Maintenance Management
Gain a thorough understanding of Maintenance Management in manufacturing, with insights into their application, benefits, and strategic importance in the industry.
Overview of Maintenance Management
Maintenance Management is a strategic approach that focuses on the upkeep and optimization of manufacturing equipment and processes. It encompasses various maintenance strategies—preventive, predictive, and corrective—each designed to ensure machines operate at peak efficiency. Preventive maintenance involves regular checks and servicing to prevent issues before they arise, predictive maintenance uses data and analytics to forecast potential failures, and corrective maintenance addresses unexpected breakdowns. By understanding and implementing these strategies, manufacturing professionals can significantly reduce unnecessary downtime, minimize costs, and ensure consistently high product quality. The competitive advantage gained through effective Maintenance Management is invaluable, making it a critical component of achieving operational excellence.
Role in Manufacturing Efficiency
The role of Maintenance Management in enhancing manufacturing efficiency cannot be overstated. It is pivotal in ensuring seamless operations by reducing machine breakdowns and maintaining high-quality production outputs. A structured maintenance strategy improves equipment availability and extends machinery lifespan, while optimizing resource usage. For instance, consider a manufacturing plant that experiences frequent equipment malfunctions. Implementing a robust Maintenance Management system can mitigate these issues by identifying potential problems before they lead to costly downtimes. By focusing on key operational metrics such as throughput, cycle time, and overall equipment effectiveness (OEE), professionals can leverage Maintenance Management insights to drive efficiency. The ultimate aim is to maintain high production levels with minimal disruptions, thereby maximizing profitability and competitive advantage.
Navigate Manufacturing Project Success with Meegle
Historical development of maintenance management
Origins of Maintenance Management
The concept of Maintenance Management has undergone significant transformation since the Industrial Revolution. Initially, maintenance activities were reactive—performed only when equipment failed, leading to substantial downtime and productivity loss. During this era, the focus was primarily on repairing broken machinery, with little regard for systematic upkeep. This changed with the introduction of Total Productive Maintenance (TPM) and Reliability-Centered Maintenance (RCM) in the late 20th century, marking a shift towards preventive strategies. TPM emphasizes proactive maintenance to improve equipment reliability, while RCM focuses on understanding the functions and potential failures of machinery to devise appropriate maintenance plans. These methodologies laid the foundation for modern Maintenance Management, highlighting the importance of anticipating and preventing equipment issues before they occur.
Evolution Over Time
As manufacturing processes evolved, so did Maintenance Management. The transition from basic repair practices to sophisticated, technology-driven strategies was driven by advancements in machinery, automation, and data analytics. Modern techniques such as predictive maintenance harness sensors and IoT devices to gather real-time data, enabling early detection of equipment failures. For example, a manufacturing company might use IoT sensors to monitor the vibration levels of machinery, predicting when a motor is likely to fail. This proactive approach allows for timely interventions, reducing downtime and associated costs. Moreover, data analytics and machine learning have facilitated deeper insights into equipment performance, enabling manufacturers to optimize their operations and significantly reduce costs. The evolution of Maintenance Management reflects the industry's shift towards integrating technology for enhanced efficiency and reliability.
Click here to read our expertly curated top picks!
Core principles and techniques
Fundamental Concepts
At the heart of Maintenance Management are fundamental concepts aimed at minimizing downtime and ensuring equipment reliability. Key principles include:
- Preventive Maintenance: Routine checks and servicing to prevent equipment issues.
- Predictive Maintenance: Utilizes data analysis to foresee potential equipment failures.
- Corrective Maintenance: Addresses unexpected breakdowns when they occur.
These principles form the backbone of Maintenance Management strategies, enabling professionals to tailor maintenance plans specific to their manufacturing needs. Understanding these concepts allows for informed decision-making regarding maintenance schedules, resource allocation, and cost management. For instance, a manufacturing facility implementing preventive maintenance might schedule routine inspections to maintain optimal equipment performance, thereby reducing the risk of unexpected downtime. Professionals equipped with this knowledge can craft strategies that not only enhance equipment reliability but also contribute to overall operational efficiency.
Implementation Techniques
Successful implementation of Maintenance Management requires a combination of techniques such as condition monitoring, root cause analysis, and maintenance scheduling.
- Condition Monitoring: This involves tracking the health of equipment using sensors and diagnostic tools.
- Root Cause Analysis: A method to identify the underlying issues causing equipment failures.
- Maintenance Scheduling: Ensures routine checks and repairs are conducted systematically.
Consider a manufacturing company that employs condition monitoring to keep track of its machinery's temperature levels, enabling early detection of overheating issues and preemptive interventions. Root cause analysis might be used to investigate frequent malfunctions in a specific machine, leading to targeted solutions. Maintenance scheduling ensures that all necessary checks and repairs are performed on time, minimizing disruptions. By implementing these techniques, professionals can optimize their maintenance operations, ensuring high productivity and reduced costs.
Benefits and challenges
Advantages in Production
Maintenance Management offers numerous advantages that contribute to improved production outcomes, including:
- Enhanced Equipment Reliability: Regular maintenance ensures machines function optimally, reducing breakdowns.
- Reduced Operational Costs: Efficient maintenance practices minimize repair expenses and prolong machinery lifespan.
- Improved Product Quality: Consistent equipment performance leads to higher-quality outputs.
For example, a manufacturing plant that implements a comprehensive Maintenance Management strategy might experience fewer equipment failures, leading to uninterrupted production cycles and enhanced product quality. This not only boosts efficiency but also increases customer satisfaction and loyalty. Additionally, by reducing the need for costly repairs and replacements, companies can allocate resources more effectively, maximizing profitability. These tangible benefits underscore the importance of Maintenance Management in achieving operational excellence.
Potential Limitations
Despite its advantages, Maintenance Management is not without challenges.
- High Initial Investment Costs: Implementing advanced maintenance technologies requires significant upfront expenditure.
- Complex Implementation Processes: Establishing a comprehensive maintenance strategy can be complicated and time-consuming.
- Resistance to Change: Personnel may resist adopting new maintenance practices, impacting successful implementation.
For instance, a manufacturing firm might face budget constraints when investing in IoT sensors and data analytics tools necessary for predictive maintenance. The complexity of integrating these technologies into existing processes could further hinder progress. Additionally, staff may be accustomed to traditional maintenance methods, resisting changes required for a more proactive approach. To overcome these challenges, professionals must develop strategies that address budget concerns, streamline integration, and promote acceptance among personnel. Training and communication play a vital role in facilitating successful implementation and ensuring continuous improvement.
Click here to read our expertly curated top picks!
Case studies and real-world applications
Industry examples
Industry examples
Example 1: Automotive Manufacturing
In the automotive industry, a leading manufacturer implemented predictive maintenance across its assembly lines, resulting in a 30% reduction in unplanned downtime and a 20% increase in production throughput. By leveraging IoT sensors and data analytics, the company optimized its maintenance schedules, leading to significant improvements in equipment reliability and operational efficiency. This proactive approach not only reduced repair costs but also enhanced production quality, enabling the manufacturer to meet customer demands more effectively.
Example 2: Food Processing
A food processing company adopted a comprehensive Maintenance Management strategy that included both preventive and predictive maintenance techniques. The implementation resulted in enhanced quality control and reduced contamination risks, thereby improving product safety and achieving regulatory compliance. By systematically monitoring equipment health and predicting potential failures, the company maintained consistent production levels while safeguarding product integrity. This strategic approach not only reduced downtime but also fortified the company's reputation in the industry.
Example 3: Textile Manufacturing
In textile manufacturing, a company successfully integrated Maintenance Management with lean manufacturing principles, resulting in a 25% reduction in maintenance costs. By streamlining its maintenance processes and focusing on continuous improvement, the company achieved greater production efficiency and reduced waste. This integration allowed the company to maintain high-quality outputs while optimizing resource utilization, demonstrating the efficacy of combining maintenance strategies with lean principles.
Impact analysis
Impact analysis
Analyzing the impacts of Maintenance Management on manufacturing operations reveals significant improvements in efficiency, cost savings, and product quality. These real-world examples demonstrate the tangible benefits and potential return on investment for manufacturers implementing Maintenance Management strategies. By adopting proactive maintenance practices, companies can reduce downtime, enhance production throughput, and improve product quality, ultimately leading to increased customer satisfaction and competitive advantage.
Technological integration and innovations
Current Technologies
Technological advancements have revolutionized Maintenance Management practices, offering tools like IoT, AI, and machine learning for real-time monitoring and predictive analytics. These technologies enable manufacturers to anticipate equipment failures before they occur, optimizing maintenance schedules and improving equipment reliability. For instance, IoT sensors provide continuous data on machinery health, while AI algorithms predict potential malfunctions based on historical data patterns. This integration facilitates data-driven decision-making, allowing professionals to allocate resources more efficiently and reduce operational costs. By embracing these technologies, manufacturers can enhance their maintenance strategies and achieve higher levels of operational efficiency.
Future Trends
The future of Maintenance Management promises exciting developments, including the widespread adoption of AI-driven maintenance solutions and the integration of digital twins for virtual equipment modeling. These innovations will further enhance predictive capabilities and maintenance accuracy, enabling manufacturers to achieve unprecedented levels of operational efficiency and equipment reliability. AI-driven solutions will offer advanced analytics for deeper insights, while digital twins will provide virtual models for testing and simulations, allowing for more precise maintenance planning. Professionals must prepare to integrate these advancements into their maintenance strategies, ensuring they remain competitive in an evolving industry landscape.
Click here to read our expertly curated top picks!
Tips for do's and don'ts in maintenance management
Do’s | Don’ts |
---|---|
Regularly assess equipment health | Ignore early signs of equipment wear |
Invest in technology integration | Overlook training for staff |
Define clear maintenance objectives | Implement unsystematic maintenance |
Adjust strategies based on data | Rely solely on reactive maintenance |
Promote continuous improvement | Resist changes to existing processes |
Click here to read our expertly curated top picks!
Conclusion
Summary of Key Points
Maintenance Management is essential for optimizing manufacturing efficiency, enhancing equipment reliability, and reducing operational costs. By understanding its principles, techniques, and technological integrations, professionals can develop effective strategies to improve their operations. The strategic application of Maintenance Management ensures high production levels, minimal disruptions, and increased profitability.
Encouraging Ongoing Adaptation
With continuous advancements in technology, professionals are encouraged to stay updated and consider integrating innovative Maintenance Management strategies into their manufacturing processes for enhanced outcomes. Embracing these practices will ensure long-term sustainability and competitive advantage in the industry. As the manufacturing landscape evolves, proactive maintenance remains a critical component of operational excellence.
Navigate Manufacturing Project Success with Meegle
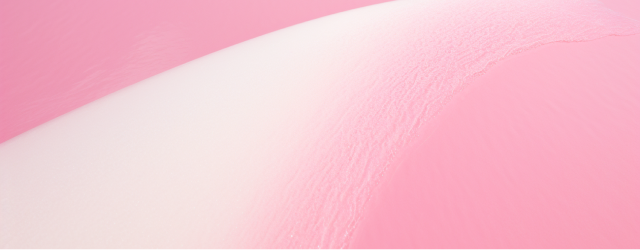
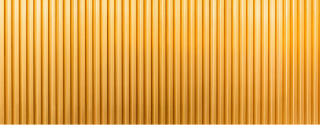
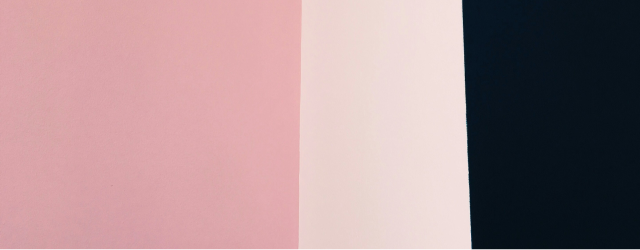
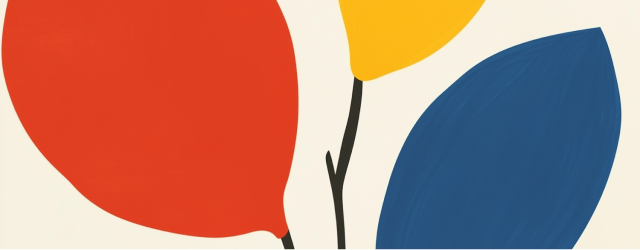
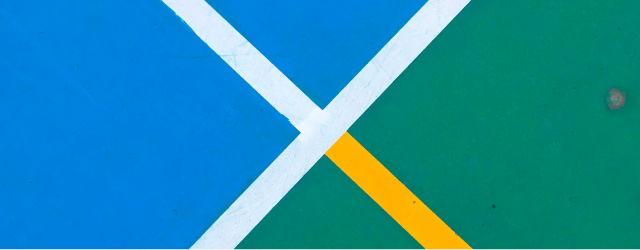
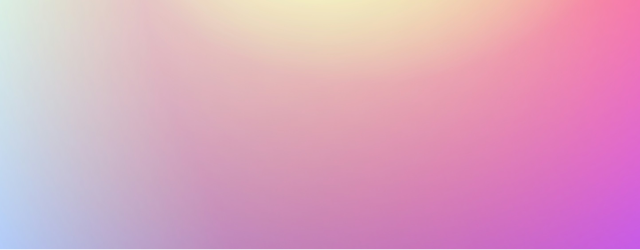
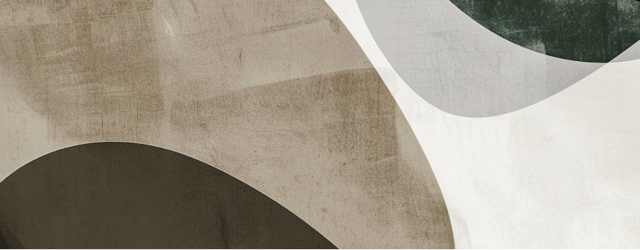
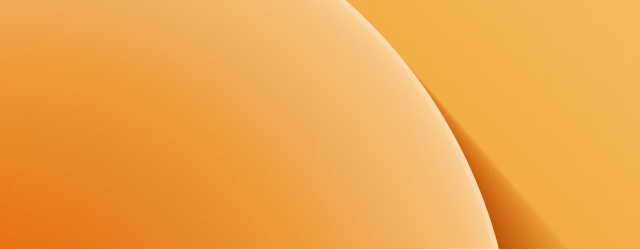