Aeronautical Manufacturing
Gain a thorough understanding of Aeronautical Manufacturing in manufacturing, with insights into their application, benefits, and strategic importance in the industry.
Overview of Aeronautical Manufacturing
Aeronautical manufacturing is a specialized sector within the global manufacturing industry that focuses on the production of aircraft components, systems, and technologies. The scope of aeronautical manufacturing encompasses a wide array of activities, from designing airframes and engines to developing avionics and control systems. This sector is critical for the advancement of aerospace technology, serving as the backbone for producing reliable and efficient aircraft that meet stringent safety and performance standards.
The economic impact of aeronautical manufacturing is profound, with the industry contributing significantly to global GDP and providing millions of jobs worldwide. For example, in 2020, the aerospace sector contributed approximately $80 billion to the U.S. economy, underscoring its importance as a driver of economic activity. With the increasing demand for air travel and the expansion of space exploration initiatives, aeronautical manufacturing continues to grow, pushing the boundaries of technology and innovation.
Furthermore, aeronautical manufacturing plays a crucial role in technological development. The industry's focus on precision engineering, material science, and advanced manufacturing techniques sets the stage for innovations that permeate other sectors. Techniques such as additive manufacturing and the use of composite materials, initially developed for aerospace applications, are now widely adopted in automotive and electronics manufacturing, demonstrating the far-reaching influence of aeronautical manufacturing.
Role in Manufacturing Efficiency
Aeronautical manufacturing is synonymous with operational efficiency, driven by the industry's relentless pursuit of quality, cost-effectiveness, and timely delivery. The integration of advanced manufacturing techniques such as lean manufacturing, automation, and digital systems has revolutionized how aerospace products are developed and produced. These methods optimize workflow, minimize waste, and enhance product quality, leading to significant improvements in manufacturing efficiency.
Lean manufacturing, for instance, is widely adopted in aeronautical manufacturing to streamline processes and eliminate inefficiencies. By focusing on continuous improvement and waste reduction, companies can enhance productivity and reduce production costs, ensuring competitive advantage in a global market. Automation further complements these efforts by enabling precise, repeatable processes that improve product consistency and reduce human error.
One notable example of improved efficiency through advanced techniques is Boeing’s use of robotics in the assembly of its 777 aircraft wings. The integration of robotic systems has reduced the time required for assembly, improved accuracy, and minimized labor costs, illustrating how aeronautical manufacturing can transform production paradigms. Such advancements not only benefit the aerospace sector but also set benchmarks for efficiency that other manufacturing industries strive to achieve.
Navigate Manufacturing Project Success with Meegle
Historical development of aeronautical manufacturing
Origins of Aeronautical Manufacturing
The origins of aeronautical manufacturing can be traced back to the early 20th century, a period marked by significant innovations in aviation. The Wright brothers’ first powered flight in 1903 is often credited with igniting interest in aircraft manufacturing, setting the stage for an industry that would evolve rapidly over the coming decades. This historic achievement demonstrated the potential of powered flight, inspiring engineers and manufacturers to explore new possibilities in air travel.
As aviation gained momentum, so did the need for specialized manufacturing techniques to produce robust and reliable aircraft. The early days of aeronautical manufacturing saw the development of basic airframes and internal combustion engines, focusing on materials like wood and fabric. The advent of World War I accelerated advancements, with manufacturers developing metal airframes and more sophisticated propulsion systems to meet military needs.
Key milestones during this period include the introduction of aluminum alloys, which significantly improved the strength-to-weight ratio of aircraft, and the development of radial engines that provided greater power and reliability. These innovations laid the groundwork for the modern aeronautical manufacturing industry, establishing foundational principles that continue to influence the sector today.
Evolution Over Time
The mid-20th century marked a transformative period for aeronautical manufacturing, characterized by rapid technological advancements and methodological innovations. The introduction of Computer-Aided Design (CAD) and Computer-Aided Manufacturing (CAM) systems revolutionized the design and production of aircraft components, enabling manufacturers to achieve unprecedented levels of precision and efficiency.
During this era, composite materials emerged as a game-changer for the industry, offering enhanced durability and reduced weight compared to traditional metal airframes. The use of composites allowed for the development of more efficient and aerodynamic aircraft, contributing to improved fuel economy and performance. The Boeing 787 Dreamliner, for example, incorporates 50% composite materials, showcasing the transformative impact of these materials on modern aircraft design.
Digital manufacturing processes further propelled the evolution of aeronautical manufacturing, facilitating the integration of sophisticated technologies like simulation, virtual testing, and digital twins. These advancements enable manufacturers to optimize design and production, reduce development costs, and enhance product quality. The continuous evolution of aeronautical manufacturing exemplifies the industry's commitment to innovation and excellence, setting benchmarks for other manufacturing sectors.
Click here to read our expertly curated top picks!
Core principles and techniques
Fundamental Concepts
Aeronautical manufacturing is grounded in several fundamental concepts that ensure the safety, reliability, and performance of aerospace products. Precision engineering is paramount, with manufacturers meticulously designing and producing components that meet exacting specifications. This attention to detail is crucial for maintaining the high standards required in aerospace applications, where even minor deviations can have significant consequences.
Material science plays a vital role in aeronautical manufacturing, with manufacturers constantly exploring new materials to enhance product performance. From lightweight composites to high-strength alloys, the choice of materials directly impacts the durability, efficiency, and safety of aircraft. Regulatory compliance is another critical principle, with stringent standards governing every aspect of aeronautical manufacturing to ensure the highest levels of safety and performance.
These foundational principles are essential for navigating the complexities of aeronautical manufacturing. By adhering to precision engineering, embracing advanced materials, and maintaining regulatory compliance, manufacturers can produce aerospace products that meet the demands of modern air travel while setting benchmarks for quality and innovation.
Implementation Techniques
Aeronautical manufacturing employs a range of advanced techniques to produce components with high precision and durability. Additive manufacturing, or 3D printing, is increasingly used to create complex parts with intricate geometries that would be challenging to produce using traditional methods. This technique allows for rapid prototyping and customization, reducing production time and costs while enhancing product flexibility.
CNC machining is another prevalent technique in aeronautical manufacturing, offering the precision and repeatability needed for producing critical aircraft components. This method involves computer-controlled machinery that can produce parts with exacting specifications, ensuring consistency and reliability across large production volumes.
Bonding technologies, such as adhesive bonding and welding, play a crucial role in assembling aircraft components. These techniques ensure robust connections between parts, contributing to the structural integrity and performance of the aircraft. By implementing these advanced techniques, aeronautical manufacturers can achieve the high standards required in aerospace applications, driving innovation and excellence.
Benefits and challenges
Advantages in Production
Aeronautical manufacturing offers numerous advantages that enhance product performance, safety, and environmental efficiency. The industry’s focus on precision engineering and advanced materials results in aerospace products that deliver superior performance and reliability. For example, the use of composite materials in aircraft design has led to significant improvements in fuel efficiency, reducing environmental impact and operational costs.
Safety standards in aeronautical manufacturing are among the highest in any industry, driven by rigorous regulatory requirements and meticulous quality control processes. This emphasis on safety not only benefits the aerospace sector but also sets benchmarks for other manufacturing industries, fostering a culture of excellence and continuous improvement.
Environmental efficiency is another significant advantage of aeronautical manufacturing, with manufacturers increasingly adopting sustainable practices and technologies. From reducing emissions through improved fuel efficiency to recycling materials and minimizing waste, the industry is committed to enhancing environmental sustainability while maintaining high performance standards.
Potential Limitations
Despite its advantages, aeronautical manufacturing faces several challenges that require strategic solutions. High production costs are a significant limitation, driven by the need for advanced technologies, specialized materials, and skilled labor. These costs can impact profitability and competitiveness, necessitating innovative approaches to cost management and efficiency enhancement.
Stringent regulatory requirements pose another challenge, with manufacturers needing to navigate complex compliance frameworks to ensure safety and performance. This requires a deep understanding of regulatory standards and a commitment to maintaining the highest levels of quality and compliance.
Complex supply chain dynamics further complicate aeronautical manufacturing, with manufacturers needing to coordinate with numerous suppliers and partners to ensure timely delivery and quality assurance. Addressing these challenges requires strategic planning, collaboration, and continuous improvement efforts to optimize processes and overcome obstacles.
Click here to read our expertly curated top picks!
Case studies and real-world applications
Industry examples
Industry examples
Boeing’s Manufacturing Innovations
Boeing stands as a leader in aeronautical manufacturing, renowned for its innovative approaches to aircraft production. The company’s integration of robotics in the assembly of its 777 wings exemplifies its commitment to efficiency and precision. By automating complex assembly processes, Boeing has reduced labor costs, improved accuracy, and enhanced production speed, setting benchmarks for industry innovation.
Airbus’s Sustainable Practices
Airbus has made significant strides in sustainability through its adoption of composite materials and eco-friendly manufacturing processes. The A350 XWB, which incorporates advanced composites, demonstrates Airbus’s dedication to reducing environmental impact while maintaining high performance standards. This focus on sustainability not only benefits the aerospace sector but also sets a precedent for other industries to follow.
Lockheed Martin’s Advanced Technologies
Lockheed Martin exemplifies innovation in aeronautical manufacturing through its use of digital twins and IoT-enabled systems. These technologies enhance product development, allowing for virtual testing and optimization before physical production. Lockheed Martin’s commitment to integrating cutting-edge technologies underscores its role as a pioneer in aerospace innovation.
Impact analysis
Impact analysis
The impact of aeronautical manufacturing is far-reaching, influencing not only the aerospace sector but also broader economic and technological landscapes. Improvements in aircraft design, driven by advanced materials and manufacturing techniques, contribute to enhanced safety, efficiency, and performance. These advancements have profound implications for air travel, supporting increased demand and expanding access to global markets.
Aeronautical manufacturing’s focus on sustainability and environmental efficiency sets benchmarks for other industries, promoting eco-friendly practices and technologies. The adoption of composite materials and energy-efficient designs reduces emissions and minimizes waste, fostering a culture of environmental responsibility.
Economic growth within the aerospace sector is another significant impact of aeronautical manufacturing, with the industry contributing billions to global GDP and providing millions of jobs worldwide. As demand for air travel and space exploration continues to grow, aeronautical manufacturing will play an increasingly vital role in driving economic activity and technological progress.
Technological integration and innovations
Current Technologies
Current technologies in aeronautical manufacturing are revolutionizing production processes and product development, driving efficiency and innovation. The Internet of Things (IoT) enables real-time monitoring and control of manufacturing systems, enhancing operational efficiency and product quality. By integrating IoT-enabled devices and sensors, manufacturers can optimize workflows, reduce downtime, and improve accuracy.
Artificial Intelligence (AI) is another transformative technology, offering predictive analytics and automation capabilities that enhance decision-making and production processes. AI-driven systems can analyze vast amounts of data, identifying patterns and insights that inform strategic planning and continuous improvement efforts.
Robotics play a crucial role in aeronautical manufacturing, automating complex tasks and improving precision. Advanced robotic systems can perform intricate assembly and fabrication processes, reducing labor costs and minimizing human error. By embracing these technologies, aeronautical manufacturers can achieve unprecedented levels of efficiency and innovation.
Future Trends
The future of aeronautical manufacturing is promising, with anticipated advancements in materials science, digital twins, and autonomous manufacturing systems poised to reshape the industry. Innovations in materials science, such as the development of ultra-lightweight alloys and smart materials, will enhance aircraft performance and fuel efficiency, driving sustainability and environmental responsibility.
Digital twins, which simulate real-world systems and processes, will revolutionize product development and optimization. By creating virtual models of aircraft components and systems, manufacturers can conduct extensive testing and analysis before physical production, reducing costs and improving quality.
Autonomous manufacturing systems, driven by AI and robotics, will further enhance efficiency and precision. These systems can perform complex tasks with minimal human intervention, reducing labor costs and improving accuracy. The integration of these technologies promises to transform aeronautical manufacturing, setting benchmarks for innovation and excellence.
Click here to read our expertly curated top picks!
Do's and dont's in aeronautical manufacturing
Do's | Dont's |
---|---|
Invest in advanced technologies | Neglect regulatory compliance |
Prioritize safety and quality | Ignore the importance of skilled workforce |
Foster innovation and continuous improvement | Overlook environmental considerations |
Click here to read our expertly curated top picks!
Faqs about aeronautical manufacturing
What is aeronautical manufacturing?
Aeronautical manufacturing is the specialized process of designing, producing, and assembling aircraft components and systems. This sector is vital for the advancement of aerospace technology, focusing on precision engineering, material science, and regulatory compliance to ensure safety, reliability, and performance of aerospace products.
How does aeronautical manufacturing impact other industries?
Aeronautical manufacturing influences other industries by driving technological advancements and setting benchmarks for quality and safety. Techniques such as additive manufacturing and the use of composite materials, initially developed for aerospace applications, are now widely adopted in automotive and electronics manufacturing, demonstrating the far-reaching impact of aeronautical innovations.
What are the key challenges in aeronautical manufacturing?
Key challenges in aeronautical manufacturing include high production costs, stringent regulatory requirements, and complex supply chain dynamics. Addressing these challenges requires strategic planning, collaboration, and continuous improvement efforts to optimize processes and overcome obstacles.
How are new technologies integrated into aeronautical manufacturing?
New technologies are integrated into aeronautical manufacturing through strategic planning and implementation. This includes assessing potential benefits, providing workforce training, and ensuring regulatory compliance. Technologies like AI, IoT, and robotics enhance production processes, driving efficiency and innovation.
What future trends are expected in aeronautical manufacturing?
Future trends in aeronautical manufacturing include advancements in materials science, digital twins, and autonomous manufacturing systems. These innovations are poised to enhance aircraft performance, fuel efficiency, and sustainability, transforming the aerospace industry and setting benchmarks for other manufacturing sectors.
Conclusion
Summary of Key Points
Aeronautical manufacturing is a pivotal sector that shapes technological progress across diverse manufacturing fields. Its focus on precision engineering, advanced materials, and regulatory compliance ensures the safety, reliability, and performance of aerospace products. The integration of innovative techniques such as additive manufacturing, CNC machining, and robotics drives efficiency and excellence, setting benchmarks for other industries. Despite challenges like high production costs and complex supply chain dynamics, aeronautical manufacturing continues to evolve, pushing the boundaries of technology and innovation.
Encouraging Ongoing Adaptation
Professionals in the manufacturing industry are encouraged to stay informed about advancements in aeronautical manufacturing and consider integrating these strategies to optimize processes and drive innovation. By embracing advanced technologies, fostering a culture of continuous improvement, and maintaining regulatory compliance, manufacturers can enhance efficiency, quality, and sustainability, leading to transformative impacts on both aerospace and general manufacturing. As the industry continues to evolve, staying ahead of trends and innovations will be crucial for maintaining competitive advantage and driving economic growth.
Navigate Manufacturing Project Success with Meegle
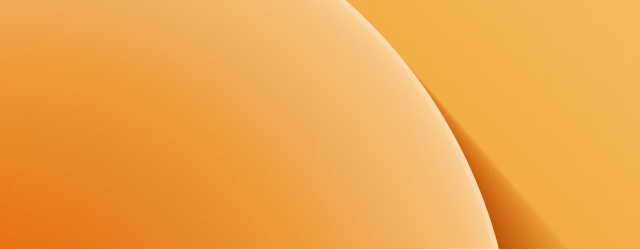
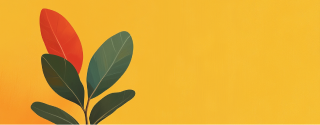
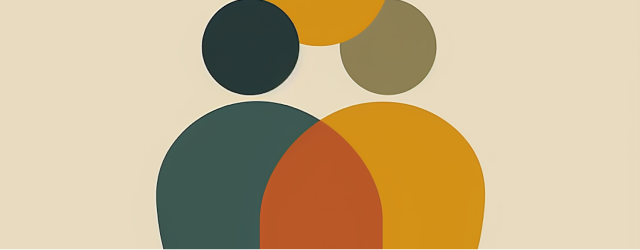
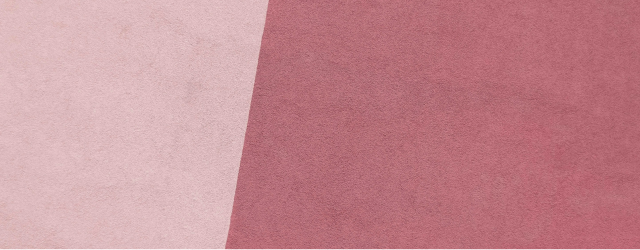
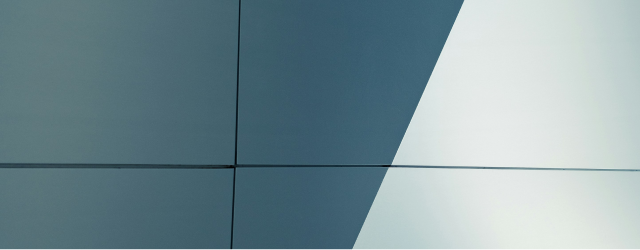
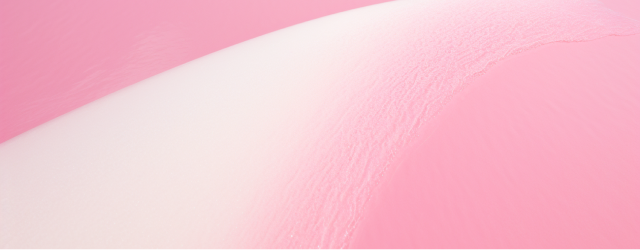