Alloy Manufacturing
Gain a thorough understanding of Alloy Manufacturing in manufacturing, with insights into their application, benefits, and strategic importance in the industry.
Overview of Alloy Manufacturing
Alloy manufacturing is the process of combining different metals or elements to create materials with superior properties. These enhanced materials are integral to industries ranging from aerospace to automotive, where characteristics like increased strength, corrosion resistance, and thermal stability are paramount. Understanding how alloys are manufactured is essential for professionals seeking to optimize the performance and durability of their products. For instance, the automotive industry relies heavily on alloys to ensure that vehicles are lightweight yet sturdy, enhancing fuel efficiency and safety. By incorporating alloys, manufacturers can tailor the properties of metals to meet specific requirements, leading to innovative solutions that address complex industrial challenges.
Role in Manufacturing Efficiency
The integration of alloy manufacturing into production processes significantly enhances efficiency and quality. Tailoring the properties of alloys to suit particular applications allows manufacturers to achieve higher performance standards while minimizing waste and energy consumption. For example, in the aerospace industry, alloys are engineered to withstand extreme temperatures and pressures, allowing for the production of lighter and more fuel-efficient aircraft. This not only streamlines operations but also results in superior product outcomes that meet stringent industry standards. Furthermore, the ability to recycle and reuse alloy materials contributes to sustainability efforts, reducing the environmental footprint of manufacturing activities.
Navigate Manufacturing Project Success with Meegle
Historical development of alloy manufacturing
Origins of Alloy Manufacturing
The history of alloy manufacturing dates back thousands of years, with early civilizations experimenting with bronze and steel. The Bronze Age marked a significant turning point, as the creation of bronze—a copper and tin alloy—revolutionized tools and weapons, paving the way for advancements in agriculture and warfare. This historical exploration highlights the ingenuity and curiosity of ancient metallurgists who laid the foundations for modern alloy manufacturing. The transition to the Iron Age further exemplified the potential of alloys, as steel became the material of choice for construction and machinery, setting the stage for the industrial advancements that followed.
Evolution Over Time
Alloy manufacturing has undergone significant technological advancements over the centuries. The Industrial Revolution was a pivotal era, as metallurgical innovations like the Bessemer process allowed for the mass production of steel, drastically changing the manufacturing landscape. As technology evolved, so did the methods of alloy production, leading to the development of specialized alloys for various applications. Today, cutting-edge techniques such as powder metallurgy and additive manufacturing are employed to create alloys with precise characteristics. These advancements have not only transformed material science and engineering but also expanded the possibilities for innovation across multiple industries.
Click here to read our expertly curated top picks!
Core principles and techniques
Fundamental Concepts
At the heart of alloy manufacturing are principles such as phase equilibrium and solubility, which dictate the behavior and characteristics of alloy systems. Phase equilibrium involves the balance between different phases of a material, ensuring the stability and uniformity of the alloy. Solubility, on the other hand, refers to the ability of elements to dissolve within a metal matrix, affecting the distribution and properties of the alloy. Understanding these fundamental concepts is crucial for professionals aiming to manipulate metal properties effectively. By mastering these principles, manufacturers can predict and control the performance of alloys, leading to optimized products that meet specific industry requirements.
Implementation Techniques
Various techniques are employed in alloy manufacturing, each offering distinct advantages for producing high-quality alloys. Casting is one of the oldest methods, involving pouring molten metal into molds to form desired shapes. Powder metallurgy, another technique, involves compressing metal powders and heating them to create solid components, allowing for precise control over composition and microstructure. Additive manufacturing, or 3D printing, represents a modern approach, enabling the creation of complex geometries with minimal waste. These techniques are not only pivotal in achieving superior material properties but also play a critical role in advancing manufacturing processes across diverse sectors.
Benefits and challenges
Advantages in Production
Alloy manufacturing provides numerous advantages, from enhancing mechanical properties to improving metallurgical compatibility. Alloys such as stainless steel and titanium are renowned for their strength, corrosion resistance, and lightweight nature, making them ideal for high-performance applications. These benefits translate into improved production processes and end products, allowing manufacturers to deliver solutions that meet rigorous industry standards. Furthermore, the versatility of alloys enables the creation of custom materials tailored to specific needs, fostering innovation and competitive advantage in the manufacturing sector.
Potential Limitations
Despite its advantages, alloy manufacturing presents challenges such as cost implications and technical complexities. The production of specialized alloys often requires significant investment in equipment and expertise, which can be a barrier for smaller manufacturers. Additionally, the intricate nature of alloy processes demands precise control and monitoring to ensure consistent quality, posing technical difficulties. Addressing these barriers involves adopting strategies such as investing in advanced technologies and fostering collaborations with industry experts, enabling professionals to maximize the potential of alloy manufacturing while mitigating its limitations.
Click here to read our expertly curated top picks!
Case studies and real-world applications
Industry examples
Industry examples
Industries such as aerospace, automotive, and electronics have successfully integrated alloy manufacturing into their operations, realizing tangible benefits through strategic alloy use. In aerospace, the development of superalloys capable of withstanding extreme temperatures has revolutionized jet engine design, enhancing efficiency and performance. The automotive sector has leveraged aluminum alloys to produce lighter vehicles, improving fuel economy and reducing emissions. In electronics, copper alloys are utilized to create durable and conductive components, ensuring reliability and longevity. These case studies demonstrate the profound impact of alloy manufacturing on various industries, highlighting its role in driving innovation and competitiveness.
Impact analysis
Impact analysis
The real-world impacts of alloy manufacturing extend beyond product performance, influencing production efficiency, product quality, and sustainability. By adopting alloy manufacturing techniques, businesses can streamline operations, reduce material usage, and minimize environmental impact, contributing to sustainability goals. Furthermore, the ability to produce high-quality alloys enhances product reliability and longevity, resulting in increased customer satisfaction and competitive advantage. Analyzing these impacts provides insights into how businesses can leverage alloy manufacturing improvements to achieve strategic objectives and maintain a leading edge in their respective industries.
Technological integration and innovations
Current Technologies
Cutting-edge technologies are reshaping how alloys are developed and applied, driving advancements in alloy manufacturing. AI-driven material design is one such innovation, enabling the prediction of alloy properties and optimization of compositions for specific applications. Advanced simulation tools allow manufacturers to model alloy behavior under various conditions, facilitating the design of materials with precise characteristics. These technologies not only enhance the efficiency and accuracy of alloy manufacturing processes but also open new avenues for innovation, empowering professionals to push the boundaries of material science and engineering.
Future Trends
Predicting future developments in alloy manufacturing involves exploring emerging materials and processes that could redefine industry standards and practices. Nanotechnology, for instance, holds the potential to create alloys with unprecedented properties, such as enhanced strength and conductivity. The integration of sustainable practices, such as the use of recycled materials and eco-friendly production methods, is expected to gain traction, aligning alloy manufacturing with global environmental goals. As these trends unfold, professionals must stay informed and adaptable, ensuring they are well-equipped to leverage new opportunities and maintain their competitive edge in the evolving manufacturing landscape.
Click here to read our expertly curated top picks!
Tips for alloy manufacturing
Do's and Don'ts
Do's | Don'ts |
---|---|
Thoroughly assess material compatibility | Avoid overlooking environmental impact |
Invest in advanced equipment and technologies | Neglect regular maintenance and quality checks |
Collaborate with experts for innovation | Ignore customer feedback and industry trends |
Click here to read our expertly curated top picks!
Conclusion
Summary of Key Points
In summary, alloy manufacturing plays a pivotal role in transforming industries by enabling the creation of materials with superior properties. From its historical roots to modern innovations, alloy manufacturing has evolved to become a cornerstone of manufacturing efficiency and sustainability. Professionals who understand the core principles and techniques of alloy manufacturing can leverage its advantages to enhance product performance, streamline operations, and maintain a competitive edge. By addressing challenges and embracing technological advancements, businesses can unlock the full potential of alloy manufacturing, driving innovation and success in the global market.
Encouraging Ongoing Adaptation
As the manufacturing landscape continues to evolve, it is imperative for professionals to remain proactive in adapting alloy manufacturing techniques to meet changing industry demands. Continuous improvement through the integration of new technologies, sustainable practices, and strategic collaborations will ensure ongoing success. By staying informed and responsive to trends, professionals can harness the transformative power of alloy manufacturing to lead their industries into the future, maintaining competitiveness and achieving excellence in their operations.
Navigate Manufacturing Project Success with Meegle
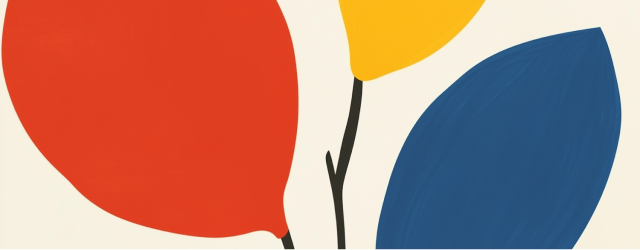
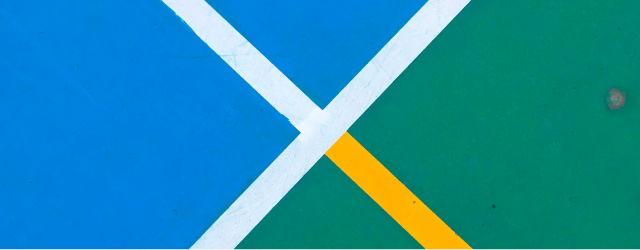
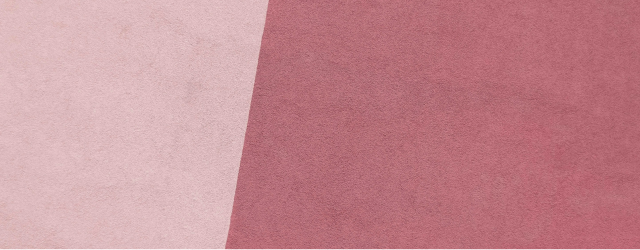
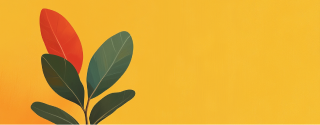
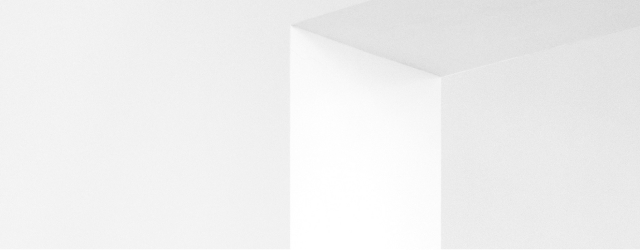
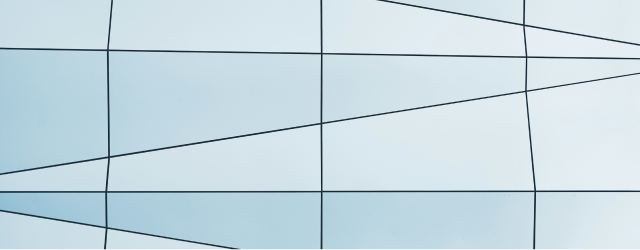
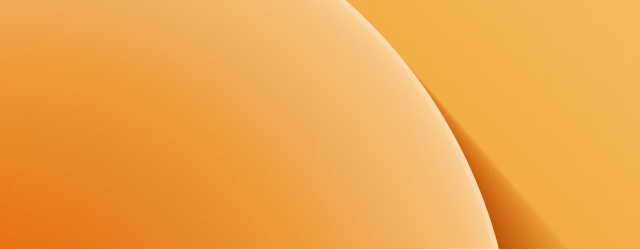
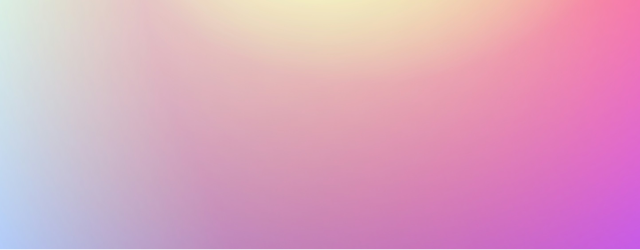