Manufacturing Cost Estimation
Gain a thorough understanding of Manufacturing Cost Estimation in manufacturing, with insights into their application, benefits, and strategic importance in the industry.
Overview of Manufacturing Cost Estimation
In the competitive landscape of manufacturing, cost estimation is akin to a compass guiding companies through the complexities of production economics. It involves determining the financial expenditure necessary to produce goods, thus playing a crucial role in budgeting, pricing strategies, and financial forecasting. Manufacturing cost estimation is not just a tool but a strategic process that empowers organizations to make informed decisions, forecast financial outcomes, and align their pricing strategies with market demands. By understanding the intricacies of cost estimation, manufacturers can safeguard their profitability while ensuring competitive pricing in the marketplace.
The process of cost estimation involves several critical components. These include direct costs such as materials and labor, and indirect costs like overheads. Material costs encompass the raw materials and parts used in production, while labor costs account for the wages of employees directly involved in manufacturing. Overheads, on the other hand, include expenses that are not directly tied to production but are necessary for operations, such as utilities and rent. By integrating these components, manufacturers can develop a comprehensive cost structure that accurately reflects the true cost of production.
Role in Manufacturing Efficiency
Manufacturing cost estimation is not merely a financial exercise; it profoundly impacts operational efficiency and product quality. Accurate cost estimation enables manufacturers to optimize resource allocation, thereby minimizing waste and reducing unnecessary expenditure. For instance, by precisely estimating the required materials and labor, companies can prevent overproduction or underutilization of resources. This operational efficiency is crucial for maintaining a lean manufacturing system where the aim is to maximize output with minimal waste.
Furthermore, precise cost estimation is directly linked to product quality. When manufacturers have a clear understanding of costs, they can invest appropriately in high-quality materials and skilled labor without compromising on profitability. This investment in quality is essential for maintaining consistency and meeting customer expectations. For example, a company producing high-end electronics must ensure that each component meets specific standards, which is only feasible with accurate cost assessments that balance quality with cost-effectiveness. In this way, cost estimation becomes a cornerstone for producing superior products that resonate with consumer expectations.
Navigate Manufacturing Project Success with Meegle
Historical development of manufacturing cost estimation
Origins of Manufacturing Cost Estimation
The roots of manufacturing cost estimation can be traced back to rudimentary methods used in traditional manufacturing setups. Early practices were largely based on rule-of-thumb estimates and were heavily reliant on the experience of craftsmen and tradespeople. These methods lacked precision and were often subject to significant inaccuracies. However, they laid the foundation for more systematic approaches that would emerge with industrial advancements.
The Industrial Revolution marked a turning point in manufacturing cost estimation. As factories proliferated and production processes became more complex, there was a growing need for systematic methodologies to assess costs accurately. The introduction of machinery and assembly line production necessitated a shift from intuitive estimates to more structured cost analysis. This era saw the genesis of cost accounting as manufacturers sought to calculate costs with greater accuracy to enhance productivity and profitability. The industrial era's demand for large-scale production efficiency spurred the development of standardized cost estimation techniques that are still in use today.
Evolution Over Time
The evolution of manufacturing cost estimation has been significantly shaped by technological advancements. The advent of computerization in the latter half of the 20th century revolutionized traditional estimation methods. Software tools and databases allowed for more accurate and efficient data processing, enabling manufacturers to calculate costs with unprecedented precision. The introduction of computerized systems facilitated detailed tracking of costs and resource allocation, reducing errors inherent in manual calculations.
Globalization further influenced cost estimation practices, introducing new complexities and methodologies. As companies expanded operations across borders, they encountered diverse cost structures affected by varying labor, material, and logistical expenses. This necessitated the adoption of more sophisticated estimation techniques capable of accommodating these complexities. For instance, multinational corporations began using activity-based costing, which assigns costs to specific activities related to production, offering a more granular view of cost drivers. The integration of global supply chains also highlighted the need for dynamic cost estimation models that could adapt to fluctuating exchange rates and international market conditions. In essence, the evolution of manufacturing cost estimation reflects a continuous adaptation to technological and market forces, ensuring its relevance in the modern industrial landscape.
Core principles and techniques
Fundamental Concepts
Understanding the principles of cost accounting is imperative for effective manufacturing cost estimation. At its core, cost accounting is a framework that helps organizations manage and control their costs. It involves identifying, measuring, recording, and analyzing costs associated with production. This discipline provides the foundational concepts that underpin cost estimation, such as cost classification, cost behavior, and cost allocation.
A critical aspect of cost estimation is cost behavior analysis, which involves understanding how costs change in response to varying levels of production. Costs can be categorized as fixed, variable, or semi-variable. Fixed costs remain unchanged irrespective of production volume, like rent and salaries. Variable costs fluctuate with production levels, such as raw materials and direct labor. Semi-variable costs contain elements of both fixed and variable costs, such as utility bills that have a base charge plus a variable component. Mastery of these concepts allows manufacturers to predict how changes in production levels impact overall costs, aiding in more accurate and efficient cost estimation.
Implementation Techniques
Several techniques are employed in manufacturing cost estimation, each with its unique applications and benefits. Among these, the bottom-up and top-down approaches are two primary methodologies. The bottom-up approach involves detailed estimation of individual cost components, which are then aggregated to form the total cost. This method is particularly useful for complex projects where precise cost tracking is essential. Conversely, the top-down approach starts with a broad estimate of the total cost and breaks it down into constituent parts. This is often employed in situations where rapid estimates are needed, such as during the early stages of project planning.
Standard costing and activity-based costing are prominent techniques in modern manufacturing. Standard costing involves setting predetermined costs for products or services, which serve as benchmarks for measuring performance. Variances between actual and standard costs are analyzed to identify efficiency levels and areas for improvement. Activity-based costing, on the other hand, assigns costs to specific activities involved in production. This technique provides a more accurate picture of cost drivers and can lead to significant insights into cost-saving opportunities. Both methods are invaluable for manufacturers seeking to optimize their cost structures and improve profitability.
Click here to read our expertly curated top picks!
Benefits and challenges
Advantages in Production
Effective manufacturing cost estimation offers several advantages, particularly in cost control and profitability. By accurately forecasting costs, manufacturers can implement measures to control expenditures, ensuring that production remains within budget. This control over costs directly contributes to enhanced profitability, as it enables companies to maximize their margins by reducing unnecessary expenses. For example, a manufacturer that accurately estimates costs can avoid unexpected financial overruns, thereby safeguarding its profit margins.
Moreover, precise cost estimation plays a critical role in strategic decision-making. It provides valuable insights that guide investment decisions, product development, and market entry strategies. Manufacturers can use cost data to evaluate the feasibility of new projects, compare alternative production methods, and assess potential returns on investment. This data-driven approach ensures that decisions are based on a solid understanding of financial implications, reducing risks and enhancing strategic planning efforts.
Potential Limitations
Despite its benefits, manufacturing cost estimation is not without challenges. One significant limitation is the accuracy of estimates, which can be affected by fluctuating market conditions or human errors. For instance, sudden changes in material prices or labor costs can lead to discrepancies in cost estimates, impacting budgetary planning and profitability. To mitigate these risks, manufacturers can employ sensitivity analysis to examine how changes in cost drivers affect overall estimates, providing a buffer against market volatility.
Another challenge is the dependency on accurate and reliable data. Effective cost estimation requires comprehensive and up-to-date data on materials, labor, and overheads. However, obtaining such data can be challenging, particularly in industries with complex supply chains or rapidly changing market conditions. Advanced data analytics and robust data management systems can help overcome these limitations by ensuring data accuracy and providing real-time insights into cost structures. By leveraging technology, manufacturers can enhance the reliability of their cost estimates and make more informed decisions.
Case studies and real-world applications
Industry examples
Industry examples
Automotive Sector
In the automotive industry, cost estimation is crucial for managing complex production processes and ensuring competitive pricing. Automotive manufacturers often deal with large volumes of components sourced from various suppliers, each with its cost structure. For instance, a leading automotive company might use cost estimation to evaluate the financial feasibility of introducing a new vehicle model. By analyzing costs associated with parts, labor, and production overheads, the company can set a competitive price that maximizes profitability while meeting consumer expectations. Cost estimation also helps automotive firms manage supply chain disruptions, ensuring that production remains cost-effective despite fluctuations in raw material prices.
Electronics Manufacturing
Electronics companies face unique challenges in balancing innovation with cost efficiency. Cost estimation plays a vital role in this industry by providing insights into the financial implications of using advanced technology and premium components. For instance, a smartphone manufacturer might use activity-based costing to identify cost drivers associated with different production stages. This approach allows the company to optimize resource allocation and reduce costs without compromising on product innovation. By accurately estimating costs, electronics manufacturers can maintain a competitive edge in a rapidly evolving market while delivering cutting-edge products at attractive prices.
Food and Beverage Industry
In the food and beverage industry, cost estimation is essential for managing ingredient costs and ensuring production efficiency. Companies in this sector often deal with volatile raw material prices, making accurate cost estimation critical for profitability. For example, a beverage company may use standard costing to establish benchmarks for ingredient costs, labor, and overheads. Variances between actual and standard costs are analyzed to identify areas for cost reduction and efficiency improvements. Through precise cost estimation, food and beverage manufacturers can maintain consistent product quality while optimizing their cost structures, ensuring that they remain competitive in a dynamic market environment.
Impact analysis
Impact analysis
In examining the tangible improvements brought about by effective cost estimation, several case studies highlight its impact on profitability and market competitiveness. For instance, a manufacturing firm that implemented activity-based costing saw a significant reduction in overhead expenses and improved resource allocation. By identifying high-cost activities, the company streamlined its processes, leading to a 15% increase in profit margins within a year. Similarly, another manufacturer that adopted advanced cost estimation software experienced enhanced accuracy in its financial forecasts, enabling more strategic investment decisions and a stronger competitive position in the market.
The lessons learned from these applications underscore the importance of refining cost estimation strategies. Manufacturers that integrate advanced estimation techniques with robust data analytics can achieve substantial cost savings and operational efficiencies. By continuously improving their cost estimation processes, companies can enhance their financial performance, adapt to market changes, and sustain long-term growth.
Click here to read our expertly curated top picks!
Technological integration and innovations
Current Technologies
The integration of technology in manufacturing cost estimation has revolutionized traditional practices, making them more efficient and accurate. Enterprise Resource Planning (ERP) systems, for example, play a crucial role in facilitating cost estimation by providing a centralized platform for data management and analysis. These systems enable real-time tracking of costs, resources, and production processes, allowing manufacturers to make informed decisions based on up-to-date information. By leveraging ERP systems, companies can streamline their estimation processes, reduce errors, and enhance overall operational efficiency.
Artificial Intelligence (AI) and machine learning are also transforming cost estimation by enhancing accuracy and predictive capabilities. These technologies can analyze vast amounts of data to identify patterns and trends that inform cost predictions. For instance, machine learning algorithms can forecast changes in material prices or labor costs, enabling companies to adjust their estimates proactively. By incorporating AI and machine learning into their cost estimation practices, manufacturers can achieve greater precision and adaptability, ultimately improving their competitive edge in the market.
Future Trends
Looking ahead, digital twins and the Internet of Things (IoT) are expected to revolutionize manufacturing cost estimation processes. Digital twins, which create virtual replicas of physical systems, allow manufacturers to simulate production processes and assess costs in real-time. This capability enables companies to optimize resource allocation, identify potential inefficiencies, and improve cost estimation accuracy. Similarly, IoT technology facilitates real-time data collection and analysis, providing insights into cost drivers and enabling dynamic cost estimation.
Blockchain technology also holds promise for enhancing transparency and accuracy in cost estimation. By creating an immutable record of transactions and costs, blockchain can ensure the integrity of data used in cost estimation. This transparency is particularly valuable in industries with complex supply chains, where accurate data is essential for reliable cost estimation. By adopting these emerging technologies, manufacturers can not only improve their cost estimation practices but also gain a competitive advantage in an increasingly digital and interconnected world.
Click here to read our expertly curated top picks!
Tips for do's and dont's in manufacturing cost estimation
Do's | Don'ts |
---|---|
Utilize reliable data sources | Ignore external market factors |
Regularly update cost models | Rely solely on historical data |
Engage cross-functional teams | Exclude operational insights |
Implement robust software tools | Overcomplicate estimation processes |
Validate with industry benchmarks | Neglect regular performance reviews |
Click here to read our expertly curated top picks!
Conclusion
Summary of Key Points
Manufacturing cost estimation is a strategic process that plays a vital role in budgeting, pricing, and financial forecasting. By understanding the components of cost estimation and employing advanced methodologies, manufacturers can optimize their operations, enhance profitability, and maintain competitive pricing. The integration of technology and continuous improvement are essential for refining cost estimation practices and achieving long-term success.
Encouraging Ongoing Adaptation
As the manufacturing landscape evolves, professionals must remain abreast of technological advancements and industry trends. By embracing innovations such as AI, IoT, and blockchain, manufacturers can enhance the accuracy and efficiency of their cost estimation processes. Ongoing adaptation and refinement of cost estimation practices are crucial for optimizing outcomes and sustaining competitive advantage in a dynamic and rapidly changing market.
Navigate Manufacturing Project Success with Meegle
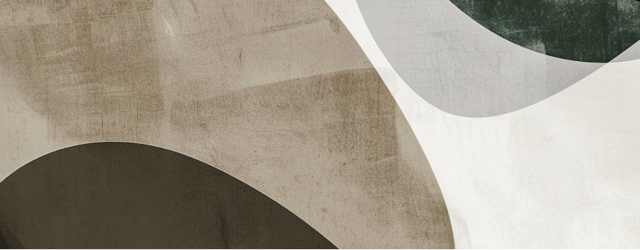
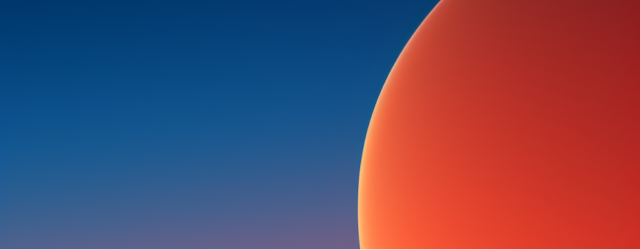
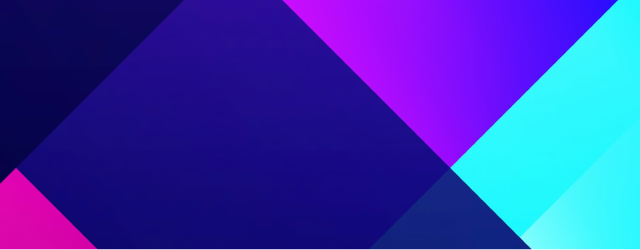
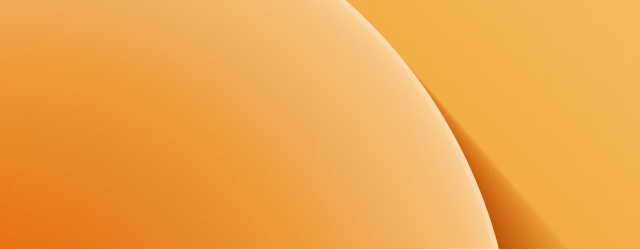
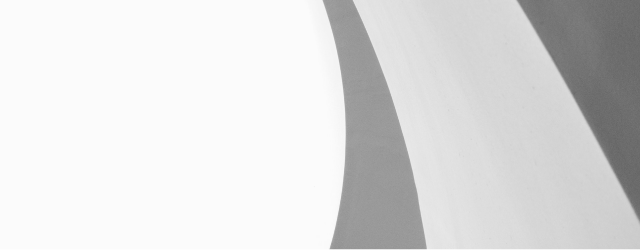
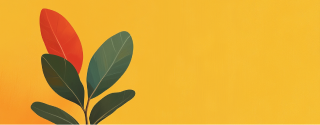
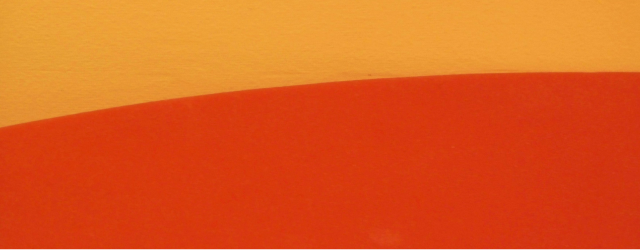
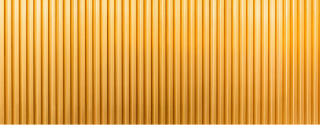