IoT In Manufacturing
Gain a thorough understanding of IoT in Manufacturing in manufacturing, with insights into their application, benefits, and strategic importance in the industry.
Overview of IoT in Manufacturing
The Internet of Things (IoT) refers to a network of physical devices, vehicles, appliances, and other items embedded with sensors, software, and network connectivity, allowing them to collect and exchange data. In the context of manufacturing, IoT facilitates real-time data exchange, predictive maintenance, and advanced analytics. Through IoT, traditional manufacturing processes are transformed into smart manufacturing systems where each component communicates seamlessly, contributing to a more cohesive and efficient production environment.
One of the primary advantages of IoT in manufacturing is its ability to reduce costs. By providing real-time insights into equipment performance and production processes, IoT enables manufacturers to optimize operations and minimize resource wastage. According to a report by McKinsey, IoT could potentially create up to $3.7 trillion in economic value per year in manufacturing alone by 2025. Moreover, IoT contributes to increased productivity by automating manual tasks and enabling machines to perform at optimal efficiency levels.
Quality improvement is another critical aspect of IoT in manufacturing. By leveraging IoT technologies, manufacturers can monitor product quality in real time, identify defects early in the production cycle, and implement corrective measures promptly. This not only enhances product quality but also reduces the time and cost associated with quality control processes. A study conducted by Deloitte highlights that IoT-enabled quality control can lead to a 10% improvement in manufacturing efficiency.
In summary, IoT is revolutionizing the manufacturing landscape by facilitating real-time data exchange, enabling predictive maintenance, and transforming traditional processes into smart, interconnected systems. Its potential to reduce costs, increase productivity, and improve product quality makes it an indispensable tool for manufacturers aiming to stay competitive in the digital age.
Role in Manufacturing Efficiency
IoT plays a pivotal role in streamlining manufacturing operations by enabling automation and connectivity across various stages of production. By integrating IoT devices such as sensors, connected machinery, and smart meters, manufacturers can gather and analyze data in real time, leading to significant efficiency enhancements.
One of the key benefits of IoT in manufacturing is the reduction of downtime. Through predictive maintenance powered by IoT, manufacturers can monitor the condition of machinery and equipment in real time, anticipating potential failures before they occur. This proactive approach minimizes unplanned downtime, ensuring that production lines run smoothly and efficiently. For instance, a leading automotive manufacturer implemented IoT-based predictive maintenance and reduced equipment downtime by 20%, resulting in substantial cost savings.
IoT also optimizes supply chain management by providing real-time visibility into inventory levels, production status, and demand forecasts. With IoT-enabled sensors and connected devices, manufacturers can track the movement of raw materials and finished goods throughout the supply chain, ensuring timely deliveries and reducing lead times. This enhanced visibility allows manufacturers to respond quickly to changing market demands and optimize their production schedules accordingly.
Furthermore, IoT facilitates the integration of various systems within a manufacturing plant, enabling seamless communication between machines, processes, and personnel. This connectivity allows for the automation of repetitive tasks, improving overall operational efficiency. For example, a consumer electronics company integrated IoT into its manufacturing processes, resulting in a 15% reduction in production cycle time and a 12% increase in overall efficiency.
In conclusion, IoT applications significantly enhance manufacturing efficiency by minimizing downtime, optimizing supply chain management, and enabling automation across various stages of production. By leveraging IoT technologies, manufacturers can achieve higher levels of productivity, reduce operational costs, and stay competitive in today's dynamic market landscape.
Navigate Manufacturing Project Success with Meegle
Historical development of iot in manufacturing
Origins of IoT in Manufacturing
The origins of IoT in manufacturing can be traced back to the early concepts of machine-to-machine (M2M) communication and industrial automation. The foundation for IoT was laid in the late 20th century when manufacturers began exploring ways to improve operational efficiency and reduce costs through automation. The introduction of sensors and programmable logic controllers (PLCs) marked the initial steps towards IoT adoption in manufacturing.
One of the significant milestones in the development of IoT in manufacturing was the advent of radio-frequency identification (RFID) technology in the 1990s. RFID enabled manufacturers to track and manage inventory more efficiently, laying the groundwork for the integration of IoT into supply chain management. This technology provided a glimpse into the potential of IoT to enhance visibility and traceability in manufacturing operations.
The evolution of IoT in manufacturing gained momentum with the advancement of wireless communication technologies in the early 2000s. The proliferation of wireless networks and the Internet allowed manufacturers to connect devices and systems within their facilities, enabling real-time data exchange and remote monitoring. This marked a shift towards more interconnected and data-driven manufacturing processes.
Significant developments in IoT for manufacturing occurred in the mid-2010s with the emergence of cloud computing and big data analytics. These technologies enabled manufacturers to process and analyze vast amounts of data generated by IoT devices, unlocking new insights and opportunities for optimization. The integration of cloud-based platforms further facilitated the scalability and flexibility of IoT solutions in the manufacturing sector.
In summary, the historical development of IoT in manufacturing can be attributed to the convergence of M2M communication, industrial automation, RFID technology, wireless networks, cloud computing, and big data analytics. These advancements have paved the way for IoT to become a transformative force in the manufacturing industry, driving efficiency, innovation, and competitiveness.
Evolution Over Time
The evolution of IoT applications within the manufacturing industry has been marked by technological and methodological advancements that have revolutionized traditional manufacturing processes. Over time, manufacturing has progressed from manual, labor-intensive methods to more intelligent, data-driven approaches, facilitated by the integration of IoT technologies.
Initially, the focus of IoT in manufacturing was on enhancing operational efficiency through automation and real-time data exchange. As IoT technologies matured, manufacturers began leveraging advanced analytics and machine learning algorithms to derive actionable insights from the vast amounts of data generated by connected devices. This shift enabled manufacturers to optimize production processes, improve product quality, and enhance decision-making.
The adoption of IoT technologies has also led to the emergence of smart manufacturing, where every aspect of the production process is interconnected and optimized. Smart factories leverage IoT to monitor and control machinery, track inventory levels, and manage production schedules in real time. This level of connectivity and automation has transformed manufacturing into a more agile and responsive industry.
Various industries have successfully adopted IoT technologies and adapted them to suit their specific operational needs. For example, the automotive industry has integrated IoT to enhance vehicle production processes, improve supply chain efficiency, and enable predictive maintenance. Similarly, the electronics industry has leveraged IoT to monitor production lines, optimize energy consumption, and ensure product quality.
The evolution of IoT in manufacturing has also been driven by the increasing demand for sustainability and environmental responsibility. IoT technologies enable manufacturers to monitor energy usage, reduce waste, and implement environmentally friendly practices. This emphasis on sustainability has further accelerated the adoption of IoT in manufacturing, aligning with the industry's commitment to reducing its environmental footprint.
In conclusion, the evolution of IoT in manufacturing has been characterized by technological advancements, the rise of smart manufacturing, and the pursuit of sustainability. As IoT continues to evolve, manufacturers are poised to unlock new opportunities for efficiency, innovation, and competitiveness in the ever-changing industrial landscape.
Click here to read our expertly curated top picks!
Core principles and techniques
Fundamental Concepts
The core principles of IoT in manufacturing revolve around connectivity, data collection, real-time analytics, and integration with other technological advancements. These fundamental concepts are essential for understanding how IoT transforms manufacturing processes and drives efficiency and innovation.
Connectivity is the backbone of IoT in manufacturing, enabling seamless communication between devices, machines, and systems. IoT devices, equipped with sensors and communication interfaces, collect data from various sources and transmit it to a centralized platform for analysis. This connectivity allows manufacturers to monitor and control every aspect of their operations in real time, ensuring optimal performance and efficiency.
Data collection is a critical component of IoT in manufacturing. IoT devices continuously gather data on equipment performance, production status, environmental conditions, and more. This data is then processed and analyzed to derive actionable insights that drive decision-making and process optimization. The ability to collect and analyze large volumes of data in real time empowers manufacturers to make informed decisions and respond quickly to changing conditions.
Real-time analytics is another fundamental concept of IoT in manufacturing. By leveraging advanced analytics and machine learning algorithms, manufacturers can gain valuable insights into their operations, identify trends and patterns, and predict future outcomes. Real-time analytics enables manufacturers to optimize production processes, improve product quality, and enhance overall efficiency.
Integration with other technological advancements, such as artificial intelligence (AI) and machine learning (ML), is a key principle of IoT in manufacturing. IoT technologies can be integrated with AI and ML algorithms to enable predictive maintenance, automate quality control processes, and enhance decision-making. This integration allows manufacturers to harness the full potential of IoT and drive innovation in their operations.
In summary, the fundamental concepts of IoT in manufacturing encompass connectivity, data collection, real-time analytics, and integration with other technological advancements. These principles are essential for unlocking the potential of IoT and transforming manufacturing processes into more efficient, data-driven systems.
Implementation Techniques
The successful implementation of IoT solutions in manufacturing requires careful planning, strategic deployment, and robust data management practices. Various techniques and methods can be employed to ensure the seamless integration of IoT technologies into existing manufacturing environments.
One of the key techniques for implementing IoT in manufacturing is the deployment of sensors and connected devices. These devices are strategically placed throughout the manufacturing facility to collect data on equipment performance, production processes, and environmental conditions. It is essential to select the right type of sensors and devices that align with the specific needs and goals of the manufacturing operation.
Integrating IoT with existing systems is another crucial technique for successful implementation. Manufacturers need to ensure that IoT devices and platforms are compatible with their current infrastructure and can seamlessly communicate with other systems, such as enterprise resource planning (ERP) and manufacturing execution systems (MES). This integration enables the smooth flow of data across different systems, facilitating real-time monitoring and decision-making.
Data management and security are paramount in IoT implementation. Manufacturers must establish robust data management practices to ensure the integrity, accuracy, and accessibility of the data collected by IoT devices. Additionally, implementing strong security measures is essential to protect sensitive data from cyber threats and unauthorized access. Encryption, access control, and regular security audits are some of the best practices for ensuring data security in IoT environments.
Furthermore, manufacturers should adopt a phased approach to IoT implementation, starting with pilot projects to test and validate the technology before full-scale deployment. This approach allows manufacturers to identify potential challenges, refine their strategies, and ensure that IoT solutions align with their operational goals. Continuous monitoring and evaluation of IoT performance are also crucial to identify areas for improvement and optimize the implementation process.
In conclusion, the successful implementation of IoT in manufacturing involves deploying sensors and connected devices, integrating IoT with existing systems, and establishing robust data management and security practices. By adopting these techniques and best practices, manufacturers can unlock the full potential of IoT and drive efficiency, innovation, and competitiveness in their operations.
Benefits and challenges
Advantages in Production
Integrating IoT into manufacturing processes offers a myriad of advantages, transforming production operations and enhancing overall efficiency. IoT technologies enable manufacturers to achieve significant improvements in production efficiency, quality control, supply chain management, and customer satisfaction.
One of the primary advantages of IoT in production is the ability to optimize manufacturing processes and reduce operational costs. IoT devices provide real-time insights into equipment performance, enabling manufacturers to identify inefficiencies and implement corrective measures promptly. This optimization leads to reduced resource wastage, lower energy consumption, and improved production efficiency. According to a study by Accenture, IoT-driven efficiency improvements can result in a 10% reduction in production costs for manufacturers.
Quality control is another critical area where IoT makes a substantial impact. By leveraging real-time data and advanced analytics, manufacturers can monitor product quality throughout the production cycle, identify defects early, and implement corrective actions. This proactive approach enhances product quality, reduces rework and scrap rates, and ensures compliance with industry standards. A case study by GE Digital highlights that IoT-enabled quality control can lead to a 20% improvement in product quality for manufacturers.
IoT also enhances supply chain management by providing real-time visibility into inventory levels, production status, and demand forecasts. With IoT-enabled sensors and connected devices, manufacturers can track the movement of raw materials and finished goods throughout the supply chain, ensuring timely deliveries and reducing lead times. This enhanced visibility allows manufacturers to respond quickly to changing market demands and optimize their production schedules accordingly.
Moreover, IoT technologies contribute to improved customer satisfaction by enabling manufacturers to deliver high-quality products and meet delivery commitments consistently. By optimizing production processes and ensuring product quality, manufacturers can enhance their reputation, build customer trust, and foster long-term relationships.
In conclusion, integrating IoT into manufacturing processes offers substantial advantages, including improved production efficiency, enhanced quality control, optimized supply chain management, and increased customer satisfaction. These benefits position manufacturers to stay competitive in today's dynamic market landscape and drive long-term success.
Potential Limitations
While IoT offers numerous benefits, its implementation in manufacturing is not without challenges. Manufacturers must navigate potential limitations and address key issues to fully realize the potential of IoT in their operations. Some of the common challenges associated with IoT in manufacturing include cybersecurity risks, high initial costs, and complexities in system integration.
Cybersecurity risks are a significant concern for manufacturers implementing IoT solutions. With the proliferation of connected devices and the exchange of sensitive data, the potential for cyber threats and unauthorized access increases. Manufacturers must implement robust cybersecurity measures to protect their IoT ecosystems, including encryption, access control, and regular security audits. According to a report by Gartner, 20% of organizations reported IoT-related security incidents in 2020, highlighting the importance of prioritizing cybersecurity in IoT environments.
High initial costs are another challenge that manufacturers may encounter when implementing IoT solutions. The deployment of IoT devices, sensors, and platforms requires significant upfront investment, which can be a barrier for some manufacturers. However, it is essential to consider the long-term benefits and return on investment (ROI) that IoT can bring. Implementing IoT incrementally, starting with pilot projects, can help manufacturers manage costs and demonstrate the value of IoT before full-scale deployment.
System integration complexities can also pose challenges for manufacturers adopting IoT technologies. Integrating IoT devices and platforms with existing systems, such as ERP and MES, requires careful planning and coordination. Manufacturers must ensure compatibility and seamless communication between different systems to enable real-time data exchange and optimize operations. Collaborating with experienced IoT solution providers and leveraging open standards can help address integration challenges.
To overcome these challenges, manufacturers should adopt a strategic approach to IoT implementation, prioritizing cybersecurity measures, managing costs effectively, and ensuring seamless system integration. By addressing these limitations, manufacturers can unlock the full potential of IoT and drive efficiency, innovation, and competitiveness in their operations.
Click here to read our expertly curated top picks!
Case studies and real-world applications
Industry examples
Industry examples
Several industries have successfully implemented IoT in manufacturing, demonstrating the transformative power of this technology. These real-world examples highlight the strategies employed, technologies used, and outcomes achieved, offering valuable insights for manufacturers seeking to leverage IoT in their operations.
One notable example is the automotive industry, where IoT has been integrated to enhance vehicle production processes, improve supply chain efficiency, and enable predictive maintenance. A leading automotive manufacturer implemented IoT sensors and connected devices to monitor equipment performance and detect potential issues before they lead to downtime. This proactive approach resulted in a 25% reduction in equipment failure rates and a 15% increase in overall production efficiency.
The electronics industry has also embraced IoT to optimize manufacturing processes and ensure product quality. A consumer electronics company integrated IoT technologies into its production lines, enabling real-time monitoring of equipment performance and environmental conditions. This integration allowed the company to identify and address quality issues early, reducing defect rates by 30% and improving overall product quality.
In the consumer goods sector, IoT has been leveraged to enhance supply chain management and improve customer satisfaction. A global consumer goods manufacturer implemented IoT-enabled sensors and connected devices to track inventory levels and monitor product movement throughout the supply chain. This real-time visibility allowed the company to optimize inventory management, reduce lead times, and ensure timely deliveries, resulting in a 20% increase in customer satisfaction.
These industry examples demonstrate the diverse applications and benefits of IoT in manufacturing, from optimizing production processes to enhancing supply chain efficiency and improving product quality. By leveraging IoT technologies, manufacturers across various sectors can achieve significant efficiency improvements, reduce costs, and enhance their competitiveness in the market.
Impact analysis
Impact analysis
The tangible impacts of IoT on real-world manufacturing scenarios are profound, transforming business processes, improving decision-making, and contributing to achieving sustainability goals. IoT has brought about significant improvements in various aspects of manufacturing operations, leading to enhanced efficiency, innovation, and competitiveness.
One of the key impacts of IoT in manufacturing is the transformation of business processes. IoT technologies enable manufacturers to automate repetitive tasks, optimize production schedules, and streamline operations. This transformation leads to increased agility and responsiveness, allowing manufacturers to adapt quickly to changing market demands and customer preferences. A study by Capgemini highlights that IoT-enabled automation can result in a 20% increase in production efficiency and a 15% reduction in operational costs for manufacturers.
Improved decision-making is another significant impact of IoT in manufacturing. By providing real-time insights and advanced analytics, IoT empowers manufacturers to make informed decisions based on data-driven insights. This enhanced decision-making capability allows manufacturers to optimize production processes, improve product quality, and reduce resource wastage. A case study by Cisco demonstrates that IoT-driven decision-making can lead to a 30% improvement in overall manufacturing efficiency.
IoT also contributes to achieving sustainability goals in manufacturing by enabling manufacturers to monitor energy usage, reduce waste, and implement environmentally friendly practices. By optimizing production processes and reducing resource consumption, IoT helps manufacturers minimize their environmental footprint and align with sustainability initiatives. A report by the World Economic Forum highlights that IoT-enabled sustainability initiatives can result in a 15% reduction in energy consumption and a 10% decrease in carbon emissions for manufacturers.
In conclusion, IoT has brought about tangible impacts and improvements in real-world manufacturing scenarios, transforming business processes, improving decision-making, and contributing to achieving sustainability goals. These impacts position manufacturers to stay competitive in today's dynamic market landscape and drive long-term success.
Technological integration and innovations
Current Technologies
The integration of current technologies is integral to realizing the full potential of IoT in manufacturing. These technologies enhance the capabilities of IoT devices, enabling manufacturers to achieve higher levels of efficiency, innovation, and competitiveness. Several key technologies play a crucial role in IoT-enabled manufacturing environments, including cloud computing, edge computing, artificial intelligence (AI), and machine learning (ML).
Cloud computing is a fundamental technology that supports IoT in manufacturing by providing scalable and flexible infrastructure for data storage, processing, and analysis. By leveraging cloud-based platforms, manufacturers can collect, store, and analyze vast amounts of data generated by IoT devices, enabling real-time insights and decision-making. Cloud computing also facilitates seamless communication and collaboration across different manufacturing sites and departments.
Edge computing is another critical technology that enhances the capabilities of IoT in manufacturing. By processing data closer to the source, edge computing reduces latency and bandwidth usage, enabling real-time analytics and decision-making. This technology is particularly beneficial for time-sensitive applications, such as predictive maintenance and quality control, where immediate insights are essential for optimizing operations.
Artificial intelligence (AI) and machine learning (ML) are transformative technologies that empower manufacturers to derive actionable insights from IoT data. By leveraging AI and ML algorithms, manufacturers can predict equipment failures, optimize production schedules, and automate quality control processes. These technologies enable manufacturers to achieve higher levels of efficiency, reduce operational costs, and enhance product quality.
In addition to these technologies, several emerging innovations are shaping the future of IoT in manufacturing. 5G connectivity, for example, promises to revolutionize manufacturing by providing ultra-fast and reliable communication between IoT devices. Advanced robotics and automation technologies are also driving innovation, enabling manufacturers to automate complex tasks and achieve higher levels of precision and efficiency.
In conclusion, the integration of current technologies, including cloud computing, edge computing, AI, and ML, is essential for unlocking the full potential of IoT in manufacturing. These technologies enhance the capabilities of IoT devices and empower manufacturers to achieve higher levels of efficiency, innovation, and competitiveness.
Future Trends
The future of IoT in manufacturing promises to be exciting, with several emerging trends and technological developments poised to shape the industry's landscape. These future trends are expected to drive further advancements in efficiency, innovation, and competitiveness, positioning manufacturers for long-term success.
One of the most anticipated trends in IoT for manufacturing is the widespread adoption of 5G connectivity. With its ultra-fast and reliable communication capabilities, 5G is set to revolutionize manufacturing operations by enabling seamless communication between IoT devices and systems. This enhanced connectivity will facilitate real-time data exchange, remote monitoring, and automation, driving significant efficiency improvements and innovation.
Advanced robotics and automation technologies are also expected to play a pivotal role in the future of IoT in manufacturing. These technologies will enable manufacturers to automate complex tasks, achieve higher levels of precision and accuracy, and reduce labor costs. Collaborative robots, or cobots, are particularly promising, as they can work alongside human operators, enhancing productivity and flexibility in manufacturing environments.
Blockchain integration is another emerging trend that holds great potential for IoT in manufacturing. By providing a secure and transparent ledger for data exchange, blockchain technology can enhance supply chain traceability, improve data security, and facilitate seamless collaboration among stakeholders. This integration will enable manufacturers to build trust and transparency in their operations, enhancing customer satisfaction and compliance with regulatory requirements.
The convergence of IoT with other emerging technologies, such as augmented reality (AR) and virtual reality (VR), is also expected to drive innovation in manufacturing. AR and VR technologies can enhance training and maintenance processes, allowing operators to visualize complex data and perform tasks more efficiently. This convergence will empower manufacturers to optimize operations, reduce downtime, and enhance overall efficiency.
In conclusion, the future trends of IoT in manufacturing, including 5G connectivity, advanced robotics, blockchain integration, and the convergence with AR and VR technologies, promise to drive significant advancements in efficiency, innovation, and competitiveness. As these trends continue to evolve, manufacturers are poised to unlock new opportunities and achieve long-term success in the ever-changing industrial landscape.
Click here to read our expertly curated top picks!
Do's and don'ts of iot implementation in manufacturing
Do's | Don'ts |
---|---|
Conduct a thorough needs analysis | Don't overlook cybersecurity measures |
Invest in scalable IoT solutions | Avoid choosing technology based solely on cost |
Train staff on new technologies | Don't ignore the importance of data analytics |
Monitor and evaluate IoT performance | Don't assume immediate results |
Click here to read our expertly curated top picks!
Conclusion
Summary of Key Points
Throughout this article, we have explored the transformative potential of IoT in manufacturing, highlighting its role in enhancing efficiency and fostering innovation. We began by defining IoT within the manufacturing context and discussing its ability to facilitate real-time data exchange, predictive maintenance, and advanced analytics. We examined how IoT streamlines manufacturing operations, reduces downtime, optimizes supply chain management, and ensures product quality. The historical development and evolution of IoT in manufacturing were explored, shedding light on the technological advancements that have driven its adoption. We delved into the core principles and techniques of IoT, emphasizing connectivity, data collection, real-time analytics, and integration with other technologies. The benefits and challenges of IoT implementation were discussed, supported by industry examples and impact analysis. Finally, we provided a step-by-step guide for implementing IoT in manufacturing, along with a table of do's and don'ts to ensure successful implementation.
Encouraging Ongoing Adaptation
As the manufacturing landscape continues to evolve, it is crucial for professionals to stay informed about the latest IoT advancements and consider integrating IoT into their manufacturing strategies. The potential of IoT to drive efficiency, innovation, and competitiveness is immense, and manufacturers must continuously adapt to harness its full benefits. By embracing IoT technologies and staying abreast of emerging trends such as 5G connectivity, advanced robotics, and blockchain integration, manufacturers can position themselves for long-term success. Continuous adaptation and innovation are key to remaining competitive in the ever-changing industrial landscape. Let us embrace the transformative power of IoT and unlock new possibilities for the future of manufacturing.
Navigate Manufacturing Project Success with Meegle
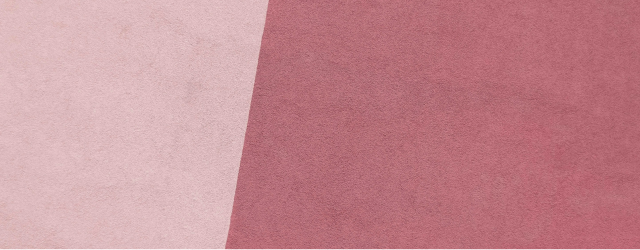
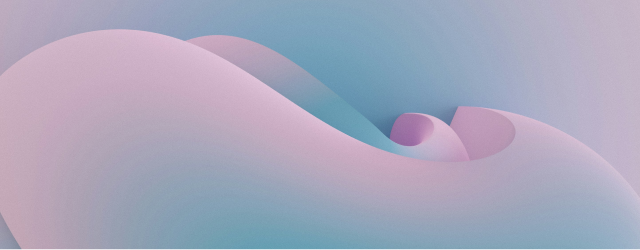
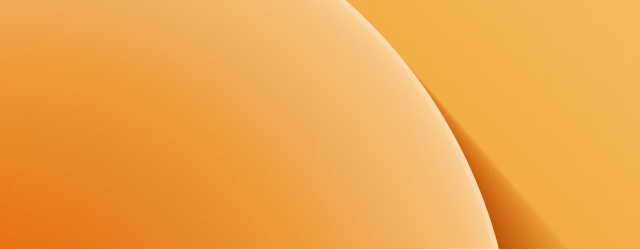
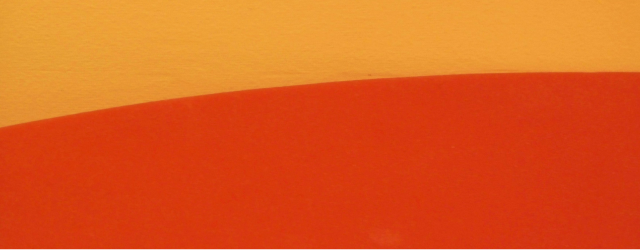
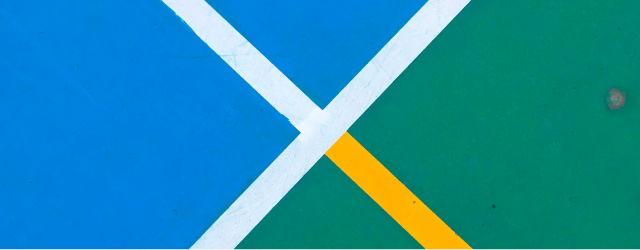
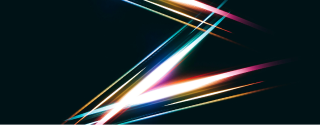
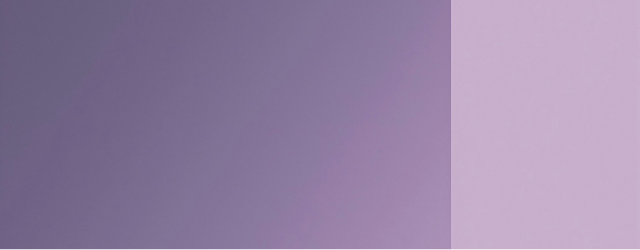
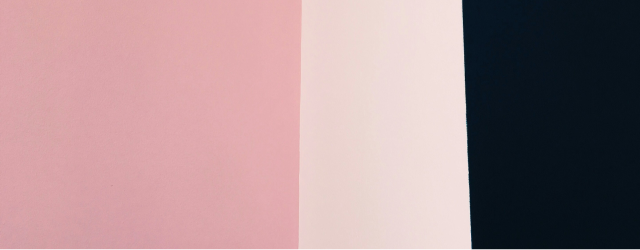