Cleanroom Manufacturing
Gain a thorough understanding of Cleanroom Manufacturing in manufacturing, with insights into their application, benefits, and strategic importance in the industry.
Overview of Cleanroom Manufacturing
Cleanroom manufacturing is a sophisticated process designed to maintain environments where contamination control is crucial. Defined as spaces wherein the concentration of airborne particles is regulated to specified limits, cleanrooms play a pivotal role in sectors that demand stringent cleanliness standards. The primary goal is to prevent contamination from affecting the product quality, ensuring that production meets the high standards set by regulatory bodies and consumer expectations.
The importance of such controlled environments cannot be overstated, especially as industries face mounting pressure to adhere to increasingly strict regulatory requirements. The demand for high-quality products has soared, driven by consumer expectations for safety and efficacy. For instance, in the pharmaceutical industry, cleanrooms are essential to prevent the risk of contamination during drug manufacturing, thereby safeguarding consumer health. Similarly, the electronics sector relies on cleanrooms to prevent microscopic particles from affecting the functionality of sensitive components like semiconductors.
As the global market becomes more competitive, the reliance on cleanroom standards is growing. Companies are investing in cutting-edge cleanroom technologies to ensure their products are not only compliant with international standards but also stand out in quality and performance. This focus on cleanliness is not just about meeting standards; it's about surpassing them to gain a competitive edge. In essence, cleanroom manufacturing is about optimizing processes to produce superior products while minimizing risks—a fundamental aspect of modern industries.
Role in Manufacturing Efficiency
The role of cleanroom environments in enhancing manufacturing efficiency is profound. By providing a controlled setting that reduces defects and improves yield rates, cleanrooms contribute significantly to the overall manufacturing process. The impact extends beyond mere contamination control; it encompasses cost management and time efficiency, which are crucial for businesses aiming to maximize profitability.
Cleanrooms are vital in reducing the incidence of product defects, which can be costly both financially and reputationally. For example, in semiconductor fabrication, even a minuscule particle can ruin batches of microchips, leading to substantial financial losses. Cleanrooms mitigate this risk, ensuring that products meet exact specifications and perform reliably. The consistency provided by cleanroom environments translates into improved yield rates, minimizing waste and optimizing resource utilization.
Moreover, cleanrooms facilitate compliance with international standards and certifications, which are often prerequisites for entering global markets. By maintaining rigorous cleanliness levels, companies can easily achieve industry certifications like ISO 14644, which is crucial for international trade. Compliance not only opens doors to new markets but also assures customers of the product's quality and safety.
The integration of cleanroom practices into manufacturing processes can lead to remarkable improvements in efficiency. Companies benefit from reduced downtime and fewer delays, as cleanrooms streamline operations and minimize disruptions caused by contamination. The result is a more agile production process that can respond swiftly to market demands, thereby enhancing competitiveness. Cleanrooms, therefore, are not just about maintaining cleanliness; they are about fostering an environment where manufacturing excellence can thrive.
Navigate Manufacturing Project Success with Meegle
Historical development of cleanroom manufacturing
Origins of Cleanroom Manufacturing
The concept of cleanroom manufacturing has evolved significantly since its inception, rooted in early laboratory practices where contamination control was a necessity rather than a choice. Initially, cleanrooms were simple setups designed to protect sensitive experiments from environmental pollutants. Over time, they expanded into industrial applications, becoming a cornerstone of manufacturing processes in various sectors.
The origins of cleanroom technology can be traced back to the mid-20th century, with significant advancements made during and post-World War II. The need for contamination-free environments became pronounced in the aerospace and defense industries, where precision was crucial in manufacturing components for aircraft and missiles. These early cleanrooms were rudimentary, focusing primarily on controlling airflow and minimizing particle contamination.
A key milestone in cleanroom development came with the invention of the laminar flow cleanroom by physicist Willis Whitfield in the 1960s. This innovation revolutionized cleanroom design by introducing a system where air flows uniformly across all surfaces, significantly reducing airborne particles. Whitfield's design laid the foundation for modern cleanrooms, enabling industries like semiconductor manufacturing to flourish by providing environments where particle contamination was minimized.
As the industrial landscape evolved, cleanroom technology adapted to meet the growing demands of sectors such as pharmaceuticals and biotechnology. The development of high-efficiency particulate air (HEPA) filters was a crucial advancement, allowing cleanrooms to achieve unprecedented levels of cleanliness. These filters are capable of trapping particles as small as 0.3 microns with 99.97% efficiency, setting a new benchmark for air cleanliness in manufacturing environments.
Evolution Over Time
The evolution of cleanroom manufacturing techniques has been marked by continuous advancements in technology and materials, reflecting the changing needs of industries. Significant improvements have been made in filtration systems, air handling, and automated monitoring, transforming cleanrooms into sophisticated environments capable of maintaining stringent cleanliness standards.
Filtration systems have seen remarkable enhancements, with the introduction of ultra-low penetration air (ULPA) filters, which offer even higher efficiency compared to traditional HEPA filters. These filters are designed to trap particles as small as 0.12 microns with an efficiency of 99.999%, making them ideal for industries where ultra-clean environments are critical. The development of such advanced filtration technologies has enabled cleanrooms to achieve cleanliness levels that were previously unattainable.
Air handling systems have also undergone significant advancements, with modern systems incorporating features like variable air volume (VAV) control, ensuring optimal air circulation and temperature regulation within cleanrooms. These systems are designed to maintain consistent airflow patterns, reducing the risk of contamination by ensuring that airborne particles are continually removed from the environment.
The impact of digital transformation on cleanroom management and operational efficiency cannot be overstated. Automated monitoring systems have become integral to cleanroom operations, providing real-time data on air quality, particle count, and environmental conditions. These systems enable proactive management of cleanroom environments, allowing for swift adjustments to maintain optimal cleanliness levels. The integration of data analytics and artificial intelligence further enhances cleanroom operations by predicting potential contamination risks and suggesting mitigation strategies.
The evolution of cleanroom manufacturing is a testament to the industry's commitment to excellence. As technology continues to advance, cleanrooms are becoming more efficient, reliable, and capable of meeting the highest standards of cleanliness required by modern industries. This continuous evolution ensures that cleanrooms remain at the forefront of manufacturing innovation, providing environments where precision and quality are non-negotiable.
Click here to read our expertly curated top picks!
Core principles and techniques
Fundamental Concepts
Cleanroom design revolves around several key principles, including airflow control, filtration, and environmental monitoring, which are essential for maintaining cleanliness and preventing contamination. Each of these elements plays a vital role in ensuring that cleanrooms operate at optimal levels, providing environments where precise manufacturing can occur without the risk of contamination.
Airflow control is a fundamental aspect of cleanroom design, influencing how air moves within the space to minimize the presence of airborne particles. Cleanrooms typically employ laminar airflow systems, where air flows in parallel layers with minimal disruption, ensuring that particles are continuously swept away. This controlled airflow is crucial in preventing contamination, as it helps maintain a consistent environment where manufacturing processes can occur without interruption.
Filtration is another critical component of cleanroom design, with HEPA and ULPA filters being the standard in air purification. These filters are designed to trap particles of varying sizes, ensuring that the air within the cleanroom remains free of contaminants. The classification system for cleanrooms, based on particle count and air cleanliness levels, is directly tied to the effectiveness of these filtration systems. Cleanrooms are classified according to ISO standards, such as ISO 14644, which specifies the maximum allowable particle count per cubic meter at various cleanliness levels.
Environmental monitoring is essential for maintaining cleanroom integrity, involving continuous assessment of air quality, temperature, humidity, and particle count. Monitoring systems provide real-time data, enabling swift responses to potential contamination threats. Personnel, equipment, and material management also play a crucial role in maintaining cleanroom environments. Proper training, strict protocols, and adherence to cleanliness standards are necessary to ensure that cleanrooms function effectively and consistently.
Implementation Techniques
Implementing cleanroom standards involves a combination of methods and technologies that are designed to maintain optimal cleanliness levels. Key elements include the use of HEPA filters, cleanroom garments, and controlled entry systems, each contributing to the overall efficacy of cleanroom environments.
HEPA filters are integral to cleanroom operations, providing the primary means of air purification by trapping particles as small as 0.3 microns. These filters are vital for maintaining air cleanliness, ensuring that the environment remains free from contaminants that could jeopardize product quality. The selection and maintenance of filtration systems are crucial, as they directly impact the effectiveness of contamination control measures.
Cleanroom garments are another essential component, designed to prevent personnel from introducing contaminants into the cleanroom environment. These garments typically include coveralls, gloves, masks, and shoe covers, all aimed at minimizing the transfer of particles from skin or clothing. Proper donning and doffing procedures are necessary to ensure that garments function effectively, underscoring the importance of training and adherence to protocols.
Controlled entry systems are employed to regulate access to cleanrooms, ensuring that only authorized personnel can enter these sensitive environments. These systems may include air showers, interlocking doors, and access control measures, all designed to minimize the risk of contamination from external sources. Validation and qualification processes are crucial in cleanroom setup and maintenance, ensuring that systems function as intended and meet desired cleanliness standards.
The significance of training and protocols for personnel working within cleanrooms cannot be overstated. Proper training ensures that staff understand the importance of cleanliness and adhere to protocols designed to maintain cleanroom integrity. Continuous education and reinforcement of best practices are necessary to prevent complacency and ensure that cleanrooms operate at optimal levels.
Benefits and challenges
Advantages in Production
Cleanrooms offer numerous advantages in production, enhancing product quality and consistency across various manufacturing sectors. By providing a controlled environment free from contaminants, cleanrooms enable manufacturers to produce high-quality products that meet stringent industry standards.
One of the primary benefits of cleanrooms is their ability to ensure product consistency, which is crucial for industries like pharmaceuticals and electronics. Consistent production quality minimizes the risk of defects, ensuring that products perform reliably and meet customer expectations. For instance, in the pharmaceutical industry, cleanrooms are essential for maintaining the sterility of drug manufacturing processes, safeguarding consumer health and safety.
Cleanrooms also play a vital role in advancing research and development efforts, providing controlled environments where experimentation can occur without the risk of contamination. This is particularly important in biotechnology, where cleanrooms enable precise manipulation of biological materials, fostering innovation and development of new treatments and therapies.
Regulatory compliance is another significant advantage offered by cleanrooms. By maintaining rigorous cleanliness standards, companies can easily achieve industry certifications, which are often prerequisites for entering global markets. Compliance with standards like ISO 14644 assures customers of product quality and safety, enhancing brand reputation and opening doors to new market opportunities.
The benefits of cleanrooms extend beyond product quality, contributing to improved efficiency and cost management in manufacturing processes. By reducing the incidence of defects and minimizing waste, cleanrooms optimize resource utilization, maximizing profitability for businesses. In essence, cleanrooms provide an environment where manufacturing excellence can thrive, fostering innovation and competitiveness in a rapidly evolving global market.
Potential Limitations
Despite their numerous advantages, cleanrooms present several challenges that manufacturers must address to maintain their efficacy. These challenges include high operational costs, complexity in design and maintenance, and the need for specialized training, each posing potential risks to cleanroom operations.
Operational costs associated with cleanrooms can be significant, particularly in terms of initial setup and ongoing maintenance. The investment in advanced filtration systems, environmental monitoring technology, and specialized equipment can strain budgets, especially for small and medium-sized enterprises. However, these costs are often offset by the benefits of improved product quality and reduced defect rates, highlighting the importance of strategic planning and resource allocation.
Design and maintenance complexity is another challenge, requiring careful consideration of airflow patterns, filtration systems, and environmental controls. Cleanrooms must be meticulously designed to ensure optimal cleanliness levels, which can be challenging given the varying requirements of different industries. Maintenance involves regular audits, inspections, and adjustments to ensure that systems function effectively, necessitating a dedicated team of experts to oversee operations.
Specialized training is crucial for personnel working within cleanrooms, ensuring that staff adhere to protocols and understand the importance of cleanliness. The need for ongoing education and reinforcement of best practices can be challenging, particularly in industries with high staff turnover. Failure to maintain cleanliness standards can lead to system failures and contamination breaches, jeopardizing product quality and safety.
To mitigate these challenges, companies must adopt strategic approaches that enhance cleanroom efficacy. This includes investing in cutting-edge technologies, implementing robust training programs, and fostering a culture of continuous improvement. By addressing potential limitations proactively, manufacturers can ensure that cleanrooms function optimally, maintaining the integrity of production processes and safeguarding product quality.
Click here to read our expertly curated top picks!
Case studies and real-world applications
Industry examples
Industry examples
Cleanroom manufacturing has been successfully implemented across various industries, each benefiting from the controlled environments that enhance product innovation and market competitiveness. Detailed examples from sectors such as semiconductor fabrication, biotechnology, and medical device production highlight the transformative impact of cleanrooms.
In semiconductor fabrication, cleanrooms are indispensable for ensuring the integrity of microchips, which are susceptible to contamination from microscopic particles. Companies like Intel have invested heavily in state-of-the-art cleanroom facilities, enabling them to produce high-performance chips that power modern technology. The precision and reliability of cleanroom environments have allowed semiconductor manufacturers to achieve remarkable innovations, enhancing their market competitiveness.
Biotechnology companies also rely on cleanrooms to ensure the sterility of biological materials during research and development. Firms like Genentech use cleanrooms to maintain stringent cleanliness standards, fostering innovation in the development of new therapies and treatments. The ability to conduct experiments in controlled environments has led to breakthroughs in biotechnology, advancing healthcare and improving patient outcomes.
Medical device production is another sector that benefits significantly from cleanroom environments. Companies like Medtronic utilize cleanrooms to manufacture devices with precision and reliability, ensuring that products meet the highest industry standards. The controlled environment provided by cleanrooms allows medical device manufacturers to produce products that are safe and effective, enhancing their market reputation and competitiveness.
Unique approaches and adaptations made by these companies underscore the versatility of cleanroom manufacturing. By tailoring cleanroom environments to meet specific needs, industries can optimize processes and achieve remarkable results. The success stories of these companies highlight the transformative impact of cleanrooms, fostering innovation and competitiveness in various sectors.
Impact analysis
Impact analysis
The tangible impacts of cleanroom manufacturing on productivity, quality assurance, and cost management are profound, underscoring the value of these controlled environments in modern production processes. Companies that have implemented cleanrooms have experienced remarkable improvements in efficiency, reliability, and overall performance.
Productivity is significantly enhanced by cleanrooms, which streamline operations and minimize disruptions caused by contamination. The consistency provided by cleanroom environments allows manufacturers to maintain continuous production, reducing downtime and delays. This improved efficiency translates into faster time-to-market for products, enhancing competitiveness in a rapidly evolving industry landscape.
Quality assurance is another area where cleanrooms have a dramatic impact, ensuring that products meet stringent industry standards. The controlled environment provided by cleanrooms reduces the incidence of defects, ensuring that products perform reliably and meet customer expectations. This commitment to quality enhances brand reputation, attracting new customers and opening doors to new market opportunities.
Cost management is also improved by cleanroom manufacturing, as the reduction in defects and waste optimizes resource utilization. Companies benefit from minimized financial losses attributed to product recalls and defects, maximizing profitability and enhancing competitiveness. The strategic use of cleanroom environments allows manufacturers to achieve remarkable results, fostering innovation and excellence in production processes.
Specific metrics or KPIs used by companies to measure the success of cleanroom operations include yield rates, defect rates, and compliance with industry standards. These metrics provide valuable insights into cleanroom performance, enabling companies to make informed decisions and enhance operational efficiency. Case studies showcasing dramatic improvements or breakthroughs resulting from cleanroom implementation highlight the transformative impact of these environments, fostering innovation and competitiveness across various industries.
Technological integration and innovations
Current Technologies
The integration of current technologies into cleanroom operations has transformed these environments into sophisticated spaces capable of maintaining stringent cleanliness standards. Advanced air filtration systems, IoT monitoring devices, and automation in material handling are among the technologies that enhance cleanroom performance and efficiency.
Air filtration systems have seen significant advancements, with the introduction of ULPA filters offering enhanced efficiency compared to traditional HEPA filters. These filters are designed to trap particles as small as 0.12 microns, ensuring that cleanrooms maintain optimal air cleanliness levels. The development of advanced filtration technologies has enabled cleanrooms to achieve unprecedented levels of cleanliness, essential for industries where precision is critical.
IoT monitoring devices have become integral to cleanroom operations, providing real-time data on air quality, particle count, and environmental conditions. These devices enable proactive management of cleanroom environments, allowing for swift adjustments to maintain optimal cleanliness levels. The integration of data analytics and AI further enhances cleanroom performance by predicting potential contamination risks and suggesting mitigation strategies.
Automation in material handling is another area where technology has transformed cleanroom operations, streamlining processes and minimizing the risk of contamination. Automated systems ensure precise handling and movement of materials within cleanrooms, reducing the potential for human error and enhancing efficiency. The integration of robotics and automation into cleanroom environments has led to remarkable improvements in productivity and reliability.
Innovations in cleanroom construction materials and design have also contributed to improved efficiency and sustainability. The use of advanced materials that minimize particle generation and enhance durability has transformed cleanroom environments, allowing for more reliable and efficient operations. These innovations highlight the industry's commitment to excellence, ensuring that cleanrooms remain at the forefront of manufacturing innovation.
Future Trends
As technology continues to evolve, cleanroom manufacturing is poised to experience significant advancements that will enhance efficiency, reliability, and competitiveness. Future developments and innovations in cleanroom technology, including the rise of smart cleanrooms and digital twins, are expected to transform these environments into sophisticated spaces capable of maintaining optimal cleanliness levels.
Smart cleanrooms represent the next frontier in cleanroom innovation, integrating IoT devices, data analytics, and AI to enhance performance and efficiency. These cleanrooms are designed to provide real-time insights into environmental conditions, enabling proactive management of cleanliness levels. The integration of smart technologies into cleanroom environments is expected to lead to remarkable improvements in productivity, reliability, and overall performance.
Digital twins are another emerging trend, offering virtual representations of cleanroom environments that provide valuable insights into operations and potential risks. These digital models enable manufacturers to simulate cleanroom conditions, identify potential contamination threats, and optimize processes for enhanced efficiency. The use of digital twins in cleanroom environments is expected to lead to significant improvements in operational efficiency and reliability.
Increased automation and robotics in cleanroom environments are anticipated to transform manufacturing processes, streamlining operations and minimizing the risk of contamination. The integration of advanced robotics into cleanroom settings is expected to enhance precision and reliability, fostering innovation and competitiveness across various industries.
Anticipated changes in industry regulations and standards may impact cleanroom manufacturing, necessitating adaptations in technology and processes. The industry's commitment to excellence ensures that cleanrooms remain at the forefront of manufacturing innovation, providing environments where precision and quality are non-negotiable. By embracing future trends and integrating best practices, manufacturers can maintain a competitive edge and foster innovation in a rapidly evolving global market.
Click here to read our expertly curated top picks!
Do's and don'ts in cleanroom manufacturing
Do's | Don'ts |
---|---|
Maintain rigorous cleanliness protocols. | Neglect regular maintenance and audits. |
Ensure all personnel are properly trained. | Allow unauthorized access to cleanrooms. |
Use appropriate cleanroom garments. | Overlook minor breaches in protocol. |
Regularly monitor and adjust airflows. | Rely on outdated technology and practices. |
Invest in quality filtration systems. | Compromise on material and equipment quality. |
Click here to read our expertly curated top picks!
Conclusion
Summary of Key Points
Cleanroom manufacturing is a sophisticated process designed to maintain environments where contamination control is crucial, playing a pivotal role in enhancing product quality and consistency across various sectors. The integration of advanced technologies into cleanroom operations has transformed these environments into sophisticated spaces capable of maintaining stringent cleanliness standards. Despite challenges such as high operational costs and complexity in design, cleanrooms offer numerous advantages, including improved efficiency, regulatory compliance, and enhanced innovation.
Encouraging Ongoing Adaptation
To maintain a competitive edge in relevant industries, professionals must keep abreast of advancements in cleanroom technology and integrate best practices into their operations. Continuous improvement and adaptation are essential for fostering innovation and excellence in cleanroom environments. By embracing future trends and technological innovations, manufacturers can ensure that cleanrooms remain at the forefront of manufacturing innovation, providing environments where precision and quality are non-negotiable.
Navigate Manufacturing Project Success with Meegle
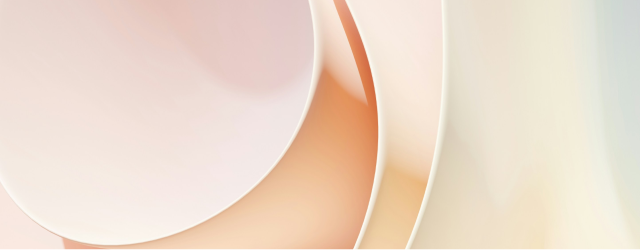
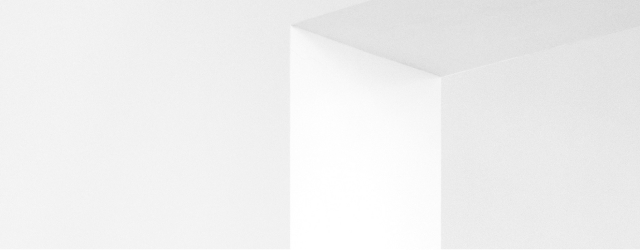
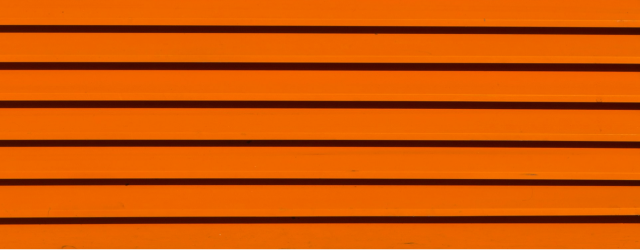
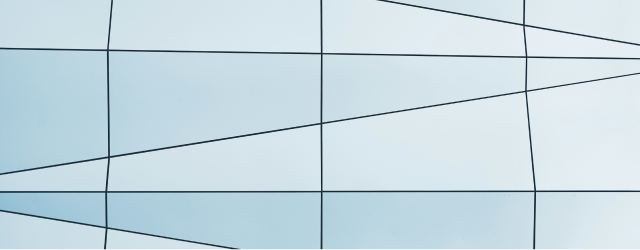
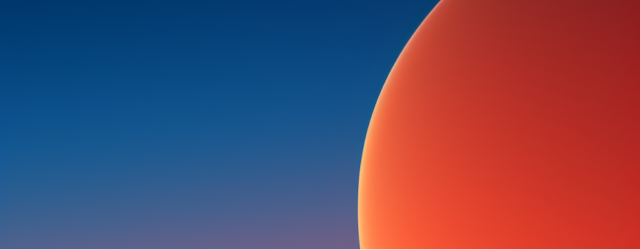
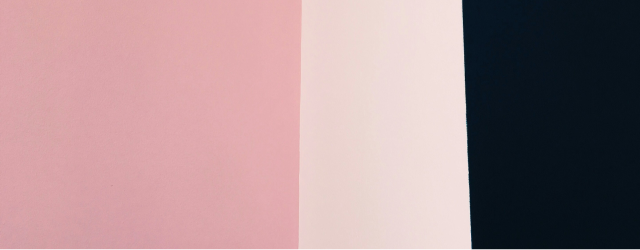
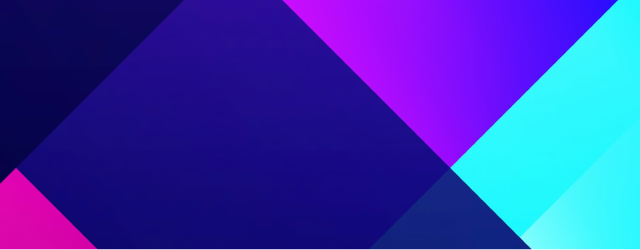
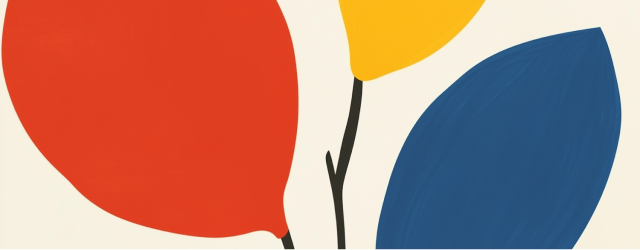