Agile Manufacturing
Gain a thorough understanding of Agile Manufacturing in manufacturing, with insights into their application, benefits, and strategic importance in the industry.
Overview of Agile Manufacturing
Agile Manufacturing is a strategic approach that focuses on the ability of a manufacturing system to respond quickly and efficiently to changes in the market. Unlike traditional manufacturing methods, which often prioritize cost reduction and consistent production rates, Agile Manufacturing emphasizes flexibility, responsiveness, and customer-centric production. This methodology allows companies to rapidly adjust their processes and outputs in response to shifts in consumer demand, technological advancements, and competitive pressures. At its core, Agile Manufacturing is about creating a dynamic production environment that encourages innovation and continuous improvement.
The significance of Agile Manufacturing in modern production cannot be overstated. As industries across the globe face unprecedented challenges—ranging from supply chain disruptions to the increasing demand for customization—companies that can quickly adapt will be better positioned to succeed. Agile Manufacturing enables businesses to maintain high levels of productivity while also being agile enough to pivot when necessary. This adaptability is crucial in an era where product lifecycles are becoming shorter, and consumer preferences are more volatile than ever.
Key elements that characterize Agile Manufacturing include modular production processes, real-time data utilization, and a strong focus on customer feedback. By incorporating these elements, manufacturers can create a more fluid and responsive production system. For instance, modular design allows for quicker adjustments in product specifications without significant downtime. Real-time data analytics enable manufacturers to make informed decisions promptly, enhancing their ability to meet customer needs effectively. This customer-centric approach not only improves satisfaction but also encourages loyalty and repeat business.
Role in Manufacturing Efficiency
Agile Manufacturing significantly impacts operational efficiency by streamlining processes and enhancing product quality. One of the primary ways it achieves this is through the reduction of production times. By implementing Agile practices, manufacturers can decrease the time it takes to bring a product from concept to market. This is particularly beneficial in industries where being first to market can offer a significant competitive advantage. For example, in the fast-paced electronics industry, companies that quickly release new gadgets often capture a larger market share.
Moreover, Agile Manufacturing enhances product quality by fostering a culture of continuous improvement. By regularly soliciting customer feedback and incorporating it into the production process, manufacturers can refine their products to better meet consumer needs. This iterative approach not only boosts customer satisfaction but also leads to the development of higher-quality products. Brands like Zara have successfully utilized Agile practices to streamline their supply chain, reducing lead times and improving product quality.
Several companies have demonstrated improved efficiency through Agile Manufacturing. Tesla, for instance, has embraced Agile principles to enhance its production processes. By using real-time data and maintaining a flexible production line, Tesla can quickly adapt to changes in demand and address quality issues promptly. This agility has contributed to Tesla's reputation for innovation and efficiency in the highly competitive automotive industry.
Navigate Manufacturing Project Success with Meegle
Historical development of agile manufacturing
Origins of Agile Manufacturing
The concept of Agile Manufacturing emerged in response to the limitations of traditional manufacturing methods, which often struggled to keep pace with rapid changes in technology and consumer demand. The origins of Agile Manufacturing can be traced back to the late 20th century, a period characterized by significant shifts in global manufacturing dynamics. During this era, companies began to recognize the need for more flexible and responsive production systems that could quickly adapt to changes in the market.
Early pioneers of Agile Manufacturing played a crucial role in shaping the methodology as we know it today. One notable figure is Dr. Rick Dove, who, in the early 1990s, introduced the concept of Agile Manufacturing as part of a research initiative at Lehigh University. His work emphasized the importance of adaptability and responsiveness in manufacturing, laying the groundwork for the development of Agile principles. Similarly, companies like Toyota, with their lean manufacturing practices, contributed to the evolution of Agile concepts by demonstrating the benefits of streamlined production processes and continuous improvement.
The initial challenges faced by Agile Manufacturing were not insignificant. Traditional manufacturing systems were often rigid and resistant to change, making the transition to a more flexible approach difficult. Additionally, the lack of technological infrastructure at the time limited the ability of manufacturers to implement real-time data analysis and modular design effectively. However, these challenges also led to significant breakthroughs. As technology advanced, manufacturers began to adopt automation and digital tools that facilitated Agile practices. This evolution marked a turning point for Agile Manufacturing, allowing it to gain traction and become a viable alternative to conventional methods.
Evolution Over Time
The evolution of Agile Manufacturing has been significantly influenced by technological advancements, globalization, and the digital transformation of industries. As technology has progressed, manufacturers have been able to leverage new tools and systems to enhance their agility and responsiveness. The advent of automation and robotics, for example, has enabled companies to streamline their production processes and reduce lead times. By automating repetitive tasks, manufacturers can free up resources to focus on innovation and strategic decision-making, further enhancing their agility.
Globalization has also played a pivotal role in the evolution of Agile Manufacturing. As companies expanded their operations across borders, the need for more adaptable and responsive production systems became apparent. Agile Manufacturing allows businesses to quickly adjust their strategies in response to changes in global markets, such as shifts in consumer preferences or fluctuations in supply chain dynamics. This adaptability is crucial for companies operating in the global marketplace, where competition is fierce and margins can be slim.
The digital transformation of industries has further propelled the evolution of Agile Manufacturing. With the rise of digital technologies, manufacturers can now leverage real-time data and analytics to make informed decisions quickly. This capability enhances their ability to respond to changes in demand, optimize production processes, and improve product quality. The integration of digital tools, such as the Internet of Things (IoT) and artificial intelligence (AI), has also facilitated the development of smart factories, where systems are interconnected and can communicate seamlessly. This connectivity allows for greater flexibility and efficiency, aligning perfectly with the principles of Agile Manufacturing.
As a result of these influences, current Agile practices have been shaped into a sophisticated and effective methodology that offers numerous benefits to manufacturers. By embracing technological advancements, adapting to globalization, and leveraging digital tools, Agile Manufacturing has become a cornerstone of modern production strategies. Companies that adopt this approach can achieve a competitive edge by enhancing their efficiency, responsiveness, and ability to innovate.
Click here to read our expertly curated top picks!
Core principles and techniques
Fundamental Concepts
Agile Manufacturing is founded on several key principles that distinguish it from traditional manufacturing methods. These principles include adaptability, collaboration, and continuous improvement. Adaptability is crucial in Agile Manufacturing, as it allows companies to quickly adjust their production processes in response to changes in market demand or technological advancements. This flexibility enables manufacturers to stay competitive in a rapidly changing industry landscape.
Collaboration is another fundamental principle of Agile Manufacturing. By fostering a collaborative environment, companies can encourage cross-functional teams to work together effectively. This teamwork not only enhances communication and innovation but also allows for more efficient problem-solving and decision-making. In Agile Manufacturing, collaboration extends beyond internal teams to include suppliers, customers, and other stakeholders, ensuring that everyone is aligned and working towards common goals.
Continuous improvement is at the heart of Agile Manufacturing. This principle emphasizes the importance of regularly evaluating and refining production processes to enhance efficiency and quality. By adopting an iterative approach, manufacturers can identify areas for improvement and implement changes quickly. This focus on continuous improvement ensures that companies remain agile and responsive to changes in the market or technology.
Customer feedback is a critical component of Agile Manufacturing, as it provides valuable insights that can inform production decisions. By actively soliciting and incorporating customer feedback, manufacturers can improve product quality and ensure that their offerings meet consumer needs. This customer-centric approach enhances satisfaction and loyalty, ultimately driving business success.
When comparing Agile Manufacturing with lean manufacturing, it is important to note that while both methodologies emphasize efficiency and waste reduction, they differ in their approach. Lean manufacturing focuses on eliminating waste and optimizing processes to achieve a steady production flow. In contrast, Agile Manufacturing prioritizes flexibility and responsiveness, allowing for rapid adjustments in production processes. Despite these differences, the two approaches can complement each other, as both aim to enhance operational efficiency and product quality.
Implementation Techniques
Implementing Agile Manufacturing in a production setting requires a strategic approach that incorporates several practical methods. One such technique is modular design, which involves creating products with interchangeable components. This approach allows manufacturers to quickly modify product specifications without significant downtime or cost increases. By adopting modular design, companies can enhance their flexibility and responsiveness, enabling them to better meet changing consumer demands.
Cross-functional teams play a crucial role in implementing Agile Manufacturing. By bringing together individuals with diverse expertise and perspectives, companies can foster a collaborative environment that encourages innovation and problem-solving. These teams can work together to identify areas for improvement, develop new strategies, and implement changes effectively. Cross-functional collaboration also ensures that all stakeholders are aligned and working towards common goals, further enhancing efficiency and productivity.
Rapid prototyping is another key technique in Agile Manufacturing. This approach involves quickly creating and testing new product iterations, allowing manufacturers to refine their designs and processes based on real-time feedback. By adopting rapid prototyping, companies can reduce development times and improve product quality, ultimately enhancing their ability to respond to market changes and consumer needs.
Overcoming implementation challenges is critical for the successful adoption of Agile Manufacturing. Common challenges include resistance to change, resource constraints, and a lack of understanding of Agile principles. To address these challenges, companies can invest in training programs that educate employees on Agile methodologies and foster a culture of continuous improvement. Additionally, leadership support is essential in driving change and ensuring that all stakeholders are committed to the Agile transformation.
Benefits and challenges
Advantages in Production
Agile Manufacturing offers several benefits that contribute to increased flexibility, faster time-to-market, and improved customer satisfaction. One of the primary advantages of Agile Manufacturing is its ability to enhance flexibility in production processes. By adopting Agile principles, companies can quickly adjust their operations in response to changes in consumer demand, technological advancements, or market dynamics. This flexibility enables manufacturers to stay competitive in an ever-changing industry landscape.
Faster time-to-market is another significant benefit of Agile Manufacturing. By streamlining production processes and incorporating rapid prototyping techniques, companies can reduce development times and bring products to market more quickly. This speed is particularly advantageous in industries where being first to market can provide a competitive edge. For example, in the fast-paced fashion industry, brands like Zara have successfully implemented Agile practices to reduce lead times and ensure that their products are always in line with the latest trends.
Improved customer satisfaction is a key outcome of Agile Manufacturing, as it emphasizes a customer-centric approach. By actively soliciting and incorporating customer feedback, manufacturers can develop products that better meet consumer needs and preferences. This focus on the customer not only enhances satisfaction but also encourages loyalty and repeat business. Companies like Dell have leveraged Agile practices to improve their product offerings and provide customers with a more personalized experience.
Case studies illustrate the positive impacts of Agile Manufacturing on production. For instance, Harley-Davidson successfully implemented Agile practices to enhance its production efficiency and product quality. By adopting modular design and cross-functional teams, the company was able to streamline its operations and reduce lead times, ultimately improving customer satisfaction and gaining a competitive advantage in the market.
Potential Limitations
While Agile Manufacturing offers numerous benefits, it also presents certain challenges and limitations that companies must address to ensure successful implementation. One of the primary challenges is cultural resistance to change. Traditional manufacturing systems are often characterized by rigid hierarchies and established processes, making it difficult for employees to embrace new methodologies. To overcome this resistance, companies can invest in training programs that educate employees on Agile principles and foster a culture of continuous improvement.
Resource constraints are another limitation associated with Agile Manufacturing. Implementing Agile practices often requires significant investments in technology, infrastructure, and personnel. Companies may struggle to allocate the necessary resources to support the transition to Agile Manufacturing. To address this challenge, businesses can prioritize investments based on their specific needs and capabilities, ensuring that they focus on the most critical areas for improvement.
Leadership support is crucial in overcoming the challenges associated with Agile Manufacturing. Leaders play a vital role in driving change and ensuring that all stakeholders are committed to the Agile transformation. By fostering a supportive environment and providing the necessary resources, leaders can facilitate the successful implementation of Agile practices and help the organization achieve its goals.
In addition to these challenges, companies may face difficulties in maintaining the balance between flexibility and efficiency. While Agile Manufacturing emphasizes adaptability, it is essential to ensure that production processes remain efficient and cost-effective. By carefully monitoring and evaluating production metrics, companies can identify areas for improvement and optimize their operations accordingly.
Click here to read our expertly curated top picks!
Case studies and real-world applications
Industry examples
Industry examples
Several industries and companies have successfully implemented Agile Manufacturing, showcasing its effectiveness in enhancing production efficiency and innovation. One notable example is the automotive industry, where companies like Toyota have embraced Agile practices to streamline their operations and improve product quality. By adopting modular design and cross-functional teams, Toyota has been able to reduce lead times and develop vehicles that meet changing consumer demands.
In the electronics industry, companies like Apple have leveraged Agile Manufacturing to maintain their competitive edge. By integrating real-time data analysis and rapid prototyping techniques, Apple can quickly adapt to market changes and release new products that align with consumer preferences. This agility has contributed to Apple's reputation for innovation and quality in the highly competitive electronics market.
The fashion industry is another sector that has benefited from Agile Manufacturing. Brands like Zara have successfully implemented Agile practices to reduce production times and ensure that their products are always in line with the latest trends. By maintaining a flexible and responsive supply chain, Zara can quickly adjust its operations in response to changes in consumer demand, ultimately enhancing its ability to stay ahead of the competition.
Impact analysis
Impact analysis
The tangible impacts of Agile Manufacturing in real-world scenarios can be measured using various metrics, such as production speed, quality improvements, and customer satisfaction. Companies that have adopted Agile Manufacturing practices often report significant improvements in these areas, demonstrating the effectiveness of the approach in enhancing production efficiency and innovation.
For example, Harley-Davidson's implementation of Agile practices resulted in a 30% reduction in production lead times and a 20% improvement in product quality. These improvements not only enhanced customer satisfaction but also contributed to the company's competitive advantage in the market. Similarly, Dell's adoption of Agile Manufacturing enabled the company to reduce its product development cycle by 50%, allowing it to release new products more quickly and efficiently.
Lessons learned from these case studies highlight the importance of collaboration, adaptability, and continuous improvement in achieving successful outcomes. By fostering a culture of innovation and embracing Agile principles, companies can enhance their ability to respond to market changes and optimize their production processes. Best practices include investing in technology and infrastructure, fostering cross-functional collaboration, and prioritizing customer feedback to ensure that products meet consumer needs and expectations.
Technological integration and innovations
Current Technologies
Several current technologies enhance or rely on Agile Manufacturing, facilitating real-time data analysis and decision-making. One such technology is the Internet of Things (IoT), which allows manufacturers to connect devices and systems within their production environment. By leveraging IoT, companies can collect and analyze data in real-time, enabling them to make informed decisions quickly and improve production efficiency.
Artificial Intelligence (AI) is another technology that plays a crucial role in Agile Manufacturing. AI-powered systems can analyze vast amounts of data and provide insights that inform production decisions. For example, AI can be used to predict equipment failures, optimize supply chain operations, and enhance product quality. By integrating AI into their production processes, manufacturers can improve their agility and responsiveness, ultimately enhancing their ability to meet consumer demands.
Cloud computing is also integral to Agile Manufacturing, as it provides the infrastructure needed to store and process data efficiently. By leveraging cloud-based systems, manufacturers can access data and insights from anywhere, ensuring that they have the information needed to make informed decisions. Cloud computing also facilitates collaboration between teams, enabling them to work together more effectively and efficiently.
Innovative applications of these technologies include the development of smart factories, where systems and devices are interconnected and can communicate seamlessly. In a smart factory, data from sensors and devices is collected and analyzed in real-time, allowing manufacturers to optimize their production processes and enhance efficiency. This connectivity aligns perfectly with the principles of Agile Manufacturing, enabling companies to maintain a flexible and responsive production environment.
Future Trends
The future of Agile Manufacturing is likely to be shaped by several emerging trends and innovations in technology. One such trend is Industry 4.0, which refers to the integration of digital technologies into manufacturing processes. Industry 4.0 technologies, such as IoT, AI, and robotics, are expected to drive significant advancements in Agile Manufacturing by enhancing connectivity, automation, and data analysis.
Another emerging trend is the use of digital twins, which are virtual replicas of physical systems or processes. Digital twins allow manufacturers to simulate and analyze production scenarios in a virtual environment, enabling them to identify areas for improvement and optimize their operations. By leveraging digital twins, companies can enhance their agility and responsiveness, ultimately improving their ability to meet consumer demands.
Smart factories are also expected to play a significant role in the future of Agile Manufacturing. As technology continues to advance, smart factories will become more prevalent, offering manufacturers enhanced connectivity and real-time data analysis capabilities. This connectivity will enable companies to maintain a flexible and responsive production environment, aligning perfectly with the principles of Agile Manufacturing.
The potential impact of these trends on Agile practices is significant, as they offer manufacturers new tools and capabilities to enhance their agility and responsiveness. By embracing these emerging technologies, companies can improve their production efficiency and innovation, ultimately gaining a competitive edge in the market.
Click here to read our expertly curated top picks!
Tips for do's and dont's
Do's | Don'ts |
---|---|
Foster open communication | Ignore employee feedback |
Invest in training programs | Overlook the importance of planning |
Embrace technology | Resist change |
Encourage collaboration | Work in silos |
Focus on customer needs | Neglect quality control |
Click here to read our expertly curated top picks!
Faqs about agile manufacturing
What is Agile Manufacturing?
Agile Manufacturing is a strategic approach that emphasizes flexibility, adaptability, and customer-centric production. It focuses on creating a dynamic production environment that can quickly respond to changes in market demand, technological advancements, and competitive pressures. Agile Manufacturing incorporates elements such as modular design, cross-functional teams, and real-time data analysis to enhance production efficiency and innovation.
How does Agile Manufacturing differ from Lean Manufacturing?
While both Agile and Lean Manufacturing aim to enhance efficiency and reduce waste, they differ in their approach. Lean Manufacturing focuses on optimizing processes to achieve a steady production flow and eliminate waste. In contrast, Agile Manufacturing prioritizes flexibility and responsiveness, allowing for rapid adjustments in production processes based on changing market demands and consumer preferences.
What are the key benefits of implementing Agile Manufacturing?
Implementing Agile Manufacturing offers several benefits, including increased flexibility, faster time-to-market, and improved customer satisfaction. By adopting Agile practices, companies can quickly adjust their production processes in response to changes in demand or market dynamics. This adaptability allows manufacturers to stay competitive in a rapidly changing industry landscape.
What challenges might a company face in adopting Agile Manufacturing?
Companies may face challenges such as cultural resistance to change, resource constraints, and maintaining a balance between flexibility and efficiency when adopting Agile Manufacturing. Overcoming these challenges requires leadership support, investment in training programs, and a strong commitment to fostering a culture of continuous improvement and collaboration.
How can Agile Manufacturing contribute to sustainability?
Agile Manufacturing can contribute to sustainability by promoting efficient resource usage, reducing waste, and enhancing product quality. By adopting flexible and responsive production processes, manufacturers can minimize their environmental impact and optimize their operations to align with sustainable practices. Additionally, Agile principles encourage continuous improvement and innovation, which can lead to the development of more sustainable products and processes.
Conclusion
Summary of Key Points
Agile Manufacturing is a transformative approach that emphasizes flexibility, adaptability, and customer-centric production. By adopting Agile principles, manufacturers can enhance their production efficiency, reduce lead times, and improve product quality. This approach is particularly relevant in today's fast-paced production environments, where companies must quickly respond to changes in market demand and technological advancements. Agile Manufacturing offers numerous benefits, including increased flexibility, faster time-to-market, and improved customer satisfaction. However, successful implementation requires addressing challenges such as cultural resistance, resource constraints, and maintaining a balance between flexibility and efficiency.
Encouraging Ongoing Adaptation
As technology continues to evolve and market dynamics shift, it is crucial for professionals to remain informed about new developments in Agile Manufacturing. Continuous adaptation and improvement are essential for maintaining a competitive edge and achieving long-term success. By staying informed and integrating Agile practices into their operations, manufacturers can enhance their production efficiency and innovation, ultimately gaining a competitive advantage in the market. The journey towards Agile Manufacturing is ongoing, and companies that embrace this approach will be better positioned to thrive in the ever-changing manufacturing landscape.
Navigate Manufacturing Project Success with Meegle
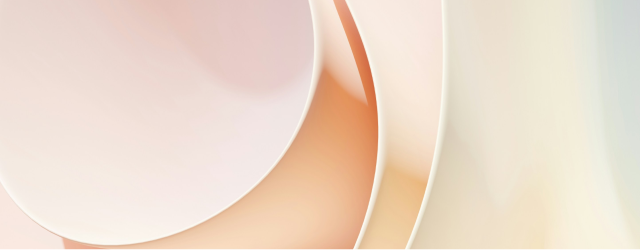
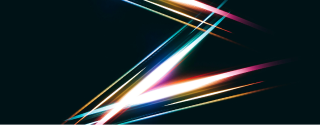
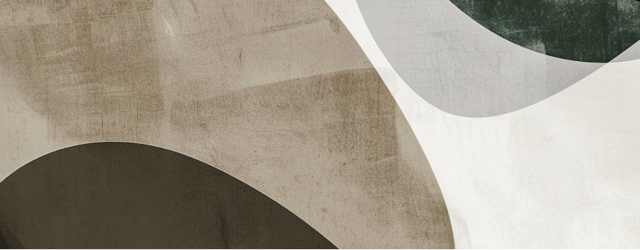
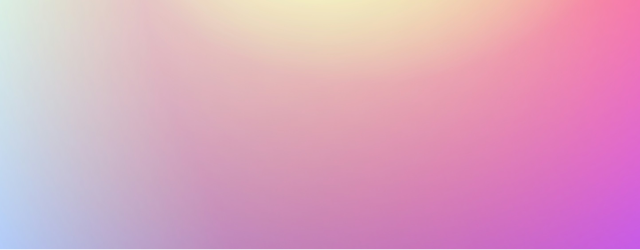
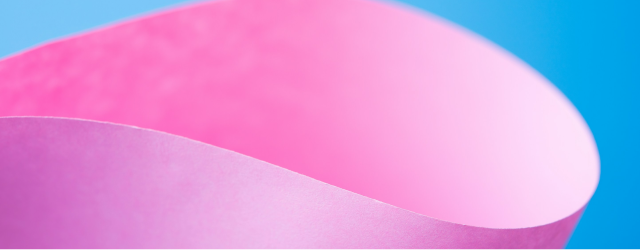
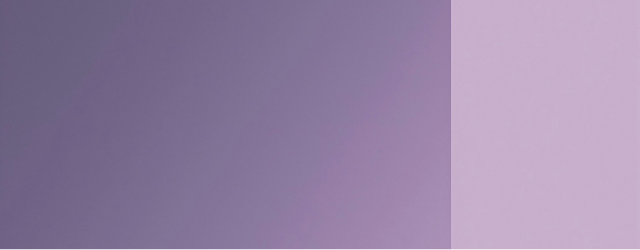
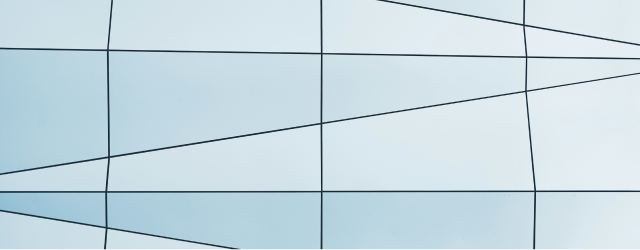
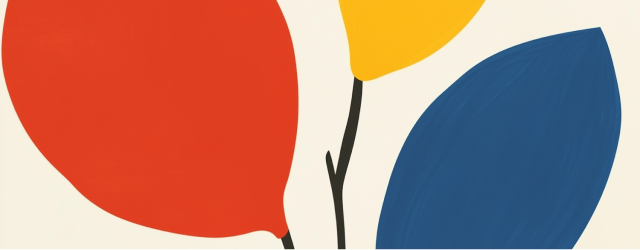