CMM Inspection
Gain a thorough understanding of CMM Inspection in manufacturing, with insights into their application, benefits, and strategic importance in the industry.
Introduction to the Article
In the ever-evolving landscape of modern manufacturing, precision and efficiency are paramount. As industries strive to meet rigorous quality standards and optimize production processes, Coordinate Measuring Machine (CMM) inspection emerges as a pivotal technology. CMM inspection is not just a tool; it is the backbone of quality assurance in manufacturing, ensuring that every component meets exact specifications. In this article, we delve into the world of CMM inspection, exploring its critical role in maintaining precision and operational efficiency. Whether you're a seasoned professional or new to the field, this comprehensive exploration will arm you with the insights needed to maximize the benefits of CMM inspection in your manufacturing processes.
Navigate Manufacturing Project Success with Meegle
Understanding cmm inspection
What is CMM Inspection?
Coordinate Measuring Machine (CMM) inspection is a sophisticated process that involves the precise measurement of the physical geometrical characteristics of an object. It employs a combination of highly sensitive probes and advanced software to capture details about an object's dimensions and shape. This technology is essential in verifying that manufactured parts conform to their design specifications, which is crucial in industries where even the slightest deviation can result in product failure.
The core components of a CMM include a probing system, a control unit, and software that processes measurement data. The probing system, which can be tactile or non-contact, interacts with the object being measured to collect data points. These data points are then translated into a digital map of the object's surface by the control unit. The software analyzes this data to provide a precise measurement, which can be compared against design specifications. This level of accuracy makes CMMs indispensable in sectors such as aerospace, automotive, and medical device manufacturing, where the highest degree of precision is required.
Importance in Manufacturing
In the world of manufacturing, maintaining high standards of product quality and consistency is non-negotiable. CMM inspection is central to achieving these goals. It ensures that products meet specified tolerances, which is essential for customer satisfaction and regulatory compliance. By detecting deviations early in the production process, CMM inspection reduces the likelihood of costly rework and scrap, ultimately enhancing operational efficiency.
The ability of CMMs to provide accurate, repeatable measurements makes them invaluable for quality control. They allow manufacturers to identify defects and make necessary adjustments before products reach the market. This not only safeguards the brand's reputation but also ensures that the final product performs as intended. In industries where precision is paramount, such as aerospace or medical devices, CMM inspection is the difference between success and failure. Its role in maintaining product integrity cannot be overstated, making it a cornerstone of modern manufacturing practices.
Historical development of cmm inspection
Origins of CMM Technology
The origins of CMM technology can be traced back to the early days of precision engineering, where the need for accurate measurement tools was first realized. Initially, measurements were taken manually using simple tools like calipers and micrometers. However, as industrial processes became more complex and the demand for higher precision grew, the limitations of manual measurement methods became apparent. This led to the development of automated measurement systems in the mid-20th century.
The first CMMs were introduced in the 1960s. These early machines were a significant leap forward, allowing for more precise and consistent measurements than previously possible. They used a combination of mechanical and electronic components to measure an object's dimensions accurately. Over time, these machines evolved to include more sophisticated technologies, such as computer-aided design (CAD) integration and advanced probing systems. This evolution laid the groundwork for modern CMMs, which are now integral to quality assurance in manufacturing.
Technological Evolution
The technological evolution of CMM inspection has been marked by several key milestones. One of the most significant advancements was the integration of CMMs with CAD systems. This allowed for more seamless data transfer and analysis, enhancing the speed and accuracy of measurements. The transition from manual to automated processes further improved efficiency, allowing CMMs to operate with minimal human intervention.
Software improvements have also played a crucial role in the evolution of CMM technology. Modern CMM software can handle complex geometries and large datasets, providing detailed analysis and reporting capabilities. Additionally, advancements in probing technology have expanded the capabilities of CMMs. Today, they can use a variety of probes, including tactile, laser, and optical, to measure different types of surfaces and materials. These innovations have made CMM inspection more versatile, accurate, and efficient, ensuring its continued relevance in the manufacturing industry.
Click here to read our expertly curated top picks!
Core principles and techniques
Fundamental Concepts in CMM Inspection
To effectively utilize CMM inspection, one must understand its fundamental concepts. At the heart of this technology is the probing system, which interacts with the object being measured. Probing can be contact-based, involving physical touch, or non-contact, using lasers or optical sensors. The choice of probing system depends on the material and geometry of the part being measured.
Coordinate systems are another essential aspect of CMM inspection. They provide a reference framework for measurement, ensuring consistency and accuracy. An object is mapped in a 3D space, and its dimensions are measured relative to this coordinate system. Error compensation is also crucial, as it accounts for any deviations that may occur due to environmental factors or machine inaccuracies. By applying these principles, CMM inspection achieves the high level of precision necessary for quality assurance in manufacturing.
Techniques for Implementation
Various techniques are employed in CMM inspection to cater to different measurement needs. Contact probing, one of the most common methods, involves a probe physically touching the object's surface to collect data points. This technique is highly accurate and suitable for measuring simple geometries and hard materials.
Laser scanning is another technique that uses laser beams to capture the object's surface data. It is ideal for measuring complex shapes and soft materials, as it does not require physical contact. Optical measurement, which uses cameras and sensors to capture images of the object, is also gaining popularity. Each of these techniques has its advantages and is chosen based on the specific requirements of the measurement task. Understanding the strengths and limitations of each technique is essential for effective CMM inspection.
Benefits and challenges
Advantages of Implementing CMM Inspection
The implementation of CMM inspection in manufacturing brings numerous advantages. One of the most significant benefits is improved quality control. By providing precise and repeatable measurements, CMMs ensure that products meet the required specifications, reducing the risk of defects and enhancing customer satisfaction. This, in turn, leads to cost savings by minimizing the need for rework and scrap.
CMM inspection also improves production efficiency. By automating the measurement process, CMMs reduce the time and labor required for quality assurance. This allows manufacturers to increase throughput and meet tight production deadlines. Additionally, the data collected by CMMs can be used for process optimization, identifying areas for improvement and enhancing overall operational efficiency. The economic impact of these advantages is significant, as they contribute to a more streamlined and cost-effective manufacturing process.
Addressing Challenges and Limitations
Despite its many benefits, implementing CMM inspection can present challenges. One of the most common hurdles is the high initial cost of purchasing and setting up CMM equipment. This can be a significant investment, particularly for small and medium-sized enterprises. However, the long-term benefits of reduced waste and improved quality often justify the initial expense.
Another challenge is the need for specialized training. Operating CMMs requires a certain level of expertise, and companies must invest in training programs to ensure their staff can use the equipment effectively. Additionally, CMMs are not suitable for all measurement tasks. For example, they may struggle with highly reflective surfaces or very soft materials. Overcoming these challenges requires careful planning and consideration of the specific requirements of the manufacturing process. By addressing these limitations, manufacturers can fully leverage the benefits of CMM inspection.
Click here to read our expertly curated top picks!
Case studies and real-world applications
Successful industry implementations
Successful industry implementations
In the aerospace industry, where precision and safety are paramount, CMM inspection has become an integral part of quality assurance. Companies like Boeing and Airbus have incorporated CMMs into their manufacturing processes to ensure that aircraft components meet stringent tolerances. By doing so, they have reduced the risk of defects and improved the overall reliability of their products. This has not only enhanced their reputation for quality but also led to significant cost savings by minimizing rework and scrap.
Similarly, in the automotive industry, leading manufacturers such as Ford and General Motors have embraced CMM technology to maintain high standards of quality and consistency. By using CMMs to measure critical components such as engine parts and chassis, they can guarantee that their vehicles meet safety regulations and customer expectations. The implementation of CMM inspection has allowed these companies to optimize production processes, reduce lead times, and increase overall efficiency.
Analyzing impact
Analyzing impact
The impact of CMM inspection on product quality and operational efficiency is evident in the success stories of companies that have integrated this technology into their operations. For instance, a leading medical device manufacturer reported a 30% reduction in defects after implementing CMM inspection. This not only improved patient safety but also led to a 20% increase in production efficiency by streamlining quality control processes.
In the electronics industry, a major smartphone manufacturer utilized CMM technology to enhance the precision of component assembly. This resulted in a 15% decrease in product returns due to quality issues, ultimately boosting customer satisfaction and brand loyalty. These examples highlight the tangible benefits of CMM inspection in improving product quality, enhancing efficiency, and driving business success.
Technological integration and innovations
Current Technologies Enhancing CMM Inspection
The integration of current technologies such as the Internet of Things (IoT) and Artificial Intelligence (AI) is revolutionizing CMM inspection. IoT-enabled CMMs can communicate with other machines and systems, facilitating real-time data exchange and analysis. This connectivity allows for more efficient monitoring and control of the measurement process, reducing downtime and improving overall productivity.
AI is also playing a significant role in enhancing CMM inspection. By leveraging machine learning algorithms, CMMs can analyze large datasets to identify patterns and trends. This enables predictive maintenance, where potential issues are detected and addressed before they lead to equipment failure. AI also enhances the accuracy of measurements by compensating for environmental factors and machine errors. The integration of these technologies is transforming CMM inspection into a more intelligent and efficient process.
Predicting Future Trends
Looking to the future, several trends are likely to shape the evolution of CMM inspection. One such trend is the increasing automation of measurement processes. As technology advances, CMMs will become more autonomous, requiring minimal human intervention. This will further enhance efficiency and reduce the likelihood of errors.
Another emerging trend is the use of digital twin technology. By creating a virtual replica of the physical object, manufacturers can simulate and analyze measurements before actual production. This allows for more accurate planning and design, ultimately improving the quality of the final product. Additionally, advancements in machine learning and AI will continue to enhance the capabilities of CMMs, making them more adaptable and versatile. These trends hold the potential to revolutionize CMM inspection and reshape the manufacturing landscape.
Click here to read our expertly curated top picks!
Tips for effective cmm inspection
Do's | Don'ts |
---|---|
Regularly calibrate your CMM equipment for precise measurements. | Avoid skipping training sessions for CMM operators. |
Integrate CMM with CAD systems for streamlined processes. | Don't ignore software updates that enhance functionality. |
Document inspection results meticulously for future reference. | Avoid relying solely on manual measurements for complex geometries. |
Click here to read our expertly curated top picks!
Conclusion
Recap of Key Points
Throughout this article, we have explored the critical role of CMM inspection in modern manufacturing. From its origins in precision engineering to its current applications in various industries, CMM technology has revolutionized quality control and efficiency. By providing precise and repeatable measurements, CMMs ensure that products meet stringent specifications, enhancing customer satisfaction and reducing costs.
Encouraging Adaptation and Continuous Learning
As technology continues to evolve, it is essential for professionals in the manufacturing sector to stay informed about the latest developments in CMM inspection. By embracing new technologies and continuously improving their skills, they can ensure that their manufacturing processes remain efficient and competitive. This commitment to adaptation and learning will enable manufacturers to harness the full potential of CMM inspection for improved outcomes.
Navigate Manufacturing Project Success with Meegle
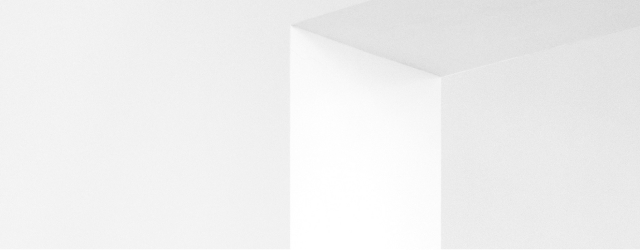
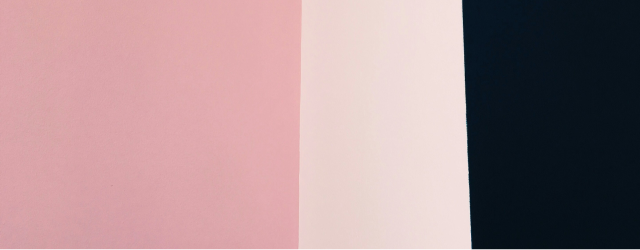
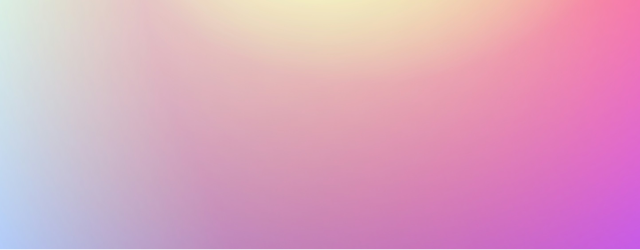
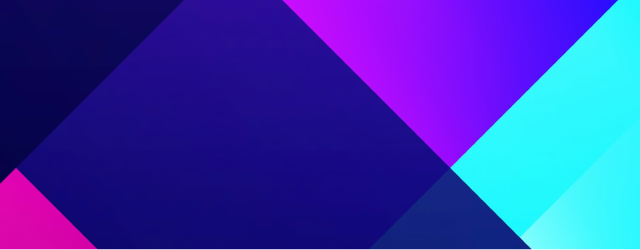
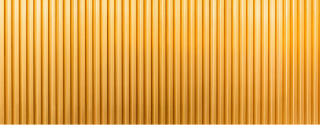
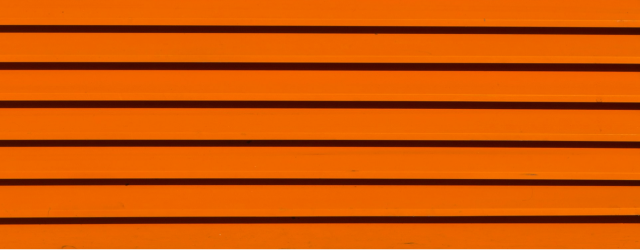
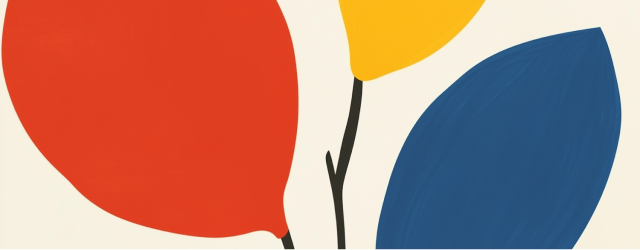
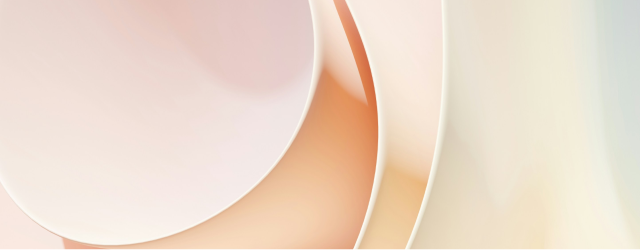