Assembly Jig
Gain a thorough understanding of Assembly Jig in manufacturing, with insights into their application, benefits, and strategic importance in the industry.
Overview of Assembly Jig
Assembly jigs are indispensable fixtures in the manufacturing industry, designed to enhance precision and efficiency during assembly processes. They serve as guides for components, ensuring that each piece fits together correctly, which is crucial for maintaining consistency and quality in mass production environments. The fundamental definition of an assembly jig revolves around its capability to hold parts in exact alignment, facilitating the production of components with minimal variation. This precision is particularly important in industries such as aerospace, automotive, and electronics, where even minute discrepancies can lead to significant issues.
Moreover, assembly jigs streamline workflows by reducing the need for manual adjustments and interventions. By providing a stable and reliable framework for assembly tasks, they minimize human error and enhance the overall speed of production. For instance, consider the automotive industry, where the assembly of intricate car parts requires exact alignment to ensure safety and performance. An assembly jig can significantly reduce assembly time while enhancing precision, leading to a higher quality output.
In essence, the significance of assembly jigs extends beyond mere assembly support. They are instrumental in creating standardized processes that lead to efficient manufacturing cycles. As manufacturing continues to evolve, the reliance on assembly jigs is expected to grow, highlighting their fundamental role in the industry. The ongoing development of advanced jig systems reflects the industry's commitment to improving production methods, ultimately fostering innovation and excellence in manufacturing.
Role in Manufacturing Efficiency
The implementation of assembly jigs in manufacturing has led to significant enhancements in operational efficiency and product quality. These tools are integral to the manufacturing process, offering a range of benefits that optimize productivity while reducing costs. One of the primary advantages of assembly jigs is their ability to minimize manual intervention, thereby enhancing the consistency and quality of products. By providing a structured framework for assembly, jigs ensure that components are accurately aligned, reducing the likelihood of errors and defects.
Assembly jigs also contribute to faster production times. In industries where speed and accuracy are paramount, such as electronics manufacturing, jigs facilitate streamlined processes by eliminating unnecessary steps and reducing assembly time. For example, in semiconductor manufacturing, where precision is vital, assembly jigs can significantly reduce the time required to assemble complex components, leading to increased productivity and reduced labor costs.
Furthermore, assembly jigs play a crucial role in reducing waste. By ensuring precise alignment and reducing the need for rework, they help manufacturers optimize material usage, thereby minimizing waste and associated costs. This efficiency is particularly important in sectors where sustainability and cost-effectiveness are priorities.
In addition to these benefits, assembly jigs enable scalability in manufacturing processes. As production volumes increase, the standardization provided by jigs ensures consistent quality across large batches of products. This capability is essential for industries experiencing rapid growth, allowing manufacturers to meet increased demand without compromising on quality.
Overall, assembly jigs are vital tools for optimizing manufacturing processes. Their impact on reducing waste, improving accuracy, and enabling scalability highlights their importance in the modern manufacturing landscape, making them essential for professionals seeking to enhance efficiency and quality in their operations.
Navigate Manufacturing Project Success with Meegle
Historical development of assembly jig
Origins of Assembly Jig
The concept of assembly jigs has a rich historical background, tracing back to early manufacturing practices where craftsmen devised methods to hold parts in place during assembly. These primitive tools laid the foundation for the sophisticated fixtures used in modern production environments. The origins of assembly jigs can be linked to the industrial revolution, a period marked by significant advancements in manufacturing techniques. During this era, the need for increased production speed and precision drove the development of basic jigs as craftsmen sought to improve efficiency in their work.
In the early days, assembly jigs were simple tools made from wood or metal, designed to hold components in place while craftsmen performed manual assembly tasks. These jigs provided a framework for maintaining alignment and accuracy, allowing manufacturers to produce consistent and reliable products. As industries began to grow, the demand for more efficient assembly techniques became apparent, leading to the evolution of jigs into more complex and specialized tools.
One notable example of early assembly jig use is in the production of firearms. Gunmakers developed jigs to hold gun parts in place while assembling intricate mechanisms, ensuring precision and reliability in the final product. This practice was essential for maintaining the safety and performance of firearms, highlighting the importance of jigs in achieving consistent quality.
As manufacturing techniques continued to evolve, the complexity and functionality of assembly jigs increased. The introduction of interchangeable parts in the late 19th century further underscored the necessity of jigs in achieving uniformity and precision. This period marked a significant shift in manufacturing practices, where the use of assembly jigs became standard in industries such as automotive and aerospace.
Today, the legacy of these early practices is evident in the sophisticated assembly jig systems used in modern manufacturing. The evolution from simple tools to advanced fixtures reflects the industry's ongoing commitment to efficiency and precision, cementing the role of assembly jigs as indispensable components in the manufacturing process.
Evolution Over Time
Over the years, assembly jigs have undergone significant transformations, driven by technological advancements and changing manufacturing needs. The evolution of assembly jig designs and materials has played a crucial role in shaping their current functionality and efficiency, making them indispensable tools in modern production environments.
Initially, assembly jigs were crafted from basic materials such as wood and metal, designed to hold components in place during manual assembly processes. As manufacturing techniques advanced, the demand for more precise and durable jigs led to the adoption of new materials and designs. The introduction of steel and other robust metals marked a significant shift in jig construction, allowing for greater accuracy and reliability in assembly tasks.
The development of computer-aided design (CAD) technology further revolutionized assembly jig design. CAD systems enabled manufacturers to create highly detailed and precise jig models, improving accuracy and reducing the likelihood of errors. This technological advancement facilitated the production of jigs with complex geometries and intricate features, tailored to specific manufacturing requirements.
Additionally, the advent of automation systems has significantly impacted the evolution of assembly jigs. Automated jigs are equipped with sensors and actuators, allowing for real-time monitoring and adjustments during assembly processes. This integration of technology has enhanced the functionality of jigs, providing manufacturers with greater control and flexibility in their operations.
The evolution of assembly jigs is also characterized by the adoption of modular designs. Modular jigs allow manufacturers to easily customize and adapt jigs to different assembly tasks, providing versatility and scalability in production processes. This flexibility is particularly beneficial in industries with diverse product lines, enabling manufacturers to efficiently switch between different assembly configurations.
Overall, the evolution of assembly jigs reflects the industry's commitment to innovation and efficiency. The continuous development of materials, designs, and technologies has resulted in advanced jig systems that enhance precision, reduce costs, and optimize manufacturing processes. As manufacturing continues to evolve, the role of assembly jigs is expected to grow, highlighting their importance in achieving excellence in production environments.
Click here to read our expertly curated top picks!
Core principles and techniques
Fundamental Concepts
The effectiveness of assembly jigs relies on several core principles that underpin their successful application in various manufacturing settings. Understanding these fundamental concepts is crucial for professionals seeking to optimize their use of assembly jigs and enhance production efficiency.
-
Precision: Precision is the cornerstone of assembly jig design and application. By ensuring accurate alignment and positioning of components, jigs facilitate the production of high-quality products with minimal variation. This precision is essential in industries where consistency and reliability are paramount, such as aerospace and automotive manufacturing.
-
Repeatability: Repeatability refers to the ability of assembly jigs to consistently reproduce the same results across multiple production cycles. By providing a stable and reliable framework for assembly tasks, jigs minimize the likelihood of errors and defects, enhancing product quality and reducing the need for rework.
-
Durability: Durability is a critical factor in assembly jig design, as jigs must withstand the rigors of production environments while maintaining their functionality. By selecting robust materials and implementing effective maintenance strategies, manufacturers can ensure the longevity and reliability of their jigs, reducing costs and downtime.
These core principles are essential for achieving optimal results with assembly jigs. By prioritizing precision, repeatability, and durability, professionals can enhance their manufacturing processes and achieve consistent and reliable outcomes. The application of these principles is particularly important in industries where accuracy and efficiency are paramount, making assembly jigs indispensable tools for success.
Implementation Techniques
There are numerous techniques involved in the design and application of assembly jigs, each tailored to specific manufacturing requirements. Understanding these techniques is essential for professionals seeking to implement effective jig systems and optimize their production processes.
-
Modular Jig Systems: Modular jig systems offer versatility and scalability in manufacturing environments. By allowing manufacturers to easily customize and adapt jigs to different assembly tasks, modular systems provide flexibility and efficiency in production processes. This approach is particularly beneficial in industries with diverse product lines, enabling manufacturers to efficiently switch between different assembly configurations.
-
Dedicated Jigs: Dedicated jigs are designed for specific assembly tasks, providing specialized support and precision. By tailoring jigs to particular components and processes, manufacturers can achieve greater accuracy and reliability in their operations. This technique is commonly used in industries such as electronics and aerospace, where precision and consistency are critical.
-
Advanced Materials: The selection of advanced materials is crucial in assembly jig design, as it impacts the durability and functionality of the jig. By utilizing materials such as steel, aluminum, and composites, manufacturers can enhance the longevity and reliability of their jigs, reducing costs and downtime. The use of advanced materials also enables the production of jigs with complex geometries and intricate features, tailored to specific manufacturing requirements.
Overall, these implementation techniques provide professionals with practical strategies for optimizing the use of assembly jigs. By understanding and applying these techniques, manufacturers can enhance precision, reduce costs, and improve efficiency in their production processes, ultimately achieving excellence in manufacturing environments.
Benefits and challenges
Advantages in Production
Assembly jigs offer numerous benefits that enhance production processes, leading to more efficient and reliable manufacturing outcomes. Understanding these advantages is crucial for professionals seeking to optimize their use of jigs and improve productivity in their operations.
-
Reduced Labor Costs: Assembly jigs minimize the need for manual intervention, streamlining workflows and reducing labor costs. By providing a structured framework for assembly tasks, jigs enhance efficiency and speed, allowing manufacturers to achieve higher output levels with fewer resources.
-
Improved Product Quality: Precision and consistency are key benefits of assembly jigs, leading to improved product quality. By ensuring accurate alignment and positioning of components, jigs reduce the likelihood of errors and defects, enhancing the reliability and performance of products.
-
Enhanced Efficiency: Assembly jigs optimize manufacturing processes by eliminating unnecessary steps and reducing assembly time. In industries where speed and accuracy are paramount, such as electronics and aerospace manufacturing, jigs facilitate streamlined workflows, leading to increased productivity and reduced costs.
-
Scalability: Assembly jigs enable scalability in production processes, allowing manufacturers to efficiently meet increased demand without compromising on quality. By providing standardized frameworks for assembly tasks, jigs ensure consistent quality across large batches of products, essential for industries experiencing rapid growth.
Overall, the advantages of assembly jigs contribute to more efficient and reliable manufacturing outcomes, making them indispensable tools for professionals seeking to enhance productivity and quality in their operations. By understanding and leveraging these benefits, manufacturers can achieve excellence in production environments, ultimately fostering innovation and success in the industry.
Potential Limitations
Despite their benefits, assembly jigs can present challenges that manufacturers must address to maximize their effectiveness in production settings. Understanding these potential limitations is crucial for professionals seeking to optimize their use of jigs and overcome obstacles in their operations.
-
High Initial Costs: The initial costs associated with assembly jigs can be significant, particularly when investing in advanced systems and materials. However, the long-term benefits of jigs, such as reduced labor costs and improved product quality, often outweigh these initial expenses, providing a favorable return on investment.
-
Maintenance Requirements: Regular maintenance is essential for ensuring the longevity and reliability of assembly jigs. By implementing effective maintenance strategies, manufacturers can minimize downtime and reduce costs, ultimately enhancing the efficiency of their operations.
-
Customization Challenges: While modular jig systems offer versatility, the customization of dedicated jigs can be challenging and time-consuming. Manufacturers must carefully consider their specific assembly requirements and invest in tailored solutions to achieve optimal results.
Overall, addressing these potential limitations is essential for maximizing the effectiveness of assembly jigs in production settings. By understanding and mitigating these challenges, manufacturers can enhance precision, reduce costs, and improve efficiency in their operations, ultimately achieving excellence in manufacturing environments.
Click here to read our expertly curated top picks!
Case studies and real-world applications
Industry examples
Industry examples
Many industries have successfully integrated assembly jigs into their production processes, leading to significant improvements in efficiency and quality. Understanding these examples is crucial for professionals seeking to optimize their use of jigs and enhance productivity in their operations.
Automotive Industry
In the automotive industry, assembly jigs play a crucial role in ensuring precision and reliability during the assembly of complex car components. By providing a structured framework for tasks such as engine assembly and body alignment, jigs minimize human error and enhance product quality. For instance, leading automotive manufacturers like Toyota have leveraged advanced jig systems to optimize their production processes, achieving higher output levels and improved product performance.
Aerospace Industry
The aerospace industry relies heavily on assembly jigs to achieve the precision and consistency required for the assembly of intricate aircraft components. By utilizing advanced jigs, manufacturers can enhance the reliability and safety of their products. For example, Boeing has implemented sophisticated assembly jig systems to streamline the production of aircraft parts, reducing labor costs and enhancing efficiency in their operations.
Electronics Industry
In the electronics industry, assembly jigs are essential for achieving the accuracy and speed required for the assembly of complex components such as semiconductor devices and circuit boards. By providing a stable framework for assembly tasks, jigs minimize errors and enhance product quality. Leading electronics manufacturers like Intel have integrated advanced jig systems into their production processes, achieving higher output levels and improved product reliability.
Overall, these industry examples underscore the importance of assembly jigs in achieving excellence in manufacturing environments. By understanding and leveraging the benefits of jigs, professionals can optimize their production processes and foster innovation and success in their operations.
Impact analysis
Impact analysis
Through real-world applications, assembly jigs have demonstrated tangible impacts on manufacturing outcomes. Understanding these effects is crucial for professionals seeking to optimize their use of jigs and enhance productivity in their operations.
-
Increased Production Speed: Assembly jigs facilitate streamlined workflows, reducing assembly time and enhancing production speed. In industries where speed is paramount, such as electronics and automotive manufacturing, jigs enable manufacturers to achieve higher output levels with fewer resources.
-
Enhanced Accuracy: The precision provided by assembly jigs leads to improved accuracy in manufacturing processes, reducing the likelihood of errors and defects. By ensuring accurate alignment and positioning of components, jigs enhance product reliability and performance.
-
Reduced Costs: Assembly jigs minimize the need for manual intervention and rework, reducing labor costs and optimizing material usage. By streamlining workflows and enhancing efficiency, jigs contribute to cost-effective production processes.
Overall, the impact of assembly jigs on manufacturing outcomes highlights their importance in achieving excellence in production environments. By understanding and leveraging these effects, professionals can optimize their use of jigs and enhance productivity and quality in their operations, ultimately fostering innovation and success in the industry.
Technological integration and innovations
Current Technologies
Modern manufacturing is increasingly reliant on advanced technologies that enhance the functionality of assembly jigs. Understanding these technologies is crucial for professionals seeking to optimize their use of jigs and improve efficiency in their operations.
-
Computer-Aided Design (CAD): CAD systems enable manufacturers to create highly detailed and precise jig models, improving accuracy and reducing the likelihood of errors. By utilizing CAD technology, professionals can design jigs with complex geometries and intricate features, tailored to specific manufacturing requirements.
-
Automation Systems: Automated jigs are equipped with sensors and actuators, allowing for real-time monitoring and adjustments during assembly processes. By integrating automation technology, manufacturers can enhance the functionality of jigs, providing greater control and flexibility in their operations.
-
Advanced Materials: The selection of advanced materials such as steel, aluminum, and composites impacts the durability and functionality of assembly jigs. By utilizing these materials, manufacturers can enhance the longevity and reliability of their jigs, reducing costs and downtime.
Overall, these current technologies provide professionals with practical strategies for optimizing the use of assembly jigs. By understanding and leveraging these technologies, manufacturers can enhance precision, reduce costs, and improve efficiency in their production processes, ultimately achieving excellence in manufacturing environments.
Future Trends
As manufacturing continues to evolve, new trends and innovations are emerging that will shape the future of assembly jigs. Understanding these developments is crucial for professionals seeking to remain competitive and efficient in the evolving manufacturing landscape.
-
Smart Jigs: The integration of smart technology into assembly jigs is expected to revolutionize their functionality and efficiency. By utilizing sensors, actuators, and IoT technology, smart jigs can provide real-time data and feedback, enhancing control and flexibility in manufacturing processes.
-
Artificial Intelligence (AI): AI technology is predicted to play a significant role in the development of advanced jig systems. By enabling predictive analytics and automated adjustments, AI can optimize jig functionality and enhance precision and efficiency in assembly tasks.
-
Sustainable Materials: The adoption of sustainable materials in jig design is expected to increase, driven by the growing demand for environmentally friendly manufacturing practices. By utilizing materials such as recycled composites and biodegradable polymers, manufacturers can enhance sustainability and reduce their environmental impact.
Overall, these future trends highlight the ongoing innovation and evolution of assembly jig techniques. By understanding and leveraging these developments, professionals can optimize their use of jigs and enhance productivity and quality in their operations, ultimately fostering innovation and success in the industry.
Click here to read our expertly curated top picks!
Do's and don'ts of assembly jig usage
Do's | Don'ts |
---|---|
Ensure precision in design | Avoid complex jig designs unnecessarily |
Regularly maintain jigs | Neglect routine inspections |
Train staff thoroughly | Assume all employees understand jig use |
Incorporate feedback for improvement | Ignore user feedback and experiences |
Adapt jigs to specific needs | Use generic jigs for all applications |
Click here to read our expertly curated top picks!
Conclusion
Summary of Key Points
Assembly jigs are indispensable tools in the manufacturing industry, designed to enhance precision and efficiency during assembly processes. Their ability to hold and guide components ensures accurate alignment and positioning, reducing the likelihood of errors and defects. By minimizing manual intervention and streamlining workflows, jigs contribute to faster production times and reduced costs, making them essential for achieving excellence in manufacturing environments.
The historical development of assembly jigs traces back to early manufacturing practices, where craftsmen devised methods to hold parts in place during assembly. Over the years, jigs have undergone significant transformations, driven by technological advancements and changing manufacturing needs. The evolution of jig designs and materials has resulted in sophisticated systems that enhance precision, reduce costs, and optimize manufacturing processes.
Understanding the core principles and techniques of assembly jigs is crucial for professionals seeking to optimize their use and enhance production efficiency. By prioritizing precision, repeatability, and durability, manufacturers can achieve consistent and reliable outcomes in their operations. The implementation of modular jig systems, dedicated jigs, and advanced materials provides practical strategies for optimizing jig functionality and achieving excellence in manufacturing environments.
Encouraging Ongoing Adaptation
As manufacturing continues to evolve, professionals must continually explore and integrate assembly jig techniques to remain competitive and efficient in the evolving landscape. The adoption of smart technology, AI, and sustainable materials is expected to revolutionize jig functionality and efficiency, providing new opportunities for innovation and success.
By understanding and leveraging these developments, professionals can optimize their use of jigs and enhance productivity and quality in their operations. The ongoing adaptation and exploration of assembly jig techniques will enable manufacturers to achieve excellence in production environments, ultimately fostering innovation and success in the industry.
In conclusion, assembly jigs are vital tools for optimizing manufacturing processes and achieving excellence in production environments. By understanding their history, principles, benefits, and challenges, professionals can enhance their use of jigs and foster innovation and success in their operations.
Navigate Manufacturing Project Success with Meegle
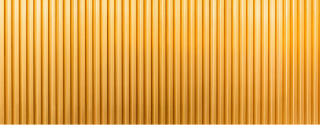
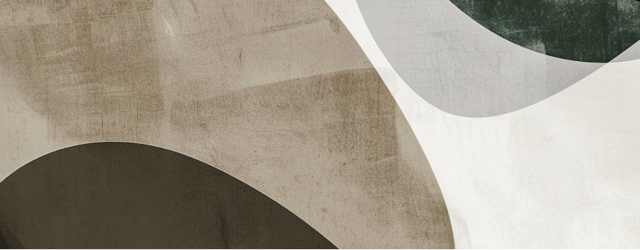
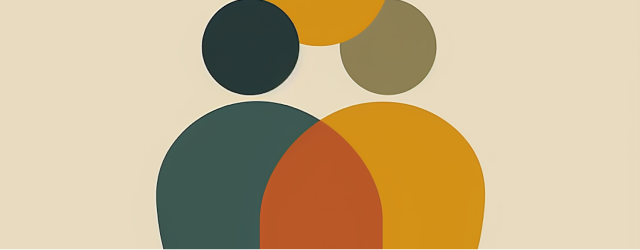
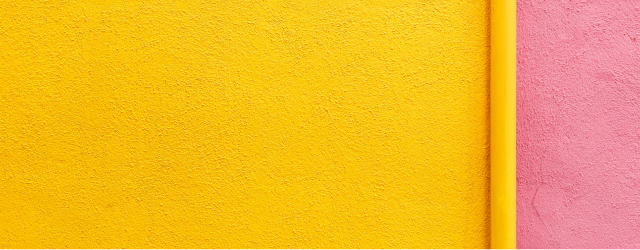
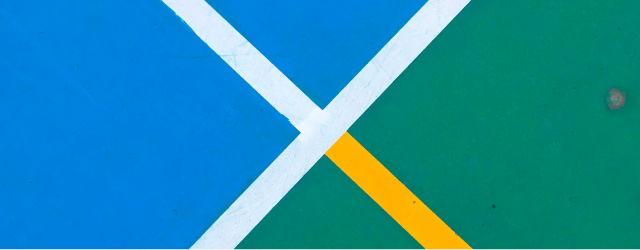
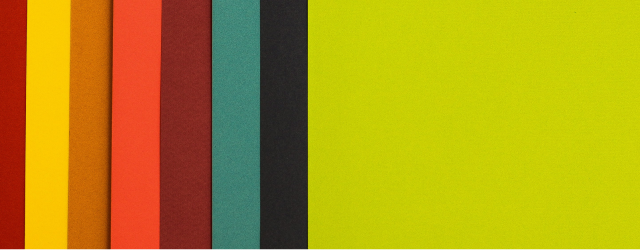
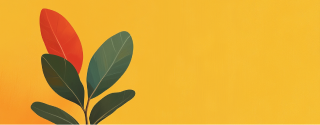
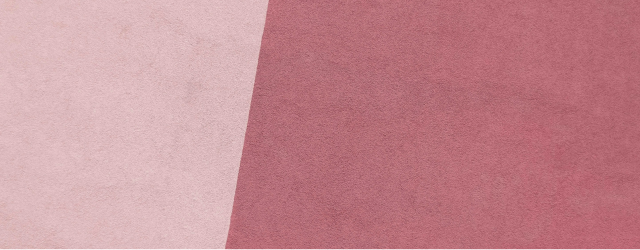