Tool And Die Making
Gain a thorough understanding of Tool and Die Making in manufacturing, with insights into their application, benefits, and strategic importance in the industry.
Overview of Tool and Die Making
In the world of manufacturing, tool and die making stands as a cornerstone in the production process, playing a pivotal role in the creation of precision tools and molds that define product quality and consistency. This specialized craft involves designing and creating tools which are essential for shaping materials into desired forms, and dies, which are used for cutting, shaping, or forming materials. The accuracy and precision of these tools directly impact the final product, making tool and die making a critical component in industries ranging from automotive to consumer electronics.
Tool and die making encompasses various types of tools and dies, each tailored to specific applications. Stamping dies are used to cut and shape sheet metal, while plastic molds are integral in the injection molding process, producing everything from simple plastic containers to complex automotive parts. Forging dies, on the other hand, are used to shape heated metal, contributing to the manufacturing of robust and durable components. Each type of tool and die requires a unique set of skills and knowledge, highlighting the multifaceted nature of this craft.
The importance of tool and die making cannot be overstated. Precision tools ensure not only the consistency of products but also their quality. A poorly designed tool or die can lead to defects, increased waste, and higher production costs. Therefore, the expertise in tool and die making is crucial for manufacturers aiming to maintain high standards of production efficiency and quality control. As industries continue to innovate, the demand for skilled tool and die makers remains strong, underscoring the significance of mastering this craft.
Role in Manufacturing Efficiency
The role of tool and die making in enhancing manufacturing efficiency is paramount. By creating precision tools and dies, manufacturers can significantly reduce waste and improve the accuracy of their production processes. This craft is closely linked to lean manufacturing practices, which emphasize minimizing waste while maximizing productivity. Effective tool design leads to faster production cycles, reduced material usage, and lower operational costs, all of which contribute to a more efficient manufacturing system.
One of the key aspects of tool and die making is its ability to streamline production processes. For instance, a well-designed stamping die can cut and shape materials with minimal waste, ensuring that each piece is identical in size and shape. This uniformity not only enhances product quality but also reduces the need for rework, saving both time and resources. Similarly, precision plastic molds can produce components with intricate details without the need for additional finishing, further speeding up production and reducing costs.
The symbiotic relationship between tool and die making and lean manufacturing is evident in industries such as automotive and aerospace, where precision and efficiency are critical. By investing in high-quality tools and dies, these industries can achieve substantial cost savings and productivity gains. Furthermore, the integration of advanced technologies such as computer-aided design (CAD) and computer-aided manufacturing (CAM) allows for faster and more accurate tool design, further enhancing manufacturing efficiency.
In conclusion, tool and die making is an essential component of modern manufacturing processes. Its ability to reduce waste, improve precision, and streamline production cycles makes it invaluable for manufacturers aiming to achieve high levels of efficiency and quality control. As industries continue to evolve, the demand for skilled tool and die makers will remain strong, highlighting the importance of mastering this craft.
Navigate Manufacturing Project Success with Meegle
Historical development of tool and die making
Origins of Tool and Die Making
The roots of tool and die making can be traced back to ancient civilizations, where early artisans employed basic techniques to craft metalwork and pottery. These rudimentary methods laid the foundation for the sophisticated processes we witness today. In ancient Egypt, for example, metalworkers used simple stone tools to shape copper and bronze, setting the stage for more complex metalworking techniques that would emerge in later centuries. Similarly, in ancient China, artisans developed intricate methods for casting bronze, demonstrating the ingenuity and skill that characterized early die-making practices.
As civilizations advanced, so too did the techniques and tools used in tool and die making. The industrial revolution marked a significant turning point, as mechanized processes began to replace manual labor. The introduction of steam-powered machinery enabled faster and more precise production methods, transforming tool and die making into a vital component of industrial manufacturing. During this period, advancements in metallurgy and engineering allowed for the creation of more durable and efficient tools and dies, laying the groundwork for modern practices.
One of the most notable developments in the history of tool and die making was the emergence of interchangeable parts, pioneered by figures such as Eli Whitney in the late 18th century. This innovation revolutionized manufacturing by allowing for the mass production of standardized components, greatly enhancing efficiency and reducing costs. The concept of interchangeable parts required precision tools and dies, further underscoring the importance of this craft in manufacturing history.
Today, tool and die making continues to evolve, driven by technological advancements and the increasing demand for precision and efficiency. While the fundamental principles remain rooted in history, modern practices have incorporated cutting-edge technologies such as computer-aided design (CAD) and computer-aided manufacturing (CAM), enabling unprecedented levels of complexity and accuracy in tool design and production. As we look to the future, the rich history of tool and die making serves as a testament to its enduring significance in the manufacturing industry.
Evolution Over Time
The evolution of tool and die making has been marked by significant technological advancements that have shaped contemporary practices. From manual methods to automated systems, this craft has undergone a remarkable transformation, driven by the relentless pursuit of precision and efficiency in manufacturing processes. One of the most pivotal shifts in tool and die making was the introduction of Computer Numerical Control (CNC) technology, which revolutionized the industry by automating the cutting and shaping of materials.
CNC technology, which emerged in the mid-20th century, allowed for precise control over machining operations, enabling the production of complex components with minimal human intervention. This automation not only increased productivity but also improved the accuracy and consistency of tool and die making processes. The ability to program machines to perform intricate tasks marked a significant departure from traditional manual methods, setting the stage for more advanced manufacturing techniques.
Another milestone in the evolution of tool and die making was the advent of computer-aided design (CAD) and computer-aided manufacturing (CAM) technologies. These tools enable designers to create detailed digital models of tools and dies, which can then be translated into precise manufacturing instructions. CAD/CAM systems have streamlined the design and production processes, reducing the time and cost associated with tool development. This integration of digital technology has empowered manufacturers to produce highly customized and complex tools with ease.
In recent years, the emergence of additive manufacturing, or 3D printing, has introduced new possibilities for tool and die making. This technology allows for the creation of intricate shapes and geometries that were previously difficult or impossible to achieve with traditional methods. The ability to rapidly prototype and iterate designs has further accelerated the evolution of tool and die making, enabling manufacturers to respond quickly to changing demands and innovate with greater flexibility.
As we reflect on the evolution of tool and die making, it is clear that technological advancements have played a crucial role in shaping the industry. From CNC machines to CAD/CAM systems and 3D printing, these innovations have driven unprecedented levels of precision and efficiency in manufacturing processes. As technology continues to advance, the future of tool and die making promises even greater possibilities, ensuring its continued relevance and importance in the manufacturing landscape.
Core principles and techniques
Fundamental Concepts
Understanding the fundamental concepts of tool and die making is essential for anyone involved in the production of precision tools and molds. These concepts form the foundation of the craft, guiding the design and fabrication processes to ensure optimal performance and durability. Key principles such as tolerances, material selection, and tool life are critical considerations that impact the quality and efficiency of tool and die making.
Tolerances refer to the permissible limits of variation in the dimensions of a tool or die. Precision is paramount in tool and die making, as even slight deviations can lead to defects, increased waste, and compromised product quality. Establishing tight tolerances ensures that each tool and die meets the exact specifications required for the intended application, resulting in consistent and reliable production outcomes. Achieving precise tolerances requires a deep understanding of machining processes and the ability to control variables that affect dimensional accuracy.
Material selection is another crucial aspect of tool and die making. The choice of materials for tools and dies directly influences their performance, durability, and cost-effectiveness. Factors such as hardness, wear resistance, and thermal conductivity must be considered when selecting materials to ensure they can withstand the demands of the manufacturing process. Common materials used in tool and die making include steel, carbide, and ceramic composites, each offering unique properties that suit specific applications.
The concept of tool life is integral to ensuring the longevity and efficiency of tools and dies in production. Tool life refers to the duration a tool can effectively perform before needing replacement or maintenance. Factors such as material properties, operating conditions, and maintenance practices all contribute to tool life. Implementing proper maintenance protocols, such as regular inspections and timely replacements, can significantly extend tool life, resulting in cost savings and improved production efficiency.
In summary, mastering the fundamental concepts of tool and die making is essential for achieving precision, durability, and efficiency in manufacturing processes. By understanding tolerances, selecting appropriate materials, and optimizing tool life, manufacturers can produce high-quality tools and dies that contribute to consistent and reliable production outcomes. As industries continue to evolve, these core principles remain vital to the success of tool and die making.
Implementation Techniques
The implementation techniques in tool and die making are as diverse as the applications they serve. From milling and drilling to surface grinding and heat treatment, a variety of methods are employed to ensure precision and durability in the production of tools and dies. Each technique plays a crucial role in transforming raw materials into finely crafted components that meet the stringent requirements of modern manufacturing processes.
One of the primary techniques used in tool and die making is milling, a machining process that involves removing material from a workpiece using rotary cutters. Milling is essential for creating complex shapes and features on tools and dies, such as slots, grooves, and contours. The precision and versatility of milling make it a fundamental technique in tool and die making, allowing manufacturers to achieve intricate designs with tight tolerances.
Drilling is another common technique, used to create holes and cavities in workpieces. In tool and die making, drilling is often employed to produce precise holes that serve as mounting points or channels for fluid flow. The accuracy of drilling operations is critical, as even minor deviations can affect the functionality and performance of the tool or die. Advanced drilling equipment, such as CNC drills, ensures that holes are positioned and sized correctly, contributing to the overall quality of the final product.
Surface grinding is a finishing technique that enhances the smoothness and precision of tool and die surfaces. By removing small amounts of material, surface grinding achieves the desired surface finish and dimensional accuracy. This technique is particularly important for tools and dies that require tight tolerances and high-quality finishes, such as molds used in injection molding processes. Surface grinding ensures that the final product is free from imperfections and ready for use in production.
The role of heat treatment in tool and die making is crucial for enhancing tool durability and performance. Heat treatment involves altering the microstructure of materials through controlled heating and cooling processes, improving their hardness and wear resistance. Techniques such as annealing, quenching, and tempering are employed to achieve the desired material properties, ensuring that tools and dies can withstand the demands of manufacturing operations.
In conclusion, the successful implementation of techniques such as milling, drilling, surface grinding, and heat treatment is essential for achieving precision and durability in tool and die making. By employing these methods, manufacturers can produce high-quality tools and dies that meet the exacting standards of modern production processes. As technology continues to advance, the refinement and optimization of these techniques will remain a key focus for tool and die makers.
Click here to read our expertly curated top picks!
Benefits and challenges
Advantages in Production
The advantages of tool and die making in production are manifold, contributing to higher quality and efficiency in manufacturing processes. By employing precision tools and dies, manufacturers can achieve consistency across production batches, reduce material waste, and realize cost savings. The ability to produce customized tools tailored to specific applications further enhances production outcomes, making tool and die making an invaluable asset to industries worldwide.
One of the primary benefits of tool and die making is its contribution to higher production quality. Precision tools and dies ensure that each component is manufactured to exact specifications, resulting in products that meet stringent quality standards. This consistency not only enhances the reputation of manufacturers but also reduces the need for rework, saving time and resources. By investing in high-quality tools and dies, companies can achieve superior product quality, which is essential for maintaining competitiveness in today's market.
Another significant advantage is the cost-effectiveness of tool and die making. While the initial investment in precision tools and dies may be substantial, the long-term savings are considerable. Customized tools designed for specific applications can significantly reduce material waste, leading to cost savings in raw materials and production processes. Additionally, precision tooling minimizes the likelihood of defects and rework, further reducing costs associated with production errors. The ability to produce high-quality products efficiently translates into increased profitability for manufacturers.
The role of precision tooling in achieving consistency across production batches is crucial for industries that require standardized components. Whether in automotive manufacturing or consumer electronics, consistency ensures that each product performs reliably and meets customer expectations. Precision tools and dies enable manufacturers to produce identical components with minimal variation, reducing the risk of defects and enhancing overall product quality. This consistency is vital for maintaining customer satisfaction and building long-term relationships.
In summary, the advantages of tool and die making in production are clear. From higher production quality to cost-effectiveness and consistency, precision tools and dies offer significant benefits to manufacturers across various industries. By investing in high-quality tooling and embracing the principles of tool and die making, companies can achieve superior production outcomes and maintain a competitive edge in the marketplace.
Potential Limitations
Despite the numerous advantages, tool and die making is not without its challenges. High initial costs, complex design requirements, and tool wear are some of the limitations that manufacturers face when implementing tool and die making processes. Addressing these challenges is essential for maximizing the benefits of precision tooling and ensuring optimal production outcomes.
One of the most significant limitations of tool and die making is the high initial costs associated with equipment and tooling. Precision tools and dies require significant investment in terms of design, fabrication, and maintenance. The cost of advanced technologies such as CNC machines and CAD/CAM systems can be substantial, posing a barrier to entry for some manufacturers. However, the long-term benefits of precision tooling often outweigh the initial expenses, as the savings in production costs and improved product quality can lead to increased profitability.
Complex design requirements present another challenge in tool and die making. Designing tools and dies that meet the exact specifications of a given application requires a deep understanding of material properties, machining processes, and production constraints. The complexity of these designs can make the tool and die making process time-consuming and resource-intensive. Collaboration between designers, engineers, and production teams is essential to overcome these challenges and ensure that tools and dies are designed effectively.
Tool wear is an inherent limitation in tool and die making, as the constant use of tools and dies leads to deterioration over time. Regular maintenance and updates are necessary to ensure that tools perform optimally and maintain their precision. This requirement for ongoing maintenance can be resource-intensive, but neglecting it can lead to increased downtime, reduced productivity, and compromised product quality. Implementing proper maintenance protocols and investing in high-quality materials can help mitigate the impact of tool wear.
To overcome these challenges, manufacturers can invest in modern technologies and training for die makers. By embracing advanced technologies such as CNC machines and CAD/CAM systems, companies can streamline the design and production processes, reducing costs and improving efficiency. Additionally, training programs for die makers can enhance their skills and knowledge, enabling them to tackle complex design requirements with confidence.
In conclusion, while tool and die making presents several challenges, these limitations can be addressed through strategic investment in technology and training. By recognizing and overcoming these obstacles, manufacturers can maximize the benefits of precision tooling and achieve superior production outcomes.
Case studies and real-world applications
Industry examples
Industry examples
Tool and die making has been the backbone of various industries, each harnessing its precision and efficiency to drive production quality and innovation. Notably, industries such as automotive, aerospace, and consumer electronics have integrated tool and die making processes to enhance their manufacturing capabilities.
In the automotive sector, companies like General Motors have embraced tool and die making for producing components with intricate geometries and tight tolerances. The precision tooling used in the production of engine parts and body panels ensures consistency and quality, which are paramount in automotive manufacturing. By investing in high-quality tools and dies, General Motors has been able to achieve superior product quality and reduce production costs, maintaining its competitive edge in the industry.
Similarly, the aerospace industry has benefited from the precision and customization offered by tool and die making. Boeing, a leading aerospace manufacturer, utilizes advanced tooling techniques to produce components for aircraft with exceptional accuracy and durability. The integration of tool and die making in aerospace manufacturing allows for the production of lightweight and robust components that meet stringent safety and performance standards. This precision is crucial for ensuring the reliability and efficiency of aircraft in demanding conditions.
In the consumer electronics industry, companies like Apple have leveraged tool and die making to produce intricate components used in smartphones and other electronic devices. The ability to create complex designs with high precision is essential for achieving the sleek and functional products that consumers demand. By utilizing precision tooling, Apple ensures consistency across its production batches, maintaining the high quality and reliability of its products.
These industry examples highlight the significant impact of tool and die making on production quality and efficiency. The ability to produce customized and precise components allows these companies to maintain their competitive advantage and deliver products that meet the demanding requirements of their industries.
Impact analysis
Impact analysis
Conducting an impact analysis of tool and die making in specific industries reveals measurable improvements in production speed and product quality. The precision and efficiency of tooling processes contribute to enhanced operational outcomes, enabling manufacturers to innovate and customize products with greater flexibility.
In the automotive industry, tool and die making has led to productivity gains by reducing the time required for manufacturing processes. Precision tools and dies enable faster production cycles, allowing manufacturers to meet increasing demands for automotive components without sacrificing quality. Statistical data from industry reports indicate that companies utilizing advanced tool and die making techniques have achieved a reduction in production times by up to 30%, resulting in cost savings and increased profitability.
The aerospace industry has witnessed similar benefits, with tool and die making contributing to the production of high-quality components that meet stringent safety and performance standards. Advanced tooling processes allow for the creation of lightweight and durable components, enhancing the efficiency of aircraft and reducing fuel consumption. Industry experts estimate that precision tooling has contributed to a 20% improvement in aerospace manufacturing efficiency, translating into significant cost savings and improved operational outcomes.
In the consumer electronics sector, tool and die making has enabled the production of intricate components with precision, meeting the demands for sleek and functional devices. By leveraging advanced tooling techniques, manufacturers can achieve consistency in production batches, ensuring that each component meets the exact specifications required for high-quality electronic devices. This precision is crucial for maintaining customer satisfaction and brand reputation.
Overall, the impact analysis of tool and die making in various industries underscores its significance in driving production efficiency and product quality. The ability to innovate and customize products with precision tooling allows manufacturers to remain competitive and respond to changing market demands with agility.
Click here to read our expertly curated top picks!
Technological integration and innovations
Current Technologies
The integration of current technologies in tool and die making has transformed the industry, enhancing precision and efficiency in manufacturing processes. Technologies such as computer-aided design (CAD), computer-aided manufacturing (CAM), and CNC machines have revolutionized tool and die making, enabling the creation of complex and customized components with unmatched accuracy.
CAD/CAM software provides manufacturers with powerful tools for designing and producing precision tools and dies. By creating detailed digital models, designers can visualize the final product and optimize its features before production begins. CAD/CAM systems streamline the design process, reducing the time and cost associated with tool development. This technology enables manufacturers to produce highly customized tools that meet specific requirements, enhancing product quality and efficiency.
CNC machines have automated the machining processes, allowing for precise control over cutting, milling, and drilling operations. These machines reduce the need for manual intervention, increasing productivity and improving the consistency of tool and die making processes. CNC technology enables the production of intricate components with tight tolerances, contributing to higher quality and efficiency in manufacturing. The accuracy and speed of CNC machines have made them indispensable in tool and die making.
The integration of IoT and AI in tool design and production has further improved efficiency and precision. IoT sensors collect data on tool performance, providing real-time insights into operational conditions and enabling predictive maintenance. AI algorithms analyze data to optimize tool design, enhancing performance and reducing wear. This integration of IoT and AI empowers manufacturers to achieve greater efficiency and accuracy, ensuring that tools and dies meet the exacting standards of modern production processes.
In addition to these technologies, the use of advanced materials such as carbide and ceramic composites has enhanced tool durability and performance. These materials offer superior hardness and wear resistance, ensuring that tools can withstand the demands of manufacturing operations. The use of advanced materials extends tool life, resulting in cost savings and improved production efficiency.
Future Trends
The future of tool and die making promises exciting developments and innovations that will further enhance the precision and efficiency of manufacturing processes. As industries continue to evolve, emerging trends such as smart manufacturing, automation, and data analytics offer new possibilities for tool and die making.
Smart manufacturing is poised to revolutionize tool and die making by integrating advanced technologies such as IoT and AI into production processes. Smart systems will enable real-time monitoring and optimization of tool performance, reducing downtime and enhancing efficiency. The ability to collect and analyze data will empower manufacturers to make informed decisions, ensuring that tools and dies are designed and fabricated to meet the exacting standards of modern production.
Further automation will drive the evolution of tool and die making, reducing the need for manual intervention and increasing productivity. Automated systems will enable faster production cycles, allowing manufacturers to respond to changing demands with agility. The integration of robotics and machine learning will enhance the precision and accuracy of tool and die making processes, contributing to higher quality and efficiency.
The use of data analytics will optimize tool design, enabling manufacturers to achieve greater precision and customization. By analyzing data on material properties, machining processes, and operational conditions, manufacturers can refine tool designs to meet specific requirements. The ability to leverage data insights will enhance the performance and durability of tools and dies, resulting in cost savings and improved production outcomes.
Emerging materials and technologies such as nanotechnology and bio-inspired designs offer new possibilities for tool and die making. These innovations will enable the creation of tools with enhanced properties, such as increased hardness and wear resistance. The use of advanced materials will further extend tool life, contributing to cost savings and improved efficiency.
Click here to read our expertly curated top picks!
Tips for successful tool and die making
Do's and Dont's
Navigating the complexities of tool and die making requires adherence to best practices and the avoidance of common pitfalls. By following practical tips, professionals can enhance their skills and ensure successful outcomes in tool and die making processes.
Do's | Don'ts |
---|---|
Regularly update your skills with new technologies and methods. | Neglect the importance of quality control and testing. |
Invest in high-quality materials for longer tool life. | Overlook regular maintenance and updates of tools. |
Collaborate with designers to ensure practical tool designs. | Ignore feedback from production teams regarding tool performance. |
These actionable do's and don'ts provide valuable guidance for professionals in tool and die making, helping them navigate the complexities of the craft and achieve optimal production outcomes.
Faqs about tool and die making
Common Questions
Understanding the intricacies of tool and die making requires clarification of common uncertainties. This FAQ section addresses frequently asked questions to provide insights into the craft and its significance.
What is the difference between a tool and a die?
A tool is a device used to shape or form materials, while a die is a specialized tool used for cutting, shaping, or forming materials. Both tools and dies are essential in manufacturing processes, contributing to precision and efficiency.
How does tool wear impact production efficiency?
Tool wear can lead to decreased precision and increased downtime, affecting production efficiency. Regular maintenance and updates are necessary to ensure that tools perform optimally and maintain their accuracy.
What are the key factors to consider in tool design?
Key factors in tool design include tolerances, material selection, and tool life. Precision and accuracy are critical considerations that impact the quality and efficiency of tool and die making processes.
How has technology transformed Tool and Die Making?
Technology has revolutionized tool and die making by introducing advanced technologies such as CAD/CAM, CNC machines, and IoT sensors. These innovations have enhanced precision, efficiency, and customization in manufacturing processes.
What training is essential for becoming a skilled die maker?
Training in tool design, machining techniques, and material properties is essential for becoming a skilled die maker. Continuous learning and adaptation to new technologies are crucial for success in the ever-evolving field of tool and die making.
Click here to read our expertly curated top picks!
Conclusion
Summary of Key Points
Tool and die making is an essential component of modern manufacturing processes, offering significant benefits in terms of precision, efficiency, and customization. Throughout the article, we have explored the historical evolution, current practices, and future trends in tool and die making. The integration of advanced technologies such as CAD/CAM software, CNC machines, and IoT sensors has revolutionized the industry, enabling manufacturers to produce high-quality tools and dies with precision and efficiency.
The advantages of tool and die making are clear, from higher production quality to cost-effectiveness and consistency. Precision tools and dies contribute to superior product quality, reduced material waste, and increased profitability. By investing in high-quality tooling and embracing the principles of tool and die making, companies can achieve optimal production outcomes and maintain a competitive edge in the marketplace.
Encouraging Ongoing Adaptation
As industries continue to evolve, it is essential for professionals to stay updated with technological advancements and consider integrating tool and die making into their manufacturing strategies. Continuous learning and adaptation are vital for success in the ever-evolving field of tool and die making. By embracing new technologies and refining their skills, professionals can enhance their capabilities and achieve superior production outcomes.
In conclusion, tool and die making remains a critical component of modern manufacturing processes, offering significant benefits in precision, efficiency, and customization. By mastering the techniques and staying updated with technological advancements, professionals can ensure optimal production outcomes and maintain their competitive edge in the marketplace.
Navigate Manufacturing Project Success with Meegle
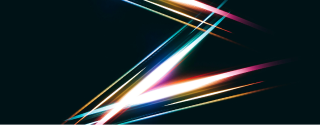
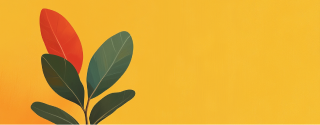
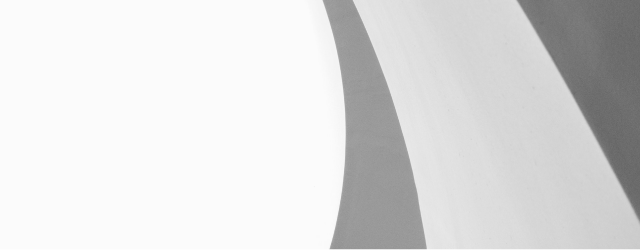
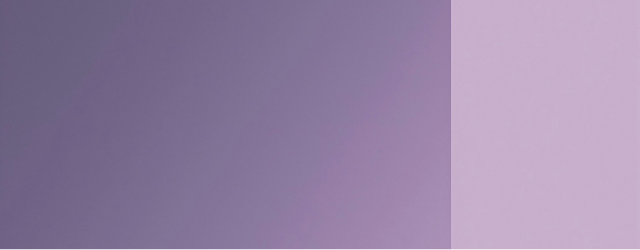
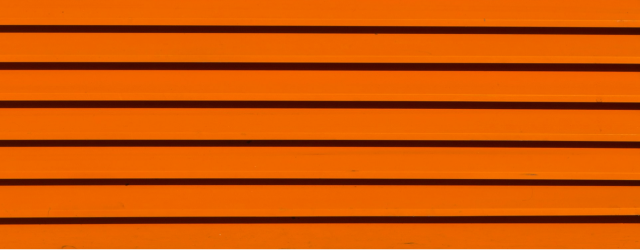
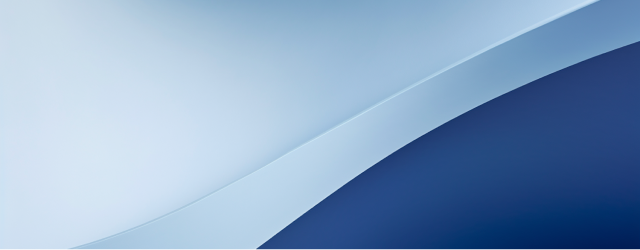
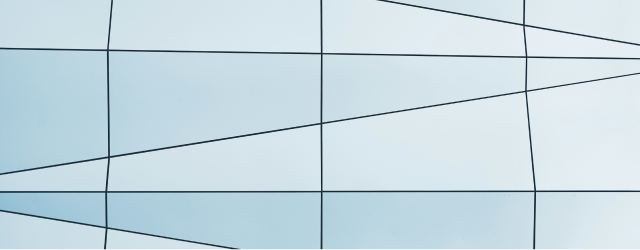
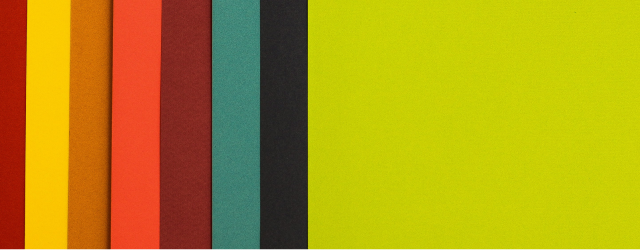