Assembly Line
Gain a thorough understanding of Assembly Line in manufacturing, with insights into their application, benefits, and strategic importance in the industry.
Overview of Assembly Line
An assembly line is a manufacturing process wherein parts are added to a product in a sequential manner, moving it from workstation to workstation until the final product is assembled. Each station typically performs a specific task, contributing to the overall production of the product. The core components of an assembly line include workers or machines, conveyor belts, and workstations configured for specific tasks. This setup allows for a streamlined production process that is both efficient and scalable.
Assembly lines play a fundamental role in manufacturing due to their ability to produce goods quickly and consistently. By breaking down the production process into smaller, manageable tasks, assembly lines enable manufacturers to achieve high levels of efficiency and output. This division of labor not only speeds up production but also reduces errors and ensures uniformity in the quality of the final product. The assembly line remains a critical element in production processes worldwide, as it facilitates mass production while maintaining quality standards.
Role in Manufacturing Efficiency
The efficiency of manufacturing operations is greatly enhanced by the adoption of assembly lines. By structuring the production process into a series of repetitive tasks, assembly lines minimize waste and optimize resource utilization. This streamlined approach reduces production time, allowing manufacturers to meet market demands swiftly and effectively.
Assembly lines also contribute to increased productivity by enabling workers to specialize in specific tasks, thereby improving skill proficiency and reducing the likelihood of errors. This specialization not only boosts individual productivity but also enhances the overall output of the manufacturing process. Moreover, assembly lines ensure consistent product quality, as each step is standardized and monitored for precision.
The correlation between streamlined processes and competitive advantage is evident in industries where speed and quality are crucial. Companies that utilize efficient assembly lines can produce and deliver products faster than their competitors, gaining a significant edge in the market. In today's fast-paced economy, the ability to adapt and scale production quickly is vital, and assembly lines provide the framework for achieving these objectives.
Navigate Manufacturing Project Success with Meegle
Historical development of assembly line
Origins of Assembly Line
The concept of the assembly line dates back to the early 20th century, with Henry Ford being one of its most notable pioneers. Ford's introduction of the assembly line in the automotive sector revolutionized production by drastically reducing the time and cost required to manufacture vehicles. His implementation involved breaking down the assembly of the Model T into 84 distinct steps, with workers assigned to specific tasks along a moving conveyor belt.
Ford's assembly line faced initial challenges, including figuring out how to balance the speed of production with quality control. There were also difficulties in coordinating the flow of materials and ensuring workers adapted to the repetitive nature of their tasks. However, the breakthroughs achieved, such as the dramatic reduction in the Model T's production time from 12 hours to about 90 minutes, set a foundation that modern assembly systems continue to build upon.
Evolution Over Time
The evolution of assembly lines has been marked by significant technological and methodological shifts. From manual processes heavily reliant on human labor, assembly lines have embraced automation and robotics to enhance efficiency and precision. The integration of Information Technology (IT) has further revolutionized assembly operations, enabling real-time monitoring and data-driven decision-making.
Technological advancements have facilitated the development of advanced assembly systems capable of adapting to varying production needs. Robotics and automation have replaced manual labor in many instances, allowing for faster and more consistent production. IT integration has also introduced sophisticated tracking and management systems, ensuring each step of the assembly process is optimized for maximum productivity.
These evolutions have not only increased the speed and accuracy of production but have also expanded the capabilities of assembly lines to handle complex manufacturing tasks. The continuous improvement of assembly technologies ensures that manufacturers can keep pace with the demands of the modern market while maintaining high standards of quality and efficiency.
Click here to read our expertly curated top picks!
Core principles and techniques
Fundamental Concepts
Several fundamental concepts underpin the efficiency and scalability of assembly lines. These include division of labor, workflow sequencing, and process standardization. The division of labor involves assigning specific tasks to workers or machines, allowing each to focus on their area of expertise. This specialization improves proficiency and reduces errors, contributing to a smoother production process.
Workflow sequencing refers to arranging tasks in a logical order to maximize efficiency. By ensuring each step follows naturally from the previous one, assembly lines minimize downtime and maintain a continuous flow of production. Process standardization involves establishing consistent procedures across all production stages, ensuring uniformity in output and reducing variability in product quality.
These concepts are crucial for optimizing assembly line operations. By ensuring a structured approach to production, manufacturers can achieve high levels of efficiency and scalability, enabling them to meet market demands effectively.
Implementation Techniques
The implementation of assembly lines involves various techniques tailored to specific production needs. Continuous flow production is a method where products move through the assembly line without interruptions, minimizing wait times and maximizing efficiency. Modular assembly involves breaking down the production process into interchangeable units, allowing for flexibility in handling different products or variations.
Just-in-time (JIT) manufacturing is another technique that focuses on producing goods only as needed, reducing inventory costs and waste. This method requires precise coordination and forecasting to ensure materials and components are available exactly when required. Selecting the appropriate technique depends on factors such as product complexity, production volume, and industry requirements.
These techniques offer manufacturers a range of options for implementing assembly lines, enabling them to tailor the process to their specific needs. By choosing the right approach, manufacturers can optimize their operations and improve their competitive position in the market.
Benefits and challenges
Advantages in Production
Assembly lines offer numerous benefits that enhance production efficiency and effectiveness. Among the most significant advantages is the reduction in production time. By streamlining tasks and eliminating unnecessary steps, assembly lines enable manufacturers to produce goods swiftly, meeting market demands with agility.
Cost reduction is another key benefit, as assembly lines optimize resource utilization and minimize waste. This efficient approach lowers manufacturing expenses, allowing companies to achieve better profitability and competitiveness. Improved product uniformity is also a notable advantage of assembly lines, as standardization ensures consistent quality across all production units.
Furthermore, assembly lines increase adaptability to market demands, allowing manufacturers to scale production quickly in response to changing consumer preferences or economic conditions. This flexibility is crucial in today's dynamic market environment, where the ability to adjust and innovate is vital for success.
Potential Limitations
Despite their numerous advantages, assembly lines also present certain challenges that manufacturers must address. High initial setup costs can be a barrier, as establishing an assembly line requires significant investment in equipment and infrastructure. However, the long-term cost savings and efficiency gains often outweigh these initial expenses.
Inflexibility in handling product variations is another limitation, as assembly lines are traditionally designed for producing uniform items. This rigidity can hinder innovation and adaptation to new products or designs. To mitigate this, manufacturers can invest in flexible automation solutions that allow for quick adjustments and customization.
Worker dissatisfaction is also a concern, as the repetitive nature of assembly line tasks can lead to decreased morale and productivity. To address this, companies should focus on workforce training and development, ensuring employees are engaged and equipped with the skills needed to thrive in a modern manufacturing environment.
Click here to read our expertly curated top picks!
Case studies and real-world applications
Automotive industry
Automotive industry
The automotive industry has long been a leader in implementing assembly lines to boost production efficiency and output quality. Car manufacturers like Toyota have pioneered techniques such as lean manufacturing, which emphasizes waste reduction and continuous improvement. By integrating assembly lines with advanced automation and robotics, automotive companies can produce vehicles with precision and speed, meeting consumer demands while maintaining high standards of quality.
Electronics manufacturing
Electronics manufacturing
In the electronics sector, assembly lines play a crucial role in producing consumer electronics with precision and speed. Companies like Apple and Samsung utilize sophisticated assembly systems to manufacture complex devices such as smartphones and tablets. These systems integrate cutting-edge technologies like robotics and IoT to ensure seamless production and real-time quality control, enabling manufacturers to deliver products that meet rigorous performance and design standards.
Food and beverage industry
Food and beverage industry
The food and beverage industry has adapted assembly lines to maintain hygiene standards and product consistency. Companies like Nestlé employ assembly lines in food processing plants to ensure efficient and sanitary production of various products. These lines incorporate automation and advanced monitoring systems to maintain quality and safety, allowing manufacturers to meet stringent regulatory standards while delivering high-quality products to consumers.
Impact analysis
Impact analysis
Quantifiable results achieved through assembly line implementation include significant productivity metrics, cost savings, and quality improvements. For instance, the automotive industry has seen production rates increase exponentially due to efficient assembly systems, reducing the time required to manufacture vehicles and boosting output volumes.
Technological integration and innovations
Current Technologies
Modern assembly lines are enhanced by technologies such as robotics, AI, IoT, and digital twins. Robotics facilitate precise and efficient production, performing tasks with speed and accuracy beyond human capabilities. AI algorithms optimize operations by analyzing data and predicting maintenance needs, ensuring maximum uptime and productivity.
IoT connectivity enables real-time monitoring and control of assembly processes, allowing manufacturers to adjust and optimize production in response to market demands. Digital twins replicate physical assembly lines in a virtual environment, providing insights into performance and enabling predictive analysis for better decision-making.
These technologies collectively transform assembly line operations, enhancing efficiency and adaptability in a rapidly evolving manufacturing landscape.
Future Trends
Upcoming trends in assembly line manufacturing include increased automation and collaborative robotics (cobots) working alongside human operators. These cobots enhance productivity by performing repetitive tasks while allowing humans to focus on more complex problem-solving activities.
AI-driven analytics will further revolutionize assembly processes, providing deeper insights into operations and enabling predictive maintenance to minimize downtime. The integration of machine learning algorithms will allow assembly lines to adapt dynamically to changing production needs, optimizing efficiency and output quality.
These innovations promise to redefine the future of assembly line manufacturing, offering manufacturers new opportunities to enhance productivity and competitiveness.
Click here to read our expertly curated top picks!
Do's and don'ts of assembly line implementation
Do's | Don'ts |
---|---|
Ensure thorough planning and analysis before implementation. | Avoid skipping the needs assessment phase. |
Invest in training and upskilling workers regularly. | Don't overlook the importance of staff involvement. |
Integrate technology to enhance efficiency and adaptability. | Avoid relying solely on outdated methods. |
Continuously monitor and refine processes for improvement. | Don't ignore feedback from operators. |
Click here to read our expertly curated top picks!
Conclusion
Summary of Key Points
Assembly lines have evolved significantly from their historical roots, integrating advanced technologies to enhance efficiency and productivity. The core principles of division of labor, workflow sequencing, and process standardization remain crucial for optimizing operations. Despite challenges, the benefits of assembly lines, such as reduced production time and improved product quality, are evident across various industries.
Through case studies, the transformative power of assembly lines in sectors like automotive, electronics, and food processing highlights their role in driving innovation and competitiveness. The integration of current technologies and anticipation of future trends further underscores the importance of assembly lines in modern manufacturing.
Encouraging Ongoing Adaptation
Industry professionals are urged to embrace continuous learning and adaptation to leverage assembly lines effectively. Staying abreast of technological advancements and market demands is crucial for maintaining competitiveness in an evolving manufacturing landscape. By fostering innovation and investing in workforce development, manufacturers can harness the full potential of assembly lines to meet future challenges and opportunities head-on.
Navigate Manufacturing Project Success with Meegle
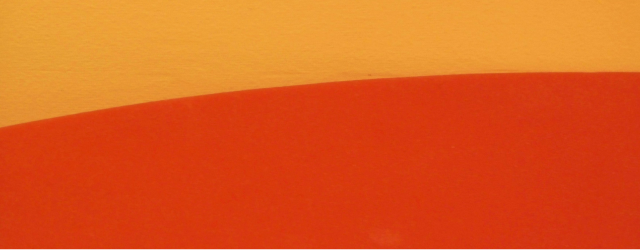
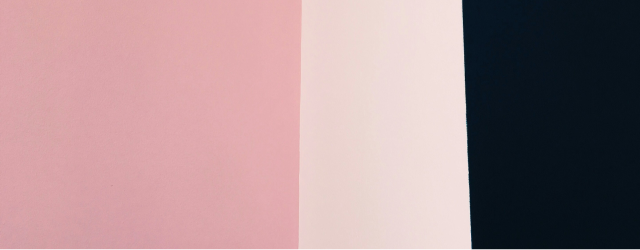
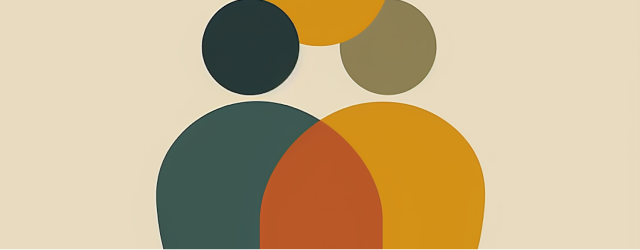
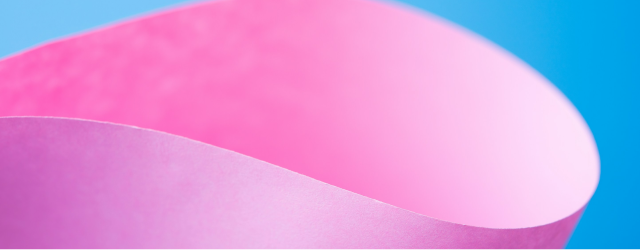
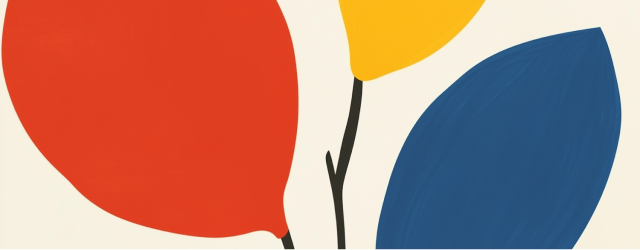
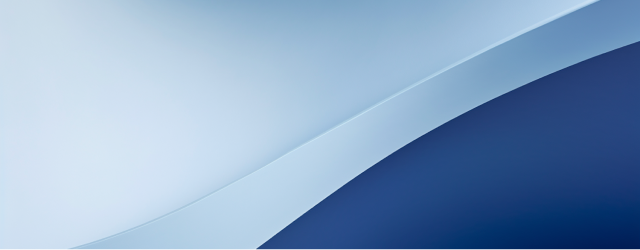
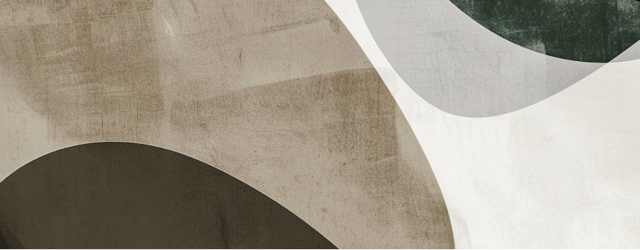
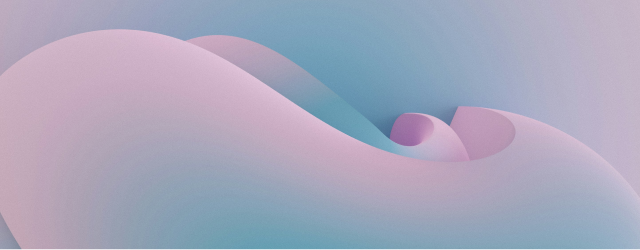