has been marked by significant technological advancements and a shift from prototyping to full-scale production. Initially, 3D printing was primarily used for creating prototypes, allowing designers and engineers to test and iterate on their designs quickly. However, as the technology matured, it expanded into areas of production, where entire products are manufactured using 3D printing methods.
One of the driving forces behind this evolution has been the innovation in software and materials. Advances in CAD (Computer-Aided Design) software have enabled more complex and intricate designs to be executed with precision. The development of new materials, such as metal powders, biocompatible polymers, and high-strength composites, has expanded the potential applications of 3D printing, making it feasible for industries like automotive and aerospace to produce end-use parts.
The influence of software and materials innovation cannot be underestimated. Modern 3D printers are equipped with sophisticated software that optimizes the printing process, enhances precision, and reduces errors. Furthermore, the development of materials tailored to specific applications has allowed 3D printing to move beyond prototyping, facilitating the production of durable, functional products. This evolution has opened new avenues for manufacturing, enabling companies to explore innovative solutions to complex engineering challenges.
Core principles and techniques of 3d printing
Fundamental Concepts
At the heart of 3D printing is the concept of additive manufacturing, a process that builds objects layer by layer from a digital model. This approach contrasts with traditional subtractive manufacturing techniques, which involve cutting away material to create a desired shape. Additive manufacturing offers several advantages, including reduced material waste, increased design flexibility, and the ability to create complex geometries that are difficult or impossible to achieve with subtractive methods.
The layer-by-layer process fundamental to 3D printing is a crucial aspect of its operation. Each layer is typically a fraction of a millimeter thick, allowing for precise control over the object's dimensions. The process begins with a digital 3D model, designed using CAD software, which is then sliced into thin layers. The printer builds the object one layer at a time, adhering each new layer to the previous one until the final product is complete.
CAD plays an essential role in 3D printing, providing the digital blueprint for the objects to be printed. Designers use CAD software to create detailed models, which can be manipulated, tested, and optimized before printing. This digital-first approach not only streamlines the design process but also reduces the likelihood of errors and ensures consistency across multiple production runs.
Implementation Techniques
3D printing encompasses a variety of techniques, each with its unique advantages and applications. Among the most popular methods are Fused Deposition Modeling (FDM), Stereolithography (SLA), and Selective Laser Sintering (SLS), each suited to different industry needs and material requirements.
-
Fused Deposition Modeling (FDM) involves extruding thermoplastic materials through a heated nozzle, building objects layer by layer. It is widely used due to its affordability and versatility, making it ideal for prototyping and small-scale production in industries such as consumer goods and education.
-
Stereolithography (SLA) utilizes a laser to cure liquid resin into solid objects, offering high precision and smooth surface finishes. SLA is favored in industries requiring detailed and complex designs, such as jewelry and dentistry.
-
Selective Laser Sintering (SLS) employs a laser to fuse powdered materials, such as plastics or metals, creating durable and complex parts. SLS is popular in aerospace and automotive industries due to its ability to produce strong, lightweight components.
The role of materials in determining the technique used in 3D printing is significant. Different techniques are optimized for specific materials, influencing the choice of method based on the desired properties of the final product. For example, FDM is suitable for thermoplastics, while SLA is preferred for photopolymers. The availability and development of new materials continue to drive innovation and expand the applications of 3D printing across various industries.
Click here to read our expertly curated top picks!
Benefits and challenges of 3d printing in manufacturing
Advantages in Production
3D printing offers numerous advantages in production, notably in customization, rapid prototyping, and sustainability. One of the most significant benefits is the ability to customize and personalize products to meet specific consumer needs. Unlike traditional manufacturing, which often involves mass production of identical items, 3D printing allows for unique designs and tailored solutions, enhancing customer satisfaction and enabling businesses to tap into niche markets.
Rapid prototyping is another key advantage, revolutionizing product development by enabling quick iterations and testing of designs. This capability allows manufacturers to accelerate the development cycle, reduce time-to-market, and respond swiftly to changing consumer demands. For example, companies like Nike utilize 3D printing to rapidly prototype footwear designs, optimizing performance and aesthetics before mass production.
Sustainability is a crucial consideration in modern manufacturing, and 3D printing excels in promoting energy and material efficiency. The additive manufacturing process minimizes waste, using only the necessary materials to create objects, and reduces energy consumption by streamlining production. Additionally, 3D printing enables localized production, reducing the need for transportation and lowering carbon emissions. These sustainability benefits align with global efforts to reduce environmental impact and promote responsible manufacturing practices.
Potential Limitations
Despite its many advantages, 3D printing faces several challenges and limitations that must be addressed for wider adoption in manufacturing. One significant challenge is the high initial investment costs associated with acquiring 3D printing equipment and materials. For small and medium-sized enterprises, these costs can be prohibitive, hindering the adoption of the technology.
Limitations in scalability and material range also pose challenges for 3D printing. While it excels in producing customized and small-batch items, scaling up production for mass manufacturing remains a hurdle. Additionally, the range of materials suitable for 3D printing is limited compared to traditional manufacturing methods, restricting the types of products that can be created.
However, potential solutions and future improvements are on the horizon. Advances in materials science are expanding the range of printable materials, offering new possibilities for product development. Furthermore, innovations in printer technology and software are improving scalability and reducing costs, making 3D printing more accessible to a broader range of industries. As these improvements continue, the adoption of 3D printing in manufacturing is likely to accelerate, overcoming the current limitations and unlocking new opportunities for innovation.
Case studies and real-world applications
Industry examples
Industry examples
3D printing is already making significant inroads in various industries, transforming the way products are designed, developed, and manufactured. The automotive industry is one such sector where 3D printing is used extensively for producing parts and components. Companies like Ford and BMW leverage 3D printing to create lightweight, durable components that enhance vehicle performance and fuel efficiency. The technology also allows for rapid prototyping and testing of new designs, accelerating the development cycle and enabling more innovative products.
In aerospace engineering, 3D printing is employed to develop lightweight components crucial for aircraft performance. For instance, companies like Boeing and Airbus use 3D printing to produce parts that reduce the overall weight of their aircraft, leading to improved fuel efficiency and reduced emissions. The ability to create complex geometries also allows for more efficient designs, enhancing the aerodynamics and structural integrity of the components.
The medical field is another area where 3D printing is making a substantial impact. The technology is used to produce customized prosthetics and implants tailored to individual patient needs, improving the fit and functionality of these devices. Additionally, 3D printing enables the creation of surgical models and tools, allowing for more precise and effective procedures. Companies like Stryker and Medtronic utilize 3D printing to innovate in the medical sector, offering solutions that enhance patient care and outcomes.
Impact analysis
Impact analysis
The economic impact of 3D printing on manufacturing is profound, offering improvements in product lifecycle and innovation speed. By enabling rapid prototyping and customization, 3D printing reduces development time and costs, allowing for more efficient production processes. This agility enables companies to respond swiftly to market demands and maintain competitive edges, fostering innovation and driving growth.
In terms of environmental impact, 3D printing promotes sustainability outcomes by minimizing waste and reducing energy consumption. The additive manufacturing process uses only the necessary materials to create objects, reducing excess and promoting responsible manufacturing practices. Additionally, localized production reduces the need for transportation, lowering carbon emissions and aligning with global efforts to reduce environmental impact.
The combination of economic and environmental benefits makes 3D printing a compelling option for manufacturers seeking to innovate and improve their operations. As the technology continues to evolve, its potential to transform industries and drive sustainable practices will only grow, unlocking new opportunities for innovation and growth.
Click here to read our expertly curated top picks!
Technological integration and innovations in 3d printing
Current Technologies
The integration of advanced technologies such as the Internet of Things (IoT) and artificial intelligence (AI) is enhancing 3D printing processes, driving new levels of efficiency and precision. IoT enables interconnected devices to communicate and coordinate during the printing process, optimizing production and reducing errors. AI algorithms can analyze data from previous prints to improve future outcomes, ensuring consistent quality and reducing material waste.
Advancements in 3D printing software and hardware are also revolutionizing the industry. Modern printers are equipped with sophisticated software that enhances precision and reduces errors, while innovations in hardware are improving printing speeds and capabilities. These advancements are expanding the applications of 3D printing, enabling manufacturers to explore new solutions to complex engineering challenges.
Material innovations are another crucial aspect of the evolving 3D printing landscape. The development of new materials tailored to specific applications is expanding the potential uses of 3D printing across various industries. High-strength composites, biocompatible polymers, and metal powders are just a few examples of materials driving innovation and expanding the possibilities for 3D printing. As these innovations continue, the adoption of 3D printing in manufacturing is likely to accelerate, overcoming current limitations and unlocking new opportunities for innovation.
Future Trends
The future of 3D printing in Industry 4.0 is promising, with the potential to revolutionize manufacturing and drive new levels of customization and decentralization. As technology continues to evolve, breakthroughs in materials science and printing techniques will expand the range of applications for 3D printing, enabling more complex and intricate designs.
Mass customization and decentralized manufacturing are likely to become more prevalent as 3D printing technology advances. The ability to produce customized products on demand allows manufacturers to tailor solutions to specific consumer needs, enhancing customer satisfaction and enabling businesses to tap into niche markets. Decentralized manufacturing, facilitated by 3D printing, reduces the need for centralized production facilities, enabling localized production and reducing transportation costs and emissions.
The role of 3D printing in Industry 4.0 will be integral to the transformation of manufacturing, offering new opportunities for innovation and growth. As companies continue to explore the possibilities of 3D printing, its potential to drive sustainable practices and improve operational efficiency will only grow, shaping the future of manufacturing and driving new levels of competitiveness.
Click here to read our expertly curated top picks!
Tips for effective use of 3d printing in manufacturing
Do's | Don'ts |
---|---|
Evaluate compatibility with business needs | Overlook initial costs and investments |
Continuously monitor technological advancements | Ignore training and skill development |
Focus on quality and precision in designs | Neglect regular maintenance and updates |
Click here to read our expertly curated top picks!
Conclusion
Summary of Key Points
3D printing is revolutionizing manufacturing by offering new possibilities for customization, rapid prototyping, and sustainability. Its transformative impact on traditional manufacturing methodologies is profound, challenging the norms of manufacturing economics and logistics. The technology enhances operational efficiency and design capabilities, reducing waste and lowering production costs. As industries increasingly adopt 3D printing, it paves the way for new business models and strategies, driving innovation and growth.
Encouraging Ongoing Adaptation
Professionals in the manufacturing sector are encouraged to explore 3D printing for competitive advantage. The importance of staying informed on advancements and innovations in 3D printing technology cannot be overstated. As the technology continues to evolve, its potential to transform industries and drive sustainable practices will only grow, unlocking new opportunities for innovation and growth. By embracing 3D printing, manufacturers can stay ahead of the curve, maintaining competitiveness and driving the future of manufacturing.
Navigate Manufacturing Project Success with Meegle
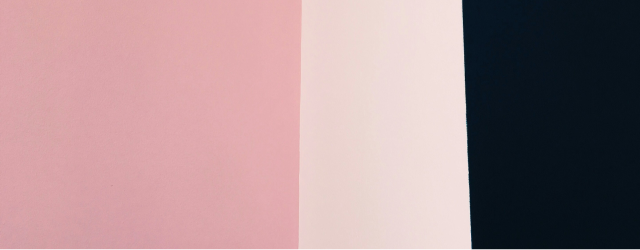
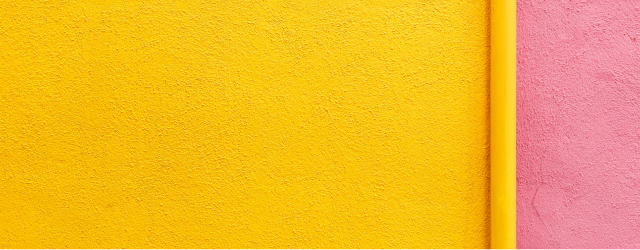
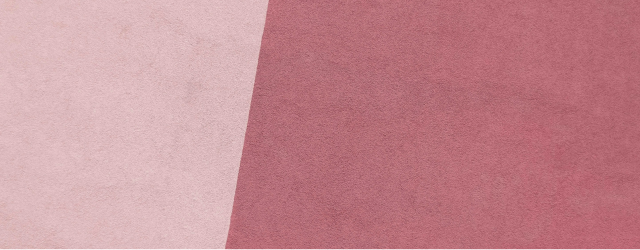
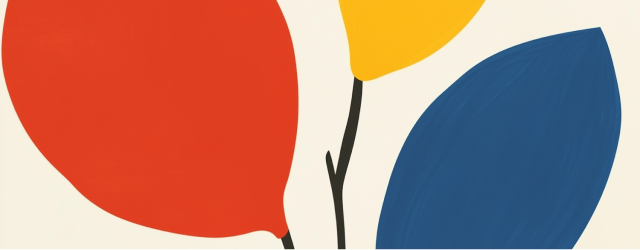
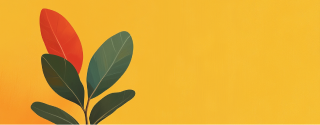
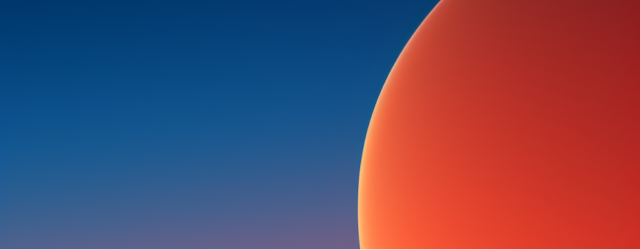
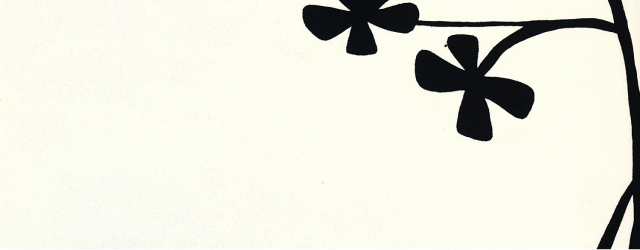
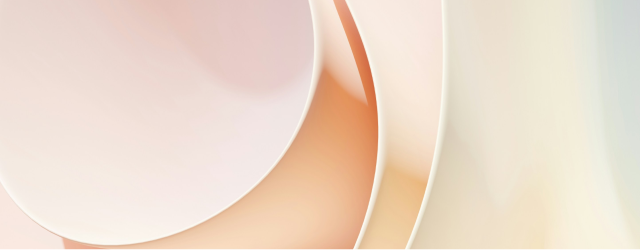