Sand Casting
Gain a thorough understanding of Sand Casting in manufacturing, with insights into their application, benefits, and strategic importance in the industry.
Overview of Sand Casting
Defining Sand Casting and Its Vital Role in Manufacturing
Sand casting is a manufacturing process that involves creating a mold from sand and then pouring molten metal into the mold to form a desired shape. This technique is revered for its versatility, allowing manufacturers to produce metal parts that range from a few grams to several tons in weight. Crucially, sand casting plays a vital role in industries such as automotive, aerospace, and heavy machinery, where it helps fabricate components that require precision and durability. The process can accommodate a wide range of metals, including aluminum, bronze, and cast iron, making it highly adaptable to diverse manufacturing needs.
One of the core advantages of sand casting is its cost-effectiveness. Compared to other casting methods like die casting or investment casting, sand casting requires relatively inexpensive materials and equipment. This affordability, coupled with its ability to produce complex shapes without extensive machining, makes it an attractive option for manufacturers striving to minimize production costs. For example, in the automotive industry, where production volumes are high, the ability to create intricate engine parts with minimal material wastage is invaluable. Sand casting also supports the production of both small and large components, providing the flexibility needed in various manufacturing contexts.
Moreover, sand casting contributes significantly to manufacturing efficiency. By leveraging the inherent properties of sand, which can be compacted and shaped with precision, manufacturers can achieve intricate designs and high dimensional accuracy. This precision is crucial in industries such as aerospace, where even minor deviations in component specifications can have critical implications. The automotive sector offers a prime example: here, sand casting is used to produce engine blocks, a process that benefits from the ability to create complex internal geometries that optimize fuel efficiency and performance. In summary, sand casting is a keystone technique in modern manufacturing, offering a harmonious blend of cost-effectiveness and precision that meets the complex demands of today's industrial landscape.
Role in Manufacturing Efficiency
Enhancing Operational Efficiency and Product Quality through Sand Casting
The integration of sand casting techniques in manufacturing operations significantly enhances efficiency and product quality. One of the primary ways sand casting achieves this is through its ability to streamline production cycles. By reducing the need for extensive machining, sand casting allows manufacturers to produce intricate components quickly and with less resource consumption. This efficiency is particularly beneficial in industries where time-to-market is a critical factor, such as consumer electronics and automotive sectors.
A notable example can be seen in the automotive industry, where a streamlined production cycle directly translates to increased competitiveness. For instance, the production of engine components using sand casting techniques allows for rapid prototyping and iteration, reducing lead times and enabling manufacturers to respond swiftly to market demands. Furthermore, sand casting's adaptability to a wide range of metal alloys ensures that manufacturers can tailor their production processes to meet specific material properties and performance criteria.
In addition to operational efficiency, sand casting also contributes to enhanced product quality. The process allows for the creation of components with complex geometries and fine details, which are often challenging to achieve through other manufacturing methods. By utilizing specialized sand mixtures and advanced molding techniques, manufacturers can produce castings with high dimensional accuracy and superior surface finishes. This precision is crucial in industries like aerospace, where even the slightest imperfections can compromise structural integrity and performance.
Moreover, sand casting helps reduce environmental impact by minimizing material wastage. Unlike machining processes that cut away excess material, sand casting forms components directly from molten metal, resulting in less scrap and resource consumption. Manufacturers can further enhance sustainability by implementing closed-loop systems for sand reclamation and recycling, aligning with industry trends towards eco-friendly practices. Overall, sand casting's contribution to manufacturing efficiency and product quality makes it an indispensable technique, enabling businesses to achieve operational excellence while meeting the demands of a rapidly evolving market.
Navigate Manufacturing Project Success with Meegle
Historical development of sand casting
Origins of Sand Casting
Tracing the Historical Roots of Sand Casting
The origins of sand casting can be traced back to ancient civilizations, where innovative artisans harnessed the natural properties of sand to create functional and decorative objects. Evidence of early sand casting techniques has been discovered in regions such as Egypt and China, where artisans crafted intricate jewelry, tools, and ceremonial objects using rudimentary sand molds. These early practitioners recognized the versatility of sand as a mold material, appreciating its ability to withstand high temperatures and retain intricate details.
In ancient Egypt, for instance, sand casting was employed to produce bronze statues and religious artifacts. The process involved creating a pattern of the desired object, surrounding it with sand to form a mold, and then pouring molten bronze into the cavity. After cooling, the mold would be broken away, revealing the final cast object. This early adoption of sand casting not only facilitated the creation of complex shapes but also enabled the production of multiple copies of the same design, laying the foundation for mass production techniques.
Similarly, in ancient China, sand casting was used to produce a wide array of metal implements, from agricultural tools to weaponry. The Chinese artisans refined the process by developing specialized sand mixtures that improved mold durability and casting precision. This refinement allowed for the production of intricate castings, such as the famous bronze vessels and bells of the Shang and Zhou dynasties. These artifacts, which feature intricate patterns and inscriptions, demonstrate the advanced skill and craftsmanship of early sand casters.
As sand casting techniques spread across different cultures, they evolved in response to local materials and technological advancements. By the time of the Industrial Revolution, sand casting had become a well-established method for producing metal parts on a larger scale. The development of more sophisticated machinery and materials during this period enabled further refinement of sand casting techniques, paving the way for its widespread adoption in modern manufacturing. In summary, the historical development of sand casting is a testament to human ingenuity and adaptability, showcasing how this ancient technique has evolved to meet the changing needs of society over millennia.
Evolution Over Time
Technological and Methodological Advancements in Sand Casting
Over the centuries, sand casting has undergone significant technological and methodological advancements, evolving from simple hand-crafted processes to sophisticated techniques incorporating cutting-edge technologies. One of the key innovations that revolutionized sand casting was the introduction of green sand molds. Green sand, a mixture of sand, clay, and water, offers excellent moldability and reusability, making it a preferred choice for many foundries. This development marked a departure from earlier methods that relied on dry sand molds, which were less versatile and more labor-intensive.
Another major advancement in sand casting came with the introduction of chemically bonded sand molds. These molds use chemical binders to enhance mold strength and durability, allowing for greater precision and reduced production time. The use of chemically bonded sand molds has been particularly beneficial in industries that require high-quality castings with intricate details, such as aerospace and automotive sectors. This innovation has enabled manufacturers to achieve exceptional dimensional accuracy and surface finishes, even in complex geometries.
In recent years, the integration of digital technologies has further transformed sand casting processes. The adoption of computer-aided design (CAD) and computer-aided manufacturing (CAM) systems has streamlined the design and production of molds, enabling greater precision and customization. These digital tools allow engineers to simulate casting processes, optimize mold designs, and predict potential defects before physical production begins. This capability not only reduces material wastage and rework but also accelerates the development of new products.
Moreover, advancements in automation and robotics have enhanced the efficiency and consistency of sand casting operations. Automated molding machines and robotic arms can perform repetitive tasks with high precision, reducing the reliance on manual labor and minimizing the risk of human error. These technologies have enabled foundries to increase production capacity while maintaining high-quality standards, meeting the demands of modern manufacturing environments.
In conclusion, the evolution of sand casting has been characterized by continuous innovation and adaptation to new technologies, ensuring its continued relevance in the manufacturing industry. By embracing these advancements, manufacturers can harness the full potential of sand casting to produce high-quality components efficiently and cost-effectively.
Click here to read our expertly curated top picks!
Core principles and techniques
Fundamental Concepts
Key Concepts and Principles Underpinning Sand Casting
At the heart of sand casting are several fundamental concepts and principles that govern the creation of molds and the casting process. Understanding these core principles is essential for achieving successful outcomes in sand casting operations. One of the primary concepts in sand casting is mold design. The mold serves as the cavity into which molten metal is poured, and its design must account for factors such as shrinkage, draft angles, and parting lines. These considerations ensure that the final casting accurately reflects the desired shape and dimensions.
Another crucial principle in sand casting is sand composition. The properties of the sand used in the mold significantly impact the casting's quality and accuracy. Foundries typically use a mixture of sand, clay, and water, known as green sand, for its excellent moldability and reusability. The sand's grain size, moisture content, and clay content must be carefully controlled to achieve the desired mold strength and surface finish. In some cases, chemically bonded sand is used for more precise or complex castings, offering greater strength and dimensional stability.
Metal pouring techniques also play a vital role in sand casting. The pouring process involves transferring molten metal into the mold cavity, and it must be executed with precision to prevent defects such as porosity or incomplete fill. Foundries must carefully control the temperature and flow rate of the molten metal to ensure proper mold filling and solidification. Additionally, the use of risers and gating systems helps manage the flow of metal, reducing the risk of defects and ensuring uniform cooling.
Gating and riser design are another critical aspect of sand casting. The gating system directs the flow of molten metal into the mold cavity, while risers provide a reservoir of additional metal to compensate for shrinkage during solidification. Proper design and placement of these elements are essential to minimize defects and ensure uniform filling of the mold. Considerations such as the size and location of gates, the number and positioning of risers, and the use of chills (metal inserts used to control cooling rates) must be carefully evaluated.
In conclusion, the fundamental concepts of mold design, sand composition, metal pouring, and gating systems form the backbone of sand casting. By mastering these principles, manufacturers can achieve high-quality castings with precision and consistency, meeting the demands of diverse industrial applications.
Implementation Techniques
Exploring Various Sand Casting Techniques and Methods
The implementation of sand casting encompasses a wide array of techniques, each tailored to specific requirements and material properties. This diversity of methods ensures adaptability across different manufacturing contexts, enabling foundries to produce high-quality metal castings efficiently and cost-effectively.
One of the most common sand casting techniques is the use of green sand molds. Green sand, composed of sand, clay, and water, is renowned for its moldability and reusability. This technique is widely employed in the production of cast iron components, offering an excellent balance between cost-effectiveness and quality. Green sand casting is ideal for producing large volumes of parts with relatively simple shapes, such as engine blocks and pipe fittings.
Another widely used sand casting method is shell molding, which involves creating a thin shell of sand bonded with a thermosetting resin. The shell provides excellent surface finish and dimensional accuracy, making it suitable for producing intricate castings with fine details. Shell molding is often used in the automotive and aerospace industries, where precision and surface quality are paramount. The process is particularly advantageous for small to medium-sized parts with complex geometries.
Investment casting, also known as lost wax casting, is a specialized sand casting technique used for producing exceptionally precise and intricate components. The process involves creating a wax pattern of the desired part, coating it with a ceramic shell, and then melting out the wax to form a mold. Investment casting is widely used in the production of turbine blades, medical implants, and jewelry, where tight tolerances and intricate designs are required. While more expensive than traditional sand casting methods, investment casting delivers unparalleled precision and surface quality.
In addition to these techniques, foundries may employ variations such as vacuum casting and centrifugal casting, each offering unique advantages for specific applications. Vacuum casting, for example, creates a vacuum within the mold to reduce gas porosity and improve surface finish, making it ideal for components requiring high integrity. Centrifugal casting utilizes centrifugal force to distribute molten metal evenly within the mold, resulting in castings with uniform density and mechanical properties, commonly used for cylindrical parts like pipes and bushings.
In conclusion, the diverse range of sand casting techniques ensures that manufacturers can select the most suitable method for their specific needs, balancing cost, quality, and production volume. By exploring and mastering these techniques, foundries can deliver high-quality castings that meet the diverse demands of modern manufacturing.
Benefits and challenges
Advantages in Production
Benefits of Sand Casting in Manufacturing Processes
Sand casting offers numerous advantages that make it an invaluable technique in manufacturing, particularly when it comes to production processes. One of the primary benefits of sand casting is its cost-effectiveness. Compared to other casting methods, such as die casting or investment casting, sand casting requires relatively inexpensive materials and equipment. This affordability is particularly advantageous for manufacturers producing large volumes of parts, as it helps keep production costs low.
Another significant advantage of sand casting is its flexibility in design. The process allows for the production of complex shapes and intricate geometries that would be challenging to achieve with other manufacturing methods. This flexibility is crucial in industries such as automotive and aerospace, where components often require intricate internal passages and fine details. For example, sand casting enables the production of complex engine components with optimized designs that enhance performance and fuel efficiency.
Sand casting also excels in producing large parts with consistent quality. The process can accommodate a wide range of metal alloys, including aluminum, bronze, and cast iron, offering manufacturers the flexibility to choose materials based on specific application requirements. This adaptability is particularly beneficial in the heavy machinery industry, where large castings are often used for components such as gear housings and pump casings.
Furthermore, sand casting supports rapid prototyping and iteration, allowing manufacturers to quickly develop and refine new products. By using easily modifiable sand molds, foundries can produce prototypes and conduct testing without the need for expensive tooling or extensive rework. This capability accelerates product development cycles and provides a competitive edge in markets where innovation and speed are key differentiators.
In addition to these advantages, sand casting contributes to environmental sustainability by minimizing material wastage. Unlike machining processes that remove material to create the final shape, sand casting forms components directly from molten metal, resulting in less scrap and resource consumption. Manufacturers can further enhance sustainability by implementing closed-loop systems for sand reclamation and recycling, aligning with industry trends towards eco-friendly practices.
In summary, the benefits of sand casting in manufacturing processes are manifold, offering cost-effectiveness, design flexibility, and environmental sustainability. By leveraging these advantages, manufacturers can achieve operational excellence and deliver high-quality products that meet the demands of a rapidly evolving market.
Potential Limitations
Challenges and Limitations Associated with Sand Casting
Despite its many advantages, sand casting is not without its challenges and limitations. One of the primary challenges associated with sand casting is achieving high surface finish quality. The inherent texture of sand molds can result in a rough surface finish on the final casting, which may require additional machining or finishing processes to meet specific aesthetic or functional requirements. This can increase production costs and lead times, particularly for components with tight tolerances or complex geometries.
Another limitation of sand casting is dimensional accuracy. While the process is capable of producing complex shapes, achieving precise dimensions and tolerances can be challenging due to factors such as mold degradation and metal shrinkage during solidification. Variations in sand composition, moisture content, and compacting pressure can also impact mold stability and dimensional consistency. To address these challenges, manufacturers must implement rigorous quality control measures and utilize advanced mold design techniques to minimize deviations and ensure consistency.
Mold degradation is another significant issue in sand casting, particularly in high-volume production environments. Repeated use of sand molds can lead to wear and degradation, resulting in defects such as mold distortion, surface irregularities, and poor dimensional accuracy. To mitigate these issues, foundries may need to invest in mold maintenance and repair, as well as regularly replace worn-out molds to maintain product quality and consistency.
Furthermore, sand casting can pose environmental challenges, particularly in terms of waste generation and energy consumption. The process generates significant amounts of sand waste, which can pose disposal challenges if not properly managed. Additionally, the energy-intensive nature of melting and pouring metal can contribute to increased energy consumption and greenhouse gas emissions. To address these environmental concerns, manufacturers must implement sustainable practices such as sand recycling, energy-efficient melting technologies, and emissions control measures.
In conclusion, while sand casting offers numerous benefits, it is important for manufacturers to be aware of its limitations and challenges. By understanding and addressing these issues, manufacturers can optimize their sand casting processes to achieve high-quality outcomes while minimizing costs and environmental impact. Through continuous innovation and improvement, sand casting can remain a valuable and effective manufacturing technique for a wide range of applications.
Click here to read our expertly curated top picks!
Case studies and real-world applications
Industry examples
Industry examples
Successful Implementation of Sand Casting in Various Industries
Sand casting finds widespread application across diverse industries, each leveraging its strengths to achieve unique production goals. These real-world examples illustrate the versatility and impact of sand casting in different manufacturing contexts.
In the automotive industry, sand casting plays a crucial role in the production of engine components such as cylinder heads and engine blocks. For instance, Ford Motor Company's Windsor Engine Plant in Canada utilizes sand casting to manufacture aluminum engine blocks for their vehicles. The plant's advanced sand casting techniques enable the production of complex internal geometries that optimize engine performance and fuel efficiency. By employing sand casting, Ford achieves a balance between cost-effectiveness and high-quality output, maintaining competitiveness in a market driven by innovation and performance.
The aerospace industry also relies heavily on sand casting for the production of critical components. Rolls-Royce, a renowned manufacturer of aircraft engines, uses sand casting to produce turbine blades and other complex parts for their engines. The precision and flexibility of sand casting allow Rolls-Royce to create intricate designs that enhance engine efficiency and reliability. The use of advanced sand casting techniques, combined with rigorous quality control measures, ensures that the components meet the stringent safety and performance standards required in the aerospace sector.
In the heavy equipment manufacturing industry, companies like Caterpillar utilize sand casting to produce large castings used in construction and mining equipment. The process enables the production of robust components such as gear housings and pump casings, which are essential for the reliable operation of heavy machinery. Sand casting's ability to produce large parts with consistent quality and material properties makes it an ideal choice for heavy equipment manufacturers seeking durability and performance in demanding environments.
Furthermore, the energy sector benefits from sand casting's capabilities in producing components for power generation equipment. General Electric (GE) uses sand casting to manufacture turbine casings and other critical parts for their power plants. The process allows GE to create complex components that withstand high temperatures and pressures, ensuring the reliability and efficiency of their power generation systems.
These industry examples demonstrate the diverse applications and advantages of sand casting across various sectors. By harnessing the process's flexibility, cost-effectiveness, and precision, manufacturers can achieve their production goals and maintain a competitive edge in their respective industries.
Impact analysis
Impact analysis
Analyzing Tangible Impacts of Sand Casting in Real-World Scenarios
In real-world applications, the impacts of sand casting techniques are evident in improved product performance, reduced lead times, and enhanced competitive advantage. Analyzing specific case studies provides valuable insights into how sand casting has led to tangible improvements in manufacturing outcomes and operational efficiencies.
One case study involves the use of sand casting in the production of hydraulic components for construction machinery. A leading manufacturer faced challenges in meeting the growing demand for hydraulic valves and cylinders while maintaining high-quality standards. By implementing advanced sand casting techniques, the company was able to streamline production processes and reduce lead times significantly. The flexibility of sand casting allowed for rapid prototyping and iteration, enabling the manufacturer to quickly adapt to changing customer requirements. As a result, the company achieved a 20% increase in production capacity and improved its market responsiveness, gaining a competitive edge in the industry.
In the automotive sector, a case study highlights the impact of sand casting on the production of lightweight engine components. A major automotive manufacturer sought to reduce vehicle weight to enhance fuel efficiency and meet stringent emissions regulations. By utilizing sand casting to produce aluminum engine blocks, the manufacturer achieved a 15% reduction in component weight compared to traditional cast iron blocks. This weight reduction contributed to improved fuel economy and reduced emissions, aligning with the industry's sustainability goals. Additionally, the cost-effectiveness of sand casting allowed the manufacturer to maintain profitability while investing in innovative lightweight materials.
The aerospace industry provides another compelling example of sand casting's impact on product performance and safety. A renowned aircraft engine manufacturer implemented sand casting to produce turbine blades with complex internal cooling channels. These advanced designs enhanced the blades' thermal efficiency and durability, resulting in improved engine performance and reliability. The precision and consistency of sand casting ensured that the components met stringent safety and performance standards, contributing to the overall success and reputation of the manufacturer's engines in the aerospace market.
Furthermore, in the renewable energy sector, sand casting has played a pivotal role in the production of wind turbine components. A leading wind turbine manufacturer utilized sand casting to produce large nacelle components and gearbox housings. The process's ability to handle large castings and intricate designs enabled the manufacturer to optimize the performance and efficiency of their turbines. As a result, the company achieved substantial gains in energy output and reliability, strengthening its position in the growing renewable energy market.
These case studies illustrate the tangible benefits of sand casting in real-world scenarios, showcasing its impact on product performance, operational efficiency, and competitive advantage. By leveraging the process's capabilities, manufacturers can achieve their production goals and drive innovation in their respective industries.
Technological integration and innovations
Current Technologies
Technologies Enhancing or Relying on Sand Casting
Current technological advancements have significantly enhanced the capabilities and applications of sand casting, making it a more efficient and precise manufacturing process. One of the primary technologies that have integrated with sand casting is computer-aided design (CAD). CAD systems allow engineers to create detailed and accurate digital models of the components to be cast. These digital models can be used to simulate casting processes, optimize mold designs, and predict potential defects before physical production begins. By identifying and addressing issues in the design phase, manufacturers can reduce material wastage and rework, ultimately leading to cost savings and improved product quality.
Another technology enhancing sand casting is computer-aided manufacturing (CAM). CAM systems automate the production of molds by translating CAD models into precise tool paths for CNC machines. This automation ensures the consistent and accurate creation of molds, reducing the risk of human error and enhancing production efficiency. By integrating CAD and CAM systems, manufacturers can achieve a seamless transition from design to production, accelerating the development of new products and improving overall efficiency.
In addition to CAD and CAM, advancements in automation and robotics have further improved sand casting processes. Automated molding machines and robotic arms can perform repetitive tasks with high precision, reducing the reliance on manual labor and minimizing the risk of defects. These technologies enable foundries to increase production capacity while maintaining high-quality standards, meeting the demands of modern manufacturing environments.
3D printing is another technology that has found applications in sand casting, particularly in the creation of complex molds and prototypes. By using 3D printing, manufacturers can produce intricate mold patterns with exceptional precision and detail, enabling the production of castings with complex geometries that would be challenging to achieve through traditional methods. This technology also facilitates rapid prototyping and iteration, allowing manufacturers to test and refine their designs quickly.
Moreover, advancements in materials science have led to the development of new sand compositions and binders that enhance mold strength and durability. These innovations have improved the quality and consistency of castings, reducing production defects and enhancing overall product performance.
In conclusion, the integration of modern technologies with sand casting has revolutionized the process, enhancing its precision, efficiency, and capabilities. By embracing these advancements, manufacturers can optimize their sand casting operations, achieve high-quality outcomes, and remain competitive in a rapidly evolving industrial landscape.
Future Trends
Predicting Future Developments in Sand Casting Technology
As manufacturing continues to evolve, future trends in sand casting promise exciting advancements that could redefine the process and its applications. Innovations in materials science, sustainability practices, and digitalization are poised to shape the future of sand casting, offering new opportunities for efficiency and precision.
One of the key future trends in sand casting is the development of advanced materials and binders that enhance mold performance. Researchers are exploring the use of novel materials, such as nanocomposites and high-performance ceramics, to improve mold strength, thermal stability, and dimensional accuracy. These advancements could enable the production of castings with even greater precision and surface quality, meeting the demands of industries that require high-performance components.
Sustainability is another area where future trends in sand casting are likely to have a significant impact. As environmental concerns continue to rise, manufacturers are seeking ways to minimize the environmental footprint of sand casting processes. Future developments may include the adoption of eco-friendly binders and sand reclamation systems that reduce waste and energy consumption. Additionally, the integration of renewable energy sources into foundry operations could further enhance the sustainability of sand casting, aligning with global efforts to reduce carbon emissions and promote green manufacturing practices.
Digitalization and Industry 4.0 technologies are also expected to play a crucial role in the future of sand casting. The implementation of the Internet of Things (IoT) devices and sensors within foundries can enable real-time monitoring and data collection, providing valuable insights into process performance and quality control. By leveraging big data analytics and artificial intelligence, manufacturers can optimize sand casting processes, predict defects, and make informed decisions to enhance efficiency and product quality.
Furthermore, advancements in additive manufacturing and 3D printing are likely to influence the future of sand casting. The combination of these technologies could enable the creation of complex molds and patterns with unprecedented precision and customization. This capability could open up new possibilities for the production of customized components and prototypes, catering to the growing demand for personalized and innovative products.
In summary, the future of sand casting is poised for transformative advancements that promise to enhance efficiency, precision, and sustainability. By embracing these trends, manufacturers can stay ahead of the curve and capitalize on new opportunities in the ever-evolving industrial landscape.
Click here to read our expertly curated top picks!
Tips for do's and don'ts in sand casting
Do's | Don'ts |
---|---|
Ensure proper mold preparation for accuracy | Avoid using low-quality sand to prevent defects |
Regularly test and maintain equipment | Don't rush the cooling process, as it can lead to defects |
Implement quality control measures at each stage | Avoid neglecting environmental considerations |
Click here to read our expertly curated top picks!
Faqs about sand casting
Common Questions
Addressing Frequently Asked Questions about Sand Casting
Navigating the intricacies of sand casting can lead to numerous questions from professionals in the field. This section addresses common questions, providing clear and concise answers to facilitate a better understanding of this versatile manufacturing technique.
What is Sand Casting?
A Detailed Explanation of Sand Casting
Sand casting is a manufacturing process that uses sand molds to form complex metal components. It is widely used across various industries for its versatility and efficiency, allowing for the production of parts in a range of sizes and complexities.
How Does Sand Casting Compare to Other Casting Methods?
Comparative Analysis of Sand Casting and Alternative Techniques
Sand casting is often compared to methods like die casting and investment casting. The key differences lie in cost, complexity, and production speed. Sand casting is more cost-effective and suitable for producing large parts, while die casting offers tighter tolerances and is ideal for high-volume production.
What Materials Can Be Used in Sand Casting?
Exploring Material Compatibility in Sand Casting
Sand casting is compatible with a wide range of metals, including aluminum, bronze, and cast iron. Each material is chosen based on specific application requirements, such as strength, weight, and corrosion resistance.
How Can Quality Be Ensured in Sand Casting?
Quality Control Measures in Sand Casting
Ensuring quality in sand casting involves regular mold inspections, precise temperature control, and adherence to industry standards. Implementing rigorous quality control measures at each stage of the process helps achieve consistent and high-quality outcomes.
What Are the Environmental Impacts of Sand Casting?
Understanding Environmental Considerations in Sand Casting
Sand casting can have environmental impacts, such as waste generation and energy consumption. Manufacturers must address these concerns through sustainable practices, such as sand recycling and energy-efficient melting technologies, to minimize environmental footprint.
Conclusion
Summary of Key Points
Recapping the Essential Aspects of Sand Casting
Throughout this comprehensive guide, we have explored the nuances of sand casting, from its historical roots and core principles to its applications and future trends. Sand casting stands as a pivotal manufacturing process, offering a harmonious blend of cost-effectiveness and precision. By understanding its fundamental concepts and implementation techniques, manufacturers can harness its full potential to produce high-quality components efficiently.
The benefits of sand casting are manifold, including flexibility in design, environmental sustainability, and the ability to produce large parts with complex geometries. However, it is essential to address the challenges associated with sand casting, such as surface finish quality and dimensional accuracy, to optimize the process and achieve consistent outcomes.
Through real-world examples and case studies, we have seen how sand casting contributes to improved product performance and operational efficiency across various industries. As technological advancements continue to shape the manufacturing landscape, sand casting is poised for exciting developments that promise to enhance its capabilities and applications.
Encouraging Ongoing Adaptation
Promoting Integration of Sand Casting in Manufacturing Strategies
As manufacturing landscapes continue to shift, professionals must remain adaptable, embracing techniques like sand casting to drive innovation and efficiency. By staying updated on the latest trends and advancements in sand casting technology, manufacturers can identify new opportunities and enhance their production processes.
Incorporating sand casting into manufacturing strategies requires a commitment to continuous improvement and a willingness to embrace new technologies. By integrating digital tools, automation, and sustainable practices, manufacturers can optimize their sand casting operations and achieve long-term success.
Ultimately, sand casting remains a valuable and effective manufacturing technique, offering versatility and precision that meet the demands of a rapidly evolving industrial landscape. By leveraging its strengths and addressing its challenges, manufacturers can achieve their production goals and maintain a competitive edge in their respective industries.
Navigate Manufacturing Project Success with Meegle
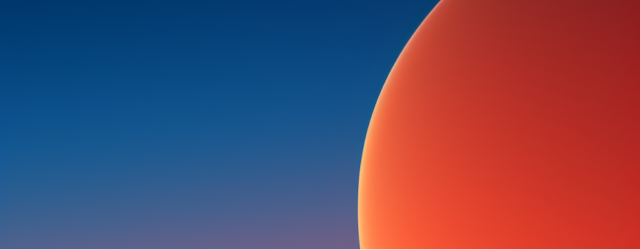
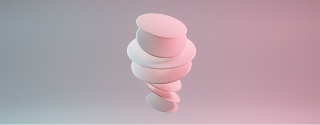
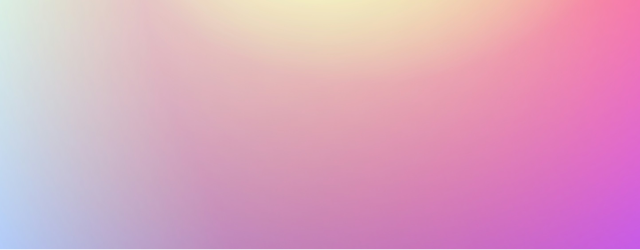
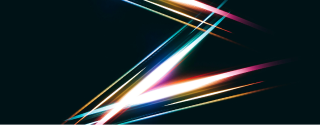
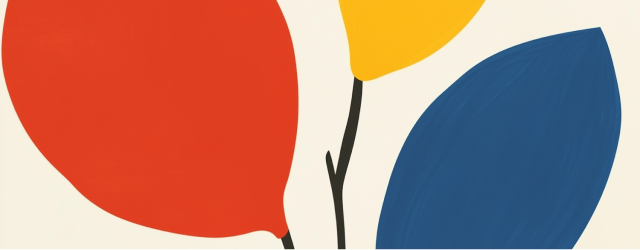
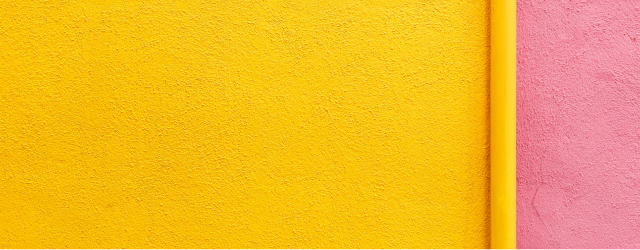
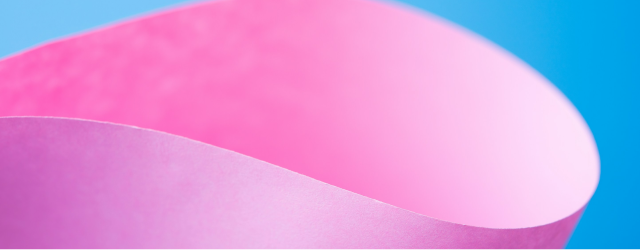