ABS Plastic Manufacturing
Gain a thorough understanding of ABS Plastic Manufacturing in manufacturing, with insights into their application, benefits, and strategic importance in the industry.
Overview of ABS Plastic Manufacturing
ABS plastic manufacturing is the process of transforming raw Acrylonitrile Butadiene Styrene material into practical, consumer-ready products. This involves a series of steps that leverage the unique properties of ABS, including high impact resistance, good tensile strength, and excellent machinability. These attributes make ABS plastic a preferred choice for producing a wide range of products, from automotive components to electronics and household goods. Its significance in contemporary industries cannot be overstated, as ABS plastic provides a solution for manufacturers seeking materials that combine durability with versatility. The polymer's ability to withstand temperature fluctuations and its ease of processing further solidifies its role in producing durable and versatile products. Industries such as automotive, consumer electronics, and construction have long relied on ABS plastic for essential components, showcasing its broad application spectrum. The advent of advanced manufacturing techniques has only enhanced its appeal, allowing for more efficient production processes and innovative product designs.
Role in Manufacturing Efficiency
ABS plastic plays a pivotal role in streamlining manufacturing processes. Its inherent properties facilitate easier handling and processing, reducing production time and costs. The material's consistency allows for high precision in manufacturing, positively impacting product quality and scalability. Moreover, ABS plastic supports sustainable manufacturing practices. Its recyclability and energy-efficient processing methods contribute to a reduced environmental footprint, aligning with the growing demand for green manufacturing solutions. ABS's adaptability to various manufacturing techniques, including injection molding, 3D printing, and CNC machining, further underscores its efficiency. These methods allow manufacturers to optimize production for cost-effectiveness and scalability, maintaining high standards of product quality. By leveraging ABS plastic, companies can produce intricate designs and complex components without compromising durability or performance, ultimately achieving a competitive edge in their respective markets.
Navigate Manufacturing Project Success with Meegle
Historical development of abs plastic manufacturing
Origins of ABS Plastic Manufacturing
The journey of ABS plastic manufacturing began in the mid-20th century, marking a significant milestone in materials science. Initially developed as a result of the increasing demand for polymers with enhanced strength and flexibility, ABS plastic quickly found its niche in the manufacturing industry. Early applications included automotive components and consumer goods, where the material's resilience and adaptability were crucial. Key figures in its development include companies like Borg-Warner Corporation and Dow Chemical Company, who were instrumental in refining the manufacturing processes and expanding ABS's applications. These pioneers recognized the material's potential and invested in research and development to unlock its capabilities. Their efforts laid the foundation for ABS plastic's widespread adoption and set the stage for future advancements. Over time, technological improvements and increased understanding of the material's properties have enabled more efficient and diverse applications, solidifying ABS plastic's role as a staple in modern manufacturing.
Evolution Over Time
The evolution of ABS plastic manufacturing has been marked by significant technological advancements. From its early days as a novel polymer, ABS has undergone methodological changes that have improved production efficiency and broadened its application scope. Innovations such as advanced polymerization techniques and enhanced molding processes have allowed for more precise control over material properties, resulting in superior product quality. These advancements have also facilitated the development of new applications and industries relying on ABS plastic. For example, the introduction of computer-aided manufacturing technologies has revolutionized the production landscape, allowing for customized solutions and rapid prototyping. As a result, ABS plastic manufacturing has become more agile and responsive to industry demands, paving the way for continuous innovation. The ongoing evolution of ABS plastic manufacturing showcases the dynamic nature of the industry, driven by the quest for better performance, sustainability, and cost-effectiveness.
Click here to read our expertly curated top picks!
Core principles and techniques
Fundamental Concepts
Understanding the fundamental concepts of ABS plastic is essential for mastering its manufacturing process. ABS is a copolymer made from Acrylonitrile, Butadiene, and Styrene, each contributing unique properties to the final material. Acrylonitrile provides chemical resistance and thermal stability, Butadiene offers toughness and impact resistance, while Styrene imparts rigidity and ease of processing. The combination of these elements results in a material that is both strong and flexible, capable of meeting diverse manufacturing needs. The manufacturing process of ABS plastic involves polymerization and extrusion, where monomers are chemically bonded to form a stable polymer chain. This process is critical in determining the material's characteristics and suitability for various applications. By manipulating the polymerization conditions, manufacturers can tailor the properties of ABS plastic to meet specific requirements, ensuring optimal performance and quality.
Implementation Techniques
Implementing ABS plastic manufacturing techniques effectively requires a thorough understanding of various processes. Among the most common methods are injection molding, 3D printing, and CNC machining. Injection molding is widely used for producing large volumes of uniform products, leveraging ABS's ease of flow and moldability. The process involves heating ABS pellets until melted, then injecting the molten plastic into a mold cavity where it cools and solidifies. This technique is ideal for creating complex shapes with high precision and consistency. 3D printing offers an innovative approach, enabling rapid prototyping and customization. Using digital models, manufacturers can create intricate designs directly from ABS filament, reducing material waste and production time. CNC machining complements these methods by providing precise cutting and shaping capabilities for ABS plastic, ideal for applications requiring high accuracy. By following a step-by-step guide to implementing these techniques, manufacturers can optimize their processes and achieve superior results.
Benefits and challenges
Advantages in Production
ABS plastic offers numerous advantages in production, making it a valuable asset for manufacturers seeking efficiency and innovation. Its cost benefits are significant, as ABS is relatively inexpensive compared to other polymers with similar properties. This affordability, combined with its durability, makes ABS an attractive choice for producing long-lasting products without incurring high material costs. Moreover, ABS plastic's versatility allows for flexible design and manufacturing options, enabling companies to innovate and adapt to changing market demands. The material's ease of processing reduces production time, facilitating faster turnaround and increased productivity. This efficiency is crucial for maintaining competitiveness in industries with rapid product cycles. By leveraging ABS plastic, manufacturers can enhance product innovation, exploring new designs and applications that set them apart from the competition.
Potential Limitations
Despite its advantages, ABS plastic manufacturing is not without challenges. Environmental impact is a significant concern, as ABS is not biodegradable and its production can contribute to pollution. The material cost, while generally lower than alternatives, can fluctuate based on market conditions and availability. Production limitations may also arise, particularly in applications requiring extreme heat or chemical resistance, where ABS's properties may fall short. To mitigate these challenges, manufacturers can adopt strategies such as incorporating recycled ABS materials to reduce environmental footprint, optimizing processes for efficiency, and exploring hybrid materials that combine ABS with other polymers for enhanced performance. By addressing these limitations, companies can maximize the benefits of ABS plastic manufacturing while minimizing its drawbacks, ensuring sustainable and successful operations.
Click here to read our expertly curated top picks!
Case studies and real-world applications
Industry examples
Industry examples
ABS plastic's versatility is showcased through a variety of industry examples, illustrating its strategic benefits and practical applications. Companies across sectors have leveraged ABS plastic to drive innovation and achieve competitive advantages. These examples provide valuable insights into the material's capabilities and highlight its role in enhancing product quality and efficiency.
Example: automotive industry
Example: automotive industry
In the automotive industry, major manufacturers use ABS plastic for both interior and exterior components, taking advantage of its durability and aesthetic appeal. For instance, dashboards, wheel covers, and trim parts are often made from ABS due to its ability to withstand impact and temperature variations. The material's lightweight nature helps improve fuel efficiency by reducing overall vehicle weight. Companies like Ford and Toyota have integrated ABS plastic into their production lines, resulting in high-quality vehicles that meet consumer demands for both performance and design.
Example: consumer electronics
Example: consumer electronics
ABS plastic plays a crucial role in the consumer electronics sector, where it is used to manufacture durable yet lightweight devices. Products such as smartphones, laptops, and TV casings benefit from ABS's impact resistance and ability to be molded into complex shapes. Leading brands like Samsung and Apple utilize ABS plastic to create sleek, modern designs that protect internal components while maintaining portability and user appeal. This application exemplifies how ABS plastic can enhance product functionality and consumer satisfaction.
Example: construction materials
Example: construction materials
The construction industry benefits from ABS plastic in the production of robust and weather-resistant building materials. Items like plumbing pipes, fittings, and wall panels are made from ABS due to its resistance to corrosion and environmental stress. Companies such as 3M incorporate ABS plastic into their construction solutions, ensuring long-lasting performance and reduced maintenance costs. This application highlights the material's potential in creating sustainable and efficient building solutions.
Impact analysis
Impact analysis
Adopting ABS plastic provides real-world improvements in efficiency and product quality, significantly impacting customer satisfaction and market competitiveness. By utilizing ABS plastic, companies can achieve faster production cycles, reduced costs, and innovative designs that meet consumer expectations. The material's adaptability allows for customization and rapid prototyping, enabling manufacturers to respond to market trends swiftly. As a result, organizations can enhance their brand reputation and secure a stronger foothold in their respective industries. The strategic integration of ABS plastic thus plays a vital role in driving business success and fostering long-term growth.
Technological integration and innovations
Current Technologies
The integration of cutting-edge technologies in ABS plastic manufacturing has revolutionized production processes and enhanced efficiency. Automation and AI have become pivotal in optimizing manufacturing techniques, allowing for precise control over material properties and production variables. Automated systems facilitate faster and more consistent manufacturing, reducing the margin for error and increasing throughput. AI-driven analytics enable manufacturers to predict trends, optimize resource allocation, and enhance quality control measures. Technologies like robotics and IoT are also playing an increasingly significant role, streamlining operations and improving communication between devices and systems. These advancements not only improve the efficiency of ABS plastic manufacturing but also open new possibilities for innovation and customization, providing manufacturers with the tools needed to stay ahead in a competitive market.
Future Trends
The future of ABS plastic manufacturing promises exciting innovations and emerging trends. As materials science continues to evolve, breakthroughs in polymer technology could lead to enhanced ABS formulations with improved characteristics such as heat resistance and biodegradability. Advances in nanotechnology may enable the development of ABS composites with superior mechanical properties, expanding its application scope. The growing emphasis on sustainability will drive the adoption of eco-friendly manufacturing practices, potentially reducing the environmental impact of ABS plastic production. Additionally, the integration of machine learning and big data analytics will further refine manufacturing processes, facilitating predictive maintenance and real-time optimization. These trends suggest a dynamic future for ABS plastic manufacturing, where innovation and efficiency will continue to shape the industry's trajectory.
Click here to read our expertly curated top picks!
Tips for do's and don'ts
Do's | Don'ts |
---|---|
Prioritize high-quality material selection. | Overlook the environmental impact. |
Invest in modern manufacturing technologies. | Neglect regular maintenance of equipment. |
Conduct thorough market research. | Ignore customer feedback and industry trends. |
Click here to read our expertly curated top picks!
Conclusion
Summary of Key Points
ABS plastic manufacturing offers a wealth of advantages, including cost benefits, durability, and versatility. Its role in enhancing production efficiency and product innovation makes it a valuable asset for manufacturers across various industries. By understanding the core principles and techniques of ABS plastic manufacturing, companies can optimize their processes and achieve superior results. Despite potential challenges such as environmental impact and material cost, strategic integration of ABS plastic allows for sustainable and successful operations.
Encouraging Ongoing Adaptation
The dynamic nature of ABS plastic manufacturing necessitates continuous learning and adaptation. By staying informed on emerging trends and technological advancements, manufacturers can maintain a competitive edge in the market. Ongoing education and innovation are crucial for leveraging ABS plastic's full potential, driving efficiency and fostering long-term growth. Embracing new strategies and solutions ensures that companies remain agile and responsive to industry demands, ultimately achieving sustained success in the manufacturing landscape.
Navigate Manufacturing Project Success with Meegle
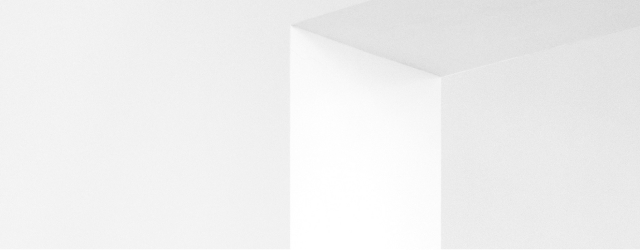
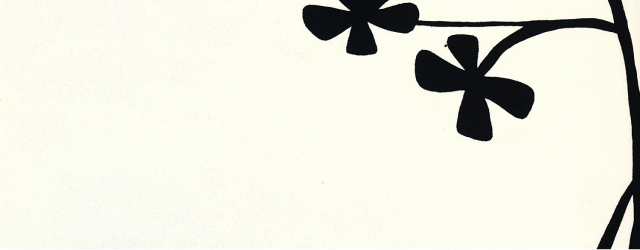
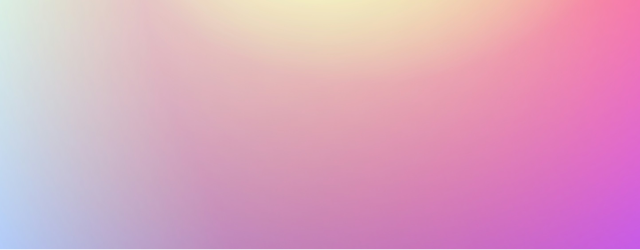
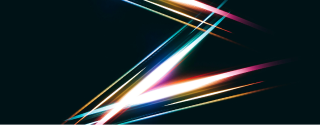
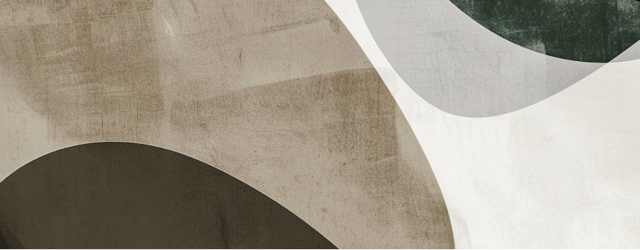
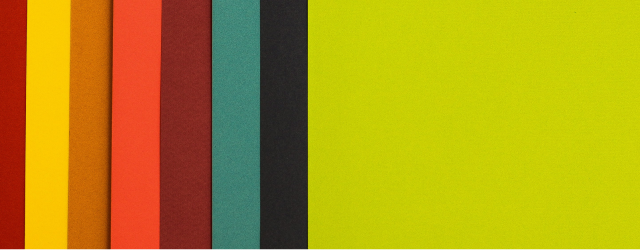
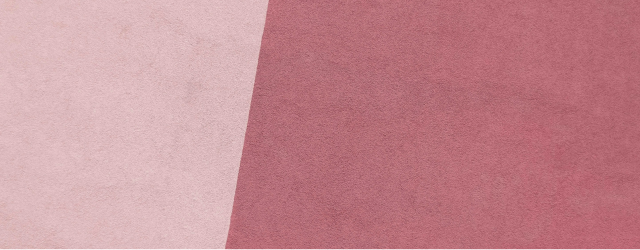